
(PDF) Calculating Cutting Force in Grinding
PDF On Jul 4, 2018, Do DUC Trung published Calculating Cutting Force in Grinding Find, read and cite all the research you need on ResearchGate.Under this criterion, an alternative, higher-price grinding media product could be cost-effective if its associated consumption rate is sufficiently lower than the Methodologies for the evaluation of grinding media consumption rates at
احصل على السعر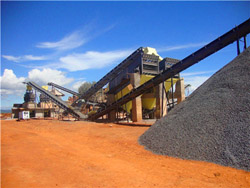
An innovative approach for determining the grinding media
The reduction rate of the coarse fraction (grinding rate, k) was calculated by the grinding kinetic eq. (4). Fig. 4 showed the relationship between ln(R 0 /R t) and The ball milling performance was characterized by grinding rate and power draw. The damping energy of ground particles obtained from DEM simulation was used A DEM based scale-up model for tumbling ball mills
احصل على السعر
Specific Material Removal Rate Calculation in Five-Axis Grinding
Specific material removal rate (MRR) q' q ′ was calculated for five-axis grinding in a virtual machining simulation environment (VMSE). The axis-symmetric tool rate and has not to date been standard-ized (Refs.2–3; 5). This is due to the sig nificantly more complex geometry of tool and gear for both continuous generat Local Simulation of the Specific Material Removal Rate
احصل على السعر
Approach for the Calculation of Cutting Forces in Generating Gear Grinding
Using these values makes it possible to obtain a calculation method for further key values such as the specific material removal rate for generating gear grinding. The wheel position was defined by 3 parameters: the distance between X W and X T (i.e., Δy), the distance between Z W and Z T (i.e., Δx), and the angle that rotated from Z T-axis to Z W-axis around X T-axis (i.e., Δαx).. The 1A1 type grinding wheel geometry was expressed by 3 variable parameters: the thickness B W, the taper angle θ Big data-oriented wheel position and geometry calculation
احصل على السعر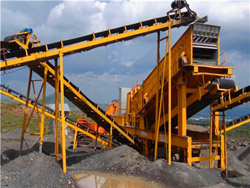
GRINDING FEEDS AND SPEEDS ABRASIVE ENGINEERING
Grinding wheel speeds should be maintalned with-in a range of 5000 to 6500 feet per minute (1525 to 1980 meters per mm), unless special conditions prevall or equipment and wheels designed for substantially higher wheel speeds are used.Su et al. proposed that all grits with the same diameter were distributed randomly and established the grinding force calculation model of a two-dimensional disc wheel. Hegeman optimized the grinding process, simplified the grits into elliptic grits, and established a three-dimensional grinding wheel model. Then, simulations of the grindingEstablishment and Verification of the Cutting Grinding Force
احصل على السعر
Development and Power Calculation of a Grinding
speed of the grinding wheel in different materials. Application of 30KhGSN2A or VT3-1 of the raised quality as the case of a grinding wheel allows to receive break rates to 667,8 and 720,2 m/s accordingly. Taking into account the safety factor of 1.4 we will get the maximum c utting speed of 484. 2 a nd 54 3.0 m /s respectively. 0 100. 200. 300The grinding rate in the X-direction was greater than that in the Y-direction, which led to a more obvious interference of abrasive grains in the X-direction. The calculation method of the material removal rate for grinding effective abrasive grains is Z w ' = (V s ∙N d)/t. During the simulation, under the same material removal rate,Surface topography modeling and analysis of camshaft
احصل على السعر
Thermal Analysis of Grinding ScienceDirect
Thermal damage is one of the main factors which affects workpiece quality and limits the production rates which can be achieved by grinding, so it is especially important to understand the underlying factors which affect the grinding temperatures. From metallurgical investigations of ground hardened steel surfaces reported in 1950 [3], it wasenergy consumption and increased the grinding rate by 1 1.1% for a similar quality of grain grind. Specific energies ranged from 5.5 to 9.5 kWh/ton for hammer thickness(PDF) DESIGN AND EVALUATE OF A SMALL HAMMER MILL
احصل على السعر
The Design of an Infeed Cylindrical Grinding Cycle
