
Simulation and optimization of crushing chamber of gyratory crusher
The gyratory crusher consists of a mantle shaft, a shell, a pinion shaft assembly, and a position system [26], the mantle shaft and the shell are eccentrically At present, there are relatively little researches on the chamber shape of the gyratory crusher, mainly focusing on cone crusher. Compared with the gyratory crusher, Simulation and optimization of crushing chamber of gyratory crusher
احصل على السعر
Gyratory Crusher an overview ScienceDirect Topics
Gyratory crushers were invented by Charles Brown in 1877 and developed by Gates around 1881 and were referred to as a Gates crusher [1]. The smaller form is described as a The gyratory crusher is widely used in primary crushing of metal ore such as iron ore and copper ore due to its high productivity and large feed inlet [ [1], [2], [3]].Simulation and optimization of gyratory crusher
احصل على السعر
Mathematics Free Full-Text Mathematical
As a result of its solution, the rational shape of the working chamber cheek of the single-roll gyratory crusher was established, representing a logarithmic spiral arc. Analytical expressions were derived A primary gyratory crusher was required to crush iron ore at the rate of 3000 t/h. The largest size of the run-of-mine ore was 1000 mm. The required product size was Gyratory and Cone Crusher ScienceDirect
احصل على السعر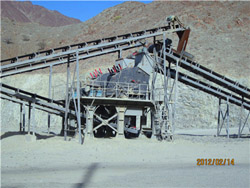
Minerals Free Full-Text Torque Analysis of a Gyratory Crusher
In this paper, a DEM model was applied to a copper mining gyratory crusher to perform a comprehensive analysis of the loads in the mantle, the crushing Gyratory crusher is a crushing equipment that uses the gyratory motion of the crushing cone in the conical cavity inside the shell to extrude, bend, and impact Gyratory Crusher SpringerLink
احصل على السعر
Simulation and optimization of gyratory crusher
However, the article did not address the problems of the optimal design for such crushers. The works [20, 21] dwell on the same method, along with the method Comminution by gyratory crusher is the first stage in the size reduction operation in mineral processing. In the copper industry, these machines are widely utilized, and their reliability has become a relevant aspect. To optimize the design and to improve the availability of gyratory crushers, it is necessary to calculate their power and torque Minerals Free Full-Text Torque Analysis of a Gyratory Crusher
احصل على السعر
THE EFFECT OF LINER WEAR ON GYRATORY
A gyratory crusher is a key mineral processing asset in a comminution circuit. A wear model with the basis in Finnie’s wear model is developed to calculate wear from combined abrasiveGyratory crusher is a kind of commonly used mining machinery. Because of its heavy workload and complex working environment, it is prone to failure and low reliability. e basis of the leaf(PDF) Fault Diagnosis of the Gyratory Crusher Based on Fast
احصل على السعر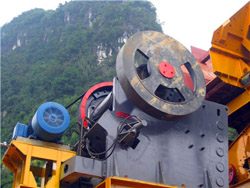
The Effect of Liner Wear on Gyratory Crushing
2 crusher performance is investigated for an Allis-Chalmers Superior 60-89 crusher. Primary gyratory crushers are commonly fed via haul trucks from one or two radial positions.A gyratory crusher consists of a movable and truncated conical head and a fixed concave shell, as is presented in Figure1. The head is integral with the main shaft, and it is covered by an element of wear named mantle. The set of these parts is the main shaft assembly. The external element is denominated concave and is fixed on the main Torque Analysis of a Gyratory Crusher with the Discrete
احصل على السعر
Chamber Optimization for Comprehensive Improvement of Cone Crusher
This study aims to analyze the impact of key structural parameters such as the bottom angle of the mantle, the length of the parallel zone, and the eccentric angle on the productivity and product quality of the cone crusher and optimize the crushing chamber to improve the crusher performance. The amount of ore in the blockage layer was On this basis, the impacts of the mantle shaft angle, the concave angle, the eccentric angle, and the mantle shaft speed on the gyratory crusher performance are explored by the method ofSimulation and optimization of gyratory crusher
احصل على السعر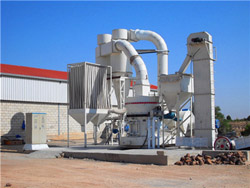
Failure analysis of eccentric bushings in large gyratory crusher
