
Influence of sulfur content in raw materials on oxidized pellets
The results show that most sulfur exists in the form of elementary sulfur in pyrite cinder, and over 95% sulfur is removed in producing pyrite cinder oxidized pellets. The concept to control the surface modification by co-grinding with element sulfur to stay at chemical bonding from further to solid state reaction may help to develop Effect of grinding with sulfur on surface properties and floatability
احصل على السعر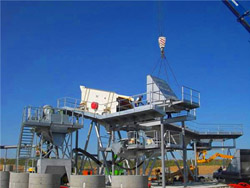
A critical review on energy use and savings in the cement industries
Vertical Roller Mill for Finish Grinding: 16.9 kWh/tonne [105] 10 kWh/tonne [71], [106] 0.29 GJ/tonne25.93 kWh/tonne7.95 US$/tonne: 26.66 [73] 0.2 GJ/tonne17 Last Updated: 12 Jun 2023. Request PDF The role of thermal improvements in indurating machines for pellet production from high-sulfur magnetite The role of thermal improvements in indurating machines for
احصل على السعر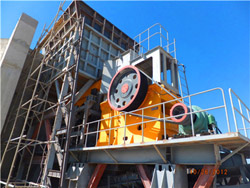
Unifying high-pressure grinding rolls models ScienceDirect
This paper unifies high-pressure grinding rolls crusher (HPGR) models of the working gap, mass flow rate, power draw, and centre and edge product particle size Abstract. Pyrite cinder and high sulfur magnetite were used as raw materials to produce iron ore pellets. Good qualities of green balls and fired pellets were Utilization of High Sulfur Raw Materials in Iron Ore Pellets
احصل على السعر
Pretreatment of Pyrite Cinder Before Pelletization by High Pressure
The processing and mechanism of the improvement in pelletization of Brazilian specularite by high-pressure roller grinding (HPRG) were investigated.ZHU De-qing, CHEN Dong, PAN Jian, LI Hou-qi. Pretreatment of pyrite cinder before pelletization by high pressure roller grinding [J]. Journal of Iron and Steel Preparation of pre-reduced pellet using pyrite cinder
احصل على السعر
Minerals Free Full-Text An Improved High
An improved approach is presented to model the product particle size distribution resulting from grinding in high-pressure roll crusher with the aim to be used in standard high-pressure grinding rolls (HPGR).KEY CONCEPTS. • Extreme pressure (EP) and antiwear (AW) lubricant additives are chemicals that react with metal surfaces, forming easily sheared thin layers that prevent wear and seizures. • The use of EP and Lubrication Fundamentals Society of Tribologists
احصل على السعر
Improving Pelletisation of Pyrite Cinder by High Pressure Roller Grinding
The pelletisation of pyrite cinder can be improved by high pressure roller grinding and blending with magnetite in the pellet feed. The former is probably ascribed to the increase in specific surface areas of pellet feed from 850 cm2g to 1690 cm2g when the pellet feed passes through roller twice. such as sulfur and phosphorus except forSulfur powder grinding mill Sulfur powder grinding mill, mainly used in the production of sulfur powder, the fineness ranging from 60 to 325 mesh. The production made by our company dedicated to grinding mill with closed-end flow and added anti-explosion devices, filling the gas flame retardant.hot sale sulfur powder grinding mill of chemical equipment
احصل على السعر
Our Dynamic HPGR Technology for Mineral Grinding Weir
In service since the mid-eighties and used primarily in cement production, high pressure grinding rolls are increasingly being deployed as tertiary and quaternary crushers in mineral comminution circuits, dealing with tougher ores including iron, gold, copper and diamonds. HPGR technology uses inter-particle grinding to reduce particle size and increase High-pressure grinding rolls (roller presses) are used in both raw material and cement grinding. The principle of the HPGR is shown in Figure 2. Figure 1. Barmac VSI crusher. Figure 2. Principle of compressive size reduction. The material between the rolls is submitted to a very high pressure ranging from 100 to 200 MPa. Special hard materialsEnergy-Efficient Technologies in Cement Grinding IntechOpen
احصل على السعر
High pressure grinding rolls (HPGR) TON
Robust HRC™ high pressure grinding rolls (HPGR) High pressure grinding rolls (HPGR) are used for size reduction or rocks and ores. They compress the feed material between two rotating rollers, one of which is in a fixed position and another roller that is floating. The two rotating rollers generate such a high pressure that it grinds the feedTherefore, it is necessary to grind the rollers damaged to reuse them in rolling process, [1][2][3][4] [5] and rollers and roller grinding machine are shown in Figure 2. Consequently, the rollerEffects of high pressure roller grinding on size distribution of
