
BALL Mill Critical Speed INFINITY FOR CEMENT
BALL Mill Critical Speed % Critical speed: Practically, mill speed between 68 and 82% of critical speed. % critical speed is the mill actual speed in RPM divided by nc. Example: 3.98 meter mill with rotational speed of 15.6 rpm The mill was simulated at different critical speeds with different mill fillings. In total, 165 scenarios were simulated. When the (PDF) Effects of Ball Size Distribution and Mill
احصل على السعر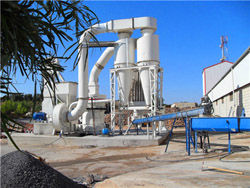
BALL MILLS Ball mill optimisation holzinger
Cement ball mills are typically two- chamber mills (Figure 2), where the first chamber has larger media with lifting liners installed, providing the coarse grinding stage, A comprehensive investigation was conducted to delineate the effect of ball size distribution, mill speed, and their interactions on power draw, charge motion, and Effects of Ball Size Distribution and Mill Speed and Their Interactions
احصل على السعر
a) Cement ball mill view, b) Cement mill sketch.
It could also be inferred that residue is inversely related to Blaine or fineness. 15 rpm mill speed is near the critical mill speed, thus Blaine is minimum whereas residue is higher at 16% (Fig. 12).This paper presents a comparison of the breakage parameters with mill speed under the standard conditions in a small laboratory ball mill of clinker and The effect of mill speed on kinetic breakage parameters of
احصل على السعر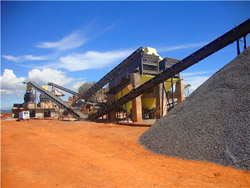
Effects of Mill Speed and Air Classifier Speed on
Abstract The research focuses on the mill speed and an air classifier speed effect on the two compartment Cement ball mill performance in terms of Blaine, The effect of the fraction of mill critical speed ( φc) on the grinding for model parameter aT was found to be different for two different samples: aT =0.0344 exp The effect of mill speed on kinetic breakage parameters of clinker
احصل على السعر
What is the optimal rotation speed for a ball mill? LinkedIn
The ideal rotational speed of a ball mill for optimal grinding depends on several factors such as the size and weight of the grinding media, the size of the mill, and the material being processedThe effect of the fraction of mill critical speed ( φc) on the grinding for model parameter aT was found to be different for two different samples: aT =0.0344 exp (0.00301 φc) for clinker and aT =0.0225 exp (0.06183 φc) for limestone. Additionally, it was found in this study that optimum grinding occurs at φc =85%, in contrast to the 70% ofThe effect of mill speed on kinetic breakage parameters of clinker
احصل على السعر
Process Training Ball Mill INFINITY FOR CEMENT
The speed of a ball mill is often expressed as the percentage of critical speed. The critical speed is attained when the centrifugal force is that high that all balls are sticking to the mill wall and rotate with the mill. /S"1 International Mining Congress and Exhibition of Turkey-IMCET 2003, (c 2003. ISBN 975-395-605-3 The Effect of Fraction of Mill Critical Speed on Kinetic Breakage Parameters of Clinker and Limestone in a Laboratory Ball Mill V. Deniz, A. Gelir & A. Demir Mining Engineering Department, University of Süleyman Demirci, Isparla, Türkiye ABSTRACT: Ball Mill Critical Speed [1d47v91w6y42] Documents and E
احصل على السعر
(PDF) Effects of Mill Speed and Air Classifier Speed on
Optimum performance of ball mill could potentially refine Blaine fineness, thereby improving the cement quality. This study investigates the effects of separator speed and mill speed on BlaineGC1. Critical Speed (nc) & Mill Speed (n) Please Enter / Step-to Input Values. Mill Eff. Dia Deff, m. CALCULATED VALUE OF nc, rpm.ball mill calculations, grinding media filling degree, ball size, mill
احصل على السعر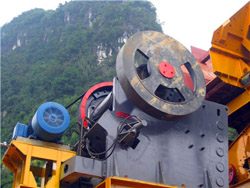
(PDF) Grinding in Ball Mills: Modeling and Process Control
A ball mill is a type of grinder widely utilized in the process of mechanochemical catalytic degradation. It consists of one or more rotating cylinders partially filled with grinding balls (madeSpeed rate refers to the ratio of the speed of the mill to the critical speed, where the critical speed is n c = 30 / R. In practice, the speed rate of the SAG mill is generally 65% to 80%. Therefore, in the experiment, the speed was set to vary in 50% and 90% of the critical speed (1.28–1.64 rad/s) for the cross-over test as shown in Table 2.Optimal Speed Control for a Semi-Autogenous Mill Based on Discrete
