
Portland cement
Portland cement is the most common type of cement in general use around the world as a basic ingredient of concrete, mortar, stucco, and non-specialty grout. It was developed from other types of hydraulic lime in England in the early 19th century by Joseph Aspdin, and is usually made from limestone. It is a fine powder, produced by heating limestone and clay minerals in a kiln to form clinker, grindFrank Bullerjahn a,Jørgen Skibsted b,Mohsen Ben Haha a Add to Mendeley https://doi/10.1016/j.jcou.2020.02.015 Get rights and content Abstract CO2 mineralisation of Portland cement: Towards understanding
احصل على السعر
The Cement Manufacturing Process Thermo Fisher
Cement manufacturing is a complex process that begins with mining and then grinding raw materials that include limestone and Portland cement, binding material in the form of a finely ground powder, usually gray, that is manufactured by burning and grinding a mixture of Portland cement Manufacturing, Composition, Uses
احصل على السعر
11.6 Portland Cement Manufacturing U.S. Environmental
11.6.1 Process Description1-7 Portland cement is a fine powder, gray or white in color, that consists of a mixture of hydraulic cement materials comprising primarily calcium Initially, Portland cement was manufactured from naturally occurring clay-rich limestone deposits having the proper CaO:SiO 2 ratio and minor element concentrations. However, Portland cement mineralogy SpringerLink
احصل على السعر
A life-cycle assessment of Portland cement
In this paper LCA is used to evaluate the environmental impact of four cement manufacturing processes: (1) the production of traditional Portland cement, (2) Production of Portland clinker is inherently associated with CO2 emissions originating from limestone decomposition, the irreplaceable large-scale source of calcium oxide needed. Besides carbon capture and CO2 Mineralization Methods in Cement and Concrete
احصل على السعر
Decarbonising the Portland and Other Cements—Via
Subsequently, Portland cement is produced by grinding the clinker with ~5% of gypsum (calcium sulphate). There are two sources of CO 2 emissions in We report a type of high-magnesium and low-silicon iron ore tailings (IOT) utilized as a raw material replacing clay to produce cement clinkers by conventional sintering process. Properties of the cement clinkers sintered at 1420 °C with different IOT addition, from 0 to 20 wt%, were investigated. The chemical and mineralogical analysis, Preparation and characterization of Portland cement clinker from
احصل على السعر
How Cement Is Made
Concrete is formed when portland cement creates a paste with water that binds with sand and rock to harden. Cement is manufactured through a closely controlled chemical combination of calcium, silicon, aluminum, The cement industry confronts significant challenges in raw materials, energy demands, and CO2 emissions reduction, which are global and local environmental concerns. Life cycle assessment (LCA) has Environmental Impact Analysis of Portland Cement
احصل على السعر
Monitoring early-age hydration and setting of portland cement
In this research, the feasibility of this method in monitoring the early-age hydration and setting process of Portland cement paste was explored. Experiments and observations on the conductance signatures obtained from the embedded piezoelectric transducers inside the cement pastes with two different water-to-cement (w/c) ratios The current overarching global environmental crisis relates to high carbon footprint in cement production, waste plastic accumulation, and growing future energy demands. A simultaneous solution to the above crises was examined in this work. The present study focused on decarbonizing the calcination process of the cement making Decarbonising the Portland and Other Cements—Via
احصل على السعر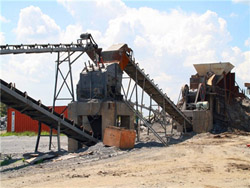
Reducing Environmental Impacts of Cement and Concrete
Portland Cement Manufacturing. Concrete is typically made up of 41% crushed rock, 26% sand, 16% water, 11% portland cement, and 6% entrained air. When combined, the cement and water form a slurry that flows between the aggregate and cures through a “hydration” process into a solid, rock-like mass.The cement industry is facing numerous challenges in the 21st century due to depleting natural fuel resources, shortage of raw materials, exponentially increasing cement demand and climate linked environmental concerns. Every tonne of ordinary Portland cement (OPC) produced releases an equivalent amount of carbon dioxide to Recent Progress in Green Cement Technology Utilizing Low-Carbon
احصل على السعر
Are You Ready for the New MACT Requirements for Portland Cement