The gyratory crusher model is PXZ1417, and its specific structure is shown in Fig. 1. The crusher is composed of external shell, mantle shaft, sliding bearing, friction disc and other parts. On this basis, the mesh division of the gyratory crusher is carried out. To improve the accuracy of analysis results, the internal core parts areJaw, gyratory, cone and roller crushers are all examples of crusher machines that utilize form conditioned compression to achieve size reduction. There is an essential and important(PDF) Cone Crusher Performance ResearchGate
احصل على السعر
Industrial Solutions Gyratory crushers ThyssenKrupp
The bevel gear and pinion of the crusher are both of a cyclo-palloid spiral type, which allows greater forces to be absorbed and greater drive power to be installed. A B C C D F E I J H K G Gyratory crusher Weights 1) Type Feed opening Mantle diameter (oversized) Speed of eccentric bushing Max. motor power Total weight of gyratory 5 10 1 TON’s SUPERIOR® primary gyratory crushers feature crushing chambers that deliver the greatest possible throughput while placing the least stress on critical components. This means higher capacities, lower power requirements and more even wear all helping to decrease operating cost per ton. 2 TON’s MP series cone crushers process more ore Minerals processing equipment TON Corporation PDF
احصل على السعر
Fault Diagnosis of the Gyratory Crusher Based on
Gyratory crusher is a kind of commonly used mining machinery. Because of its heavy workload and complex working environment, it is prone to failure and low reliability. In order to solve this The basis weight of the gyratory crusher machine is usually 2-3 times the weight of the main part, and the basis weight of the jaw crusher machine is 5-10 times the weight of the machine itself; Sheet products generated by gyratory crusher are much less than jaw crusher. However, it also has disadvantages that the body of the gyratory An Overview on Size-Reduction
احصل على السعر
Design of a crushing system that improves the crushing
has to follow these three steps: crusher selection, crusher layout and process design. 2.4 Crushers . A crusher is a tool or machine that is used to reduce the size of a large solid particle to a smaller solid particle. The ore can have a size of up to 400mm. There are many types of crushers but the major ones are the jaw, gyratory and the coneThe practical method of operation of each type of gyratory crusher is indicated and the various methods of computing operating variables such as speed of gyration, capacities and power consumption given are prescribed by different authors. Mathematical basis of hard ware controls, their setting for integrated circuits involving one, two orMineral Processing Design and Operations ScienceDirect
احصل على السعر
(PDF) Torque Analysis of a Gyratory Crusher with the
In this paper, a DEM model was applied to a copper mining gyratory crusher to perform a comprehensive analysis of the loads in the mantle, the crushing torque, and crushing power. A novel polarGyratory Crushers. The primary rock breaker most commonly used in large plants is the gyratory crusher, of which a typical section is shown in Fig. 5. It consists essentially of a gyrating crushing head (521) working inside a crushing bowl (522) which is fixed to the frame (501). The crushing head is carried on a short solid main shaft (515Gyratory Crushers 911 Metallurgist
احصل على السعر
Analysis and optimization of cone crusher performance
The gyratory crusher is the main coarse crushing equipment for iron ore [2,3], its performance directly affects the quality and cost of subsequent iron purification. On this basis, the impacts of the mantle shaft angle, the concave angle, the eccentric angle, and the mantle shaft speed on the gyratory crusher performance are explored by theThe gyratory crusher shown in Figure 2.6 employs a crushing head, in the form of a truncated cone, mounted on a shaft, the upper end of which is held in a flexible bearing, whilst the lower end is driven eccentrically so as to describe a circle. The crushing action takes place round the whole of the cone and, since the maximum movement is at the Gyratory Crusher an overview ScienceDirect Topics
احصل على السعر
What Type of Crusher Is Best for Primary Crushing?
The main features of a Gyratory Crusher include a tall crushing chamber lined with replaceable manganese wear plates, a main shaft with head and mantle, and a spider to anchor the top of the main shaft bearing. They have an adjustable main shaft positioning system and drive assembly, and they are available in a single cylinder or
احصل على السعر