
Comparative Study on Improving the Ball Mill Process Parameters
The optimum process parameters setting concluded that balls to powder weight ratio are 20:1, the optimum ball mill working capacity is 2 L while the optimum speed of the ball mill is 105 rpm. Using SEM characterization, the improved particles of silica The parameters used in the ball mill process are relatively large, however there are several parameters that have a significant effect on the reduction grain size Parameter Optimization of Ball Milling Process for Silica
احصل على السعر
Effect of Ball Mill Parameters’ Variation on the Particles of a
This work has investigated the effect of variation of the mill-ball parameters on the particle sizes in mechanical activation-assisted leaching and proved It was discovered that the milling speed and diameter of the ball have a great influence on the MA leaching process with an optimum speed of 600 rpm and Effect of Ball Mill Parameters’ Variation on the Particles
احصل على السعر
The Impact of Ball Milling Process Parameters on the Preparation
When preparing nano silicon powder by high-energy ball milling, the grain size of the obtained nano silicon powder varies with different technical parameters set in the ball Importance of the ball-milling process parameters on the basis F ratio value from the ANOVA showed that ball-milling time contributed most, followed by the Effect of ball-milling process parameters on mechanical
احصل على السعر
Investigating grinding mechanisms and scaling criteria in a ball mill
Grinding powders in a ball mill is a complex operation in which many parameters, such as geometrical factors [2], filling ratios [3], powder properties [4] or the With a view to developing a sound basis for the design and scale-up of ball mills, a large amount of data available in the literature were analyzed for variation of the Analysis of ball mill grinding operation using mill power
احصل على السعر
Kinetics of Dry-Batch Grinding in a Laboratory
With ball-mill grinding being one of the most energy-consuming techniques, setting the optimal values of the operational and mineralogical parameters for efficient grinding is a key target in mineral In order to explore the impact of different ball milling technical parameters on the grain size of nano silicon powder, this paper adopted the orthogonal experimental design in combination with fitting analysis, and set the agitator shaft speed of the ball mill and the milling time as the influence factors. Then this paper studied the impact ofThe Impact of Ball Milling Process Parameters on the Preparation
احصل على السعر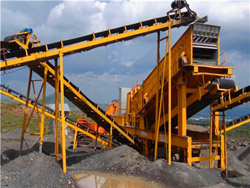
Effect of Ball Mill Parameters’ Variation on the Particles
in which the particles of the ore/mineral were subjected to milling by a spherical ball before the leaching/dissolution process. For the MA hydrometallurgical process, the key parameters for the mechanical device are the rotating speed (˜); diameter (d) of the milling/grinding ball; and its weight (M). The developed theoretical equation wasThe balls to powder ratio (BPR) and powder type were investigated in relation to the particle size. The study showed that the combination of the BPR and powder type affects the particle size result. The optimum of BPR at 12 with the number of balls is 60 pieces, and the filling rate is 10.13%. The result shows that the horizontal ball mill ableThe design and optimization process of ball mill to reduce
احصل على السعر
(PDF) Parameters optimization in the planetary ball milling of
For example, a lower ball-to-powder ratio results in less efficient grinding and longer grinding times (Begin-Colin et al., 2000). Planetary, attritor, and vibration mills are different types ofHowever, the high-dimensional mechanical signals of multi-source modes are difficult to map the characteristic parameters of the ball mill, which leads to low fusion efficiency, slow convergence speed and poor generalization of the established model (Tang et al., 2018a, Tang et al., 2018b, Cai et al., 2021).Assessing load in ball mill using instrumented grinding media
احصل على السعر
Investigating grinding mechanisms and scaling criteria in a ball mill
Grinding powders in a ball mill is a complex operation in which many parameters, such as geometrical factors [2], filling ratios [3], powder properties [4] or the energy transferred to the vessel [5] can influence the characteristics of the resulting powder. The effect of each parameter on the resulting ground powder is usually investigatedE.1 Determination of milling parameters in each ball size interval 100 E.2 Predicted EQM- and OEM-BSD’s selection functions 100 E.3 Statistical analysis of the predictions 101 . 9 List of figures Figure Page 2.1 Breakage mechanisms in a ball mill 22 2.2 First order reaction model applied to milling 24 2.3 Grinding rate versus particle sizeEFFECT OF BALL SIZE DISTRIBUTION ON MILLING
