
A review of modeling and control strategies for cone crushers
We review the state of the art developments in process modeling and cone crusher control from 1972 to 2020. • The steady-state model of Whiten (1972) is still used The size reduction process of rocks in cone crushers is one of the most important issues, particularly for the secondary and tertiary stages of crushing Evaluation of size reduction process for rock aggregates in cone crusher
احصل على السعر
Chamber Optimization for Comprehensive
This study aims to analyze the impact of key structural parameters such as the bottom angle of the mantle, the length of the An improved capacity model of the cone crushers based on the motion characteristics of particles considering the influence of the spatial compound motion of the mantle was established by analyzing the Minerals Free Full-Text An Improved Capacity
احصل على السعر
Influence of Two Mass Variables on Inertia Cone
In this paper, the process of crushing steel slag is taken as a specific research object, to analyze the influence of two mass variables on the inertia cone crusher performance. A real-time dynamic model based Introduction Process control in crushing lags several decades behind other industries such as paper, pulp, energy, and petrochemical. The industry practice is still Size reduction control in cone crushers ScienceDirect
احصل على السعر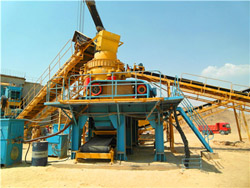
Applied Sciences Free Full-Text Prediction of
The model is important for predicting cone crusher performance along with liner wear. This work can be used for improving cone crusher performance. In addition, this paper describes a method for 1. Introduction Even though the original cone crusher patents were accepted almost 100 years ago (in the mid 1920's by E B Symons), the cone crusher concept Geometric analysis of cone crusher liner shape
احصل على السعر
Modelling of flow in cone crushers ScienceDirect
Abstract The possibility to simulate and predict cone crusher performance is of great interest for the development of crushers as well as for the design and The spring cone crusher design is able to pass uncrushable materials e.g. tramp metal, through the crushing cavity by using springs. The first hydraulic cone crusher was developed in 1948 and this allowed for the opening of Cone Crushers (Parts of a Cone Crusher) Explained
احصل على السعر
Minerals Free Full-Text An Improved Capacity
A cone crusher is a core component of the particle crushing process employed in various industrial sectors [].Capacity is one of the most important indexes of cone crushers, which determines the A range of possible solutionsto address the segregated feed is studied. The internal size reduction process occurring in a cone crusher is also modelled an simulated byapplying DEM. The results of(PDF) Application of discrete element method for
احصل على السعر
McLanahan CMB Cone Crushers
Below are suggested speed guidelines for CMB Cone Crushers: Low speed: Secondary applications, after a Jaw Crusher. Medium speed: Gravel applications with coarse feed. Standard speed: Tertiary applications (0 x 1/2”) High speed: Sand applications (4m or less) Speed ranges: Smaller head diameters (48” or smaller): 750-1,200 rpm.The interaction between these two models is quite complex as the overall size reduction in a cone crusher is a result of a repeated consecutive comminution process. The flow model is important since it describes how the rock material moves through the crusher chamber. Thereby the flow model provides input to the size reduction model.Modelling of flow in cone crushers ScienceDirect
احصل على السعر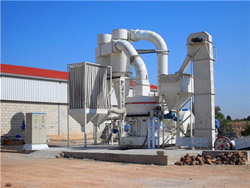
Size reduction control in cone crushers ScienceDirect
Data acquisition and control system for the experiment was built on a National Instruments cDAQ-9188 CompactDaq hardware and a LabVIEW software running on Windows PC with 1 Hz cycle rate for process control and data logging. Cone crusher size reduction control (Itävuo et al., 2012, Itävuo et al., 2013) was realized using a discrete The Nordberg® HP Series™ cone crusher product family includes altogether ten models. HP100 HP200 HP300 HP400 HP500 HP900 HP3 HP4 HP6 HP Series cone crushers provide predictable and consistent capacity, end product size, gradation and shape, making them a safe choice for aggregates and mining processes.Nordberg HP Series cone crushers High performance
احصل على السعر
CONE Chalmers Publication Library (CPL)
