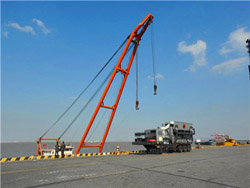
Driving investments in ore beneficiation and scrap upgrading
Three iron ore pellets existing in the market with different contents of silica are studied. For DRI calculations, the metallization and carbon contents are set to 94% and 2%, respectively. The chemical compositions of the iron ore pellets and their This chapter first provides an overview of world iron ore production and trade, as well as reserves and resources, followed by a summary of the key mining Introduction: Overview of the global iron ore industry
احصل على السعر
Iron Ore Pelletizing Process: An Overview
Iron ore and iron ore pellets are important sources of iron for manufacturing steel. The iron ore production has significantly With the growing demand for steel and the transition towards the green H 2-based direct reduction process, there is a significant expected increase in the demand Sustainability Free Full-Text Developing Iron Ore Pellets
احصل على السعر
(PDF) EVOLUTION AND GROWTH OF IRON ORE
Iron Ore Mineral Unit Capacity Fuel Type atite ore mix es whereas the use of GK for this application is lim ited. c) Pulverized Coal no yes GK can use pulverized coal injection in burner....Jose Murilo Mourao. PDF In the last years, pelletizing has been playing an important role in iron ore mining and in iron production (iron making and direct reduction). Find, read and cite(PDF) THE GROWING IMPORTANCE OF
احصل على السعر
Iron ore pelletization ScienceDirect
A brief introduction to recent developments in iron ore pelletizing is provided in this chapter, including the world output of fired pellets, pellet production processes, Iron ore pellets are essential inputs for producing direct reduced iron (DRI), but the conventional binders, used in iron ore pelletizing, introduce gangue oxides to the DRI and consequently(PDF) Iron Ore Pelletizing Process: An Overview
احصل على السعر
Rikard Edland Chalmers Publication Library (CPL)
The production of iron ore pellets, which is vital to the production of steel, is expected to be an important industry for many years to come. The pelletizing of iron Merchant DR-grade iron ore pellet demand may increase to 53 million mt in 2025 from about 38 million mt in 2020, and rise to 81 million mt in 2030, according to IIMA estimates. Around 28.5 million mt of estimated market-based DR pellet demand in 2030 is expected to come from new DR plants, mainly in Europe and the MENA region, at which DRI to underpin carbon-neutral steel; growth needed in pellet
احصل على السعر
Recycling and Reuse of Iron Ore Pellet Fines SpringerLink
During the process of iron ore pelletization and preparation of feed for DRI or reduction smelting processes, around 3% of pellet fines (less than 8 mm) are generated as undesired product in the existing pellet plants. Such pellet fines acquire more than 24 million tonnes generated all over the world. Recycling and reuse of these high gradeOur manufacturer has designed and supplied Grate Kiln for several pellet plants, playing a leading role in the industry of China. The specification ranges from φ4.0×30m to φ6.4×45mm, and theGRATE KILN is the most cost-efficient system for
احصل على السعر
Sustainability Free Full-Text Developing Iron Ore Pellets
The transformation from traditional iron- and steelmaking technologies to green H2-based new technologies will require an improvement in the quality and purity of iron ore burden materials. Iron ore pellets are essential inputs for producing direct reduced iron (DRI), but the conventional binders, used in iron ore pelletizing, introduce gangue 1. Introduction. According to the Ministry of Steel Policy 2017 declared by the Indian government, the requirement of low-grade iron ore is about 800 million tons for the production of 300 million tons of steel by 2030 [1].To meet this targeted steel demand, shifting the focus towards the utilization of banded iron ore such as banded hematite Pelletization of synthesized magnetite concentrate obtained
احصل على السعر
Reduction of low grade iron ore pellet using palm kernel shell
The ores were consumed mainly by the local cement, iron and steel plants. The Malaysian Iron and Steel Federation (MISF) estimated that the country's steel consumption increased by about 24% to 8.2 million tonnes in 2010 [3], [5]. At present, Malaysia's steel industry imports its raw material in lump and pellet forms as the mills that utilize this process also have auxiliary operations in the form of coke and sinter/pellet plants. According to the American Iron and Steel Institute, coke is the most important raw material fed into the blast furnace (Valia, 2015). It is used to reduce iron ore to iron. High quality coal is heated in an oxygen-Cost Effectiveness Analysis of HYL and Midrex DRI
