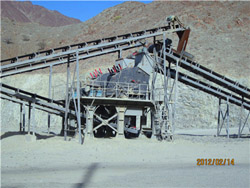
(PDF) Grinding in Ball Mills: Modeling and Process
A ball mill is a type of grinder widely utilized in the process of mechanochemical catalytic degradation. It consists of one or more Tumbling ball mills or ball mills are most widely used in both wet and dry systems, in batch and continuous operations, and on a small and large scale. Grinding elements in ball Ball Mill an overview ScienceDirect Topics
احصل على السعر
An innovative approach for determining the grinding media
Herein, an innovative approach for determining the grinding media system of ball mill based on grinding kinetics and linear superposition principle was proposed. Abstract. The paper presents an overview of the current methodology and practice in modeling and control of the grinding process in industrial ball mills. Basic Grinding in Ball Mills: Modeling and Process Control
احصل على السعر
Investigating grinding mechanisms and scaling criteria in a ball mill
Grinding powders in a ball mill is a complex operation in which many parameters, such as geometrical factors [2], filling ratios [3], powder properties [4] or the The article presents the results of laboratory-scale research on the determination of the impact of ball mill parameters and the feed directed to grinding on its Analysis of process of grinding efficiency in ball and rod mills
احصل على السعر
Grinding in Ball Mills: Modeling and Process Control
Abstract The paper presents an overview of the current methodology and practice in modeling and control of the grinding process in industrial ball mills. Basic Abstract Ball milling is a simple, fast, cost-effective green technology with enormous potential. One of the most interesting applications of this technology in the field of cellulose is the preparation and the chemical Ball milling: a green technology for the
احصل على السعر
Grinding in Ball Mills: Modeling and Process Control
The Effect of Ball Size on the Energy Efficiency of Hybrid High-Pressure Roll Mill/Ball Mill Grinding. Powder Technology, Vol. 105,1999, 199-204. 10.1016/S0032-5910(99)00138-2 Google Scholar 23.Fine grinding in traditional ball mills has not been utilised in the past due to the following perceived disadvantages: •. The mill speed has to be lower than the centrifugal speed of the mill otherwise the whole charge will rotate with the mill body and no grinding will occur. This speed limit fixes the maximum electrical power the mill canFine grinding in a horizontal ball mill ScienceDirect
احصل على السعر
Energy-Efficient Advanced Ultrafine Grinding of Particles
The present literature review explores the energy-efficient ultrafine grinding of particles using stirred mills. The review provides an overview of the different techniques for size reduction and the impact of energy requirements on the choice of stirred mills. It also discusses the factors, including the design, operating parameters, and feed material The grinding process of the ball mill is an essential operation in metallurgical concentration plants. Generally, the model of the process is established as a multivariable system characterized with strong coupling and time delay. In previous research, a two-input-two-output model was applied to describe the system, in which Process Control of Ball Mill Based on MPC-DO Hindawi
احصل على السعر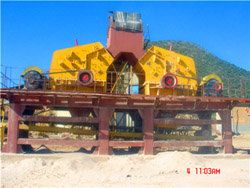
Ball milling: a green technology for the preparation and
The ball mill Ball milling is a mechanical technique widely used to grind powders into ne particles and blend materials.18 Being an environmentally-friendly, cost-effective technique, it has found wide application in industry all over the world. Since this mini-review mainly focuses on the conditions applied for the prep-The Effect of Ball Size on the Energy Efficiency of Hybrid High-Pressure Roll Mill/Ball Mill Grinding. Powder Technology, Vol. 105,1999, 199-204. 10.1016/S0032-5910(99)00138-2 Search in Google ScholarGrinding in Ball Mills: Modeling and Process Control Sciendo
احصل على السعر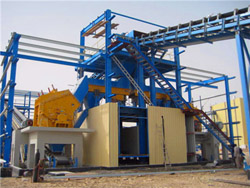
(PDF) DEM Investigation of Discrete Heat Transfer Behavior
This study presented a numerical model for the quantitative assessment of the heat transfer behavior of grinding media inside a ball mill. Effects of various mill speeds, grinding media fillingThe result revealed that the energy required by a ball mill, high-pressure homogenizer and twin screw extruder were 232.5, 43.3, and 5 kWh/kg of biomass, respectively . Kim et al. showed that a large amount of energy was needed by the planetary ball mill for grinding rice straw compared to the attrition mill.Ball milling as an important pretreatment technique in
