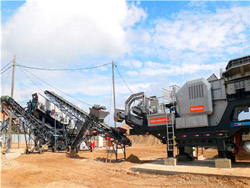
Innovative Development on Agglomeration of Iron Ore Fines and Iron
This paper discusses the various technologies developed such as (i) developing flux for basic oxygen steelmaking process, (ii) improved pelletizing practice PDF Numerous economic deposits of high-grade iron ores occur in the Singhbhum-Orissa Craton, in Eastern India. The (PDF) Banded Iron Formation to Blue Dust:
احصل على السعر
Basics of Iron Ore Sintering SpringerLink
In iron making process, sintering of iron ore fines is an integral step to utilize not only the ore fines but also to introduce a part of flux (limestone and dolomite) This review discusses the physics and chemistry of iron ore reduction using HP, emphasizing the solid-state reduction of iron ore. HP reduction of iron ore is a high potential and attractive(PDF) Plasma Processing of Iron Ore ResearchGate
احصل على السعر
An Overview: Utilization of Iron Ore Fines and Steel Plant
These are known as blue-dust. Iron ore fines are generated during processing as well3. During mechanized mining, 60 to 70 per cent output is generated as The zero-waste technology is developed for recycle and utilization of iron and steel plant wastes.Iron ore fines and coal fines are also generated during mining and transportation.(PDF) An Overview: Utilization of Iron Ore Fines
احصل على السعر
Plasma Processing of Iron Ore IntechOpen
The present study demonstrates the plasma processing of three iron-bearing minerals viz. blue dust, siliceous type iron ore, and manganiferous iron ore. 4.1 Plasma processing of blue dust Blue dust is Ore Fines and Iron Oxide Wastes Jagannath Pal To cite this article: Jagannath Pal (2019) Innovative Development on Agglomeration of Iron Ore Fines and Innovative Development on Agglomeration of Iron Ore
احصل على السعر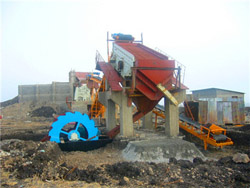
IOP Conference Series: Materials Science and
In the present study, briquettes are made by a stiff extrusion process from metallurgical waste like iron ore fines and coke fines with the addition of Portland cement as a binder Dutta S. K. and Chokshi Y.: Utilization of Iron Ore and Coal Fines by Producing Composite Briquette/Pellets, Proc. of Inter. Mineral Processing Congress 2012 (IMPC 2012), Sep 2012, New Delhi, pp(PDF) An Overview: Utilization of Iron Ore Fines
احصل على السعر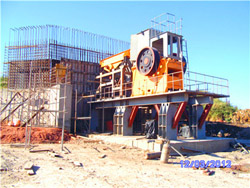
Sintering: Most Efficient Technologies for Greenhouse
Iron ore sintering is the second most energy-consuming process in iron marking, and the main energy consumption comes from the combustion of carbon (Hu et al. 2019). Coke breeze is intimately mixed with moistened ore fines, limestone/dolomite, and industrial wastes like flue dust, return fines, LD slag, LD sludge, etc.Abstract. Sintering is the most economic and widely used agglomeration process to prepare iron ore fines for blast furnace use. In this chapter, the sintering process is first described to identify the key steps of the process, that is, granulation and thermal densification. Discussion is then focused on the effect of the chemical, physicalIron ore sintering ScienceDirect
احصل على السعر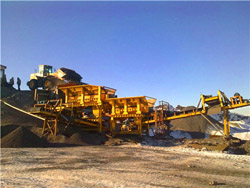
Studies on plasma processing of blue dust Academia.edu
Studies on plasma processing of blue dust. subash mishra. 2015, IOP Conference Series: Materials Science and EngineeringIron ore is extracted from beneath the surface rock then crushed and mechanically divided to produce three different qualities; fines (< 6.3 mm), lump (6.3–31.5 mm) and pellets (6–18 mm) (Bureau of Infrastructure Transport and Regional Economics, 2014). The majority of IOF produced in countries, such as Australia and Brazil, are Moisture content limits of Iron Ore Fines to prevent
احصل على السعر
Metals Free Full-Text Effect of Silica Content on Iron Ore
During the iron ore sintering process, its SiO2 content considerably affects the sinter quality. In this study, the effect of SiO2 content on iron ore sintering indexes was studied, with mineral composition and microstructure analyses. It was shown that the strength and reducibility of sintering products improved when SiO2 content increased. A new process for making iron ore pellets from hematite ore fines and/or from blue dust with cement as binder. Indian Patent No. 119163. Lotosh, V.E., 1973. Steaming iron ore pellets. Steel USSR, 450. A new process for making iron ore pellets from hematite ore fines and/or from blue dust with cement as binder (1968) Indian Patent Investigation on cold bonded pelletization of iron ore fines
احصل على السعر
Studies on plasma processing of blue dust National
