
How Cement is Made Cement Manufacturing Process
There are six main stages of the cement manufacturing process. Stage 1: Raw Material Extraction/Quarry The raw cement ingredients needed for cement Usually, the basic cement manufacturing process is divided into three production stages: raw material preparation, clinker production, and cement grinding Analysis of material flow and consumption in cement production process
احصل على السعر
Modernizing cement manufacturing in China leads to
The cement manufacturing process mainly includes four steps: resource extraction, raw material preparation, clinker calcination, cement grinding 17,18, and fossil In this chapter an introduction of widely applied energy-efficient grinding technologies in cement grinding and description of the operating principles of the related equipments and comparisons over Energy-Efficient Technologies in Cement Grinding
احصل على السعر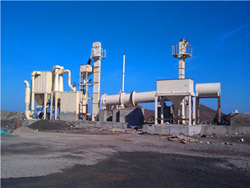
Sustainable cement production—present and future
Grinding efficiency is important for all comminution processes in a cement plant, i.e. raw material, coal and cement grinding. While the requirements are basically The increasing demand for “finer cement” products, and the need for reduction in energy consumption and green house gas emissions, reinforces the need for Cement grinding optimisation ScienceDirect
احصل على السعر
Process technology for efficient and sustainable cement production
While vertical roller mills (VRMs) are predominantly used for raw material grinding, different types of grinding systems are used for the finish grinding of cement. Within the study, it was aimed to optimize both the energy utilization and the product quality of a conventional cement grinding circuit during CEM I 42.5R cement Energy and cement quality optimization of a cement grinding circuit
احصل على السعر
Grinding process is a critical stage in cement production
• Process Dynamics: Cement grinding is a dynamic process influenced by various factors such as feed rate, mill ventilation, grinding pressure, and material moisture content. Changes in these process variables can impact the fineness control. Our cement plant consumes this industrial waste and in turn also preserves the natural resourcesJanuary 16, 2023. By. admin. Dr SB Hegde, Professor, Jain University, Bangalore, talks about pyroprocessing and the role of preheater, rotary kiln and clinker cooler in the cement manufacturing process. In the concluding part of the two-part series, we will learn more about the various factors aiding pyroprocessing. False Air in Pyro Processing.Pyroprocessing and Kiln Operation Indian Cement Review
احصل على السعر
Clinker grinding technology in cement manufacturing
Clinker grinding technology is the most energy-intensive process in cement manufacturing. Traditionally, it was treated as "low on technology" and "high on energy" as grinding circuits use more than 60 per cent of total energy consumed and account for most of the manufacturing cost. Since the increasing energy cost started burning the benefits Cement grinding unit cost. Take the annual output of 600,000 tons of large-scale cement grinding station as an example, there are three common options can be recommended: SCHEME 1: roller press + φ 3.2 ×13m ball mill; SCHEME 2: φ 3.8 ×13m closed mill; SCHEME 3: clinker fine crusher + cement roller press+φ 3.2 ×13m ball mill.Cement Grinding Unit Cement Grinding Plant Cement Grinding
احصل على السعر
Digitization and the future of the cement plant McKinsey
There’s never been a more important time to build resilience into the core of the cement value chain: the cement plant. The cement industry is being hit hard by the COVID-19 pandemic, with global demand for cement expected to decline by 7 to 8 percent in 2020—though these declines have been unevenly distributed across regions. 1 Paul 1 Potential safety hazards in the coal mill system. 1.1 Spontaneous combustion occurs. The process of cement production determines the need to use a large amount of coal. The use of coal is mostlyDISCUSSION ON SAFETY PRODUCTION OF COAL MILLING SYSTEM IN CEMENT PLANT
احصل على السعر
(PDF) Modelling of clinker cooler and evaluation of its
