
Gold Mining Process
November 1, 2021 O3 Mining The gold mining process is complex and goes beyond what most people imagine — miners in hard hats working underground or operating large, Classification of the milled ore is achieved using cyclones, which separate and sort fine particles in a liquid suspension for downstream processing, and return coarse material to the ball mill for Gold Fields South Deep Gold Mine How we
احصل على السعر
Comminution Circuits for Gold Ore Processing ScienceDirect
1. Introduction. For the vast majority of ounces of gold produced, comminution costs in the form of power, grinding media, and liners represent the single Gold processing Mining, Concentrating, Refining: The nature of the ore deposit determines the mining and mineral processing techniques applied. Oxide ore deposits are frequently of such low grade (e.g., 3 to 10 parts Gold processing Mining, Concentrating, Refining
احصل على السعر
Gold Process Mineralogy: Objectives, Techniques, and
gold in sulfi de and sulfarsenide mineral structures. Gold process mineralogy addresses all issues related to gold ore processing by the detailed study of Environmental characterization studies for gold processing include ore, waste, stockpile, tailings and residue material characterization, potential run-off material Metallurgical Test Work: Gold Processing Options, Physical
احصل على السعر
Development of ultrafine grinding at Kalgoorlie
Key words: Ultrafine grinding, Gold processing, Refractory ore, Pyrite, Vertical stirred mills, Cyanide leaching Introduction Kalgoorlie Consolidated Gold Mines The conditions of the grinding process have an impact on the surface chemistry of the minerals which is critical for the subsequent flotation process. This study A practical guide to re-treatment of gold processing residues
احصل على السعر
Combined Column and Mechanical Flotation Cell
Semi-industrial tests were conducted to investigate the feasibility and efficiency of a combined column and mechanical flotation cell process for the beneficiation of Sanshandao low-grade gold ore. The The collected samples were analyzed for 13 heavy metals including vanadium (V), chromium (Cr), manganese (Mn), nickel (Ni), copper (Cu), cadmium (Cd), cobalt (Co), lead (Pb), zinc (Zn), aluminiumThe environmental impact of gold mines:
احصل على السعر
Crushing Energy Efficiency North American Mining Magazine
According to one estimate, the mining industry consumes 12EJ per year of energy or 3.5% of total final global energy consumption.1 The energy intensity of mining is also predicted to increase over time as deposits that are lower quality, deeper and more difficult to extract are mined.It has been estimated that grinding consumes up to 4% of global electrical energy and accounts for more than 50% of the total energy used in mining operations. In addition, more than 90% of the total energy supplied in beneficiation plants is dissipated as heat, kinetic energy, noise, and inefficient breakage of ores/raw material.Minerals Special Issue : Grinding Modeling and Energy
احصل على السعر
(PDF) Optimization and performance of grinding circuits: the
Buzwagi Gold Mine (BGM) process plant was designed such that, after secondary grinding, gold and copper are recovered by flotation. However, the flotation circuit had been inefficient, and as aDownload : Download full-size image John B. Mosher presently directs the Metallurgy Department at PT Freeport Indonesia. He has extensive experience in the comminution and beneficiation of copper, gold, and lateritic nickel ores. He has worked on crushing and grinding circuits in an operational or consulting role in six continents, with a Comminution circuits for gold ore processing ScienceDirect
احصل على السعر
GOLD Indian Minerals Yearbook 2020 IBM
gold mine since 2010. At the Hutti Mineral Treatment Plant, the r.o.m. of -8" size is crushed. The final product from crushing plant, i.e. -10 mm size is stored in a 1,500 tonnes capacity fine ore bin for subsequent treatment, i.e., grinding. The Milling/Grinding process of gold ore employs two distinct grinding techniques.Refractory gold ores may be defined as those which yield low recoveries of gold when treated by the conventional grinding and cyanidation process. This refractory behaviour can vary from mild to severe with gold recoveries of 85% down to less than 30% [1]. A common cause of refractoriness is encapsulation of fine gold within the matrix ofUltra fine milling for the recovery of refractory gold
احصل على السعر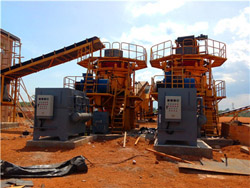
Effect of ore heterogeneity on the ball mill wear rate