احصل على السعر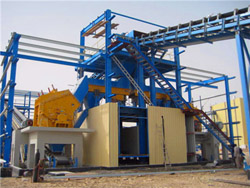
SAGMILLING.COM .:. Mill Critical Speed Determination
Result #1: This mill would need to spin at RPM to be at 100% critical speed. Result #2: This mill's measured RPM is % of critical speed. Calculation Backup: the formula used for Critical Speed is: N c =76.6 (D -0.5) where, Nc is the critical speed,in revolutions per minute, D is the mill effective inside diameter, in feet.In this study, it was found that optimum grinding occurs at 85% of critical speed, compared to the optimum grinding at 70% of critical speed of the ball mill in the cement factory. The variation of a T values with the fraction of mill critical speed ( φ c ) gave high correlation coefficients of 0.98 and 0.96 for clinker and limestoneThe effect of mill speed on kinetic breakage parameters of
احصل على السعر
Ball Mill Design/Power Calculation 911 Metallurgist
The approximate horsepower HP of a mill can be calculated from the following equation: HP = (W) (C) (Sin a) (2π) (N)/ 33000. where: W = weight of charge. C = distance of centre of gravity or charge Size of the grinding media typically varies in a range of 4-8 mm. The grinding tools reach a tip speed of 5 times the critical speed, rather creating a constant cloud of grinding media than a revolving mass of rolling and Let’s talk: polysius® booster mill the next level
احصل على السعر
AMIT 135: Lesson 7 Ball Mills & Circuits Mining Mill
At the end of this lesson students should be able to: Explain the role of ball mill in mineral industry and why it is extensively used. Describe different types of ball mill design. Describe the components of ball mill. Explain their understanding of ball mill operation. Explain the role of critical speed and power draw in design and processRaw mills usually operate at 72-74% critical speed and cement mills at 74-76%. 3.2 Calculation of the Critical Mill Speed: G: weight of a grinding ball in kg. w: Angular velocity of the mill tube in radial/second. w = 2*3.14*(n/60) Di: inside mill diameter in meter (effective mill diameter). n: Revolution per minute in rpm. Specific powercement-mill PDF SlideShare
احصل على السعر
Failure analysis of a ball mill located in a cement’s
The work herein presented analyses an existing failure in a ball mill of a cement production line. In this case, the speed is 15.4 revolutions per minute, equivalent to 70.9% of the critical speed. The ball mill feed is generally 75% mix and 25% steel. The mill is divided into two chambers (Fig. 1 a), depending on the size of the materialIn cement mills, ventilation is a critical key for maintaining temperature and material transportation. However, relationships between operational variables and ventilation factors for an industrial cement ball mill were not addressed until today. This investigation is going to fill this gap based on a newly developed concept named “conscious laboratory Ventilation Prediction for an Industrial Cement Raw Ball Mill
احصل على السعر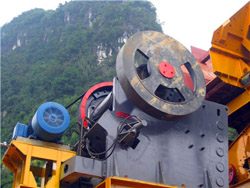
Ball Mill- Principle, Application, Uses, Critical Speed, Diagram
The diagram provided gives a visual representation of the components of a typical ball mill. Critical Speed of Ball Mill. Ball mills are also used in the cement industry to grind clinker and gypsum to produce cement. The chemical industry uses ball mills to grind chemicals to a fine powder or to mix chemicals together to create specificAutogenous and Semi-Autogenous Mills. In Mineral Processing Design and Operations (Second Edition), 2016. 9.3.4 Mill Speed. During normal operation the mill speed tends to vary with mill charge. According to available literature, the operating speeds of AG mills are much higher than conventional tumbling mills and are in the range of 80–85% of the Mill Speed an overview ScienceDirect Topics
احصل على السعر
OPTIMIZATION OF CEMENT GRINDING OPERATION IN
Operation and Elements of a Closed-Circuit Ball Mill System . Cement ball mills typically have two grinding chambers. The first chamber is filled with larger diameter grinding media andlined with lifting liners . The first chamber coarse-grinds the feed material and prepares it for the second chamber. The second chamber is the fine grinding
احصل على السعر