
Development of a Novel Grinding Process to Iron Ore
Modern iron ore pelletizing process operations may be divided into two main process sections: feedstock preparation and agglomeration processes. In most plants, the required particle size distribution (PSD) is obtained through the wet ball mill circuit.Keywords: Wet grinding; iron ore tailings; particle characteristics; mineral admixture. 1 Introduction. Iron Ore Tailings (IOTs) refer to the solid waste associated with the process Different Effects of Wet and Dry Grinding on the Activation of Iron Ore
احصل على السعر
Impact of ball filling rate and stirrer tip speed on milling iron ore
The wet grinding of iron ore powder was investigated using a stirred media mill. In this study, the fitting degree of four cumulative undersize distribution functions Most of the high-grade hematite iron ores are typically subjected to simple dry processes of crushing and classification to meet the size specifications required for Comminution and classification technologies of iron ore
احصل على السعر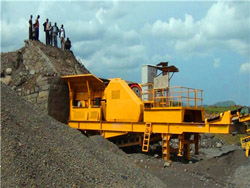
Iron ore beneficiation: an overview ScienceDirect
Dry processing of iron ore: In dry processing of iron ore, ROM is generally crushed below 40 mm through three-stage crushing and thus segregated by screening Herein, micro iron ore tailings (micro-IOTs) were prepared by wet-grinding and applied to improve sulphoaluminate cement (SAC) performance. The physicochemical properties of Preparation of Micro-Iron Ore Tailings by Wet-Grinding and
احصل على السعر
Simulation of wet ball milling of iron ore at Carajas, Brazil
Simulation of wet ball milling of iron ore at Carajas, Brazil ScienceDirect Abstract Introduction Section snippets References (22) Cited by (41) International open access • Green shift significantly increases the demand for the raw materials. • There is a prominent need to reduce water use in the production of primary Towards waterless operations from mine to mill ScienceDirect
احصل على السعر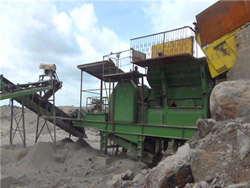
Optimization of Solids Concentration in Iron Ore
The paper demonstrates the application of this methodology to optimize solids concentration in ball milling of an iron ore from Brazil. The wet grinding experiments were conducted in bench An iron ore mill relies on the grinding and impact of grinding balls to complete iron ore crushing. The operating process of an iron ore mill is as follows: first, Friction and wear of liner and grinding ball in iron ore ball mill
احصل على السعر
Wet ball milling of niobium by using ethanol, determination
The wet milling process is the main technique used for commercial production 9. In ancient times, solvents, e.g., ethanol has been used during the milling process to make metal flakes 10. TheTo cite this article: Iman Mor adi & Mehdi Irannajad (2023): Effect of wet ball milling on copper ore flotation by fractal geometry,Separation Science and Technology,DOI: 10.1080/01496395.2023(PDF) Effect of wet ball milling on copper ore flotation by
احصل على السعر
Friction and wear of liner and grinding ball in iron ore ball mill
To understand the friction and wear of working mediums in iron ore ball mills, experiments were conducted using the ball cratering method under dry and wet milling conditions, which mimic the operating conditions in ball mills. The liner sample is made of Mn16 steel, the ball had a diameter of 25 mm and was made of GCr15 steel, and the iron Keywords Pelletizing .Agglomeration .HPGR .Milling 1 Introduction Modern iron ore pelletizing process operations may be divid-ed into two main process sections: feedstock preparation and agglomeration processes. In most plants, the required particle size distribution (PSD) is obtained through the wet ball mill circuit.Development of a Novel Grinding Process to Iron Ore
احصل على السعر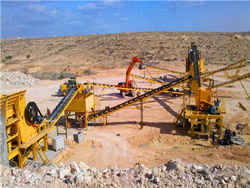
Towards waterless operations from mine to mill ScienceDirect
Magnetic separation is often carried out as a wet process but there are numerous examples of dry magnetic separation in the mineral processing industry, especially in iron ore and coal beneficiation (Andre et al., 2019, Bunting, 2022, Miceli et al., 2017, Tripathy et al., 2017, Zong et al., 2018). Other example applications include the The grinding process for all the three iron ores is carried out individually in Bond’s ball mill and the total retention time taken by each iron ore sample is calculated. The present investigation focuses on utilizing the calculated retention time of the iron ore as a standard grinding reference time to the laboratory ball mill for optimizingEstimation of Grinding Time for Desired Particle Size
احصل على السعر
Different Effects of Wet and Dry Grinding on the
Wet grinding; iron ore tailings; particle characteristics; mineral admixture 1 Introduction Iron Ore Tailings (IOTs) refer to the solid waste associated with the process of iron concentrate extraction from iron ore and are an important source of environmental pollution [1,2]. Approximately 5 billion tons of IOTs are currently present in ChinaImportant advances have been made in the last 60 years or so in the modeling of ball mills using mathematical formulas and models. One approach that has gained popularity is the population balance model, in particular, when coupled to the specific breakage rate function. The paper demonstrates the application of this methodology to Optimization of Solids Concentration in Iron Ore Ball Milling
