
Chemistry and engineering of the clinkerization process —
But since the burning temperature of alinite clinker is low (1000°–1200 °C) and the chlorine-containing waste including incinerated ash of municipal refuse might be Dry process; Suspension preheater; In-line calciner; Separate line calciner; Burning zone temperature; Back-end temperature; Oxygen control; Kiln speed; Chemical Cement Manufacturing and Process Control SpringerLink
احصل على السعر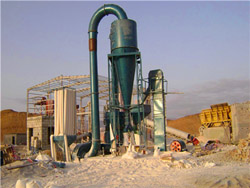
(PDF) Optimizing the Control System of Clinker Cooling:
PDF This paper aims to present efficient efforts to optimize the proportional-integral-differential (PID) controller of clinker cooling in grate Find, read the clinker silo. In the production line, water is used to cool the clinker. The cooling of the clinker also has a great influence on its quality. III. PROBLEM AI Kiln Solution For Optimized Control Siemens
احصل على السعر
Modeling of the Thermal Efficiency of a Whole Cement Clinker
This paper proposes that the scope of research should be extended to the whole clinker calcination system from its single device or specific process (i.e., its An MPC strategy is used to stabilize a temperature profile along the rotary kiln, guaranteeing good combustion conditions and maximizing production. In this paper, Optimization of the Clinker Production Phase in a Cement
احصل على السعر
Fives Burning lines for clinker production Fives Group
Fives’ burning lines integrate proprietary technologies, including: Preheater cyclones, Calciner systems ( FCB Zero-NOx Preca and FCB In-line Preca ), Rotary kilns ( FCB Kiln The clinker burning line of the plant is shown in Figure 1. The raw material, which consists of 77 wt% CaCO 3,14 wt% SiO 2,and small amounts of Al 2 O 3,Fe 2 O 3,MgCO 3,and water, isThe clinker burning line of the reference cement
احصل على السعر
Clinker Burning Kinetics and Mechanism Welcome to DTU
Abstract. The industrial cement process is subject to several changes in order to reduce the high energy consumption and thereby increase the profitability of Cement kiln is the main equipment for clinker sintering. From structure, it can be divided into rotary cement kiln and shaft kiln, while, from the working principle, it can be divided into the dry method and wet method kiln. AGICO offers different types of cement kilns from 10-5000t/d with steady running, high efficiency and large output.Clinker Production Clinker Manufacturing Cement
احصل على السعر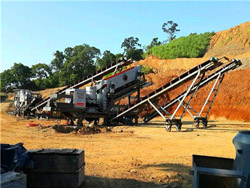
Clinker Production an overview ScienceDirect Topics
Calcination is the main process of clinker production, calcining calcium carbonate (CaCO 3) at about 900 °C to form calcium oxide, CaO, lime, and the release of carbon dioxide gas (CO 2).In the next step of the so-called clinker treatment, calcium oxide (CaO) is exposed to temperatures of 1400 °C to 1500 °C together with silica (SiO 2), aluminum oxide (Al 2 O Portland cement clinker burning, 2.2. The phase systems important for cement chemistry, 2.3. time in the mixture with molar ratio 1:1 (after ); a in dry air at 1000 °C, b in moist air at 1000 °C, c in dry air at 1200 °C. Full size image. Fields of C 3 S and C 3 A primary crystallization are denoted by dashed lines. C 1 clinkerPortland Cement Clinker SpringerLink
احصل على السعر
Fire Free Full-Text Modern Kiln Burner Technology in the
The current manuscript presents a review on existing kiln burner technologies for the cement production process, in the context of the current climate of energy transition and environmental remediation. Environmental legislation has become ever stricter in response to global climate change, and cement plants need to adapt to this The found average difference in Heat required for clinker formation between temperature 1338 °C and 1450 °C is 82.26 kJ/kg-clinker representing 2.23% of Total heat input are 3686 kJ/kg-clinker.Calculation of the formation process of clinker inside the
احصل على السعر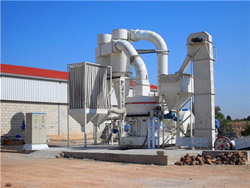
Evolution and projection of CO ScienceDirect
The number of NSP kiln lines was 173 in 2001, but by the end of 2011, there were 1637 and heat recovery system, in which the thermal energy required to burn dry materials amounts to 102 kgce/t (3100 MJ/t) for clinker. the thermal energy demand for burning clinker decreased from 154.06 kgce (4515 MJ) to 121.97 kgceThis work analyzes how gases emitted during the manufacture of clinker vary in a cement plant using two types of fuel: petroleum coke and unusable tires (UTs). This study is based on a case study(PDF) Used Tires as Fuel in Clinker Production: Economic and
