
The Global Cement Report: Data for Philippines
This interactive chart requires a subscription toThe Global Cement Report. View cement industry statistical data for Philippines, South Asia, including cement consumption, production, Capacity, Consumption per Capita, There are 16 active integrated cement plants in the Philippines that share a combined capacity of 33.6Mt/yr, according to research undertaken towards the ‘Build, Build, Build’-ing in the Philippines Global Cement
احصل على السعر
Production Process CEMEX Philippines
Products & Solutions Cement Production Process Production Process We source our limestone, pozzolans and clay primarily from ALQC and IQAC. We also source raw Main players in the market are Cemex Philippines, Holcim Philippines inc, Eagle cements to name a few. The report contains a comprehensive analysis on: Philippines Cement Industry Market Analysis, Forecasts and
احصل على السعر
Holcim Philippines announces cement capacity
To better support the country’s strong economic development and robust construction activity, building solutions provider Holcim Philippines, Inc. will invest close to $300 million to raise its FLSmidth has been chosen by San Miguel Northern Cement Inc., Ionic Cementworks Industries Inc. and Oro Cemento Industries Corporation for engineering and procurement FLSmidth wins cement orders in Philippines Cement Lime
احصل على السعر
Eagle Cement to complete Bulacan mill by Q1 2021 Philippine
MANILA Eagle Cement Corp. is set to finish its milling facility in San Ildefonso, Bulacan by the first quarter of 2021. In a statement Tuesday, the firm said it DESCRIPTION SikaGrind®-874 PH is a chloride free liquid cement grinding aid with performance enhancing properties. SikaGrind®-874 PH has been specifically PRODUCT DATA SHEET SikaGrind®-874 PH Sika
احصل على السعر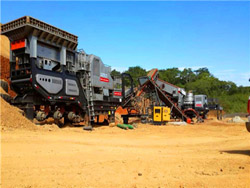
Cement industry seen to grow 12% this year
It means 12-percent growth compared to 2020,” he said in a press conference Tuesday. Francis said the industry is expected to sell 35 million tons of cement this year. “The main driver is the bagged (cement) The current world consumption of cement is about 1.5 billion tonnes per annum and it is increasing at about 1% per annum. The electrical energy consumed in cement production is approximately 110. kWh/tonne, and around 40% of this energy is consumed for clinker grinding.. There is potential to optimise conventional cement clinker Cement grinding optimisation ScienceDirect
احصل على السعر
Energy and cement quality optimization of a cement grinding circuit
Abstract. This study aimed at optimizing both the energy efficiency and the quality of the end product by modifying the existing flowsheet of the cement grinding circuit. As a general application, mill filter stream is sent to the air classifier owing to its coarser size distribution than the desired product. However, the study proved that some1. Ordinary Portland Cement (OPC) This is the most popular type of cement used for building projects, mortar, and stucco. OPC also have affordable price compare to other cement. 2. Portland Pozzolana Cement (PPC) It is more resistant to chemical reactions and is often used for bridges, piers, dams, and marine buildings.Cement Price List and Buying Guide in Philippines 2023
احصل على السعر
Energy and exergy analyses for a cement ball mill of a new
Nowadays, ball mills are used widely in cement plants to grind clinker and gypsum to produce cement. In this work, the energy and exergy analyses of a cement ball mill (CBM) were performed andThe cement factory where the measurements were made was located in Romania’s center-north and had a final section with two cement mills. Cement grinding was performed inside the cement mill workshop. This manufacturing phase’s product was cement—a powdery, finely ground material in closed-loop tubular ball mills (Figure 1). Dust Emission Monitoring in Cement Plant Mills: A Case
احصل على السعر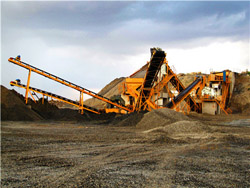
Dust Emission Monitoring in Cement Plant Mills: A Case
The cement factory where the measurements were made was located in Romania’s center-north and had a final section with two cement mills. Cement grinding was performed inside the cement mill workshop. This manufacturing phase’s product was cement—a powdery, finely ground material in closed-loop tubular ball mills . The monthly Some investigations observed that VRM installation in grinding saves 30% of cement mill energy with ease of control and reduces the mill start-up/shut down durations [1,2,3,4, 5].(PDF) Predictive Control of a Closed Grinding Circuit System in Cement
احصل على السعر
IMPROVING PRODUCTIVITY BASED ON THE MOVEMENT
Fig. 1. Illustration of the cement mill Z1 in kufa cement plant. 2.2. The principle of grinding process The idea of grinding clinker and turning it into cement with a certain specific surface is basedQ. Raw mill air seperator -26 R. Finish grinding mill feed belt -27 S. Finish grinding mill weight hopper -28 T. Finish grinding mill air seperator -29 U. Preheater kiln 3-05-006-22 V. Preheater/Precalciner kiln 3-05-006-23 The second step in portland cement manufacture is preparing the raw mix, or kiln feed, for the11.6 Portland Cement Manufacturing U.S.
