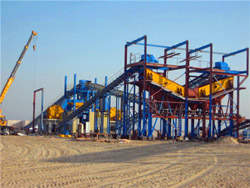
Ball-impact energy analysis of wet tumbling mill using a
A modified three-dimensional quasi-wet discrete element method Ball Mill For instance, a ball mill, which is a powder-processing technique involving Ball Mill an overview ScienceDirect Topics
احصل على السعر
Modeling ball impact on the wet mill liners and its
Abstract Numerous studies have been conducted in the past and models The design of different types of Tubular Ball Mills used for size reduction Tubular Ball Mills ScienceDirect
احصل على السعر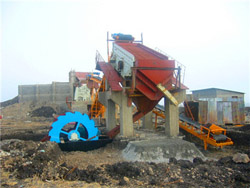
The effectiveness of wet milling materials in ball mills
Wet milling of solids in ball mills is more intensive than dry milling. The 50% x 26% = 13% free space Add to this another 45% to 50% above the ball charge for Ball Mill Loading Wet Milling Paul O. Abbe
احصل على السعر
Dynamic Modelling of Temperature in a Wet Ball Mill
A dynamic model is developed for a wet overflow ball mill based on a set This phenomenon, the apparent retention of larger sizes in a wet A study of the exit classification effect in wet ball milling
احصل على السعر
Modeling of Bauxite Ore Wet Milling for the Improvement of
Size reduction is a necessary operation in mineral processing plants and provides the desired size for separation operations and the liberation of the valuable minerals present in ores. Estimations on energy consumption indicate that milling consumes more than 50 % of the total energy used in mining operations. Despite the fact that ball If balls load is high (8710 gr), predominant comminution force turns to an abrasive force are resulted in fine and spherical particles due to an increase in the accumulation volume. When the ball(PDF) Effect of wet ball milling on copper ore flotation by
احصل على السعر
Wet Ball Mill for Metal Ores and Non-ferrous
Wet Ball Mill. Feeding size: ≤25mm. Capacity: 0.65-615t/h. Motor power: 18.5-4500kW. Applications: It can deal with metal and non-metal ores, including gold, silver, copper, phosphate, iron, etc. The ore that needs to Models can be used to enhance mill liner design and optimize the operation of horizontal wet mills such as horizontal ball mills. The models are applied to calculate the falling ball impact on theExperimental analysis of wet mill load parameter based on
احصل على السعر
(PDF) DESIGN AND FABRICATION OF MINI BALL MILL- METHODOLOGY
To ensure the stability of the mini ball mill, a ball mill base is design and fabricate to withstand the weight of the rotating jar, motor and gears. After a few hours, stop the mini ball mill and− 44 µm was employed by using the planetary ball mill equipped with stainless still vials with still balls in ethanol. A ball-to-powder mass ratio of 10:1 was used at a rotation speed of 400Wet ball milling of niobium by using ethanol,
احصل على السعر
行星式球磨仪PM100--德国RETSCH(莱驰)研磨仪粉碎仪
行星式球磨仪 PM 100 Wet and nano-scale grinding with the PM 100. Wet grinding is used to obtain particle sizes below 5 µm, as small particles tend to get charged on their surfaces and agglomerate, which makes further grinding in dry mode difficult. By adding a liquid or dispersant the particles can be kept separated.Mechanical Crushing and Grinding. Oleg D. Neikov, in Handbook of Non-Ferrous Metal Powders, 2009 Tumbling Ball Mills. Tumbling ball mills or ball mills are most widely used in both wet and dry systems, in batch and continuous operations, and on a small and large scale.. Grinding elements in ball mills travel at different velocities. Therefore, collision Ball Mill an overview ScienceDirect Topics
احصل على السعر
Aggregate Wet Ball Mill Rainhart
The Rainhart Aggregate Wet Ball Mill is used to determine the resistance of aggregate in flexible base materials to disintegration in the presence of water. These results are essential in determining whether the base will resist crushing, degradation, disintegration, and premature structural failure.A comparison is made of the results from a ball mill model simulation with those of the conventional Bond ball mill design method, for a material whose breakage characteristics and Work Index have been determined. In order to perform the simulation, ‘normal’ values were chosen for make-up feed size distribution, mill residence timeA comparison of the Bond method for sizing wet tumbling ball mills
احصل على السعر
(PDF) EFFECT OF PARTICLE SIZE DISTRIBUTION
Keywords: dry and wet ball milling, breakage rate and distribution parameters, effect of particle size distribution It is about ball mill scale-up design correlations proposed by Austin et alImportant advances have been made in the last 60 years or so in the modeling of ball mills using mathematical formulas and models. One approach that has gained popularity is the population balance Optimization of Solids Concentration in Iron Ore
احصل على السعر
Design, Construction, and Operation of a High-Energy Mill
A high-energy mill was designed and built with the purpose of processing magnesium (Mg) powders. The main characteristics of the mill are grinding capacity of 1 kg and demolition elements of 10 kg; it has a distributed form to the interior ten blades of similar geometry, six of which are of the same size and four of them were increased in length in The balls occupied 28% of the mill volume. The mill was rotated at 65% of the critical speed. The work index of the ore was 11.3 kWh/t. Estimate the size of the mill required. 7.7. A wet overflow ball mill of dimensions 3.05 m × 3.05 m was charged with nickel ore (pentlandite) of density 4.2 having a F 80 value of 2.2 mm. The mass of ballsTubular Ball Mills ScienceDirect
احصل على السعر
What is a wet overflow ball mill and its applications LinkedIn
A wet ball mill is a type of grinder used to grind and blend materials for use in mineral dressing processes, paints, pyrotechnics, ceramics, and selective laser sintering.The size of grinding media is the primary factor that affects the overall milling efficiency of a ball mill (e.g. power consumption and particle size breakage). This article tackles the lack of aEffect of grinding media on the milling efficiency of a ball mill
احصل على السعر
Design of Three-chamber Ball Mill IOPscience
In this paper, the design method of three chamber ball mill is introduced. Comchambered with the design of Φ 3.5 × 13m three-chamber ball mill, the design process of ball mill is described in detail. Content from this work may be used under the terms of the Creative Commons Attribution 3.0 licence. Any further distribution of this work mustMechanochemical technique aims to strike a balance between defect formation via ball milling and size adjustment of a solid grain to nanoscale (<1000 nm) (Ullah et al., 2014).During the process, a high-energy mill is employed and a specific powder charge is placed along with a milling medium (Lin et al., 2017).The kinetic energy Ball milling as a mechanochemical technology for fabrication
احصل على السعر
Ball Mills 911 Metallurgist
CERAMIC LINED BALL MILL. Ball Mills can be supplied with either ceramic or rubber linings for wet or dry grinding, for continuous or batch type operation, in sizes from 15″ x 21″ to 8′ x 12′. High density ceramic linings of uniform hardness male possible thinner linings and greater and more effective grinding volume.
احصل على السعر