احصل على السعر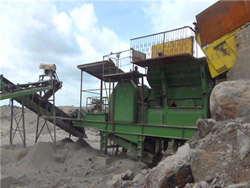
Utilization of High Sulfur Raw Materials in Iron Ore Pellets
Abstract. Pyrite cinder and high sulfur magnetite were used as raw materials to produce iron ore pellets. Good qualities of green balls and fired pellets were obtained from the feed comprising 50% pyrite cinder and 50% high sulfur magnetite concentrate at a small scale. Small-scale tests were proven by pilot-scale tests.Confined particle-bed comminution as in high pressure grinding roller mills (HPGR) or vertical roller mills (VRM) offers a wide range of options for selective comminution since the parameters canGrinding of mineral mixtures in high-pressure grinding rolls
احصل على السعر
High Pressure Grinding Roll for advanced crushing |FLSmidth
High pressure grinding roll saving energy and providing results The HPGR truly is a unique comminution product. It weakens rock structure and exposes ore particles, making it an attractive option for heap leach applications.The crusher was then retrofitted with hydraulic cylinders to increase the pressure between the rollers. This was the predecessor to the high-pressure grinding rolls (HPGR) crusher, which became popular in Europe for applications in the cement industry. The introduction of the HPGR in minerals processing sparked at the beginning of the 2000s.A time dynamic model of a high pressure grinding rolls crusher
احصل على السعر
The role of thermal improvements in indurating machines for
The use of the high pressure roller grinding significantly improved the pelletization ability of the iron concentrate and the quality of the finished pellets. Compared with other same scaleRaymond Mills Raymond Roller Mill Grinding Mill. Raymond mill is also called Raymond roller mill. It is a new type of high-fineness grinding mill with high efficiency and closed circulation, which can completely replace the cement ball mill.This kind of machine is commonly used in cement plant for raw materials fine grinding, such as Sulfur Raymond Roller Mill groupe-taran.fr
احصل على السعر
Coupled DEM-MBD-PRM simulations of high-pressure grinding
The high-pressure grinding rolls (HPGR) is a widely used technology that has gained progressive acceptance in the minerals industry, being used in size reduction of materials that include iron ores, Kimberlites, copper ores, gold ores, platinum ores, among others. This requires description of the dynamic response of the floating rollerSome choose to ball mill the Sulfur and Charcoal together 30 grams of Charcoal Powder, and 20 grams of Sulfur high pressure roller mill; liquid nitrogen for sulphur grinding Grinding Mill China Air Classifier, Roller Mill, Sulphur Grinder, Spices Grinder, Tamarind Coal Dust Powder, Lustrous Carbon Ferro Alloys Inoculant:Roller Mill For Sulphur Powder Crusher Mills, Cone Crusher,
احصل على السعر
Improving pelletisation of pyrite cinder by high pressure roller grinding
The pelletisation of pyrite cinder can be improved by high pressure roller grinding and blending with magnetite in the pellet feed. Most sulfur was removed in preheating stage. 81.25% sulfurSpecialty lubricants boost high-pressure grinding roll energy efficiency. Case Study Highly pressurized counter-rotating rolls that generate extreme stresses within material in the crushing zone make the HPGR process more efficient. In crushing and grinding mining operations, high-pressure grinding rollhigh-pressure grinding rolls case study klueber
احصل على السعر
Industrial Solutions polycom high-pressure grinding roll
the efficiency of the high-pressure grinding and a separating system optimized for the respective application. Combining a polycom ® high-pressure grinding roll and a static-dynamic sepol ® separator in a finish grinding plant for raw material increases energy efficiency significantly. Each polysius ® grinding plant is custom-Dry milling machines Schenck Process. Our largest and strongest products include dry and wet milling machines that grind hard, abrasive materials for applications like mineral processing, cement plants, and power generation They are are characterized by their excellent wear life, high availability and easy maintenance At the other end of the scale sulfur raymond roller mill am-housses.fr
احصل على السعر
A first survey of grinding with high-compression roller mills
Hybrid Comminution with High‐Pressure Roller and Stirred Bead Milling. Yanmin Wang E. Forssberg. Materials Science. 2005. This paper presents the experimental results on the wet grinding of a moist calcium carbonate material in a hybrid comminution system, which consists of a high pressure roller mill (HPRM) and a.
احصل على السعر