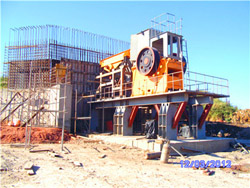
Cement Plants located in Malaysia The Global Cement Report
Cement Plants located in Malaysia Switch to statistics view Cement plant locations and information on Malaysia can be found below. For full access to the database, purchase Production of cement in Malaysia 2013-2022 Published by Statista Research Department,Mar 13, 2023 In 2022, approximately 19.86 million metric tons of cement were produced in Malaysia, a...Malaysia: cement production 2022 Statista
احصل على السعر
Malaysia Cementir Holding N.V.
Cementir Holding operates in Malaysia through Aalborg Portland Malaysia (APM), a company controlled 70% by the Group, with Adelaide Brighton as minority shareholder. APM operates in Malaysia both in the production Within southeast Asia, Malaysia represents one of the largest consumers of cement per capita. The lacklustre demand trends seen in the past 4-5 years were forecast to ameliorate in 2020 due to an influx Malaysia's cement industry faces a host of strategic
احصل على السعر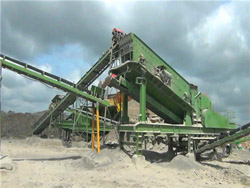
CEMENT I. Status of Industry a. Types of Products
Types of Products. Ordinary Portland Cement (OPC) HS 2523.29.900. White Cement HS 2523.21.000. Hydraulic Cement HS 2523.90.000. Blended Cement. Types of Cement Production in Malaysia averaged 1209.98 Thousands of Tonnes from 1985 until 2023, reaching an all time high of 2704.00 Thousands of Tonnes in March of 2023 and a record low of 147.00 Thousands of Malaysia Cement Production TRADING ECONOMICS
احصل على السعر
A Review on Carbon Emissions in Malaysian Cement Industry
This paper compares several methodologies for calculating CO2 emissions from cement production, including the three main components of emissions: direct The development of cement industry in Southeast Asian countries differs greatly, such as Vietnam's annual cement production capacity of more than 100 million Southeast Asia Cement Industry Report 2023: Cheap Labor and
احصل على السعر
Cement IEA International Energy Agency
Cement emissions intensity has remained relatively stable since 2018, at just under 0.6 t CO 2 per tonne of cement produced, following several years of modest increase largely due to an increasing clinker-to-cement ratio in China. To get on track with the NZE Scenario, emissions must fall by an average of 3% annually through to 2030.UPPC’s paper mill is located in Calumpit, Thailand, Vietnam, Indonesia, Philippines, Malaysia, and UK, providing packaging products and solutions to diverse industries such as food and beverage, electronics, of Siam Cement Group (SCG) 1995. SPPC and TUPI increased UPPC shareholdings to 99%. 2004.About Us SCGP
احصل على السعر
Malaysia Witnessed a Marginal Hike in the Prices of Cement and
Preserving Profit Margins. On November 18, 2022, the Malaysian government raised the list price of bagged cement from MYR19.25/50kg bag to a recommended retail price of MYR22.50/50kg bag in all regions of Malaysia. Typically, this led to a 17% increase in cement prices. according to the Sun Daily. The unit price index Palm Oil Fuel Ash (POFA) is by-product obtained by burning of fibers, shells and empty fruit bunches as fuel in palm oil mill boilers. In this investigation, three ashes were collected from different palm oil mills around Malaysia and namely CAPOFA, ALPOFA and KTPOFA. The ashes were ground to 45 μm before replace 20% by weight Palm Oil Fuel Ash: Promising supplementary cementing materials
احصل على السعر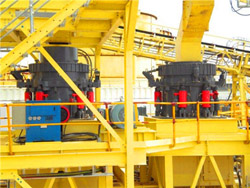
The cement mill
Cement manufacturing brief description of a cement mill. Cement clinker is usually ground using a ball mill. This is essentially a large rotating drum containing grinding media normally steel balls. However, reading an article or two is perhaps not the best way to get a clear picture of a complex process like cement production.11.6 Portland Cement Manufacturing 11.6.1 Process Description1-7 Portland cement is a fine powder, gray or white in color, that consists of a mixture of hydraulic cement materials comprising primarily calcium silicates, aluminates and aluminoferrites. More than 30 raw materials are known to be used in the manufacture of 11.6 Portland Cement Manufacturing US EPA
احصل على السعر
The Cement & Concrete Association of Malaysia Home
MS EN 197-2, Cement Part 2: Conformity evaluation. MS EN 196-1, Methods of Testing Cement Part 1: Determination of Strength. MS EN 196-2, Methods of Testing Cement Part 2: Chemical analysis of Cement. MS EN 196-3, Methods of Testing Cement Part 3: Determination of Setting Time and Soundness. MS EN 196-5, Methods of Testing It has been applied to the cement kiln process more than 170 times in 15 years, achiev-ing an impressive record of performance and sav-ings and creating value to for our the grinding circuit of a raw mill are an increase in output and a reduction in power consumption. Expert Optimizer has been successfully applied in more than 90 mills, toIndustrial : Optimization for the Cement Industry ABB
