
The Deposit Formation Mechanism in Coal-Fired
The deposit is a ring-like material adhering to the refractory brick of the rotary kiln lining during the production of iron ore pellets. In Deposit formation in the coal-fired rotary kiln is frequently found in the production of fluxed iron ore pellets by the grate-kiln process and affects normal production. In this paper, the Effects of Pellet Basicity on the Simulated Deposit Formation
احصل على السعر
Predictive models and operation guidance system for iron ore pellet
The main technologies used for iron ore pellet production include the grate-kiln, straight grate, and shaft furnace processes [1,8,9]. The dominant process adopted 43 Pellets produced to be used in ironmaking processes must have characteristics that meet the list of quality specifications (PDF) Iron Ore Pelletizing Process: An Overview
احصل على السعر
Deposit Formation in a Coal-Fired Rotary Kiln for Fluxed Iron Ore
Abstract During the roasting process of fluxed pellets in a coal-fired rotary kiln, the incomplete combustion of pulverized coal injection accelerates deposit The deposit is a ring‐like material adhering to the refractory brick of the rotary kiln lining during the production of iron ore pellets. In the initial formation stage, the The Deposit Formation Mechanism in Coal Fired Rotary
احصل على السعر
Deposit Formation in a Grate-Kiln Plant for Iron-Ore Pellet Production
It is therefore important to understand the slag formation mechanism in the grate-kiln production plant. This study initiated the investigation by in situ sampling and identifying This paper summarizes the results and highlights the main conclusions from over a decade of systematic studies of the kiln aerodynamics of an iron ore pelletizing The Aerodynamics of an Iron Ore Pelletizing Rotary Kiln
احصل على السعر
Mathematical models and expert system for grate-kiln
Grate-kiln is a widely used process for iron ore oxide pellet production in China. It is treatable, solid fuel usable ore, with large capacity, and has better thermal Deposit formation in the coal-fired rotary kiln is frequently found in the production of fluxed iron ore pellets by the grate-kiln process and affects normal Effects of Pellet Basicity on the Simulated Deposit Formation
احصل على السعر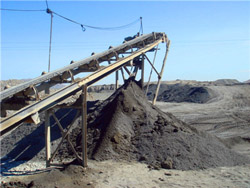
Effects of Pellet Basicity on the Simulated Deposit Formation
Deposit formation in the coal-fired rotary kiln is frequently found in the production of fluxed iron ore pellets by the grate-kiln process and affects normal production. In this paper, the effects of pellet basicity (CaO/SiO2 mass ratio) on the simulated deposit formation were investigated. The results show that the porosity of deposits samples increases from 30.8 It is an agglomerating process of converting iron ore fines into ‘uniformed sized iron ore pellets’ which can be charged directly into a blast furnace (BF) or into a vertical furnace or rotary kiln normally used Introduction to Iron ore Pellets and Pelletizing
احصل على السعر
Iron ore pelletization ScienceDirect
The pelletization process is the primary consumer of binders in the iron ore industry. The selection of an appropriate binder type and dosage is of critical importance in producing good quality pellets at a reasonable price. Binders accomplish two very important functions in iron ore pelletization: .This product is known as direct reduced iron (DRI) or sponge iron. Processes that produce iron by reduction of iron ore (in solid state) below the melting point are generally classified as DR(PDF) i) Direct Reduced Iron: Production ResearchGate
احصل على السعر
An experimental study of direct reduction of hematite by
Thermogravimetric analysis. The TG experiments in this study were carried out in a NETZSCH STA 449 F3 in non-isothermal condition. Around 50 mg pellets were heated from room temperature to 1000 °C at a heating rate of 10 °C min −1 under nitrogen with a flow rate of 100 mL min −1 for evaluation of iron oxide reduction. Experiments The deposit-forming problem is one of the main bottlenecks restricting the yield and production benefit of iron ore pellets produced by coal-fired rotary kilns. In order to implement measures to ensure the efficient production of pellets by coal-fired rotary kilns, the mechanism and influencing factors on the deposit formation were reviewed. The The Deposit Formation Mechanism in Coal-Fired Rotary Kiln for Iron Ore
احصل على السعر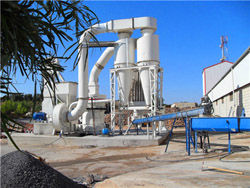