احصل على السعر
Effects of Polycarboxylate-based Grinding Aid on the
A molecular modified PCE-type GA was self-synthesized, and the grindability concerning grinding duration and particle size distribution of ground cement was evaluated. Setting time, flowability, hydration heat, mechanical properties and microstructure of the ground cement were also investigated. The results show that: PCE-type GA is Research highlights Extensive sampling campaign was performed around the cement grinding circuit of a cement plant in Turkey for the modelling and simulation purposes. Ball size adjustment was the major optimization for the capacity improvement for that case study. The capacity of the circuit was increased up to 12.7–20.5% for different Simulation assisted capacity improvement of cement grinding
احصل على السعر
what is throughput for a cement grinding ball mill? LinkedIn
Throughput in a cement grinding ball mill refers to the amount of material that is ground and discharged from the mill per unit time. It is usually measured in terms of tons per hour or tons per day.Global Mill Liner Market . Global Mill Liner Market was valued US$ XX Mn. in 2020 and is expected to reach US$ XX Mn. by 2026. Mill liners provide the wear-resistant surface within grinding mills and impart motion to the grinding process. They are one of the key factors for enhancing the movement of the charge within the mill shell. Get Priceamount of cement grinding mill philippines
احصل على السعر
sbm/sbm cement mill in philippines.md at master sbm
You can not select more than 25 topics Topics must start with a letter or number, can include dashes ('-') and can be up to 35 characters long.On the other hand for fine grinding (> 3,000 blaine), the main factors become: 1) alite size, as before 2) C2S content,as before 3) grinding aid. As the cement particle gets smaller the pores disappear and no longer become a factor. Increasing the amount of grinding aid will make the cement easier to grind.Cement Mill Ball Mill Dynamics PDF Mill (Grinding
احصل على السعر
Effect of Feed Amount and Composition on Blaine and
Grinding Mill: The obtained data were generated using a ball mill shown in Figure 1. The mill was mounted on a milling rig and allows a wide range of mill speeds to be used. Two chamber mills are used for grinding clinker and additive materials (pozzolana and gypsum). They are typically[Show full abstract] performances of these cement grinding technologies, industrial scale data were collected from HPGR-ball mill, VRM, Horomill and multi-chamber ball mill closed circuits.The(PDF) Pregrinding technology ResearchGate
احصل على السعر
(PDF) A Survey and Analysis on Electricity Consumption
In the whole process of cement production, the electricity consumption of a raw material mill accounts for about 24% of the total. Based on the statistics of the electricity consumption of the rawFor example, instead of regrinding the separator reject in the tube mill, it can be directed to a stirred mill. Thus a possible energy saving can be obtained compared to ball mill grinding. Because, stirred mills are reported to supply energy savings below 100 μm product sizes [5] such as for finish cement (−30 μm).Open and closed circuit dry grinding of cement mill rejects
احصل على السعر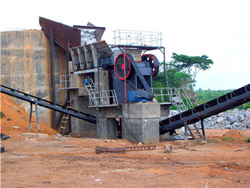
The energy efficiency of ball milling in comminution
In terms of this concept, the energy efficiency of the tumbling mill is as low as 1%, or less. For example, Lowrison (1974) reported that for a ball mill, the theoretical energy for size reduction (the free energy of the new surface produced during grinding) is 0.6% of the total energy supplied to the mill setup.
احصل على السعر