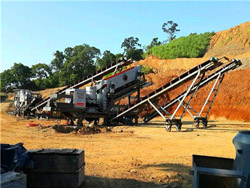
Analysis of Grinding Force and Elastic Deformation in
study of multivariables in the grinding process [8]. With regard to the grinding force model, researchers presented Processes Analysis Overview Horizontal Grinding Horizontal grinding Vertical grinding Centered grinding Centerless grinding Creep Feed Grinding and stock is Grinding and Finishing IIT Bombay
احصل على السعر
Analysis of Grinding Force and Elastic Deformation in Thread Grinding
However little research has been conducted for the thread grinding process. In this paper a numerical thread grinding model will be developed on the basis of the Only the internal thread manufacturing processes with and without chip removal using taps, thread milling, and specific internal threading processes were State of the art on internal thread manufacturing: a review
احصل على السعر
(PDF) A comprehensive review on the grinding
PDF Grinding is a manufacturing process which significantly contributes in producing high precision and durable components required in numerous Find, read and cite all the research you needAnalysis of Grinding Force and Elastic Deformation in Thread Grinding Process Authors: Wei Wang Xianying Feng Abstract and Figures Considering the grinding geometry of the thread grinding...(PDF) Analysis of Grinding Force and Elastic
احصل على السعر
Multi-component measurement of grinding force during
internal thread grinding is cylindrical; the grinding wheel of flat groove grinding and internal thread grinding is a disc wheel with tooth half angle of 𝜃, and flat Therefore, this paper proposes a form grinding simulation method that considers the geometrical relations and the relative motion during the grinding process Computerized simulation of thread form grinding process
احصل على السعر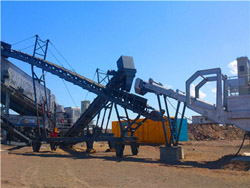
Types of Thread Manufacturing Process Methods
1. Thread cutting. Generally, it refers to the method of machining threads on the workpiece with forming tools or abrasives, mainly including turning, milling, tapping, threading, grinding, grinding, and 1. Center type grinding with axis feed: (Work spins slower) similar to cutting thread in the lathe. difference a shaped grinding wheel is used instead of the point cutting tool. (even multiple shaped grinding wheel can be used ). Speed –given by the RPM of the grinding. Several passes are necessary to complete the thread. 2.THREAD CUTTING & FORMING Concordia
احصل على السعر
State of the art on internal thread manufacturing: a review
Thread profiles can be considered as mechanical components which contributed to improving the evolution of machines and devices throughout all the history of man. The great importance of using threaded components, in industries and everyday life, is related to the versatility that allows the assembly and disassembly of components The main uses of grinding and abrasive machining: 1. To improve the surface finish of a part manufactured by other processes Examples: (a) A steel injection molding die is machined by milling; the surface finish must be improved for better plastic flow, either by manual grinding using shaped grinding tools, or by electro-grinding.Lecture 8. Metal Cutting Hong Kong University of
احصل على السعر
Research on Surface Quality and Wheel Wear of Internal Thread
Then, the influence of headstock rotating speed and grinding depth on thread surface quality was studied under the high-speed grinding condition with grinding wheel linear speed of 80 m/s. The test factors and levels are shown in Table 2. The grinding depth range is 0.01–0.05 mm, and the headstock speed range is 1–5 rpm.The model is only suitable for simple coupling motion and is based on the plane rectangular coordinate system. But the more complicated grinding process needs special consideration, such as thread(PDF) Analysis of Grinding Force and Elastic Deformation in Thread
احصل على السعر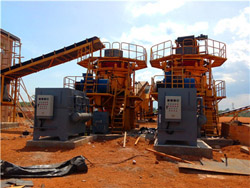
Modelling of grinding mechanics: A review ScienceDirect
Grinding is one of the most widely used material removal methods at the end of many process chains. Grinding force is related to almost all grinding parameters, which has a great influence on material removal rate, dimensional and shape accuracy, surface and subsurface integrity, thermodynamics, dynamics, wheel durability, and Volkov AE, Gazizov AF, Dzyuba VI, Medvedev VI (2014) Grinding of the inner thread without tilt of the tool spindle. J Mach Manuf Reliab 43:422–428Development and evaluation of non-contact automatic tool
