
(PDF) Grinding in Ball Mills: Modeling and Process
A ball mill is a type of grinder widely utilized in the process of mechanochemical catalytic degradation. It consists of one or more A numerical dynamic-mechanical model of a planetary ball-mill is developed to study the dependence of process efficiency on milling parameters like ball size and Modeling of the planetary ball-milling process: The case
احصل على السعر
An innovative approach for determining the grinding media
Herein, an innovative approach for determining the grinding media system of ball mill based on grinding kinetics and linear superposition principle was proposed. Ball grinding process is a grinding method of crushing ore with ball-shaped grinding medium in the grinding mill. In the ball grinding process, because the steel ball Ball Grinding Process SpringerLink
احصل على السعر
Intelligent optimal control system for ball mill grinding
Abstract: Operation aim of ball mill grinding process is to control grinding particle size and circulation load to ball mill into their objective limits respectively, while I. Introduction Grinding in ball mills is an important technological process applied to reduce the size of particles which may have different nature and a wide diversity of physical, Grinding in Ball Mills: Modeling and Process Control
احصل على السعر
Grinding in Ball Mills: Modeling and Process Control
Abstract. The paper presents an overview of the current methodology and practice in modeling and control of the grinding process in industrial ball mills. Basic Analysis of the ball mill grindability to improve the simplified grinding model S. Nomura Add to Mendeley https://doi/10.1016/j.powtec.2022.117551 Get rights and Analysis of the ball mill grindability to improve the simplified
احصل على السعر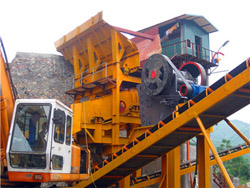
Ball Mill an overview ScienceDirect Topics
The ball mill is a tumbling mill that uses steel balls as the grinding media. The length of the cylindrical shell is usually 1–1.5 times the shell diameter (Figure 8.11 ). The feed can be The ball mill grindability test is used for describing ore hardness and it is so widespread that the Bond Work Index generated from the test is often referred to as an ore characteristic. The ore resistance to grinding and energy consumption can be expressed using the work index and Bond’s Third Theory.A new methodology to obtain a corrected Bond ball mill
احصل على السعر
(PDF) Effect of ball size distribution on milling
the grinding media and the ball size distribution of the charge, is also discussed. 2.2 Breakage mechan ism in tumbling ball mills Several mechanisms contribute to the grinding action that takesCERAMIC LINED BALL MILL. Ball Mills can be supplied with either ceramic or rubber linings for wet or dry grinding, for continuous or batch type operation, in sizes from 15″ x 21″ to 8′ x 12′. High density ceramic linings of uniform hardness male possible thinner linings and greater and more effective grinding volume.Ball Mills 911 Metallurgist
احصل على السعر
A Review of Alternative Procedures to the Bond Ball Mill
Over the years, alternative procedures to the Bond grindability test have been proposed aiming to avoid the need for the standard mill or to reduce and simplify the grinding procedure. Some of them use the standard mill, while others are based on a non-standard mill or computation techniques. Therefore, papers targeting to propose a better 8.3.2.2 Ball mills. The ball mill is a tumbling mill that uses steel balls as the grinding media. The length of the cylindrical shell is usually 1–1.5 times the shell diameter (Figure 8.11 ). The feed can be dry, with less than 3% moisture to minimize ball coating, or slurry containing 20–40% water by weight.Ball Mill an overview ScienceDirect Topics
احصل على السعر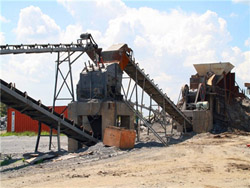
Effects of the speed ratio on the efficiency of planetary mills
1. Introduction. Planetary ball mills provide high energy density due to the superimposed effect of two centrifugal fields produced by the rotation of the supporting disc and the rotation of the vials around its own axis in the opposite direction [1].During operation, the grinding balls execute motion paths that result in frictional and impact effects.In this theory, new material characteristics have been added: the surface and volumetric density of grinding energy. The thermodynamic theory is a combination of the classical Kick’s theory and(PDF) Research on the Grinding Energy Density in a Jet Mill
احصل على السعر
The mechanochemical synthesis of polymers RSC Publishing