احصل على السعر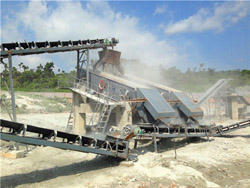
Iron Ore Processing, General SpringerLink
Iron ore handling, which may account for 20–50% of the total delivered cost of raw materials, covers the processes of transportation, storage, feeding, and washing of the ore en route to or during its various stages of treatment in the mill.. Since the physical state of iron ores in situ may range from friable, or even sandy materials, to monolithic Different milling conditions, such as wet or dry, and use of different grinding media have a great impact on the flotation performance of sulphide minerals. In the present study, the effects of wet and dry grinding and the use of different grinding media, such as mild steel (MS) and stainless steel (SS), were investigated on a Cu-sulphide ore. Effects of Different Grinding Media and Milling Conditions
احصل على السعر
Mineral processing milling
Iron Ore 0.20 Lime (industrial applications such as detergents) 0.10 China clay 0.002 Alumina 0.005 Table 3: Material Particle Size a semi-autogenous mill). The process can be carried out wet or dry. Removal of the final product can be carried out using air (where the process is dry) removing only the fines.Hydrocyclone overflow is then sent to the thickeners. The slurry is thickened in the thickener and pumped to the tailings dam. Wet-processing flowsheet of wet plant of Noamundi iron ore mines, Tata Steel Ltd is depicted in Fig. 2.10. Download : Download full-size image; Figure 2.10. Wet plant process flowsheet of Noamundi iron ore mines.Iron ore beneficiation: an overview ScienceDirect
احصل على السعر
Different Effects of Wet and Dry Grinding on the
Wet grinding; iron ore tailings; particle characteristics; mineral admixture 1 Introduction Iron Ore Tailings (IOTs) refer to the solid waste associated with the process of iron concentrate extraction from iron ore and are an important source of environmental pollution [1,2]. Approximately 5 billion tons of IOTs are currently present in China1. Introduction. Iron ore pellets are one of the significant sources of iron for iron and steel making due to their superior metallurgical performance, low energy consumption, and less emission of environmentally harmful dust and gases during the production process [1], [2], [3].The two primary raw materials for pellet production are Mechanism of magnetite iron ore concentrate morphology
احصل على السعر
Existing and New Processes for Beneficiation of Indian Iron
The iron ore industries of India are expected to bring new technologies to cater to the need of the tremendous increase in demand for quality ores for steel making. With the high-grade ores depleting very fast, the focus is on the beneficiation of low-grade resources. However, most of these ores do not respond well to the conventional Flotation of Iron Ores: A Review. A tremendous amount of research has been done on refining the flotation process for iron ore and designing the reagents which go into it. This paper reviews the industrial practices and fundamental research surrounding iron ore flotation. The advantages and disadvantages of direct flotation, cationic reverseFlotation of Iron Ores: A Review: Mineral Processing and
احصل على السعر
Simulation of wet ball milling of iron ore at Carajas, Brazil
Companhia Vale do Rio Doce (CVRD) is a world leader in production of iron ore, from its deposits in Brazil. It registered a profit of about $5 billion during 2005, more than a 60% increase from 2004, from sales of $16 billion. This resulted from increased prices of iron ore products, 71.5% higher for lump ore and 86% for pellets, plus increasesThe feed samples of X, Y, and Z iron ores were ground in the BBM (ball mill refers to a BBM of size 300 mm × 300 mm with smooth liners) to identify the PSD, BWI, and RT of each ore. Grinding experiments were conducted according to Bond’s standard test procedure [].For each iron ore sample, the RT taken to produce 250% circulating Investigation on Iron Ore Grinding based on Particle Size Distribution
احصل على السعر
Impact of ball filling rate and stirrer tip speed on milling iron ore
1. Introduction. Iron ore plays an important role in industrial raw materials worldwide. Nearly 97.5% of iron ore resources, including siderite, limonite, and oolitic hematite, etc. are typically low-grade iron ores and difficult to develop in China [1].As the Chinese economy develops, the demands for steel products grow, and the refractory iron Option 2 has an additional grinding and magnetic separation stage compared to Option 1 and is considered to be simple for design and operation. The final milling stage is carried out using energy-efficient stirred mills. Steel grinding media usage significantly increases the operating cost. Option 3.Eco-efficient and cost-effective process design for magnetite iron ore
احصل على السعر