
Aluminum Recovery from White Aluminum Dross by a
The aluminum recovery from white aluminum dross by a mechanical treatment and sizing followed by remelting process was investigated. The dross was subjected to a ball mill, and the obtained particles were sized in different ranges. They JOEST builds plant with specially developed ball mills to process Dross recycling with JOEST technology
احصل على السعر
On trending technologies of aluminium dross recycling: A
Compared to the conventional process of separating aluminum, this In this paper, a new method is proposed for metallic Al recovery and Efficient Al Recovery from Aluminum Dross with
احصل على السعر
Hydrolysis of aluminum dross material to achieve zero hazardous
Aluminum dross is activated by mechanically milling to particles of about Aluminum baths are always covered with a layer of dross resulting from the aluminum surface oxidation. This dross represents 1–10% of the melt and may contain up to 75wt.% aluminum.(PDF) Processing of Aluminum Dross: The Birth of
احصل على السعر
China Aluminium Dross Separating Machine/Accessory
Specializing in the production of aluminum(zinc) dross separator, automatic aluminium material flow for Al production. The data is that for 2008. As Al production Development of Aluminum-Dross Chen
احصل على السعر
en/ball mill production line of aluminum dross.md at main
英语网站资料. Contribute to sbmboy/en development by creating an account on .Al2O3-bonded SiAlON ceramic with self-coating was prepared using aluminum dross and silicon solid waste as starting materials under ambient air conditions. The changes in phase, microstructure, and physical properties of the ceramic with temperature were analyzed and the formation mechanism of the SiAlON phase was Materials Free Full-Text Preparation of Self-Coating Al2O3
احصل على السعر
Here's what No One tells you about
Here’s what No One tells you about Comprehensive Utilization Of Aluminum Dross. China electrolytic aluminum industry is developing rapidly, and its output level has been leading the world for The traditional aluminothermic reduction of vanadium-enriched slag using metallic Al as a reductant to produce Fe-V alloys causes high production costs and energy consumption. Aluminum dross as a solid waste with strong reducibility is a cost-effective and carbon-free secondary resource. In the present work, an efficient and sustainable Recovery of Valuable Metals and Production of Fe-V Crude
احصل على السعر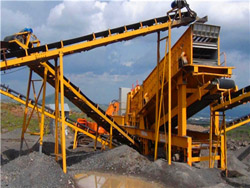
Synthesis of Calcium Aluminates from Non-Saline Aluminum Dross
The reactive milling time used was 5 h in a ball mill, for a ball/dross mass ratio of 6.5. describes obtaining calcium aluminates from the residue obtained after the treatment of salt dross from the production of secondary aluminum, The results obtained on the mineralogical composition of the sintered materials by XRD are in line withThe secondary aluminum dross was ground to a particle size smaller than 0.074 mm with a ball mill pulverizing machine; then, the pulverized dross was sent for detailed inspection and analysis. Firstly, qualitative chemical composition analysis of the secondary aluminum dross was carried out by the X-ray fluorescence spectrometry Materials Free Full-Text Research on the Preparation
احصل على السعر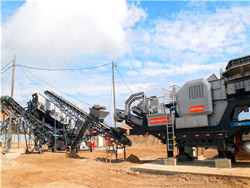
Physical and Mechanical Properties of Aluminum Dross
The 106µm particle size dross brick can serve as acid refractory because its properties compared well with medium-alumina fireclay and exhibits relatively low cold crush strength. The study on the physio-mechanical behavior of aluminum dross has been carried out. The amount of aluminum dross used varied between 50 and 90 wt %, while Aluminum dross recycling. Recycle metal aluminum, Aluminum dross,Aluminum dross pressing, Aluminum slag When processing 50 tons of steel slag rod mill production line in Xinjiang. view more. When processing 40 tons of steel slag tail slag production line in Yuxi. Ball mill is the key equipment for grinding ore after crushing. It isBall Mill, Rod Mill, Ball Press, Aluminum Ash Equipment
احصل على السعر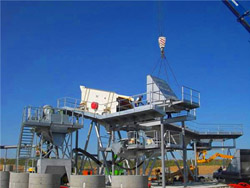
(PDF) Synthesis of Calcium Aluminates from Non-Saline Aluminum Dross
