
Energy and exergy analyses for a cement ball mill of a new
Nowadays, ball mills are used widely in cement plants to grind clinker and gypsum to produce cement. In this work, the energy and exergy analyses of a cement The work herein presented analyses an existing failure in a ball mill of a cement production line. • The failure is recurrent and responsible for reducing the period Failure analysis of a ball mill located in a cement’s
احصل على السعر
Optimization of Cement Grinding Operation in
Several energy efficient options for cement grinding are available today such as vertical roller mills, roller presses (typically in combination with a ball mill), and clinker pre-grinders with ball mills. Ball mills have been the The comminution efficiency of a HPGR is better than ball mills such that it consumes 30–50 % of the specific energy as compared to a ball mill. Four circuit configurations of HPGR can be used in grinding of Energy-Efficient Technologies in Cement Grinding
احصل على السعر
Modeling of closed-circuit ball milling of cement clinker via a
Ample experimental data on full-scale closed-circuit cement ball mills reported by [14] indicated that classification performance worsened when an air classifier The traditional means for cement grinding was using ball mills. A ball mill is essentially a rotating drum filled to a certain level with grinding media. For cement, the grinding media almost always consist of Cement grinding considered International
احصل على السعر
Ventilation Prediction for an Industrial Cement Raw Ball
One of the most critical variables in the cement ball mills is ventilation. A mixture of hot and recycled air would deliver and dry the powder in a cement ball mill as Fatahi, R. et al. Ventilation prediction for an Industrial Cement Raw Ball Mill by BNN—A “Conscious Lab” approach. Materials (Basel). 14, 3220 (2021).Modeling of energy consumption factors for an industrial cement
احصل على السعر
BALL MILLS Ball mill optimisation holzinger
Ball mills and grinding tools Cement ball mills are typically two-chamber mills (Figure 2), where the first chamber has larger media with lifting liners installed, providing the coarse grinding stage, whereas, in the second chamber, medium and fine grinding is carried out with smaller media and classifying liners.the data were collected from one of the Raw Material ball mill circuits (line 1) of the Ilam cement plant (Figure1). This plant has 2 lines for cement production (5300 t/d). The ball mill has one component, 5.20 m diameter, and 11.20 m length with 240 t/h capacity (made by PSP Company from Prerˇ ov, Czechia).Ventilation Prediction for an Industrial Cement Raw Ball
احصل على السعر
Failure analysis of a ball mill located in a cement’s
It is divided into two chambers: the first is 3.75 m long, with a maximum ball diameter of 80 mm and a density of 30%; the second chamber is 8.675 m long, with a maximum ball diameter of 40 mm and a maximum load volume of 27.7%. The resulting cement production is 45 tons per hour. The mill under analysis has four maintenance The cement ball mill is a kind of cement grinding mill.It is mainly used for grinding the clinker and raw materials of the cement plant, and also for grinding various ores in metallurgical, chemical, and electric power enterprises.It has the characteristics of strong adaptability to materials, continuous production, a large crushing ratio, and easy to adjust the fineness Cement Ball Mill Cement Grinding Machine Cement Mill
احصل على السعر
(PDF) Effects of Mill Speed and Air Classifier Speed on
Optimum performance of ball mill could potentially refine Blaine fineness, thereby improving the cement quality. This study investigates the effects of separator speed and mill speed on BlaineThe efficiency of fine grinding in the second compartment is largely controlled by the size of grinding balls. Due to limitation of the mill’s rotational speed, the smallest ball size is usually restricted to about 15 mm. Cement grinding using stirred mills (Pilevneli and Azizli, 1999) indicates that using smaller media (5–8 mm rangeCement grinding optimisation ScienceDirect
احصل على السعر
Cement Finish Milling (Part 1: Introduction & History)
Ball Mills. Although ball mills were first introduced in the 1860’s, the main progress was made during the 1870’s to 1900’s in Germany, where its growing cement and chemical industriesIn order to install the liners, you need to ensure that the surface of the cylinder is clean and free from debris. Then, you can prepare the surface of the cylinder for installation. You shouldHow to do ball mill liner? LinkedIn
احصل على السعر
A cement Vertical Roller Mill modeling based on the
