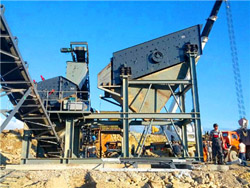
(PDF) Iron Ore Agglomeration Technologies
Iron ore sintering is a pretreatment step of smelting that agglomerates the iron ore using surface melting of green pellets to Sintering and pelletization are the most important agglomeration technologies, in this way, in the EU-27, 14 countries Iron Ore Agglomeration Technologies IntechOpen
احصل على السعر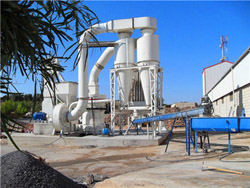
Metals Free Full-Text The Effect of Concentrate/Iron Ore
The work is focused on studying the influence of the ratio of concentrate to iron ore on the phase composition of the iron ore agglomerate. The concentrate has A process for improving the compressive strength of iron ore agglomerates, such as pellets or briquettes, used as a feed to an iron blast furnace, in which the particulate iron ore is Agglomeration of iron ores and concentrates 百度学术
احصل على السعر
Evolution behavior and mechanism of iron carbon agglomerates
Iron carbon agglomerates (ICA) are the composite burden for low-carbon blast furnace (BF) ironmaking. In order to optimize the reactivity of ICA according to the The main difference between iron ore agglomerates and CCAs is the rate-controlling step of the reduction of iron oxides. In case of iron ore agglomerates, the reduction takes place at gas-solid interfaces. Recent Trends in Ironmaking Blast Furnace
احصل على السعر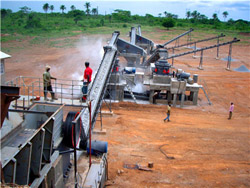
Agglomeration of Iron Ores Ram Pravesh Bhagat Taylor
Breadcrumbs Section. Click here to navigate to respective pages. This book focuses on agglomeration, or the size enlargement process, of iron ores. This process sits at the The iron-oxide material in the agglomerates consists of iron ore -- hematite and/or magnetite -- which in various forms is reduced to iron. The reduction usually takes Strength of iron-ore agglomerates during reduction
احصل على السعر
MECHANISMS OF REDUCTION OF IRON ORE/COAL AGGLOMERATES
Laboratory studies of chemical kinetics and heat transfer in the reduction of iron ore/carbon (coal) mixtures in various forms are reviewed. Therefore, the rate-limiting steps, which are of critical importance in process development, may be identified or suggested for a given set of conditions. Commercial operations using rotary hearth Iron Ore Agglomeration Technologies. Until the 1950s of the last century, the oxidized iron ores that were loaded into the blast furnace had granulometries within 10 and 120 mm. However, the depletion of high-grade iron ore sources has made necessary the utilization of concentration processes with the purpose of enriching the iron ore.[PDF] Iron Ore Agglomeration Technologies Semantic Scholar
احصل على السعر
Evolution behavior and mechanism of iron carbon agglomerates
The ICA used in this study is made of one type of iron ore, four types of coals and one type of binder. The chemical composition of iron ore is listed in Table 3, and about 80% of the iron ore is less than 75 μm.The proximate analysis, ash composition and caking characteristics of the four coals are listed in Table 4, and all coals are crushed on the specified essential factors governing the reduction disintegration behavior of the iron ore agglomerates, i.e., iron ore sinters and pellets. Reduction disintegration index (RDI) values were measured after the reduction of the agglomerate samples using the gas mixtures of CO–H 2–CO 2–N 2. The mineral textures of reduced samples wereQuantitative Evaluation of Reaction Mode and Reduction
احصل على السعر
Kinetic characterization of flash reduction process of hematite ore
The reduction degree (R) of iron ore is defined as the ratio of oxygen mass loss to the initial reducible oxygen mass in the hematite ore as shown in Eq. (1). As the experimental temperature is above 843 K, the reduction process of hematite takes place step-wise, with magnetite and wüstite as intermediates. When the hematite is completelyThermal conductivities of dense pure hematite, magnetite and wustite measured using the laser flash method as reference value have been summarized in the form of an empirical equation k=1/(AT+B). Wustite shows an almost constant and the relatively low thermal conductivity due to the lattice imperfection. Thermal resistivities, Measurement and Modeling of Thermal Conductivity for Dense Iron
احصل على السعر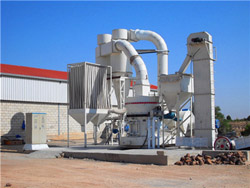
Global Iron Ore Market Report 2022: Major Players Include