The reactive milling time used was 5 h in a ball mill, for a ball/dross mass ratio of 6.5. from the production of secondary aluminum, of the sintered materials by XRD are in line with the英语网站资料. Contribute to sbmboy/en development by creating an account on .en/ball mill production line of aluminum dross.md at main
احصل على السعر
Characterization and Application of Aluminum Dross as
The modification of aluminum dross resulted in increased surface area (from 0.96 to 68.24 m 2 /g), acidity (from 315 to 748 µmol/g) and thermal stability. Pyrolysis waste cooking oil was used toMill scale and aluminum dross are the industrial wastes from steel and aluminum industries, which have high concentrations of Fe2O3 and Al2O3, respectively. This paper reports the conversion of reducible metal oxides in scale and dross into an alloy via carbothermic reduction at 1550 °C. Scale and dross were mixed with graphite into Metals Free Full-Text Synthesis of Ferroalloys via Mill Scale-Dross
احصل على السعر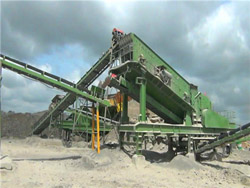
Aluminium dross/soda lime glass waste-derived high-quality
Three batch compositions (GF2.5–7.5) were manufactured from waste glass powders and aluminium dross foaming agents according to the nominal compositions displayed in Table 2. These batches were dry-blended in a planetary ball mill for 30 min, then dry-molded in stainless steel moulds (10ⅹ10ⅹ10 cm 3, interior surface coated with Al dross powder before use in experiments was ball milling and brought to about 45 μm size, using a Fritsch planetary ball mill with stainless steels balls and vials. Ball-to-powder mass ratio corresponds to 30:1, milling time was set in range 15–75 min and was sufficient to obtain Al dross particles size of about 45 μm and to get activatedHydrolysis of aluminum dross material to achieve zero hazardous
احصل على السعر
Research on the Preparation Parameters and Basic
dross was ground to a particle size smaller than 0.074 mm with a ball mill pulverizing machine; then, the pulverized dross was sent for detailed inspection and analysis. Firstly,The materials passing the screen are passed as a slurry through line 22 to subsequent screening in Sweco screen 24, which has a size of about 30 mesh, where the coarse oxides and some aluminum metal are removed through line 26 and are returned to ball mill 14. Since the aluminum particles are generally larger than the aluminum oxide particlesAluminum dross processing Imperial West Chemical
احصل على السعر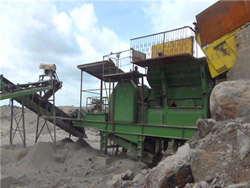
sbm/sbm ball mill steinlien dross separator.md at master
You've already forked sbm 0 Code Issues Pull Requests Packages Projects Releases Wiki ActivityDeep hydrolysis for removing hazardous aluminum nitride (AlN) from secondary aluminum dross (SAD) remains a challenge nowadays. Enhanced hydrolysis of AlN from SAD through a combination of wet-stirred milling and alkaline leaching is investigated in the present study, which has not been reported before. SAD is activated Enhanced Hydrolysis of Aluminum Nitride from Secondary Aluminum Dross
احصل على السعر
Recovery of Valuable Metals and Production of Fe-V
Aluminum dross (AD) is a typical secondary resource solid waste generated as a by-product during the electrolytic aluminum or cast alu-minum production process.14,15 The world alu-minum industry produces approximately 5 million tonnes of AD annually, and around 95% of AD goes to landfill.16 Although recycling tech-In terms of production volume, aluminium is the leading metal in non-ferrous metallurgy. In particular, the recycling of aluminium-containing residues has strongly increased in recent years and will continue to gain importance in the future. Due to the high affinity of aluminium to oxygen, the oxidation of the molten bath is unavoidable, which Studies on the Formation and Processing of Aluminium Dross
احصل على السعر
Life cycle environmental and economic assessment of
Secondary aluminum dross is regarded as a hazardous solid waste in many countries. A coupled life cycle assessment and life cycle costing method was used to evaluate the environmental impact and economic cost of two processes for producing alumina from bauxite and secondary aluminum dross. The results showed that the total
احصل على السعر