The findings could be applied in feasibility studies to calculate and evaluate grinding costs versus grinding efficiency. Keywords: Saudi gold mine, gold rock hardness, mechanical properties, petrographic descriptions, wear rate, ball mill 1. Introduction Mineral processing and mining industry is a significant part of the economy worldwide.The grinding process adopts two closed circuit grinding processes, so that the grain size of the gold mine reaches-0.074mm for 85%. One section of the mill operation uses a grid type ball mill. The second section grinding machine uses the overflow type ball mill, and the grinding&classifying system is formed in the spiral classifier machine toA Hard-to-Separation Gold Beneficiation Process and Xinhai Mining
احصل على السعر
Energy Use of Fine Grinding in Mineral Processing SpringerLink
Fine grinding, to P80 sizes as low as 7 μm, is becoming increasingly important as mines treat ores with smaller liberation sizes. This grinding is typically done using stirred mills such as the Isamill or Stirred Media Detritor. While fine grinding consumes less energy than primary grinding, it can still account for a substantial part of a mill’s the leading gold-producing nation for the first time. They were followed by Australia, the United States and South Africa; with Canada in seventh place. Gold production in South Africa has halved since the 1960s owing to declining ore grades and rapidly increasing costs (Goldsheet Mining Directory). Cyanidation is the process that accounts forHighlights of the Past Five Decades of Gold Ore
احصل على السعر
Energy efficiency • Energy intensity in copper and gold mining
The greatest energy input in copper and gold production is required for the comminution and grinding processes. The energy audit of mainly Australian copper and gold mines shows that 36 % of the overall energy consumption is attributable to comminution [1]. Previous studies had shown values between 18 % and 50 %.Definition:Gold extraction refers to the process of separating gold from gold-bearing ore. The content of gold in nature is low. In order to extract gold, it is usually necessary to first crush and grind the gold ore and use the extraction method to separate gold from the ore. For different gold-bearing ores, the selection of gold extractionSummary of Gold Extraction Process cnlitereagent
احصل على السعر
Why gold mines are adopting HPGRs to increase production
How HPGR improves gold recovery. There are two main ways mines recover gold ore from the gangue, and HPGRs can assist with each process. One of them is heap leaching and for mines using this process, we’ve found that the most efficient setup is to have a HPGR perform tertiary grinding immediately prior to recovery, completely avoiding the use of a The gold mining process is complex and goes beyond what most people imagine — miners in hard hats working underground or operating large, noisy mining equipment are images that often come to mind. However, the actual mining of gold ore is only one step in a complex gold mining process. Before miners can extract gold ore from Gold Mining Process
احصل على السعر
The Mining Process OceanaGold
The Mining Process. Gold at Macraes is known as ‘refractory ore’, which means it is ultra-fine and resistant to the typical cyanide leach process. The mining process at Macraes is circular and follows a cycle of exploration, mining, processing and rehabilitation and closure. With a 30-year history of development spanning fluctuating goldFor the purpose of this paper, gold mining residues with a particle size of approximately 70–80% finer than 74 μm are defined as slime and residues grading 10–20% finer than 74 μm as sand. The first phase of the re-treatment process is to obtain credible information with the sampling programme (and the subsequent metallurgical testwork) aA practical guide to re-treatment of gold processing residues
احصل على السعر
Summary of Gold Plants and Processes ScienceDirect
Gold recoveries 76–80% depending on carbon content of ore. Isamill ultra-fine grind to 20 μm installed in 2005. Diesel fuel added as masking agent to SAG and regrind mills49: Fosterville: Australia: Preg-robbing concentrate: Bacterial leaching: Heated leach process added after CIL to increase gold recovery: 49: Carlin: Nevada, United StatesThe mining process would utilize equipment and methods similar to the quarry 2.8 miles to the south of the CK Gold Project site. The target ore is hosted in granite and to extract the minerals, the granite must be removed for processing. Non-ore bearing rock will be removed leaving slopes and benches on the mine pit walls in a stable conditionMining Process — CK Gold Project Wyoming
احصل على السعر