احصل على السعر
Digitization and the future of the cement plant McKinsey
There’s never been a more important time to build resilience into the core of the cement value chain: the cement plant. The cement industry is being hit hard by the COVID-19 pandemic, with global demand for cement expected to decline by 7 to 8 percent in 2020—though these declines have been unevenly distributed across regions. 1 Paul There are four stages in the manufacture of portland cement: (1) crushing and grinding the raw materials, (2) blending the materials in the correct proportions, (3) burning the prepared mix in a kiln, and (4) grinding the burned product, known as “ clinker ,” together with some 5 percent of gypsum (to control the time of set of the cement).Cement Extraction, Processing, Manufacturing Britannica
احصل على السعر
Cement Analysis and Production Information Thermo Fisher
The cement production process begins with the extraction of limestone and clay from the quarry. The material is then blended, crushed and fed to the kiln. Post-kiln, the clinker is cooled and goes through a final grinding method before it is ready to ship. Portland cement, the most common type of cement, is formulated in a variety of strengthsAbstract. An improved differential evolutionary cement mill operation index decision algorithm based on constraint control and selection strategy is proposed to address the problem that the operation index is usually decided by manual experience in the cement mill operation process, which causes unqualified cement specific surface area The Decision Algorithm of Cement Mill Operation Index Based
احصل على السعر
Cement mill
Cement mill. A 10 MW cement mill, output 270 tonnes per hour. A cement mill (or finish mill in North American usage [1]) is the equipment used to grind the hard, nodular clinker from the cement kiln into the fine grey powder that is cement. Most cement is currently ground in ball mills and also vertical roller mills which are more effectiveDownload scientific diagram Cement mill process from publication: DEVELOPMENT OF A FUZZY EXPERT SYSTEM BASED ON PCS7 AND FUZZYCONTROL++ CEMENT MILL CONTROL The basic idea of this work was toCement mill process Download Scientific Diagram ResearchGate
احصل على السعر
Top 10 Cement Companies in Malaysia Rankings, Reviews
3.Negeri Sembilan Cement Industries Sdn. Bhd. Cement Industries of Malaysia Berhad (CIMA), a wholly owned subsidiary of UEM Group Berhad, is one of the leading cement manufacturers in Malaysia. It is well known for producing and distributing high quality cement, ready mixed concrete and related products since 1975.There are two primary processes used to manufacture clinker: the dry process and the wet process. Our plants use the dry process, which is more energy efficient. In the wet process, the raw materials are mixed with water to form slurry, which is fed into a kiln. Fuel costs are greater in the wet process than in the dry process because the waterProduction Process CEMEX Philippines
احصل على السعر
Cement Manufacturing Process and Its Environmental Impact
The cement manufacturing process involves the extraction and processing of raw materials, such as limestone, clay, and shale, which are then heated in a kiln at high temperatures to form clinkerCement Manufacturing Process Phase 1: Raw Material Extraction. Cement uses raw materials that cover calcium, silicon, iron and aluminum. Such raw materials are limestone, clay and sand. Limestone is for calcium. It is combined with much smaller proportions of sand and clay. Sand & clay fulfill the need of silicon, iron and Cement Manufacturing Process Phases Flow Chart Cement
احصل على السعر
The Cement Manufacturing Process Thermo Fisher Scientific
Cement manufacturing is a complex process that begins with mining and then grinding raw materials that include limestone and clay, to a fine powder, called raw meal, which is then heated to a sintering temperature as high as 1450 °C in a cement kiln. In this process, the chemical bonds of the raw materials are broken down and then they Cement production processes involve complex chemical and physical reactions during the conversion of raw materials to the final product. Moreover, the clinker burning process, which has a decisive(PDF) Parametric Studies of Cement Production Processes
احصل على السعر