احصل على السعر
4.1 Introduction 4.2 Types of grinding machines 4.2.1
4.5 Grinding machine operations The process of grinding is the operation of removing excess material from metal parts by a grinding wheel made of hard abrasives. The following operations are generally performed in a grinding machine. 1. Cylindrical grinding 2. Taper grinding 3. Gear grinding 4. Thread grinding 4.5.1 Cylindrical grindingBut the more complicated grinding process needs special consideration, such as thread grinding, the inclination angle φ of grinding wheel is also considered, and the changed orthogonal coordinateComputerized simulation of thread form grinding process
احصل على السعر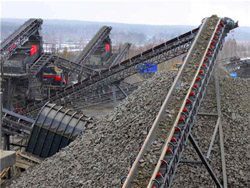
Predictive modeling of grinding force in the inner thread grinding
In this section, a theoretical model of the grinding force during inner thread grinding is detailed. A flowchart illustrating each step of the grinding force calculation process is presented in Fig. 3, which combines experimental data with the grinding force model.The chip thickness can be described using the Rayleigh probability density abrasive particles, e.g., grinding Nontraditional processes -various energy forms other than sharp cutting tool to remove material. Material Removal Processes The family tree. Cutting action involves shear deformation of work material to form a chip, and as chip is removed, new surface is exposed:TA202A: Introduction to Manufacturing Processes IIT
احصل على السعر
A study of precision grinding of micro-pitch internal thread
1 天前Section snippets PRSM nut samples. The grinding experiments were carried out on the nut of a standard PRSM RV 20, as shown in Fig. 3. The nut has a right-handed cylindrical internal thread with a straight profile, with a pitch of 1 mm, a nominal diameter of 32.5 mm, and a thread angle of 90°.Thread grinding Operation: It is done on cylindrical grinders with specially dressed wheels matching the shape of the thread as well as using a centerless grinder. Although costly thread produced by grinding is the most accurate of any manufacturing process and has a very fine surface finish. Internal and External Grinding:Grinding Machine: Definition, Parts, Working Principle, Operation
احصل على السعر
Design and development of spiral grooved grinding wheel
During the grinding process, the coolant (i.e., synthetic oil) was supplied through spindle at a constant rate of 0.075 l/s in which it spreads meticulously in the grinding interfaces/zones, i.e., between the wheel and the workpiece by the grooves. View PDF View article View in Scopus Google Scholar. 8. AL-Mokhtar O. Mohamed,information and frequency analysis of the grinding process are described. Finally, the machine learning model is discussed. A. Prerequisites Fig. 1 shows the robot used in this study. A 6-DOF manip-ulator, equipped with a six-axis force/torque (F/T) sensor and a grinder as a tool for grinding, was used in the experiments.Force control of grinding process based on frequency
احصل على السعر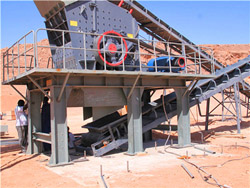
Computerised grinding procedure for large scale
grinding is between 0.5 and 1.4 μm, while after polishing it lays between 0.1 and 0.3 μm [8]. However, hand polishing has very limited impact on the surface, so the grinding process must prepare the surface as efficiently as possible. The study is dedicated to the automated grinding process and inspection procedures performedinternal thread grinding is cylindrical; the grinding wheel of flat groove grinding and internal thread grinding is a disc wheel with tooth half angle of 𝜃, and flat grinding wheel is a cylindrical wheel. For the flat grinding process, the contact between the grinding wheel and the workpiece is shown in Figure 5.Multi-component measurement of grinding force during
احصل على السعر
Centerless method of thread grinding Google Patents
The grinding of screw threads upon a work piece by means of a centerless grinding machine was first suggested by Arthur Harold Lloyd who, in his United States Patent No. 2,010,730, dated August 6, 1935, disclosed one embodiment of such a machine in which the grinding wheel, the control wheel and the work supporting blade or ledge are mounted and
احصل على السعر