Cement manufacturing requires cooling down of hot clinker at temperature of about 1350o C to temperature lower than 100 o C in a cooling system known as clinker cooler.Processes like grinding, transport of materials and crushing utilize machine drives and account for the majority of electricity consumption, as is evident in the result of the Manufacturing Energy Consumption Survey (MECS) in 1998 presented in Fig. 3.Process heating, by which clinker is made in large kilns, accounts for about 90% of the natural An overview of energy savings measures for cement industries
احصل على السعر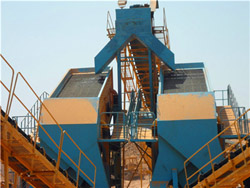
Energy-Efficient Technologies in Cement Grinding IntechOpen
The energy consumption of the total grinding plant can be reduced by 20–30 % for cement clinker and 30–40 % for other raw materials. The overall grinding circuit efficiency and stability are improved. The maintenance cost of the ball mill is reduced as the lifetime of grinding media and partition grates is extended. 2.5.The cement industry is highly energy-intensive, consuming approximately 7% of global industrial energy consumption each year. Improving production technology is a good strategy to reduce the energy needs of a cement plant. The market offers a wide variety of alternative solutions; besides, the literature already provides reviews of Technological Energy Efficiency Improvements in Cement Industries
احصل على السعر
Advanced Process Control (APC) and analytics for
The ABB Ability TM Expert Optimizer (EO) is an APCA solution for controlling, stabilising, and optimising cement and mining processes. Incorporating state-of-the-art optimisation and analytics technologies, the Grinding of clinker consumes power in the range of 2.5 kWh/ton of clinker produced. These and other pyroprocessing parameters make cement production costly. The pyroprocessing process in kilns and A Review on Pyroprocessing Techniques for
احصل على السعر
How does a raw mill work in a cement plant? LinkedIn
Grinding mills for cement plant. A raw mill is a key piece of equipment used in a cement plant to grind raw materials into a fine powder. It works by crushing and grinding materials such ascement ball mill. Application: limestone, clay, coal, feldspar, calcite, talc, iron ore, copper, phosphate, graphite, quartz, slag. Capacity: 0.65-615T/H. The cement ball mill usually can be applied to raw meal grinding or cement grinding. Besides, the cement ball mill also can be used for metallurgical, chemical, electric power, other miningRaw mill Cement Plant, Cement Equipment
احصل على السعر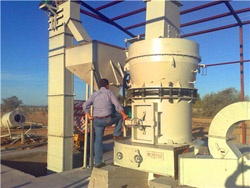
Review on energy conservation and emission reduction
Cement production utilizes a considerable amount of energy which is also responsible for different greenhouse gas emissions.This review aims to help the cement industry to select the best method for improving energy efficiency and emission reduction. Various energy conservation and emission reduction approaches are considered for raw cessfully for many years in cement plants to grind and dry raw materials simultaneously with moisture contents up to 20% by weight. eir production can be as high as 400 tons(PDF) A Review on Pyroprocessing Techniques for Selected
احصل على السعر
Analysis of material flow and consumption in cement production process
The recycle rate of waste gas discharged from the clinker production system is remarkably higher than that of the raw meal and cement grinding system. In the surveyed cement plant, 1.21 t of limestone, 0.09 t of silica, and 5.81 t of air are required to produce one ton of cement (P.O.42.5); meanwhile, 4.79 t of waste gas is discharged into The cement manufacturing process mainly includes four steps: resource extraction, raw material preparation, clinker calcination, cement grinding 17,18, and fossil fuel burning 19.Modernizing cement manufacturing in China leads to
احصل على السعر
Clay calcination technology: state-of-the-art review by the
LOI is a well-known indicator in cement plants and its use for calcination of clay is direct . The calibration of the LOI on a performance-based approach makes this indicator valuable. The conditions of calcination giving the highest strength can be targeted in terms of LOI. On the contrary, the most common grinding process in cement plantsStage 2: Grinding, Proportioning, and Blending The crushed raw ingredients are made ready for the cement-making process in the kiln by combining them with additives and grinding them to ensure a fine homogenous mixture. The composition of cement is proportioned here depending on the desired properties of the cement. How Cement is Made Cement Manufacturing Process
احصل على السعر