Fig. 1 Upper part: Examples of (a) a planetary ball mill (Fritsch planetary ball mill P7) and (b) a vibrational ball mill (Retsch mixer mill MM400). Lower part: Procedure of milling jar filling for (left) a planetary ball mill and (right) a vibrational ball mill. (I) The empty milling jars are equipped with a seal and milling balls.The dry grinding experiment was operated in the ball mill (Φ460 × 600 mm) with steel ball as grinding media at mill speed . Conclusion (1) An innovative approach for determining the grinding ball system based on grinding kinetics and linear superposition principle was proposed. The grinding experiment was operated with the Anshan type iron An innovative approach for determining the grinding media
احصل على السعر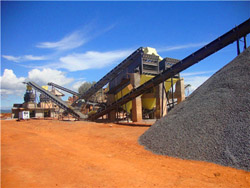
Investigation on Iron Ore Grinding based on Particle Size Distribution
The feed samples of X, Y, and Z iron ores were ground in the BBM (ball mill refers to a BBM of size 300 mm × 300 mm with smooth liners) to identify the PSD, BWI, and RT of each ore. Grinding experiments were conducted according to Bond’s standard test procedure [].For each iron ore sample, the RT taken to produce 250% circulating Fine grinding mills can be categorized into five groups [48]: impact mills, ball media mills, air jet mills, roller mills, and those of some other type, including disc mills. Impact mills and air jet mills are based on single impacts, as presented in Fig. 4 a, while ball media mills utilize double impacts between metal surfaces (Fig. 4 b).Fine grinding of wood Overview from wood breakage to
احصل على السعر
Modeling of the planetary ball-milling process: The case
Among high-energy ball mills, the planetary is a mechanically simple and versatile device for efficient grinding. It is usually made of two or more jars, rotating at an angular velocity ω around their axis (see Fig. 1), installed on a disk rotating at angular velocity Ω.Grinding occurs by impact among the milling media (balls and jars), driven by Grinding in Ball Mills: Modeling and Process Control. Vladimir Monov, Blagoy Sokolov and. Stefan Stoenchev. Published Online: 16 Mar 2013. Volume & Issue: Volume 12 (2012) Issue 2 (June 2012) Page range: 51 68.Grinding in Ball Mills: Modeling and Process Control Sciendo
احصل على السعر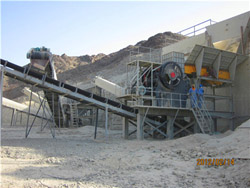
Heat generation model in the ball-milling process of a tantalum
environment during the grinding process of the ball mill. Furthermore, the density (2313kg/m3) and s pecific heat (853 J/kgK) of ore from P enolta mine were experimentally found.The process of ball milling and the materials that compose planetary ball mills are highly complex, and the existing research on the change in ball-milling energy is not mature. The theoretical model of a ball mill was established for the first time to simulate the motion, collision process, energy transfer, and temperature change of small balls during Model Study of Mechanicochemical Degradation in a Planetary Ball Mill
احصل على السعر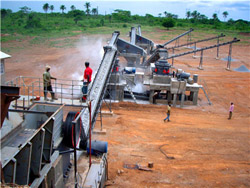
(PDF) Hybrid Intelligent Modeling Approach for the Ball Mill Grinding
The tests covered a range of slurry concentrations from 30 to 55 vol.% solid and fractional interstitial bed filling (U) from 0.3 to 1.75, at a fixed ball load (30% of mill volume) and 70% ofThe Effect of Ball Size on the Energy Efficiency of Hybrid High-Pressure Roll Mill/Ball Mill Grinding. Powder Technology, Vol. 105,1999, 199-204. 10.1016/S0032-5910(99)00138-2 Google Scholar 23.Grinding in Ball Mills: Modeling and Process Control
احصل على السعر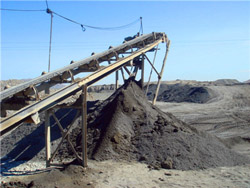
Grinding in Ball Mills: Modeling and Process Control
There are three types of grinding media that are commonly used in ball mills: • steel and other metal balls; • metal cylindrical bodies called cylpebs; • ceramic balls with regular or high density. Steel and other metal balls are the most frequently used grinding media with sizes of the balls ranging from 10 to 150 mm in diameter [30].The ball mill grinding is a complex process with many influencing factors, and these influencing factors restrict and affect each other. K. Fang, “Uniform design-application of number theory method in experimental design,” Acta Mathematicae Applicatae Sinica, vol. 3, pp. 363–372, 1980. View at: Google Scholar.Study on Preparation and Characterization of Graphene Based on Ball
احصل على السعر
Intelligent optimal control system for ball mill grinding
Operation aim of ball mill grinding process is to control grinding particle size and circulation load to ball mill into their objective limits respectively, while guaranteeing producing safely and stably. The grinding process is essentially a multi-input multi-output system (MIMO) with large inertia, strong coupling and uncertainty characteristics.
احصل على السعر