
刨(planing)、铣(milling)、磨(grinding)等加工一金属平面
13 个回答 默认排序 颓废男孩 以为自己是未来的独立产品设计师 关注 看了好多回答,都说到了粗加工, 精加工 ;但是大家忘了还有一个荒加工用于对付铸铁床架的,这个一般都是刨床干,即便现在超大 直线件 的部分加工还是要依赖 龙门刨 吧。 我始终觉 应用于工件的切割(Cutting)、精磨(Grinding)、研磨(Lapping)和抛光(Polishing)它们只是一种精密机械,半导体加工设备,分单面和双面磨削加工中grinding, lapping, polishing 有什么区别?_百度知道
احصل على السعر
Key issues and challenges in spice grinding ScienceDirect
Several techniques and methods are being applied in the spice grinding process like conventional grinding (hammer, plate, pin mill), superfine grinding (ball, jet, The fine grinding mills are classified often into five major groups (i) impact mills, (ii) ball media mills, (iii) air jet mills, (iv) roller mills, and (v) shearing attrition mills Chapter 10 Selection of Fine Grinding Mills ScienceDirect
احصل على السعر
Steady-state and dynamic simulation of a grinding mill using grind
A semi-autogenous grinding mill is simulated with gradient and non-gradient based extremum seeking controllers to maximize the mill performance using Introduction The operation of any mill has a distinct signature which is a combination of the mill type and operating conditions, and of the ore properties Extended grinding curves are essential to the comparison of milling
احصل على السعر
PARAMETER OPTIMIZATION OF LARGE SAG MILL LINER
The working performance indicators of the SAG mill mainly include grinding efficiency, grinding effect, crushing energy consumption and wear of the liner A semi-autogenous grinding mill is simulated with gradient and non-gradient based extremum seeking controllers to maximize the mill performance using grind Applying grindcurves to mill operation and optimisation
احصل على السعر
Choosing the right strategy: cryogrinding vs. ball milling comparing
The grinding was performed in a dry state using a cryogenic grinder 6970EFM Freezer/Mill® (6970 EFM, SPEX SamplePrep, Metuchen, NJ, USA) which , G. Lorenz Add to Mendeley https://doi/10.1016/S0007-8506 (07)61285-2 Get rights and content This paper presents ‘acceptable grinder criteria’ for An Analytical Study of Three Point Grinding Methods for
احصل على السعر
MILLING METHODS COMPARISON GUIDE
points. Cryo-milling also prevents overheating of the mill itself, which can be a risk with very hard materials. Cryo-milling can apply to mechanical milling, media milling, and jet milling. CRYO-MILLING MEDIA MILLING Media milling refers to a process in which grinding media — such as balls or beads made of steel, glass, ceramic, or plasticby the mill and product-related stress models in the given grinding process. According to the product-dependent stress model, the product quality and grinding fineness can be determined by two facts: the number of stress cases and the stress intensity. An important aspect in the ultrafine grinding of the materials is the attainable finalEnergy-Model and Life Cycle-Model for Grinding
احصل على السعر
Machining Processes: Turning, Milling, and Drilling
Milling Process. Milling operations involve using multi-point rotary cutters to remove material from a workpiece. There are two main types of milling operations: face milling and peripheral milling. Face milling cuts flat Cryogenic (C2) 7.06 2 Cause Energy requirement − 1.85 6 Effect. Dry ice (C3) 3.89 Cause Grinding time − 0.21 Effect. Chilling (C4) 3.47 Cause Grinding loss − 0.25 Effect. Grinding zone(PDF) Key issues and challenges in spice grinding
احصل على السعر
Tool path generation of ultra-precision diamond turning: A
In the calculation of tool path, milling cutters are regarded as ideal surfaces of revolution, and examples include spherical cutters, torus cutters, and even generalized cutters with a freeform generatrix curve. 10 The abovementioned ultra-precision grinding and fly-cutting belong to this kind of processing according to the kinematics1. Introduction. Since grinding mills have a significant impact on the final economic performance of a mineral processing plant (McIvor and Finch, 1991, Sosa-Blanco et al., 2000), it is important to operate them at the point which will optimize the economic performance of the plant (Cramer, 2008, Matthews and Craig, 2013).Grinding mill Steady-state and dynamic simulation of a grinding mill using grind
احصل على السعر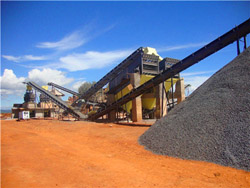
(PDF) Energy-Model and Life Cycle-Model for Grinding
Weronika Kruszelnicka. Fine and ultrafine grinding processes require energy inputs, which significantly affect the energy and the environmental balance in the life cycle of grinded products. ThisSAG MILLING CIRCUIT OVERVIEW Amongst the problems that face SAG milling operations are ore feed inconsistency, energy inefficiency, instability of operating point, and particle size of grind output. Increasing economic pressure to raise throughput only serves to aggravate these existing problem areas.Performance Audit of a Semi-autogenous Grinding Mill Circuit
احصل على السعر