production costs. Prediction of crusher performance has been focused on, since crushing is a vital process for both industries. In this thesis a method for prediction of cone crusher performance is presented. The model is based on the laws of mechanics and constitutive relations concerning rock breakage characteristics.Nordberg® GP™ cone crushers have a simple but strong two-point supported shaft design that offers mechanical reliability. Furthermore, the GP cone crushers are equipped with automation system that continuously monitors crusher load and operating parameters to ensure optimal operating condition and maximized availability.Nordberg® GP Series™ cone crushers TON
احصل على السعر
Applied Sciences Free Full-Text Prediction of Cone Crusher
Cone crushers are used in the aggregates and mining industries to crush rock material. The pressure on cone crusher liners is the key factor that influences the hydraulic pressure, power draw and liner wear. In order to dynamically analyze and calculate cone crusher performance along with liner wear, a series of experiments are performed Therefore, the working process of the cone crusher is taken as the specific analysis object, and considering the amount of ore uplift, the traditional mathematical model of crusher productivity was Chamber Optimization for Comprehensive
احصل على السعر
Analysis and optimization of cone crusher performance
The objective of cone crusher optimization is the maximal output of the cone crusher, as shown in Eq. (7). The product quality including particle size and particle shape are taken as constraints of optimization, as shown in Eq. To accurately simulate the crushing process of the ore in the crusher based on the discrete element method (DEMFrom large primary jaws and gyratories to cone and impact crushers for tertiary and quaternary finishing, TON equipment is manufactured to meet your material reduction requirements. The crushers are built to perform with the lowest cost per ton, featuring a unique combination of crusher cavity design, crushing forces, reliability and safety.Crushing TON
احصل على السعر
Crushing and Screening Handbook AusIMM
mum production capacity by adjusting process parameters on-line. Original wear and spare parts using origi-nal TON wear parts is the key to a successful crushing process. The design of our certifi ed wear parts starts with CAD simulations of the crusher cavity, which is the heart of the crush-ing process. By computer based planning andNordberg® MP™ crushers bring cone crusher performance to a new level. They provide the highest crushing power for any cone crusher of similar size. Advanced crushing dynamics leads to more work per cycle. The MP™ crushers increase the power draw resulting in an increase in capacity, and a higher power-to-production ratio and energy efficiency.Nordberg® MP Series™ cone crushers TON
احصل على السعر
Research on the Wear Behavior of the Fixed Cone Liner of a Cone Crusher
Taking reducing the wear of the fixed cone liner of a cone crusher as the starting point, the movement and geometry parameters of the cone crusher are studied using the discrete element method. To improve the service life and working efficiency of the whole cone crusher. The UG model and discrete element Yade model of the cone mechanism used. Crushers are classified based on mechanism are of three types namely Cone crusher, Jaw crusher, Impact crusher. Cone Crushers are used as secondary crushers in mine or ore processing plants where the process of reduction in size takes place. They follow ‘crush using compression’ mechanism. 2. Literature reviewCrusher &RQH&UXVKHU IOPscience
احصل على السعر
Energy Efficiency of a Cone Crusher with Stops SpringerLink
The crushing process in a cone crusher is more energy efficient than that in a compression crusher, allowing for smaller motors and lower energy costs. Theoretically, the reduction in the force required to break brittle materials can be twice as much. Crushing a piece due to shear forces and the constant size of the discharge gap of a coneThis paper reports the calibration and validation of a cone crusher model using industrial data. Usually, there are three calibration parameters in the condensed breakage function; by contrast, in(PDF) Calibration and Validation of a Cone Crusher Model
احصل على السعر
Geometric analysis of cone crusher liner shape
This simplicity also allowed the Whiten crusher model (Whiten, 1972) to describe jaw crusher performance with only three parameters K1 which correlates with CSS, K2 which relates to OSS and t 10 which provides for a similar degree of severity of breakage for each particle which is caught and a probability curve for capture.The
احصل على السعر