
Installed cost comparison for cement grinding systems
Installed cost comparison for cement grinding systems. Abstract: As the Vertical Roller Mill (VRM) becomes more widely accepted for new cement grinding systems differences in installed costs between a VRM and a ball mill system are more frequently According to the cost breakdown provided by Terembula (2004) and Conroy (1998) for new and upgraded cement plants in USA, purchase cost of the equipment for each production step accounts on...Installed cost comparison for cement grinding systems
احصل على السعر
Grinding process optimization IEEE Xplore
The modular vertical roller mill for grinding cement raw material, cement clinker, and additives with an installed power of up to 12,000 kW was specifically designed to meet the demand for increased grinding capacities and optimized maintenance concepts.Cement grinding and the different mill systems 3. Factors affecting cement mill performance 4. Improvement possibilities and case examples 5. Conclusions Roller Mill Investment cost [%] 100 125 130 Annual plant availability [%] 97 99 85 90 88 90 1-day Technical Seminar International Cement Review
احصل على السعر
Optimizing Operating Costs to Improve Profitability in a Cement
Level 1: Optimize the operation with no or very little investment by adjusting the operational strategy and attending to maintenance areas. Level 2: Improve operation through minor investments and staff training. Level 3: Incur into bigger investments; however, with Typical specific energy consumption is 30 kWh/t in grinding of cement. Barmac-type crushers found application as a pre-grinder in cement grinding circuits operating with ball mills to reduce the specific Energy-Efficient Technologies in Cement Grinding
احصل على السعر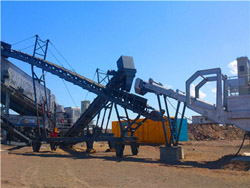
Cement Grinding Plant Price, 2023 Cement Grinding Plant Price
Cement Grinding Plant Price Select 2023 high quality Cement Grinding Plant Price products in best price from certified Chinese Cement Production Plant manufacturers, Cement Mixing Plant suppliers, wholesalers and factory on Made-in-China100.00. About 29% of the expense is spent on energy, 27% on raw materials, 32% on labor and 12% on depreciation in a cement industry. Therefore, cement industry is characterised by intensive industry throughout its production stages and the A critical review on energy use and savings in the cement industries
احصل على السعر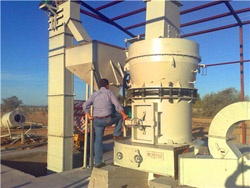
Review on vertical roller mill in cement industry & its
All grinding processes in the cement industry are operated dry. The capacities of grinding mills range from 300 − 1000 TPH for Limestone and for cement grinding it varies from minimum 50 TPH while larger installations are up to 450 TPH [8].Energy-efficiency measures for finish grinding in cement industry. This section describes measures to improve energy efficiency for the finish grinding process in cement plants. 5.1. Process control and management in grinding mills for finish grinding. An overview of energy savings measures for cement industries
احصل على السعر
Cement grinding: VRM or ball mill? LinkedIn
Investment cost. A VRM is a compact unit, making the footprint of the installation smaller and reducing the civil engineering costs when compared to a ball mill system. Savings are also made dueWhen grinding raw meal, the unit power consumption of the vertical roller mill and the roller press is about the same, which is 7-8kWh/t. But the vertical mill is usually slightly higher. The system of the vertical grinding mill is simple and stable. It has ideal adaptability to material moisture and can achieve the goal of energy saving on theComparison Of Cement Vertical Roller Mill And Roller Press
احصل على السعر
Mini Cement Plant EPC Cement Line Capacity 70 600 TPD
With quick building time and low investment cost, a mini cement plant is the best cement production solution for small and medium-sized cement manufacturers. AGICO designs and builds mini cement plants for you at the best price! preheater, rotary kiln, and cement grinding mill. Cement Crusher. The cement crusher is the key equipment for rawThe cement grinding plant is a vital link of the finished cement production. The cement grinding plant also called cement grinding unit, is used to grind clinker into qualified cement. With the development of the cement industry, cement grinding plant becomes more common. As an individual section of finished cement production, at this Cement Grinding Plant Overview Cement Grinding Unit AGICO Cement
احصل على السعر
Installed cost comparison for cement grinding systems