The global iron ore mining market is expected to grow from $166.94 billion in 2021 to $188.69 billion in 2022 at a compound annual growth rate (CAGR) of 13.0%. The iron ore mining market isIron ores, agglomerates. EC number: 265-996-3 CAS number: 6 The product of agglomerating iron ore fines, concentrates, iron sinter, and other iron-bearing materials. Includes pellets, nodules and briquettes.Registration Dossier ECHA
احصل على السعر
Strength of iron-ore agglomerates during reduction
The iron-ore agglomerates are normally tested in a reduction gas consisting of 35% CO, 5% CO2 and 60% N2 by volume at 1,000. Heating is done in a nitrogen atmosphere, after which the agglomerates are reduced isothermically for a certain length of time. A couple of the agglomerates are then compressed one at a time -- still at reductionThe thermal conductivity of dense pure and reduced iron ore agglomerates and nonfired pellets were measured using the laser flash method (LFM) [17]. Sundarmutri and Rao [18], [19] determined the thermal diffusivity and conductivity of fired spherical hematite pellets and dried pellets using transient conduction for radial heat flow.A comprehensive characterization on the structural and
احصل على السعر
FLX-2001 Iron Ore FLUXANA
Name of substance iron ores, agglomerates Identifiers CAS No 6 EC No 265-996-3 SECTION 4: First aid measures 4.1 Description of first aid measures FLX-2001 Iron Ore United Kingdom: en Page: 2 / 13. 5.3 Advice for firefighters In case of fire and/or explosion do not breathe fumes.The iron ore agglomerates obtained by the present invention exhibit appropriate chemical, physical and metallurgical qualities as shown in Tables 1, 2 and 3 below, and thus are presented as an alternative to the metal charge in the reduction furnace.KR20220013351A Iron ore fine agglomerate manufacturing
احصل على السعر
(PDF) The angle of repose and size segregation of
The apparent density of iron ore gr anules fluctuated slightly within the range from 2.8 g/cm 3 to 3.2 g/cm 3,varying with the specific mater ial properties of individual granule samples .Agglomerates for blast furnaces can be produced with ore grades lower than 65% Fe. Vale says it is working to increase its production of high-quality iron ore and expand its capacity to concentrate ore, which also raises the iron ore grade, enabling the company to meet demand from steelmakers for these products.Vale makes headway on low-emission iron ore briquette
احصل على السعر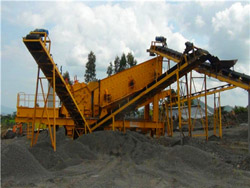
Effect of Iron Content on Thermal Conductivity of
We have simultaneously measured thermal conductivity (λ) and thermal diffusivity (κ) for polycrystalline ferropericlase with different Fe contents (Fp 3, Fp 5, Fp 10, Fp 20, Fp 30 and Fp 50) up to 23 GPa and 1100 K by a pulse heating method.Experiment results reveals that even small amounts of Fe in ferropericlase can strongly reduce the The mechanisms of agglomeration and defluidization and fluidization characteristic of iron oxide particles were investigated based on the theory of surface diffusion, interface reaction, surface nano/microeffect, and phase transformation. Moreover, a mathematical model was developed to predict the high-temperature defluidization Mechanism and Prevention of Agglomeration/Defluidization during
احصل على السعر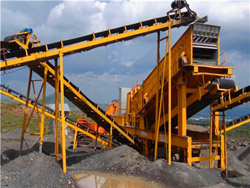
Effect of Added Olivine on Iron Ore Agglomerate During
Agglomerates were exposed to different experimental conditions to study the effect of olivine on the behavior of magnetite and hematite at high temperatures. Olivine particles were found to reactIron ore is agglomerated either with the sintering or with the pelletizing process. In addition, carbon composite agglomerates (CCAs), which refer to agglomerates containing carbon and iron-bearing materials and possibly a binder, could be charged from the top of the BF (Ahmed et al., 2014). The most important reducing agent for the BF isExtensive review of the opportunities to use biomass-based
احصل على السعر
(PDF) Iron Ore Agglomeration Technologies Provisional chapter Iron Ore
Iron ore sintering is a pretreatment step of smelting that agglomerates the iron ore using surface melting of green pellets to improve the quality of the steel product. The sintering process notThe standardization applied to iron ore was followed. The best result of crushing strength was 98.52 daN/pellet. The agglomerates with approved crushing strength for use in electric furnaces were smelted to produce alloys containing nickel; the agglomerates were characterized by scanning electron microscopy.Agglomeration and Characterization of Nickel Concentrate
احصل على السعر