On December 20, 2012, EPA finalized amendments to the agency’s air toxics rules for Portland cement manufacturing. The rules call for dramatic reductions of mercury, acid gases, particulate matter (PM) and total hydrocarbons from cement kilns and continued monitoring to ensure compliance. The rule applies to both existing and new Currently, the Max Myanmar Cement Plant, which is the focus of this study, produces Ordinary Portland Cement (OPC) following the process outlined above. It has a capacity of 2100 t d −1 and uses electricity from a 13 KV national grid line, which is sourced from hydropower.Life cycle assessment of a cement plant in Naypyitaw, Myanmar
احصل على السعر
Hydration Mechanism of Portland Cement Prepared from
The results of experiments show that the hydration mechanism is similar to ordinary Portland cement. The hydration process can be divided into five stages: (I) initial period; (II) induction period; (III) acceleration period; (IV) deceleration period; (V) final period And the hydrates are basically the same as Portland cement, mainly containing the The procurement of high-quality aggregates is a global problem. In Chile, mining companies are in the process of developing massive underground projects that require the extensive use of Portland cement concrete (PCC), approximately 60%–75% of which is aggregate. Currently, mining projects transport all the required aggregate to the ScienceDirect Sustainable decision-making through stochastic
احصل على السعر
Portland cement Michigan State University
Portland cement is not a brand name, but the generic term for the type of cement used in virtually all concrete, just as stainless is a type of steel and sterling a type of silver. Aspdin's quest for a manufactured counterpart to natural or Roman cement a crude formulation of lime and volcanic ash used as early as 27 BC led to his discovery and patent of For the latter, in comparison to the clinkerization process of Portland cement where 1450 °C is normally required, the operation temperature can be reduced to 1250 °C for CSA cement [19]. Such a temperature difference would also contribute to a reduction of up to 0.04 tons of CO 2 per ton of CSA cement production.Recent progress and technical challenges in using calcium
احصل على السعر
All You Want to Know about Portland Cement and Its Process
Ordinary (Portland cement Type 1): Common or general-purpose cement for construction works, such as building bridges, reservoirs, culverts, sewers and railway structures, and tanks. Modified (Portland cement Type 2) : General use, especially when moderate sulfate resistance or moderate heat of hydration is required.In fact, 1 t of ordinary Portland cement can consume more than 1.5 t of raw materials and 2.93–6.28 GJ of thermal energy, besides 65 to 141 kWh of electrical energy (Huntzinger and Eatmon, 2009, Madlool et al., 2011, Valderrama et al., 2012). Cement production involves the mining of raw in cement manufacturing process. JLife cycle assessment of the production of cement: A Brazilian
احصل على السعر
Research of technological properties of cement slurries based on
Dependence of dynamic shear stress on shear rate for solutions based on Portland cement and magnesia cement The study found that over time at the same rotational speeds, the shear stressesMixing of raw materials: The processes used for the manufacture of portland cement can be classified as dry and wet. In dry process. The raw materials are first reduced in size of about 25mm in crushers and Crushed material is ground to get fine particles into ball mill or tube mill. Each material after screening is stored in a separate Manufacture Of Portland Cement Process Flow chart civil
احصل على السعر
Life cycle carbon footprint measurement of Portland cement and
Portland cement and ready mix concrete were selected as examples in this study to demonstrate the the GHG emissions during the cement manufacture process were calculated as 0.950 kg CO 2-e per kilogram of clinker produced and 0.917 kg CO 2-e per kilogram of JEMAI (2011) Mining—limestone. Carbon Footprint of ProductsProduction of Portland clinker is inherently associated with CO2 emissions originating from limestone decomposition, the irreplaceable large-scale source of calcium oxide needed. Besides carbon capture and storage, CO2 mineralization is the only lever left to reduce these process emissions. CO2 mineralization is a reversal reaction to CO2 Mineralization Methods in Cement and Concrete Industry
احصل على السعر
Implementing Sustainable Cement Production Methods: Two Key
In fact, the Portland Cement Association (PCA), the premier policy, research, education and market intelligence organization serving America’s cement manufacturing, recently stated, “America’s cement producers have a strong culture of innovation that has led to gains in energy efficiency and new sustainable manufacturing
احصل على السعر