احصل على السعر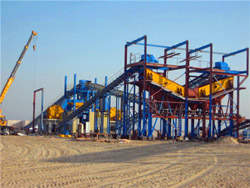
Impact energy of particles in ball mills based on DEM
It has been shown that the grinding of ball mills of different sizes follows the first-order kinetics. Although different collision environments exist with different sizes of mills, impact energy is a useful index that determines the grinding rate. Regardless of the mill size, for a given material, a unique correlation exists between impactVarious devices have been used for processing B powder, including attritor mills, conventional planetary mills, tumbler mills/mixers, vibratory mills, shaker mills, and uni-ball mills [161][162(PDF) Process Engineering with Planetary Ball Mills
احصل على السعر
Ball mill load status identification method based on the
A ball mill is important grinding equipment in a concentrator, and the accurate detection of the load status ensures that the ball mill runs in the best state, which helps optimize the grinding process, ensure the stable operation of the ball mill equipment, and save energy. The current mainstream detection methods cannot easily detect the Currently, the cost of steel balls amounts to 45% of the total cost of grinding materials in ball mills (Lameck, 2005). The remaining costs include energy consumption and ball mill lining. Given a high demand for steel balls for balls mills, these balls are now produced on a mass scale. In effect, manufacturers of steel balls are developing newOn some problems of producing grinding media by cross
احصل على السعر
Energy Use of Fine Grinding in Mineral Processing SpringerLink
Fine grinding, to P80 sizes as low as 7 μm, is becoming increasingly important as mines treat ores with smaller liberation sizes. This grinding is typically done using stirred mills such as the Isamill or Stirred Media Detritor. While fine grinding consumes less energy than primary grinding, it can still account for a substantial part of a mill’s Download. The Planetary Ball Mill PM 100 is a powerful benchtop model with a single grinding station and an easy-to-use counterweight which compensates masses up to 8 kg. It allows for grinding up to 220 ml sample material per batch. The extremely high centrifugal forces of Planetary Ball Mills result in very high pulverization energy and行星式球磨仪PM100--德国RETSCH(莱驰)研磨仪粉碎仪
احصل على السعر
Ball Mill- Principle, Application, Uses, Critical Speed, Diagram
There are several uses of ball mills, which are as follows: I. Grinding: One of the primary uses of a ball mill is for grinding materials. Ball mills are commonly used in the production of cement, silicate products, new building materials, fertilizers, refractory materials, ferrous and non-ferrous metals, and glass ceramics, among others.This study presented a numerical model for the quantitative assessment of the heat transfer behavior of grinding media inside a ball mill. Effects of various mill speeds, grinding media filling, and the number of lifters on heat transfer were studied and verified by comparing the experimental results and the numerical simulations calculated by DEM DEM Investigation of Discrete Heat Transfer Behavior of the Grinding
احصل على السعر
Ball Mill TY Ultrafine Powder Technology
The ball mill is the key equipment for crushing the material after it is crushed. Ball mills are widely used in cement, silicate products, new building materials, refractory materials, fertilizers, ferrous and non-ferrous metal beneficiation and glass ceramics and other production industries, dry or wet grinding of various ores and otherThe experimental study was carried out in a lab-scale planetary ball mill (Droide®, Shanghai). As shown in Fig. 1, the planetary ball mill contains a disk and four grinding bowls, each with a capacity of 1000 mL.For a clearer explanation, a simplified diagram is used, as shown in Fig. 2.The centers of rotation and revolution are O r and O Investigation of the ball wear in a planetary mill by DEM simulation
احصل على السعر
Effects of grinding aids on model parameters of a cement ball mill
This research focuses on investigating the effects of the three different grinding aids, consisting of a mixture of amine, glycol and polyol in different ratios, on the model parameters of a two-compartment cement ball mill and an air classifier. Within the content of this work, sampling campaigns were organized around a cement grinding
احصل على السعر