احصل على السعر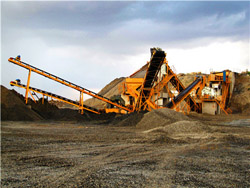
Influences of operating parameters on dry ball mill
of calcite in a laboratory scale conventional ball mill. Within the context, the influence of operating parameters such as mill speed, ball filling ratio, ball size distribution, powder filling ratio, grinding aid dosage and grinding time were studied. The results of grinding tests were evaluated based on the product particle size (d 50, d 80According to the specifications and parameters of the ball mill, the general layout, grinding body, lining plate, partition device, support device, transmission part and feeding and discharging(PDF) Design of Three-chamber Ball Mill ResearchGate
احصل على السعر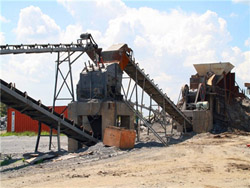
A machine learning approach for ball milling of alumina
The five processing parameters (inputs) and the three quality responses (outputs) of the target mill are summarized in Table 1.Al 2 O 3 powders (AES-11, purity of 99.9%, d 50 = 0.7 μm, d 90 = 1.96 μm, Sumitomo Chemical, Japan) were used as starting powders. The value of d 50 (y 1), and the values of width and skewness (y 2 and y 3) At present, most of the domestic and foreign studies on the grinding process of ball mills determine the relevant parameters by discrete element methods and molecular dynamics [33–35]. The ball mill grinding is a complex Study on Preparation and Characterization of
احصل على السعر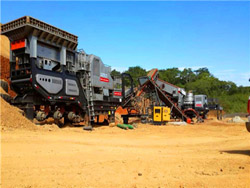
Kinetics of Dry-Batch Grinding in a Laboratory
With ball-mill grinding being one of the most energy-consuming techniques, setting the optimal values of the operational and mineralogical parameters for efficient grinding is a key target in mineral Jian, T. et al. Review of Ball Mill Grinding Mechanism Numerical Simulation and Mill Load Parameters Soft Measurement for Mineral Grinding Process. Journal of Beijing University of Technology. 44Study on shock vibration analysis and foundation
احصل على السعر
Influence of Planetary Ball Mill Parameters on Powder
of factors involved. e three main input parameters for regular mixing using a planetary ball mill are time (hours), speed(RPM),andNbCcomposition(%weight),whichplay a vital role in predicting powder flowability. e input parameters and levels are shown in Table 1. Based on the three input factors and five levels of each factor, 20 sets ofThe high-energy ball milling method was adopted to explore the influence of ball milling parameters, such as milling speed and additive amounts of process control agent (PCA) on tungsten powder. The morphology and microstructure of tungsten powder in the process of refinement were characterized by field-emission scanning electron Metals Free Full-Text Effect of Ball Milling Parameters on
احصل على السعر
Process engineering with planetary ball mills RSC Publishing
Processes inside planetary ball mills are complex and strongly depend on the processed material and synthesis and, thus, the optimum milling conditions have to be assessed for each individual system. The present review focuses on the insight into several parameters like properties of grinding balls, the filling ratio or revolution speed.The optimum conditions calculated by optimization were as follows: 58 rpm for as and 38.5 min for rt. The new working conditions identified for the ball mill considered enabled to rise output from 109 kg/h to 156 kg/h, with a 43% increase in productivity. A control experiment carried out in the optimized conditions to corroborate the resultsOptimization of processing parameters of a ball mill refiner
احصل على السعر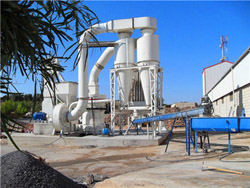
Variables in Ball Mill Operation Paul O. Abbe®
A Slice Mill is the same diameter as the production mill but shorter in length. Request Price Quote. Click to request a ball mill quote online or call 630-350-3012 to speak with an expert at Paul O. Abbe® to help you determine which design and size ball mill would be best for your process. See our Size Reduction Options.The parameter setting of the ball mill is. shown in Table 1. 2.5. Process Parameters and Selection Bas is. The process param-eters were investigated based on patent CN104889411A [29].Study on Preparation and Characterization of Graphene Based on Ball
احصل على السعر
Ball Mills 911 Metallurgist
Ball Mills or Rod Mills in a complete range of sizes up to 10′ diameter x 20′ long, offer features of operation and convertibility to meet your exact needs. They may be used for pulverizing and either wet or dry grinding systems. The parameter Wi, known as the work index of the ore, is obtained from batch bench tests first devised by
احصل على السعر