Abstract: As the Vertical Roller Mill (VRM) becomes more widely accepted for new cement grinding systems differences in installed costs between a VRM and a ball mill system are more frequently discussed. Past comparisons of total installation costs for a ball mill with high efficiency separator versus a VRM have indicated the higher equipment The coal mill uses coal, coke or grinded pet coke with different size of balls. Larger sized balls are used for impact grinding and the smaller balls are used for attrition grinding. 3.1.8. Cement mill. This is the final step in a cement manufacturing process. In this step, the clinker is ground together with additives in a cement mill.A critical review on energy use and savings in the cement industries
احصل على السعر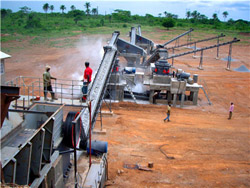
1 ASEAN GRINDING PROJECT KHD Humboldt Wedag
grinding system. Equipment description KHD provided a new energy-efficient 350tph comflex grinding circuit in finish mode to replace the line’s existing two ball mill circuits. KHD’s comflex grinding units are always engineered around a roller press as core grinding mill in close circuit with static and dynamic separators. Figure 1 and the16 October 2023. India: Dalmia Bharat has announced a planned investment of US$10.9m in a grinding unit expansion at its 1Mt/yr Banjari cement plant in Bihar. The expansion will raise the plant’s capacity by 500,000t/yr and conclude before 31 March 2025. Published in Global Cement News.Investment Cement industry news from Global Cement
احصل على السعر
Roller mills INFINITY FOR CEMENT EQUIPMENT
Roller mills have a lower specific energy consumption than tumbling mills, and require less space per unit and capacity at substantial lower investment costs. Roller mills are developed to work as air-swept grinding mills. With built-in air separators these mills grind in closed circuit, almost always as drying-grinding mills.In the project design, we will carry on the targeted design to these aspects, in order to lower the cement plant costs and obtain the best investment benefit. A cement plant built by AGICO. 2. Simplify process flow and reduce project scale reasonably. Engineering design is the key link to control the investment of a cement plant project.Lower Cement Plant Cost with 5 Strategies AGICO Cement
احصل على السعر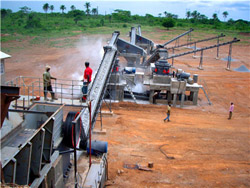
Towards a business case for CO2 mineralisation in the cement
The results reveal, first, that under rising ETS prices 41, the cost of producing ordinary Portland cement will increase by €0.85t cement −1 per €1t CO2 −1 increase in ETS price, if noIt is a kind of grinding equipment that used to grind the calcined cement clinker then make them reach the particle fineness requirement of the finished cement product. It is the core equipment of the last step in the Cement Manufacturing Machine Cement Making
احصل على السعر
Slag Mill
In addition, the slag mill can also be used in dry and wet grinding for all kinds of ores and other materials. Features 1. Low investment cost 2. Low run cost 3. High drying ability 4. Easy to operate, reliable performance 5. Stable quality 6. Convenient to maintain 7. Environmental protectionAbstract: As a world-wide leader in grinding solutions for the cement industry and understanding the changing needs of cement producers and how to tailor solutions to meet those needs. Optimizing output, improving efficiency, and reducing CO2 emissions while keeping investment costs to a minimum are common challenges that the modular vertical Grinding process optimization IEEE Xplore
احصل على السعر
A Review on Pyroprocessing Techniques for Selected Wastes
The energy efficiency of dry ball-mill grinding of cement depends on factors such as ball charge fill-ratio, mill length/diameter ratio, size distribution of the ball charge, operating conditions of the air separators, air flow through the mill, production rate, use of grinding aids, and the hardness and fineness of the feed and productAs the Vertical Roller Mill (VRM) becomes more widely accepted for new cement grinding systems differences in installed costs between a VRM and a ball mill system are more frequently discussed.Installed cost comparison for cement grinding systems
احصل على السعر
How Much Does It Cost To Start A Cement Plant?
According to the data we know, the total cost of a cement plant is estimated to be US$ 17,000 to US$ 20,000 per ton. One thing to be clear, this is just an estimation, in the real cement plant building, the cement factory cost is affected by various factors, including the significant difference in the cost of land, availability of limestoneAbstract: As the Vertical Roller Mill (VRM) becomes more widely accepted for new cement grinding systems differences in installed costs between a VRM and a ball mill system are more frequently discussed. Past comparisons of total installation costs for a ball mill with high efficiency separator versus a VRM have indicated the higher equipment Installed cost comparison for cement grinding systems
احصل على السعر
mill/sbm cost of setting up cement plant in india.md at main
Contribute to crush2022/mill development by creating an account on .
احصل على السعر