احصل على السعر
Heat Balance Analysis in Cement Rotary Kiln Science
Clinker 0.186 54 0 Coal 0.262 390 0 Table 4. Heat for evaporation of water: kcal/kg. Temp.°C 0 20 100 Heat Evaporationkcal/kg 597 586 539 2 3. Results 3.1. Basis 1. 1kg of clinker 2. Reference Temperature 0°C 3.2. Heat Outputs 3.2.1. Heat of Formation Considering loss free clinker as loss-free meal feedstock under equilibrium conditionPortland cement clinker is a hydraulic material which shall consist of at least two-thirds by mass of calcium silicates (3CaO.SiO 2 and 2CaO.SiO 2), the remainder consisting of aluminium and iron containing clinker phases and other compounds.The ratio of CaO to SiO 2 shall not be less than 2.0. The magnesium oxide content (MgO) shall not exceed 5.0% Portland Cement Clinker an overview ScienceDirect Topics
احصل على السعر
sbmchina/sbm size of cement clikner in dry process.md at
Contribute to sbmcrushers/sbmchina development by creating an account on .There are four stages in the manufacture of portland cement: (1) crushing and grinding the raw materials, (2) blending the materials in the correct proportions, (3) burning the prepared mix in a kiln, and (4) grinding the burned product, known as “ clinker ,” together with some 5 percent of gypsum (to control the time of set of the cement).Cement Extraction, Processing, Manufacturing Britannica
احصل على السعر
Paragenesis of unusual Fe-cordierite (sekaninaite)-bearing
Sekaninaite (XFe > 0.5)-bearing paralava and clinker are the products of ancient combustion metamorphism in the western part of the Kuznetsk coal basin, Siberia. The combustion metamorphic rocks typically occur as clinker beds and breccias consisting of vitrified sandstone–siltstone clinker fragments cemented by paralava, resulting from For the new dry process cement kiln, about 7D~4D from the kiln head is the transition zone. In the burning zone,the material temperature is between 1300℃~1450℃, and the flame temperature canIntroduction of Cement Kiln Working Zone
احصل على السعر
Clinkerization an overview ScienceDirect Topics
The decarbonation of limestone to give the calcium required to form silicates and aluminates in clinker releases roughly 0.53 Around 95%–97% of the world’s bioenergy is produced by directly burning biomass, generating 476 million tons of biomass ash (BA) Plant P1 employs a dry process with an annual cement production of 3.383Clinker plant is applied to clinker production, we can classify the clinker plant into two parts, preheat and precalcining, burning in the rotary kiln. AGICO Cement is a cement plant manufacturer with rich experience, and we are specialized in cement plant and cement equipment. Based on rich experience and advanced technology support, ourClinker Plant Cement Plant Cement Equipment For Clinker
احصل على السعر
A Review on Pyroprocessing Techniques for Selected Wastes
The wet and dry manufacturing processes are the two main ways of manufacturing cement . The major difference between wet and dry process is the mix preparation method before burning clinker in the kiln. The wet process involves the addition of water to the raw materials to form rawslurry which is thick. In the dry process, the raw Abstract. The use of fuel containing high sulfur is becoming one of the few choices for the cement industry due to: 1. The limited quantity of fuel on our planet according to conducted(PDF) Reducing the SO2 emission from a cement kiln
احصل على السعر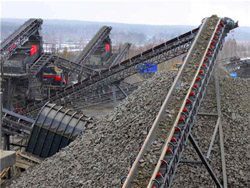
Portland cement clinker production using concentrated solar energy
The typical fuel consumption of a five-stage preheating dry kiln can reach up to 3.2–3.5 GJ/t clinker (Worrell et al., 2001). The moisture content of the raw material plays a crucial role in the heat consumption (Worrell and Galitsky, 2008). Nonetheless, energy usage in the cement industry has always been optimized for economic reasons.The volatilization rate of alkalies during clinker burning is low. Ca2SiO4 and CaSO4 upon reheating in dry atmospheres containing SO2 and O2.ResumenEl sulfosilicato de calcio se ha reportadoFormation of cement phases and kinetics of clinker
احصل على السعر
Better and cheaper cement: Optimising the right clinker
The main factors affecting clinker reactivity and PSD. Clinker mineralogy and nodule size depend largely on the feed composition and the amount, distribution and nature of the melt phase formed in the burning zone. The clinker melt promotes the reaction between belite (C 2 S) and free lime to form alite (C 3 S), so it is critical for clinker
احصل على السعر