(PDF) An Innovative Process for Production of TiO2 from
An Innovative Process for Production of TiO2 from Low Grade Raw Materials to compare reduction behavior of ilmenite ore pellet with normal iron ore pellets and. ulating a tunnel kilnIn order to explore the efficacy of iron ore–coal composite pellets over ordinary green pellets, indurated pellets, briquettes as well as standard charging of material in the form of concentric layers of iron ore and coal fines, or their mixture, these pellets were tested at 1,150 °C in a 7 tons per day (7 tpd) pilot tunnel kiln. Reduction of iron ore coal Reduction Efficiency of Iron Ore–Coal Composite Pellets in Tunnel Kiln
احصل على السعر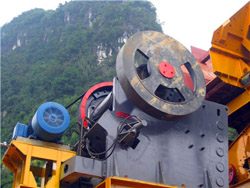
Effects of Pellet Basicity on the Simulated Deposit Formation
The three common processes used in iron ore pellet production are the shaft furnace process, the straight grate process, and the grate-kiln process. 8 As the dominant process for iron ore pellet production in China, the proportion of iron ore pellets produced by the grate-kiln process has exceeded 70%. 9 Deposit formation in a rotary Bentonite, an inorganic binder, has been the main binder used in the iron ore pelletizing. process since the beginning of pellet production in the 1950s. Bentonite promotes the forma-. tion of(PDF) Iron Ore Pelletizing Process: An Overview ResearchGate
احصل على السعر
Processes Free Full-Text NOx Emission
The NOx reduction in the iron ore pelletizing process becomes an important environmental concern owing to its role in the formation of photochemical smog and acid rain. Thus, it is essential to Keywords: Tunnel Kiln, Iron ore-coal composite pellets, Sponge iron, Thermal efficiency, Carbon utilization efficiency, Percentage metallic iron . 1. INTRODUCTION The tunnel kilns are mostly used by the ceramic industries for heating refractory and ceramic products [1-2]. In the year 1908 use of tunnel kiln started for iron SPONGE IRON PRODUCTION FROM ORE -COAL
احصل على السعر
Initial stage of deposit formation process in a coal fired grate
Serious deposits in the grate-kiln plant for iron ore pellet production can decline pellets quality and reduce production efficiency. The initial stage of deposit formation is crucial for adhesion and growth of deposit on refractories in the kiln.In this study, the simulated experiments of FeO formation indicated that the high FeO content decreased Sponge iron powder . The Höganäs process is a direct reduction method for production of sponge iron powder using magnetite ore (Fe3O4) and carbon as raw materials. The reduction process takes place in a gas fired tunnel kiln at around 1200°C for 60 hours producing a sponge iron cake that is crushed, milled andIron Manufacturing process related to the specified
احصل على السعر
DESAIN DAN SIMULASI TUNGKU BAKAR UNTUK
DESAIN DAN SIMULASI TUNGKU BAKAR UNTUK PENGOLAHAN PASIR BESI MENJADI SPONGE IRON DENGAN TEKNOLOGI TUNNEL KILN = DESIGN AND SIMULATION OF FURNACE FOR FERRUGINOUS SAND TO BE SPONGE IRON PROCESS BYThe three common processes used in iron ore pellet production are the shaft furnace process, the straight grate process,andthegrate-kilnprocess.8 Asthedominantprocessfor iron ore pellet production in China, the proportion of iron ore pellets produced by the grate-kiln process has exceeded 70%.9Effects of Pellet Basicity on the Simulated Deposit
احصل على السعر
Microstructure and phase analysis of indurated iron ore pellets
The green pellets are thermally treated in the grate and rotary kiln to increase the mechanical strength [12–14]. In the industrial process, the temperature in the rotary kiln used in iron ore pellets production is about from 1250 °C to 1350 °C, which is fired by coal or natural gas [10].In addition, an optimum route has been suggested to improve the pellet properties concerning the direct reduction process in a tunnel kiln. It is proposed that the process of direct reduction of these low-grade ilmenite composite pellets followed by smelting would lead to the development of an energy-efficient TiO 2 slag production An Optimal Route for the Preparation of Metallized Composite Pellets
احصل على السعر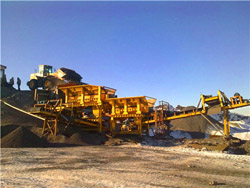
The Deposit Formation Mechanism in Coal-Fired Rotary Kiln for Iron Ore
The Deposit Formation Mechanism in Coal-Fired Rotary Kiln for Iron Ore Pellet Production: A Review. August 2021; Crystals 11(8):974; DOI:10.3390 The grate-kiln process includes pelletizing
احصل على السعر