
Grinding Mill an overview ScienceDirect Topics
The thickness of the material layer under grinding elements will exceed the maximal height for which the particles are drawn under the grinding elements, causing excessive buildup of the material in front of the grinding elements.For the past three decades the vertical roller mill has emerged to be the preferred choice for grinding raw materials. With the grinding capacity of a vertical roller Review on vertical roller mill in cement industry & its
احصل على السعر
Energy-Efficient Technologies in Cement Grinding
They are used in grinding of cement raw materials (raw meal) (i.e. limestone, clay, iron ore), cement clinker and cement additive Oriental Grinding Plant,Fine Grinding Plant,Powder Making Plant.Cement Clinker Grinding mill used in Clinker Grinding Process Plant.The raw material is. . MillRaymond grinding sbm/sbm grinding mill for plant material.md at main
احصل على السعر
How to improve grinding plant performance when
How to improve grinding plant performance when considering environmental, social and governance targets TON. Grinding Mill. Fitz Mill grinding unit is used that macerates the whole leaf into a soap-like material. From: Studies in Natural Products Chemistry, 2014. Related terms: Energy Grinding Mill an overview ScienceDirect Topics
احصل على السعر
Modeling of energy consumption factors for an industrial
It was reported that only the mill input material feed rate has a decisive influence on the mill differential pressure (ΔP) while gas flow rate, grinding pressure, and The grinding mill is often the bottleneck in the grinding circuit and defines the total capacity of the processing plant. Waste rocks occupy space from ore in the Towards waterless operations from mine to mill ScienceDirect
احصل على السعر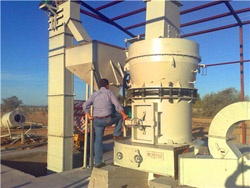
IMPROVING PRODUCTIVITY BASED ON THE MOVEMENT OF MATERIALS
PDF The problem addressed by this research is how to increase the production of cement mills in the Kufa cement plant when changed the pattern of Find, 1. Introduction 1.1. Background With the continual depletion of high grade simple ore bodies, more complex, finely disseminated ore bodies are being processed, Fine grinding: How mill type affects particle shape characteristics
احصل على السعر
Grinding Equipment, Chemical & Pharmaceutical
Ball mill material : Agate, zirconia, Building Material Shops, Manufacturing Plant, Machinery Repair Shops, Food & Beverage 1000g Grain Grinder Mill Powder Machine Swing Type Commercial1 天前MILL definition: A mill is a building in which grain is crushed to make flour. Meaning, pronunciation, translations and examplesMILL definition and meaning Collins English Dictionary
احصل على السعر
A Review of Alternative Procedures to the Bond
Determining the Bond index using the Fred Bond method [1,2] is considered the state-of-the-art methodology for mill calculations and a critical process parameter in raw materials selection and grinding The history of mill liners has evolved over time and this paper tracks the changes and development of liner technology. It provides an overview of the primary types of liners, the design and theGrinding Mill Liners- An Overview LinkedIn
احصل على السعر
Energy-Efficient Technologies in Cement Grinding IntechOpen
The energy consumption of the total grinding plant can be reduced by 20–30 % for cement clinker and 30–40 % for other raw materials. The overall grinding circuit efficiency and stability are improved. The maintenance cost of the ball mill is reduced as the lifetime of grinding media and partition grates is extended. 2.5.clogged or material becomes jammed, immediately shut off the mill. Do not overload the mills. Too much sample, too quickly may cause the mill to jam. Grinding time depends on the amount of sample. h. When grinding completed, turn off the mill at the switch. Make sure the mill is not running and the blades stopped before opening it. i.STANDARD OPERATING PROCEDURES
احصل على السعر
Operational Failure of Vertical Roller Attached to a Grinding Mill
In the present incident, one of the rollers of grinding mill in cement plant failed during operation, exhibiting longitudinal cracking over inner surface. Deposition welding was carried out just before the incident to match the worn-out profile of the roller. Investigation revealed that the subsurface of the cracked region contained discontinuities Grind curves map the essential performance measures of a grinding mill. • The need for a plant operator to manually select operating conditions is reduced. The mill grind (ψ) is the volume fraction of material in the discharge of the mill below the specification size. The broken ore below the specification size is referred to as finesExtremum seeking control for optimization of an open-loop grinding mill
احصل على السعر
Process efficiency aspects for jet mill plant operation
Different materials have been ground in Comex jets mills and the influence of the mill operating parameters such as mill filling level, distance between nozzles, feed material and rotor speed, on the grinding capacity was investigated.Additionally, the influence of the construction parameters on the operation of the mill were also established.Well, the first question is what you call a 'sample' . If it is soft plant tissue, the most practical tool are ball mills, were you can use steel balls in small plastic tubes 5 or 10 at one goHow does one grind leaf samples to a fine powder
احصل على السعر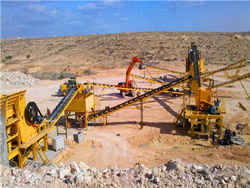
How to improve grinding plant performance when
In addition, recyclable mill liner materials may allow rubber and steel elements of worn liners to be removed and reused or recycled as raw material for new liners and prevent disposal in landfills. Professional This work concentrates on the energy consumption and grinding energy efficiency of a laboratory vertical roller mill (VRM) under various operating parameters. For design of experiments (DOE), the Minerals Free Full-Text Analysis and
احصل على السعر
Laboratory Mixer Mill MM 400 RETSCH
Mixer Mill MM 400. The Mixer Mill MM 400 is a true multipurpose mill designed for dry, wet and cryogenic grinding of small volumes up to 2 x 20 ml. It mixes and homogenizes powders and suspensions with a frequency of 30 Hz within seconds unbeatably fast and easy to operate. The compact benchtop unit is suitable for classic homogenizationA crushing plant delivered ore to a wet grinding mill for further size reduction. The size of crushed ore (F 80) was. 4.0 mm and the S.G. 2.8 t/m 3. The work index of the ore was determined as 12.2 kWh/t. A wet ball mill 1 m × 1 m was Grinding Mill an overview ScienceDirect Topics
احصل على السعر
Reducing energy consumption of a raw mill in cement industry
Several grinding methods are available in cement industry depending upon the material to be ground. In cement production process, about 26% of the total electrical power is used in grinding the raw materials. During grinding process, the energy obtained from the rotary burner is consumed. In this study, the first and second law analysis of a media and high energy intensity. The stirred media mills can work in continuous, or batch modes, and they exist in many sizes; the smallest ones have grinding chamber volumes of some milliliters and great production mills of some cubic meters. The grinding of materials down to sizes distinctly lower than 5 m has been established for theEnergy-Model and Life Cycle-Model for Grinding
احصل على السعر
From raw materials Extracting raw materials Raw
The desired raw mix of crushed raw material and the additional components required for the type of cement, e.g. silica sand and iron ore, is prepared using metering devices. Roller grinding mills and ball mills grind the mixture to a fine powder at the same time as drying it, before it is conveyed to the raw meal silos for further C. Obry. Karl-Heinrich Zysk. Vertical roller mills are the mills traditionally used for processing granulated blastfurnace slag and for grinding composite cements. From the energy aspect they areCements ground in the vertical roller mill fulfil the quality
احصل على السعر
How to choose proper grinding media for your ball mill
There are three types of grinding media that can be used in ball mills of cement plants. 1. Steel Balls. Steel balls are one of the most widely used grinding media in cement ball mills, their diameters can range from 20mm to 120mm according to different grinding requirements. In a cement ball mill, generally, φ50–100mm steel balls are used
احصل على السعر