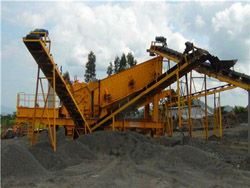
Grinding process optimization — Featuring case studies and
Grinding process optimization — Featuring case studies and operating results of the modular vertical roller mill Abstract: As a world-wide leader in grinding solutions for the The modular design of the vertical roller mill comprising 4 to 6 grinding rollers allows the continuation of mill operation even if one roller module is not available. Grinding Process Optimization Featuring Case Studies
احصل على السعر
Operational parameters affecting the vertical roller mill
This study investigated a mathematical model for an industrial-scale vertical roller mill(VRM) at the Ilam Cement Plant in Iran. The model was calibrated using the Vertical roller mill (VRM) is a type of heavy-duty and energy-intensive grinding equipment for many industries, such as cement, steel and chemical industries. It A data-driven decision-making framework for online control of vertical
احصل على السعر
(PDF) Analysis and Optimization of Grinding Performance of Vertical
PDF This work concentrates on the energy consumption and grinding energy efficiency of a laboratory vertical roller mill (VRM) under various operating Based on screening analysis, laser size analysis, grindability and rigidity tests of samples collected on line from a cement and a power plant, a simulation of the Grinding process within vertical roller mills: experiment and
احصل على السعر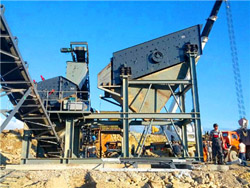
Roller Mill Based on Experimental Method ResearchGate
Roller Mill Based on Experimental Method. Minerals 2022, 12, 133. Keywords: energy consumption; grinding energy efficiency; response surface method; multi-objective DOI: 10.1016/S1674-5264(09)60018-1 Corpus ID: 110668154; Grinding process within vertical roller mills: experiment and simulation @article{Wang2009GrindingPW, [PDF] Grinding process within vertical roller mills: experiment
احصل على السعر
(PDF) Analysis and Optimization of Grinding Performance of Vertical
Productivity increase of the vertical roller mill for cement grinding. In Proceedings of the IEEE Cement Industry T echnical Conference, Hershey,P A, USA, 20–24 April 1997.The to-date biggest mill size modular vertical roller mill 6700 C-6 shows satisfactory results for cement and co mposite cement grinding. T his mill, install ed in Northern Africa, i s in(PDF) Grinding process optimization — Featuring
احصل على السعر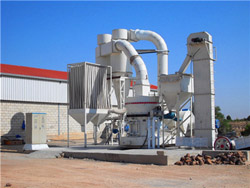
Modeling of energy consumption factors for an industrial
The raw vertical roller mill has four rollers, 3000 KW main drive, 4.8 m table diameter, 2.16 m roller diameter with 330 t/h capacity (made by LOESCHE Company from Germany).The new design of roller mill assembly consists of two rotating rollers with outer rings, between which a grinding plate is fixed permanently and the rollers are connected to drive shafts. The mill is equipped with a hopper and a grinding product basket.A study of operating parameters of a roller mill with a new
احصل على السعر
A cement Vertical Roller Mill modeling based on the
The two-time breakages are far closer to the actual product size distribution. This study investigated a mathematical model for an industrial-scale vertical roller mill (VRM) at the Ilam Cement Plant in Iran. The model was calibrated using the initial survey's data, and the breakage rates of clinker were then back-calculated.Analysis and Optimization of Grinding Performance of Vertical Roller Mill Based on Experimental Method Chang Liu 1,2, Zuobing Chen 1, Ya Mao 1, Zhiming Yao 1, Weili Zhang 2, Weidong Ye 2, YuanyuanRoller Mill Based on Experimental Method ResearchGate
احصل على السعر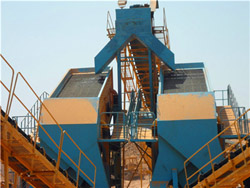
Grinding process optimization — Featuring case studies and
As a world-wide leader in grinding solutions for the cement industry and understanding the changing needs of cement producers and how to tailor solutions to meet those needs. Optimizing output, improving efficiency, and reducing CO2 emissions while keeping investment costs to a minimum are common challenges that the modular vertical roller A cement Vertical Roller Mill modeling based on the number of breakages. Vertical roller mills (VRM) are widely used to grind, dry, and select powders from various materials in the cement, electric power, metallurgical, chemical, and nonmetallic ore industries. For the sectors above, the VRM is a powerful and energy-intensive grinding Operational parameters affecting the vertical roller mill
