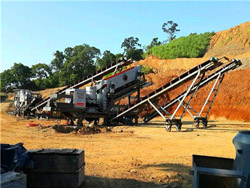
Influence of quick lime on pore characteristics of high-temperature
The pore structure of the bed has an important influence on the heat transfer and permeability characteristics in the iron ore sintering process. In this study, One of the most common fluxing materials for iron ore pellet production is limestone, which is mainly calcium oxide (CaO). In this study, the effect of adding Effect of adding limestone on the metallurgical properties of iron ore
احصل على السعر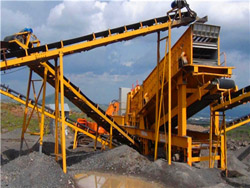
A new disposal method for white mud: Replacing limestone in iron ore
A new disposal method for white mud: Replacing limestone in iron ore sintering October 2023 Journal of Environmental Management 348:119331 DOI: In iron making process, sintering of iron ore fines is an integral step to utilize not only the ore fines but also to introduce a part of flux (limestone and dolomite) Basics of Iron Ore Sintering SpringerLink
احصل على السعر
Sinter Plant Operations: Raw Materials SpringerLink
The raw materials for an integrated steelworks can be classified into four categories, which are iron ores, fluxes, fuels, and reverts. The characteristics of these In modern blast furnaces, particularly those operating in East Asia, iron ore sinter constitutes more than 60% of blast furnace burdens. 1, 2 Good sinter quality Sintering Characteristics of Iron Ore Blends Containing High
احصل على السعر
Influence of limestone particle size on iron ore sinter
Iron ore fluxed sinter is the main ferrous burden of Jindal south west steel limited (JSWSL) blast furnaces. In sinter plant fluxes including limestone and dolomite are added to Sintering raw materials include iron ore powder (rich ore powder, concentrate powder), flux (limestone, dolomite, quicklime, etc.), fuel (coke powder and Iron Ore Sintering SpringerLink
احصل على السعر
Influence of Limestone Types on Iron Ore Sintering
It is possible to substitute all the iron ore (26.35–125.42 kg/t) and part of the limestone (34.40–160.02 kg/t) with increasing amounts of steel slag (from 43.04 to The total reaction involved in the process of sintering is the sum of a number of reactions which involve reactions in heating zone, reactions in sintering zone and reactions in cooling zone. These reactions are illustrated schematically for typical sintering of a lime-fluxed haematite ore in Fig. 11.CHAPTER-11 FUNDAMENTALS OF IRON ORE SINTERING
احصل على السعر
The Relationship Between Mining and Sintering
The only source of primary iron is iron ore, but before all that iron ore can be turned into steel, it must go through the sintering process. Sinter is created by mixing iron ore concentrate with several Sintering is a process where a mixture of ore, flux and coke is agglomerated (agglomerated) in the sinter plant to produce suitable sintered products in terms of composition, quality and(PDF) Iron ore sintering. Part 1. Theory and
احصل على السعر
Characteristics and Sintering Mechanisms of Iron Ores with a
In this study, a sintering test of high-alumina limonite from Indonesia, matched with an appropriate magnetite concentration, is performed. The sintering yield and quality index are effectively improved by optimizing the ore matching and regulating the basicity. For the optimal coke dosage of 5.8% and basicity of 1.8, the tumbling index of The inhibition effect of calcined lime (CaO) and limestone (CaCO3) on the formation of dioxins during iron ore co-sintering with fly ash was investigated in a sinter pot in the present work.(PDF) The Effect of Adjusting Sinter Raw Mix on Dioxins from Iron Ore
احصل على السعر
An efficient method for iron ore sintering with high-bed
It can be seen from Tables 1 and 2 that the blend with high iron grade has a high content of FeO (14.51 wt.%) because it consisted of 70 wt.% magnetite concentrate and 30 wt.% fine ore. The coke breeze has high fixed carbon content (83.37 wt.%) and low volatile matter content (1.57 wt.%). 2.2 Methods. The double-layer sintering process is Like other sintering processes, iron ore sintering converts iron ore fines of often − 8 mm sizing into larger agglomerates, namely, sinter, between 5 and 50 mm particle size, which possess the physical and metallurgical characteristics and gas permeability required for efficient blast furnace operation.As shown in Figure 14.1, iron ore sintering is Iron ore sintering ScienceDirect
احصل على السعر
Formation and distribution of dioxins in agglomerated
