
CASE STUDY Coker pump design Sulzer
Material considerations One of the major challenges for the coker charge pump is the coke particles that are entrained in the liquid. To prevent the larger particles √ Suitable for Multi-Drum Coker √ Footprint fits into any Existing Coker Units, Maximum Layout Flexibility √ System Flexibility -Slurry Transport via Pipeline (e.g. An AdvancedCoke Handling Process Refining Community
احصل على السعر
Closed Coke Slurry System (CCS System Refining
How the CCS-system works: No overflow of sludge & foam to settling tank Total coke batch is used as filtration bed in the dewatering bin resulting in Fast water The Coke drum design Issues to consider for extending the turnaround schedule of a delayed coking unit. Theory behind coke drum failure is discussed, with Coke drum design Home MDR
احصل على السعر
Modeling of an Industrial Delayed Coker Unit ScienceDirect
Abstract. Delayed Coker Unit (DCU) converts the vacuum residual feedstock to lighter and more valuable products such as motor fuels and eliminates the low-order Download chapter PDF Delayed coking is the most common process for upgrading of vacuum residua as well as a primary method for upgrading tar sands for the production Delayed Coking SpringerLink
احصل على السعر
Coker McKinsey Energy Insights
Coker. Also known as: delayed coker, DCU. In a refinery, the coker is the most extreme of the bottoms upgrading process units. A coker takes the lowest value bottoms material Material considerations One of the major challenges for the coker charge pump is the coke particles that are entrained in the liquid. To prevent the larger particles from choking the eye of the impeller, pumps can be Coker pump design Sulzer
احصل على السعر
Closed Coke Slurry System
Delayed Coker Unit (DCU) Triplan Technology GmbH Delayed Coker Unit Source: AFW How DCU‘sare usually presented in Brochures. 2019 TRIPLAN Technology –Proprietary & Confidential 4 Crusher Chute Coke Drum Dewatering Bin Water Settling Tank Drain Water Clean Water Pump Clean Water Tank Open System√ Suitable for Multi-Drum Coker √ Footprint fits into any Existing Coker Units, Maximum Layout Flexibility √ System Flexibility -Slurry Transport via Pipeline (e.g. 4Kilometers) for Supplying remote Power Stations / Gasification Plants / CalcinerPlantswith Petcokedirectly √ Basin Construction in Concrete (above-/underground) or Steel WorkAn AdvancedCoke Handling Process Refining Community
احصل على السعر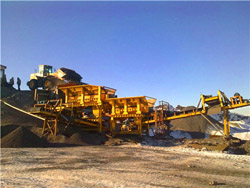
Impact of Feed Properties and Operating Parameters on
– Crusher comminution; Jet pump specification & cutting nozzle wear, under-powered systems can lead to grinding Coke cutting technique: do not use “washing” Coke reclaim: Bridge crane vs FEL Coke handling design: minimize no. of transfers • Maintain wet coke at moisture levels of 7%+ to minimize coke drying and windborneDouble Roll Crusher with integrated Chute (Proprietary Design) High Torque direct drive each roll Crushing ratio 10:1; e.g. 1.000 mm --> 100 mm ; 40” --> 4” resp. Safe & remote operation: Hydraulic chute raising Docking automatic to drum flange or bottom valve CLOSED COKE SLURRY SYSTEM (CCS SYSTEM)Closed Coke Slurry System (CCS System Refining
احصل على السعر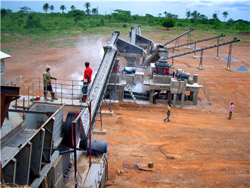
Coke drum design Home MDR
delayed coking units, which process the bottom-of-barrel material into valuable, lighter products such as gasoline and distillates. Adding a delayed coker unit to a refinery flow scheme provides a two-fold financial incentive: cheaper feedstock and a higher volume of light products. In several parts of the world, North America being more severeOf the three main types of coker used in oil refineries, the delayed coker is the most common. It supports a non-catalytic thermal process that converts a wide range of residues into high value liquid products such as liquefied petroleum gas (LPG), heavy coker gas oil (HCGO), light coker gas oil (LCGO) and almost pure carbon residue, known as Coker pump is optimizing processing performance and reliability
احصل على السعر
Meshari Alsaysabi Electrician Savage Services LinkedIn
Delayed Coker Unit and Terminal solid handling system on King Fahd Industrial Port. (Ship loader- conveyor belt-reclaimer-pump- motors-condition monitor-crusher-bridge crane- motorize DCV valve-lube oil system- hydraulic system-Switch gear low voltage and high voltage communication-PLC-Thermo graphic and current signature)=> Each coker cuts through a crusher car to a sluiceway and has the following: 3 Deheading Carts 2 Crusher Carts => Water and coke are moved by high pressure water pumps to common dewatering bins Coke is loaded on a conveyor and moved offsite Water is recycled for reuse October-2014 coking RioDelayed Coker Coke Drum Bottom Head Safety