احصل على السعر
Roller Mill Based on Experimental Method mdpi-res
optimization studies on energy consumption and grinding energy efficiency for a VRM. There are usually four kinds of VRMs in the cement production line, including raw meal mill, coal mill, Clinker Mill and cement mill, and the vertical mill occupies a large energy consumption unit.The vertical roller mill (VRM) is a new type of grinding equipment, which is the preferred equipment for raw meal grinding globally. The grinding process has the comprehensive complexity of strong nonlinearity, multi-variable strong coupling, large lag, time-varying parameters and uncertainty, and the current research on the mechanism of Research progress on control optimization of vertical roller mill
احصل على السعر
Grinding process within vertical roller mills: experiment and
This paper describes the simulation of the grinding process in vertical roller mills. It is based on actual experimental data obtained on a production line at the plant and from lab experiments. Sampling and experiments were also carried out in a power plant that has four ball-mill circuits used for coal grinding so that different equipmentObjective of this research paper is process optimization of Vertical roller mill, improvement in productivity and reduction in vibration breakdowns using seven QC tools. [10] Amudha Ganesan G. 2016 A Study on the Operating Efficiency of Major Cement Companies in South India International Journal Of Advanced Scientific Research & Increase productivity of vertical roller mill using seven QC
احصل على السعر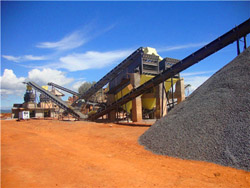
Analysis and Optimization of Grinding Performance of Vertical Roller
This work concentrates on the energy consumption and grinding energy efficiency of a laboratory vertical roller mill (VRM) under various operating parameters. For design of experiments (DOE), the response surface method (RSM) was employed with the VRM experiments to systematically investigate the influence of operating parameters on The vertical roller mill (VRM) is commonly used for secondary and tertiary crushing processes in numerous industries. In this study, the discrete element method (DEM) was employed to explore the crushing in an overflow VRM without air involved via the bonded-particle model (BPM).Analysis of vertical roller mill performance with changes in
احصل على السعر
VRM optimisation International Cement Review
VRM optimisation. Most new cement plants utilise vertical roller mills (VRM) for raw material grinding and preparation. Taking a step-by-step look at the entire roller milling process, Kline Consulting recommends routine measurements and discusses ways to overcome chemical issues to optimise operations. • incorporation of drying with The objective of the study, is to draw attention to the need of Cement grinding process optimization to minimize power consumption and achieve higher productivity. In the study the advantages of vertical roller mill are discussed over ball mills. VRM construction, its process and parameters which affects the performance and Review on vertical roller mill in cement industry & its
احصل على السعر
Numerical Study of the Flow Field in a Vertical Roller Mill
In order to reduce the larger pressure resistance (pressure difference between inlet and outlet) of a vertical roller mill, the flow field in the vertical roller mill is numerically simulated by CFD technology. Based on the simulation results, the reasons that led to the larger pressure resistance of the vertical roller mill is studied, offering the energetic efficiency of vertical roller coal mill, International Journal of Coal Preparation and Utilization, DOI: 10.1080/19392699.2020.1799200 To link to this article: https://doi.or g/10.1080An investigation of performance characteristics and
احصل على السعر
Optimizing Raw Mills Performance ; the Materials WAY
Traditionally vertical roller mills operate with feed around 80—100 mm size but reducing this to lower size has proven beneficial to capacity enhancement in number of plants; with ball mills theThis study investigated a mathematical model for an industrial-scale vertical roller mill(VRM) at the Ilam Cement Plant in Iran. The model was calibrated using the initial survey's data, and the(PDF) An approach to measuring and modelling the
احصل على السعر