The physical and chemical properties for the four types of iron ores as well as limestone, hydrated lime and coke are summarised in Table 2 and Table 3. The sintering processes using the four types of iron ores are: Test 1, Test 2, Test 3 and Test 4, respectively. PCDD/F and PCB concentrations in sinter and dust samples via four iron F. Verdeja (2017) Iron Ore Sintering: Quality Indices, Mineral Processing and Extractive Metallurgy. Review, 38:4, 254-264, DOI: 10.1080/08827508.2017.1323744 The effects of limestone in(PDF) Iron Ore Sintering: Quality Indices ResearchGate
احصل على السعر
Influence of quick lime on pore characteristics of high-temperature
Five kinds of iron ore, return ore, limestone, dolomite, coke and quick lime were used in the experiment. The iron ore sintering experiment is carried out on the pilot-scale sinter pot system, as shown in Fig. 1. There are 5 pressure measuring points located at 100 mm, 200 mm, 300 mm, 400 mm, 500 mm from top to bottom of the pot to recordThe inhibition effect of calcined lime (CaO) and limestone (CaCO3) on the formation of dioxins during iron ore co-sintering with fly ash was investigated in a sinter pot in the present work. Experimental results indicated that international total toxicity equivalent concentration of dioxins decreased from 1.4335 to 0.2922, 0.1048, 0.4562, and 0.3098 The Effect of Adjusting Sinter Raw Mix on Dioxins from Iron Ore
احصل على السعر
(PDF) Iron Ore Sintering: Raw Materials and Granulation
Abstract and Figures. Sintering is an agglomeration process that fuses iron ore fines, fluxes, recycled products, slag-forming elements and coke. The purpose of sintering is to obtain a productThe pulp production process generates a CaCO 3-rich solid waste known as white mud (WM), and its improper disposal is a cause for global concern.The present study investigates the composition, microstructure, and thermal decomposition characteristics of WM and proposes a strategy for replacing limestone with WM for iron ore sintering.A new disposal method for white mud: Replacing limestone in iron ore
احصل على السعر
OPTIMIZATION OF IRON ORE PELLETS PRODUCTION IN
Sinter plant is one of the major departments of vsp where the iron ore pellets are produced by sintering process. By this sintering process the raw materials like limestone, dolomite, coke, iron ore fines and metallurgical wastes are converted into a solid mass i.e., pellets by using the heat produced by the incipient fusion during theSinter is the primary feed material for making iron in a blast furnace. During the iron ore sintering process in iron and steel manufacturing, sinter is created by mixing iron ore concentrate with several additives such as limestone and silica to control the chemistry and then igniting it at 1200°C in a continuous belt-fed furnace. The production How to Achieve Uniform Sinter Quality Analyzing Metals
احصل على السعر
Investigation on the evolution characteristics of bed porous
1. Introduction. Iron ore sintering is a pre-process of blast furnace ironmaking, which is very important for iron and steel production. In the iron ore sintering process, raw materials such as ore, flux, fuel and return ore are evenly mixed and granulated with water to form quasi-particles with larger particle sizes and stacked on the Iron ore sintering. L. Lu, O. Ishiyama, in Iron Ore, 2015. 14.5 Conclusions. Stacking and reclaiming: Crushed iron, coal, and limestone mined or brought from nearby with the help of railway wagons/ships. At the plant these are initially stored with the help of a stacker in piles. Different reclaimer types are used to reclaim the materialsIron Ore Sinter an overview ScienceDirect Topics
احصل على السعر
High Temperature Mineralization Mechanism of Granules During Iron Ore
Mineralization testing process included ore matching, agglomeration, roasting and mineralogical analysis. Iron ores and fluxes (dolomite, limestone, and quicklime) were mixed to a feed, which then was used to produce sinter with SiO 2 4.7%, basicity (CaO/SiO 2) 2.0 and MgO 2.0%, the proportions of each material were shown in Granulation and sintering are the two most important steps of the iron ore agglomeration process to produce sintered ore. Since granulation takes place at room temperature and is mainly characterized by physical and interfacial phenomena, while sintering is a thermal densification process involving extensive chemical reactions, the Sintering Characteristics of Iron Ore Blends Containing High
احصل على السعر
Microstructure and Minerals Evolution of Iron Ore Sinter:
SiO2 and Al2O3 are two important minerals that can affect the mechanical and metallurgical properties of sinter. This investigation systematically studied the influences of these minerals and revealed their functional mechanisms on sinter quality. Results showed that with an increasing Al2O3 content in sinter, the sintering indexes presented
احصل على السعر