احصل على السعر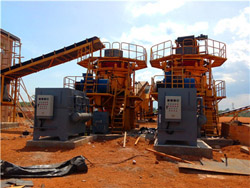
Delayed Coking SpringerLink
The first delayed coker was built by Standard Oil Whiting, IN, USA, in 1929, building upon the features of the previous thermal-cracking processes and separating the heater from the coke drum. Fouling in the furnace tubes is a significant problem in delayed coker units. Fouling deposits act as an insulating layer inside the tubes, hinderingThe coker charge pump would typically be a 2-stage radially split pump, API 610 type BB2, capable of operating at around 370 °C (700 °F) and discharge pressure around 42 bar (600 psi). More importantly, the pump needs to be capable of operating over a wide flowrate while maintaining maximum reliability.Coker pump design Optimizing processing performance and reliability
احصل على السعر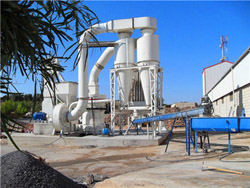
Keys To A Successful Delayed Coking Unit Revamp
Delayed Coking Unit Revamp By John E. Collins, Technical Services Manager, CB&I • Currently operates eight delayed coker units (DCUs) with combined capacity of 9.3 million • Check crusher load rating • Confirm OSBL facilities are sufficient • Check pad drainage andThe coke drums are from 6 to 9 m in diameter and up to 30 m tall. Typical on-stream times for a drum are 16–24 hr with a corresponding time needed to remove the coke from the drum and get it ready to be put back on-stream. A simplified process flow diagram for a delayed coking unit is shown in Fig. 8. TABLE II.Coking Drum an overview ScienceDirect Topics
احصل على السعر
{"payload":{"allShortcutsEnabled":false,"fileTree":{"50":{"items":[{"name":"2.500 ton ukuran pabrik semen vertikal.md","path":"50/2.500 ton ukuran pabrik semenPetroleum Refinery Engineering is one of the most important areas of Chemical Enginering.It serves the purpose of fuel production along with a great variety of hydrocarbons. Refineries are one of(OIP-2021) Internship Report on Petroleum Refinery Engineering
احصل على السعر
coker unit crusher
Crushmc1 Mastercrush Aluminum Can Crusher Recycler. The only can crusher to recycle many different sizes of aluminum cans. can recycle 12oz, 16oz, 24oz amp 32oz cans and can crush water bottles as well. solid steel with stainless steel rods and brass inserts, hardened steel bolts with lock nuts. it can be mounted vertically or horizontally. When a Coker and associated units are shut down for maintenance, an extra 1,500 contractors are brought to site.The Oil Movement and Storage area, where intermediate products are stored, has a capacity of 6.5 million barrels.Syncrude Sweet Blend, or SSB, is a 31-33 o API crude oil with 0.1- 0.2% sulphur. It contains no residue Syncrude Engineering
احصل على السعر
Food Depackaging: The Systems BioCycle
The machine can apply 13,300 to 19,200 foot-pounds of torque at a pressure of 1,740 lbs/sq. in. to the food waste and its packaging. Water is not added during processing. Recovery rates of the food contents are on the order of 99.2% and purity of the recovered material exceeds 99.5%% percent, according to Doppstadt.Delayed Coking Unit (DCU) Process Description. The main objective of the delayed coking unit is to convert low value residual products to lighter products of higher value and to produce a coke product, whose value will depend on its properties such as sulfur, metals, etc. The conversion is accomplished by heating the feed material to a high Delayed Coking Unit PDF Coke (Fuel) Cracking
احصل على السعر
Delayed Coker High Pressure Cutting Water Safety
Old 4-drum coker on 14-hr coking cycles-Manual deheading and valve operations-Old Coke Cutting System-Did not use combination tool, instead they manually changed coke bits-Cut coke through Crusher to a Sluiceway ⇒They called the employees that cut their coke "Sluicers". They cut with two sluicers....One on top and one on the A coker crane in a petrochemical plant moves hot, fresh coke fuel in the coke pit out of the way of the coke drum so that coke gets cool down. After 24 hours, the crane moves the cooled, de-watered coke to a crusher, hopper, or conveyor. The work is fast and continuous, and downtime completely halts production.Coker cranes Konecranes
احصل على السعر