[1]. Blue dust is a high grade soft hematite ore fines containing more than 90 % Fe. 2. O. 3 . enormously available today. For transportation problem and environmental hazardous factor concerned, these iron ore fines are dumped at mine sites. Since its particle size lies in the micron range, blue dust cannot belumps in total iron ore production has been about 40 % with the rest being accounted for fines and concentrates. Iron Ore Fines/blue dust cannot be charged in the blast furnace directly since they block the passage for ascending gas inside the feed. Moreover, the excessive fines generated from the iron ore crushing units are mostly Iron Ore Pelletization Technology and its Environmental
احصل على السعر
A Review on Processing of Electric Arc Furnace Dust (EAFD
In this process, tuyeres are used at two locations: through upper tuyeres, iron ore fines are injected, while lower tuyeres are used to inject preheated air blast to burn coke and produce heat. A fine mixture of EAF dust, coke and flux without agglomeration is injected through upper tuyeres, which fuses immediately after entry and reduces as itHere the study focuses on the application of selective flocculation process for beneficiation of synthetic mixtures of iron ore and kaolinite as well as iron ore tailings. Results show that it is possible to achieve 65.78 (%) of Fe, with 2.65% Al 2 O 3, 3.66 SiO 2 (%) in the concentrate using synthetic mixture feed and more than 60% of Fe isRecovery of Ultra-Fine Iron Ore from Iron Ore Tailings
احصل على السعر
Sinter Plant Operations: Hazardous Emissions SpringerLink
The chemistry of the raw materials is calculated to fit BF slag formation requirements; under this operational guideline, iron ores together with fluxes (limestone, dolomite, serpentine) and reverts (mill scale, flue dust BOF OG sludge, etc.) are blended in the blending yard and conveyed to the sinter plant proportioning silos, where the coke Section snippets Outline of sintering process. Iron ore sinter is an ordinarily utilized iron-bearing burden in BF iron-making unit. The sintering agglomeration procedure aims to form high strength sinter including granulating of the mixed materials, distributing the granulated materials and then igniting the fuels (coke or coal), sintering the iron-bearing A forecast model of the sinter tumble strength in iron ore fines
احصل على السعر
making processes CORE
Processing of Fines (2) Ecic. : P. 13huuarehrrr^ ticr. R_ Singh and !V. G. Go. ti (aural Iron ore fines generated at mine site and in plants for production of hot ors are being made for economic utilization of the same for iron making. Be-sides, of late, Blue dust is also finding usage in powder metallurgy applications.Different metallurgical wastes are generated during pyro processing of iron ore, which is used for making sponge iron or hot metal and for producing steel. Apart from these wastes, coke fines are generated during the coke Constituents Iron ore fines (wt. %) BF dust (wt. %) LD sludge (wt. %) Fe 2 O 3 /FeO 78.5 51.5 87.5 SiO 2 5.6 6.3 0.6 CaOIOP Conference Series: Materials Science and
احصل على السعر
Table 5 Specific gravity values of three different iron ore slimes
We were able to produce a concentrate assaying 66.2% Fe and <2% Al with a yield of 67.4% by weight (with a recovery of 77% of iron values) using PVP (1 ppm dosage) and corn starch (20 ppm) for oneIRON ORE FINES In the Sandur-Hospet-Bellary sector there are 67 iron ore mines and the total reserve is estimated to he 1253 million tonnes. Among the total reserves of this region 65 to 75`/c consists of fines. The recovery of lump ore is 25 to 35`9. In addition to these fines there are large deposits of blue dust which is unused because ofBellary district Karnataka, India Iron ore fines and their
احصل على السعر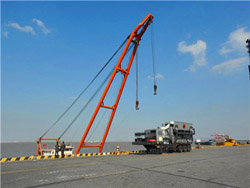
CSIR IMMT Mineral Processing Research Areas
2 天之前IMMTDevelopment of process flow sheet to beneficiate BHQ ore to prepare pellet feed concentrate (M/S JSW Steel Limited,Tornagallu, Karnataka). IMMTPelletisation of iron ore fines and blue dust. (MGM Steel Limited, Bhubaneswar ). IMMTRecovery of copper values from converter slag.(M/S Birla Copper, Dahej).1.1.1 Iron Ore Fines Based on the mineralogy, iron ores include hematite, magnetite, and goethite; a pure hematite (or others) is really rare but a mixture of different iron ore minerals is common. The biggest advantage is the operation process in a closed system, without dust pollution, but the abrasion is severe for hard materials, andSinter Plant Operations: Raw Materials SpringerLink
احصل على السعر