Comparison of Wet and Dry Grinding in Electromagnetic Mill
Comparison of dry and wet grinding process in an electromagnetic mill is presented in this paper. The research was conducted in a batch copper ore grinding. Batch mode allows for precise parametrization and constant repetitive conditions of the experiments. The following key aspects were tested: processing time, feed size, size of The following bauxite grinding circuits are the main circuits employed in the alumina industry today. Rod/Ball Mill—Open Circuit. This is probably the most common grinding mill type and has been used for over 40 years. It is often the base case considered for bauxite grinding. The mill is operated in open circuit and comprises two compartments.Physical Bauxite Processing: Crushing and Grinding of Bauxite
احصل على السعر
Extended grinding curves are essential to the comparison of milling
The grinding curve is the product size as a function of feedrate, for a fixed feed size. It is proposed that for each new milling condition, in this case a change in the percentage of ball scats in a mill, the peak in the grinding curve must be sought, and that must be used as the comparative test condition. The single-point screenings were.The idea is based on the assumption that the maximum throughput of a grinding mill is achieved at maximum power consumption [26]. Therefore, the throughput is maximized with a peak-seeking optimizer to manipulate the mill load filling up to the point where the grinding mill operates at maximum power consumption.Extremum seeking control for optimization of an open-loop grinding mill
احصل على السعر
The Evolution of Grinding Mill Power Models SpringerLink
Mill power models have been used in a variety of ways in industrial practice since power directly equates to throughput and fineness of ground product. We first start with Hogg-Fuerstenau Power Model and show how this model successfully predicted the power draw of many grinding mills in several mining operations. Then, we show how Different milling conditions, such as wet or dry, and use of different grinding media have a great impact on the flotation performance of sulphide minerals. In the present study, the effects of wet and dry grinding and the use of different grinding media, such as mild steel (MS) and stainless steel (SS), were investigated on a Cu-sulphide ore. Effects of Different Grinding Media and Milling Conditions
احصل على السعر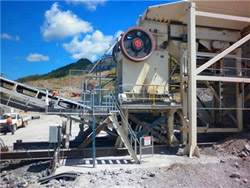
Wet Milling: The Basis for Corn Biorefineries ScienceDirect
Corn wet mills are relatively energy-, water-, and capital-intensive compared with other food processing industries. Each mill uses large amounts of water (1.5–1.78 L/kg or 10–12 gal/bu) in fractionating corn, which must be evaporated at considerable energy cost.Typical capital investments of $0.23–0.35/kg or 6–9/bu. of annual grinding capacity Figure 3 shows the schematic diagram of one of the axial flow-type impact mills called a Super Micron Mill E. This mill has a larger processing volume and operated at a middle-range speed but is capable of the finer grinding by the attrition mechanism and separation nozzle to discharge foreign materials, which often cause the reduction in the Chapter 10 Selection of Fine Grinding Mills ScienceDirect
احصل على السعر
Ball milling as an important pretreatment technique in
Zhang et al. used two ratios of grinding ball to biomass weight (20:1 and 8:1) to pretreat corncob using ball milling. The sample milled with grinding ball to biomass weight ratio of 8:1 was better amorphized in comparison to the other one, which signifies the improvement of corncob digestibility in subsequent processes . On the contrary, YuanMicro-grinding is a tool based mechanical micromachining process which is mostly applied to create and finish 3D micro-features on hard and brittle materials such as glass, silicon, alumina, etc. Miniature-sized abrasive tool comes in physical contact with the workpiece and removes the unwanted material with mostly nanometric undeformed chip A comprehensive review of micro-grinding: emphasis on
احصل على السعر
Energy efficiency of state-of-the-art grinding processes
Specific energy consumption was determined as a function of material removal rate and compared to results of milling and turning processes. The key influence factors on grinding energy efficiency and productivity are depicted. Strategies are evaluated to optimize the overall process performance from an energetic point of view.1. Introduction. Wet ball mill is one of the most predominantly used method for the purpose of mixing and grinding of raw materials in laboratories and industry [1], [2], [3].The ball mill process is very complicated process governed by many parameters, such as ball size, ball shape, ball filling, slurry loading (with respect to ball amount), powder Effect of ball size and powder loading on the milling efficiency
احصل على السعر