The model considers the mill equivalent to several grinding stages with internal classification in series, assuming the cement mill model was equivalent to a thoroughly mixed ball mill [14]. Only a few studies have been conducted on the simulation of VRMs [15]. Wang, Chen et al. 2009 use a matrix model to replicate the grinding process The cement ball mill in cement plant is usually divided into 2-4 silos, the most representative of which are the “new type of high fineness cement ball mill” and “open flow high fineness cement ball mill”. There are three cement processing circuits. 1. Open circuit grinding The ball mill in the cement plant for open circuit grindingCement Ball Mill JXSC Machine
احصل على السعر
Ventilation Prediction for an Industrial Cement Raw Ball Mill
This plant has 2 lines for cement production (5300 t/d). The ball mill has one component, 5.20 m diameter, and 11.20 m length with 240 t/h capacity (made by PSP Company from Přerov, Czechia). The mill’s rotation speeds are mainly constant (14 rpm), and there is approximately a fixed one-year period of changing liners.(1) Advantages of ball mill in cement processing. The ball mill has advantages in the production of cement and clinker. Because the particle shape produced is approximately spherical, it is beneficial to the unique advantages of raw meal calcination and "hydration hardening" of cement. This is the main reason why clinker mills still mostly useComparison of advantages and disadvantages of ball mill and vertical mill
احصل على السعر
cement ball mill LinkedIn
A ball mill is a cylindrical device used in grinding materials like ores, alloys, coal, coke, fibers, cement clinker, refractory material, ceramics, limestone, quartz, gypsum, metal oxides, slagClosed-circuit ball mills have been operated for cement milling for decades [[7], [8], [9]].Fig. 1 shows the process flow of a closed-circuit, two-compartment cement ball mill. The closed-circuit operation helped to reduce overmilling of particles [10], resulting in lower specific power consumption [11] in comparison with open-circuit operation, where Modeling of closed-circuit ball milling of cement clinker via a
احصل على السعر
Technological Energy Efficiency Improvements in Cement Industries
The cement industry is highly energy-intensive, consuming approximately 7% of global industrial energy consumption each year. Improving production technology is a good strategy to reduce the energy needs of a cement plant. The market offers a wide variety of alternative solutions; besides, the literature already provides reviews of Raw materials chemistry. Cement manufacture requires a source of calcium, such as CaCO 3 or CaMg (CO 3) 2, which comprises almost 80–90% of the total and the rest is iron oxide (Fe 2 O 3, Fe 3 O 4), quartz (SiO 2), and clay/bauxite (Al-silicates) (Aïtcin and Flatt Citation 2015; Hewlett Citation 2003; Peray and Waddell Citation 1986).Traces of Na 2 O, K 2 O, Full article: An overview of alternative raw materials used in cement
احصل على السعر
Operational parameters affecting the vertical roller mill
A cement Vertical Roller Mill modeling based on the number of breakages. Vertical roller mills (VRM) are widely used to grind, dry, and select powders from various materials in the cement, electric power, metallurgical, chemical, and nonmetallic ore industries. For the sectors above, the VRM is a powerful and energy-intensive grinding The aim of this study is to evaluate the effect that the size of grinding media exerts on ferronickel slag milling efficiency and energy savings. A series of tests were performed in a laboratory ball mill using (i) three loads of single size media, i.e., 40, 25.4, and 12.7 mm and (ii) a mixed load of balls with varying sizes. In order to simulate the Effect of Grinding Media Size on Ferronickel Slag Ball Milling
احصل على السعر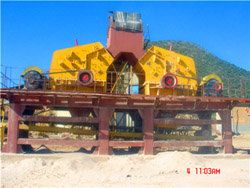
15000-HP gearless ball mill drive in cement-why not! IEEE
Over recent years, there has been a clear trend toward higher capacity cement production units. Five to ten years ago 2500 tons per day was large. Nowadays in Asia, lines are built for 10000 tons per day. The development of ball mill grinding units has not shown the same trend; output and ratings have remained more or less constant perhaps due to the The cement mill is either a Ball mill with two chambers or Vertical roller mill with inbuilt classifier. Material is ground till desired Blaine is achieved and then final product is stored in concrete silos for further blending. Ball mills have been used as the main grinding tool for cement production for over 100 years. Although easy toReview on vertical roller mill in cement industry & its
احصل على السعر