احصل على السعر
Modeling and Simulation of the MIDREX Shaft Furnace:
The direct reduction is a process for reducing iron ore and producing sponge. There are several technologies, like MIDREX1 and H.Y.L2 using the countercurrent shaft furnace to make sponge iron.. In MIDREX technology, the furnace is a vertical shaft (Fig. 1).A charge of pelletized or lump ore is loaded into the top of the furnace and M 1 1.599 25 N.A Iron ore pellets Pellet heater M 2 1.599 800 370.78 Heated iron ore pellets Pellet heater M 3 0.0812 500 155.59 H 2 entering the shaft furnace Shaft furnace(PDF) Decarbonization of the Iron and Steel Industry with
احصل على السعر
Tosyali Algerie Sets DRI Production Record in 2021,
MIDREX NG provides greater raw material flexibility by allowing the use of DRI-grade pellets, blast furnace-grade pellets, and lump ores. Compared to blast furnace ironmaking, a standard MIDREX NG plant can reduce CO 2 emissions by more than 50% and has the flexibility to be converted from 100% natural gas to 100% hydrogen as the The quality requirements of pellet, such as physical, chemical and metallurgical specifications, depend on each ironmaking furnace and thoserequirements influence the operation ofthe iron ore pelletizing plant. The idea of rolling moist fine ore in a drum to form balls and then drying and firing it was firstIron Ore Pelletizing Process: An Overview IntechOpen
احصل على السعر
Process through Multiscale Process Modeling
Iron ore pellets are charged at the top, descend due to gravity, and encounter an upward counter-flow of gas. The reducing gas (CO and H 2, plus CH 4, CO 2, and H 2O, at about 950 °C) is injected peripherally at mid-height and exits at the top. In the lower section of the furnace, of conical shape, cold natural gas is injected to cool the ironArrium Australia 0.810 0.810 0.440. 440 Iron Ore. The pelletizing process involves the preparation of ra w materials; the proportioning. and mixing of raw materials; the formation, preheating, and(PDF) Iron ore pelletization ResearchGate
احصل على السعر
Pellet feed grinding by HPGR ScienceDirect
Apart from tertiary and quaternary crushing applications in a wide variety of ore types, High Pressure Grinding Roll (“HPGR”) technology is also applied in regrinding of iron ore pellet feed concentrate. A relatively large number of units have been or are being installed in iron ore pellet feed over the last few years throughout the world, in various The MOU is to study the development of a high-quality iron ore logistics and processing facility, according to an NIDC statement circulated on Oct. 30. Ras Al-Khair is close to the industrial port city of Al Jubail, which currently imports pellets for direct-reduced iron, or DRI, plants.Brazil's Vale, Saudi Arabia's NIDC sign MOU for iron ore pellet plant
احصل على السعر
Inside Vale’s green briquette megahubs and how they will work
Saudi Arabia’s National Industrial Development Center has signed a Memorandum of Understanding with Vale to develop a 4 million tonne per year iron ore pellet plant in Ras Al-Khair Industrial City, it said. Vale’s efforts shine a spotlight on the increasing emphasis on metallics and direct-charge materials in the steel industry.In November 2022, Brazilian miner Vale, the third-largest iron ore miner and largest producer of iron ore pellets in the world, signed a memorandum of understanding (MoU) with Saudi Arabia’s National Industrial Development Center to construct an iron ore pelletising plant in Ras Al-Khair Industrial City. The plant would have an annualMENA, a potential new hub for green steel and green iron
احصل على السعر
Effects of Pellet Basicity on the Simulated Deposit Formation
1. Introduction. Iron ore pellets are an essential part of the blast furnace charge, with high grade, good strength, uniform particle size, good metallurgical properties, and so forth. 1,2 Especially, fluxed iron ore pellets have better high-temperature soft fusion performance and reduction performance. 3−5 However, the burden of the blast furnace is • ABB also conducting engineering, commissioning, project management and installation in pellet and concentrating plants. Swedish mining company LKAB dates back around 130 years and produces today 80 percent of all iron ore in Europe.ABB to provide electrification and automation technologies
احصل على السعر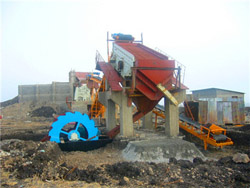
Iron Ore Pellets JSTOR
Iron Ore, 1969 (Cleveland: American Iron Ore Association, 1970), pp. 54-55. (Table 2, p. 515) suggests that Mason's data are incorrect.3 3) (p. 542) "In 1955 the first commercial production of taconite pellets was accom-plished by the Erie and Reserve Mining companies at Aurora, and Silver Bay, Min-nesota, respectively." This statement is in
احصل على السعر