Table 1. Experimental setup in infeed cylindrical grinding. The grinding power was measured during the infeed grinding and the results are shown in Figure 20 a. The grinding power in the steady state was 1.6 kW, and a time constant T = 8.2 s was found at the time the power reached 63% of 1.6 kW.Removal rate is proportional to infeed rate, v f, in plunge centerless grinding. For the particular conditions, the optimum workspeed is seen to be given approximately by v w = 0.25 m/s, when grinding with medium carbon steel, AISI 1055, or with gray cast iron. At this workspeed, the infeed rate could be increased up to the maximum powerCenterless Grinding an overview ScienceDirect Topics
احصل على السعر
Force and Temperature Modeling in 5 axis Grinding
Relating the grain-level chip thickness h to the wheel-local material removal rate per unit area m”, grinding force components from chip-formation, plowing and sliding, resolved normal and tangential to the tool surface locally were considered. A new approach to model steady-state workpiece temperatures for small tool-workpiece contact areasThe Grinding ratio is defined as the volume of material removed divided by the volume of wheel wear is calculated using Grinding Ratio = Workpiece removal parameter / Wheel Removal Parameter.To calculate Grinding ratio, you need Workpiece removal parameter (Λ W) & Wheel Removal Parameter (Λ t).With our tool, you need to enter the respective Grinding ratio Calculator Calculate Grinding ratio
احصل على السعر
Modeling and experimental study of grinding forces in surface grinding
Abstract. Grinding forces are composed of chip formation force and sliding force. A new mathematical model of grinding forces in surface grinding is developed in this paper. Effectiveness of this model is proved by comparison of the experimental results and the model calculation results. Chip formation energy can be divided into static chipwork index approximate value is exactly the same as in the first two grinding cycles of. Prepare a sample, the same as for the standard Bond test (grind to 100%. -3.327 mm). Determine the starting(PDF) A quick method for bond work index
احصل على السعر
Impact energy of particles in ball mills based on DEM simulations
Alternatively, establishing a correlation between impact energy and grinding rate provides a way of eliminating the simulation of fine particles. In the previous studies [17, 19, 20, 36], it has been shown that there is a link between grinding rate and impact energy for given grinding materials under different mill speeds and fill volumeAt present, the amortization rate for the CNC grinder is higher by about 100%. The wage rate of the operator is higher for the conventional grinder. On such a grinder, engaged in small-batch production, an operator must be able to do varied tasks. His qualifications and his pay must be adequately high.The calculation of costs of grinding on conventional and CNC grinding
احصل على السعر
(PDF) A comparison of wear rates of ball mill grinding media
The performance of grinding media in a ball mill is also measured in terms of its wear rate. Abrasive ores such as gold and copper produce high wear rates of about 120µm/hr [74]. The wear ofrpm = (2,500 × 12) / (13.25 × π) = 721. Wheel wear per grind cycle = (0.00002 × 721 × 3.09) / 8 = 0.00557 inch. Usable abrasive = (16 10.5) / 2 = 2.75 inches. Wheel life = 2.75 / 0.00557 = 493 parts/wheel. This article describes how the life of a wheel can be determined in a creep-feed grinding operation. Calculating wheel life isHow to Calculate Wheel Life in a Creep-Feed Grinding Process
احصل على السعر
Modeling of the material removal rate in internal cylindrical
In the stable grinding stage, the calculation formula of the equivalent feed rate f 2 is: (2) f 2 = v f 2 + 2 π v f t + r w n w 60 2 where f 2 is the equivalent feed rate in the stable grinding stage (mm/s), t is the machining time from the moment that the surface material of the prehole begins to be removed (s), and r 0 is theA model has been developed for flowrate between a rotating grinding wheel and a workpiece. It was found that the useful flow that passes through the contact zone is a function of the spindle power for fluid acceleration, wheel speed and delivery-nozzle jet velocity.Two loss coefficients having values less than 1 are required to be calibrated for Useful coolant flowrate in grinding ScienceDirect
احصل على السعر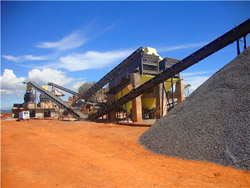
A Method to Determine the Ball Filling, in Miduk Copper
grinding rate, internal load retention time, product fractions, specific power draw, and mill performance. Therein, load density and ball filling percentage in semi-autogenous mill and its effect on the mills power draw is of great value. There exist several ways to calculating ball filling such as drawing out whole internal
احصل على السعر