
Sources of underground CO: Crushing and ambient
As a harmful gas in underground coal mine, CO seriously threatened the safety of miners. Currently, the spontaneous combustion of residual coal in goaf is 1. Sizing the plant. Real estate in an underground mine is not cheap, so the design of primary crushing plants faces more limitations underground than on the Six ways to take primary crushing underground Australian Mining
احصل على السعر
Mobile crushing solutions are making their way
Mobile crushing solutions are becoming increasingly popular in underground mining applications. Read this article where TON Outotec expert Julius Makela sat down with Mining Magazine to talk China has committed to peak its carbon emissions by 2030, which puts forward a new issue for underground metal mines—selecting a cleaner mining method which requires less energy Uncovering Cleaner Method for Underground
احصل على السعر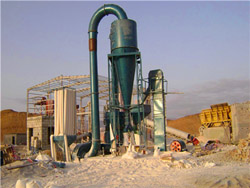
Energy Consumption in Mining Comminution ScienceDirect
In addition, HVAC energy requirements can be at least 25% of underground mine energy needs [10]. Mining energy consumption contributes to mining operational In order to realize accurate risk assessment and collaborative control of multi-hazard risk in non-coal underground mines, a space-oriented risk characterization Multi-hazard risk characterization and collaborative control
احصل على السعر
Reduction of Fragment Size from Mining to Mineral
The worldwide mining industry consumes a vast amount of energy in reduction of fragment size from mining to mineral processing with an extremely low Milev et al . [ 64] attempted to model failure mechanisms of specific seismic events in an instrumented platinum crush pillar. Three generic event types were hypothesized: shear failure in the footwall, Complexities of underground mining seismic
احصل على السعر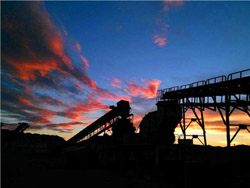
Airborne respirable dust in fully mechanised underground
The crushing and screening units are the distinct sources of dust in underground mines, because their operation involve abrasion, impaction, and dropping from heights. The quantity of dust generation depends on the operating factors, such as feed size and moisture content of rock, throughput rate, size reduction ratio, crusher type, and finesSurface and underground SSG mines show approximately the same incident rate of 2.5 per 10,000; however, surface SSG mines employ nearly 30 times more workers than underground mines The initial noise study at this mine focused on the primary crushing area, primary conveyor system, and the secondary crusher/processing Area Noise Assessment at Surface Stone, Sand, and Gravel Mines
احصل على السعر
A Guide on Mining Equipment Used in the Mining
Specialised underground mining equipment such as diggers, loaders, and trucks are used to excavate raw materials and transferred to the surface with lifts for future processing. In order to placePrimary crushing as a unit operation serves mining operations to maximize load and haul equipment utilization and milling operations as a comminution step. Many mines select primary crushers based on top size of the designed or anticipated ROM ore. This can result in a substantial excess of primary-crushing capacity for smaller operations.Comminution Circuits for Gold Ore Processing ScienceDirect
احصل على السعر
Mining with crush pillars SciELO
The practice underground is to mine the pillar holings in an updip direction. The panel siding lag was kept at the 4 m standard. Furthermore, a lagging siding or delayed pillar holings will impact on the size of the pillar formed at the mining face. Early pillar crushing is therefore not achieved and this can result in unpredictable pillarInnovation has an important role in improving the productivity, safety and sustainability of mining operations. Historically, ore transport was done by diesel trucks, but with the commitment to reduce CO2 emissions and increase mine safety, mining companies have invested in innovative, more sustainable ore transport technologies. The innovative Minerals Free Full-Text A Mine-to-Crusher Model to
احصل على السعر
Mining Industry: A Complete Guide Flyability
Mineral extraction: the process of using surface mining or underground mining techniques. Mineral handling: the process of sorting raw materials from waste materials, called tailings. Mineral processing: the process of crushing, grinding, smelting, or refining minerals into a final product for distribution.In-pit crushing and conveying (IPCC) systems (whether fixed, mobile, or semi-mobile) are an alternative to the traditional truck/shovel approach to materials handling, offering potential cost savings. Underground mining is a highly competitive industry that is often singularly focused on material production as a key performance indicatorComparison of fixed and mobile in-pit crushing and
احصل على السعر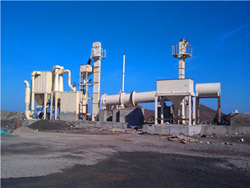
Energy Consumption in Mining Comminution ScienceDirect
In addition, HVAC energy requirements can be at least 25% of underground mine energy needs [10]. Mining energy consumption contributes to mining operational costs and occurs at all stages of the ore recovery process: blasting, excavation, crushing, transport and grinding (comminution).In the United States, some scholars attributed the causes of CO in underground mines to the underground DPM Dispersion (Yi et al., 2011). In 1994, Czechoslovakian scholar BTaraba (Taraba and Pavelek, 2014, Taraba, 1994) thought that coal crushing would generate CO, but he made no further research.Sources of underground CO: Crushing and ambient
احصل على السعر
Effects of rock dusting in preventing and reducing intensity of
Watering, water flushing, water mist spray and water barriers (Fig. 2) have been extensively used to prevent and reduce intensity of coal mine explosions in China.Coal mines in the eastern China, especially for the coal fields such as Zhaozhuang, Yanzhou, Huainan, Huaibei, etc., often apply the methods of watering and water flushing to clear An early underground mine shaft of 20 meters deep and only 38 centimeters wide were also found. The shafts contained charcoal fragments dating the activities to 1000 1200 years ago. Today the mine has secondary crushing facilities, concentrators and a refinery on site. In 1982 a series of cavities with well-crystallised minerals were25.1 Exploration: Finding minerals Mining of mineral
احصل على السعر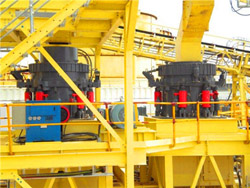
Crush pillar support designing for controlled
Introduction. Safe mining practices are aimed at maximizing the extraction of a particular orebody. Mine stability is a key consideration and the type of layout (i.e. pillar type and spans) must be suitable for the prevailing rock mining blasts, especially in underground mining. This kind of explosive leakage depends on a number of f actors such as water content in the rock m ass, in-situ stresses, stemming, and charging(PDF) Rock mechanics related to mining engineering
احصل على السعر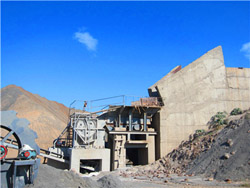
Crushers QueensMineDesignWiki
Figure 1 : Crusher Location in an Underground Mine (ugdsb.on.ca) Material Handling. The material handling portion of crushing is the means by which the ore travels from the grizzly all the way to the skip in an underground mining operation. This can easily be broken down in to three sections, pre-crushing, crushing, and post crushing.Abstract and Figures. Among different types of hazards associated with underground mining in Polish copper mines, one of the most dangerous is rock burst hazard. Having in mind that the depth of(PDF) Blasting Operations Using Different Initiation Methods
احصل على السعر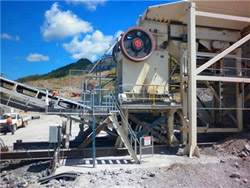
Modeling Rock Fracture Propagation and Water Inrush
Water inrush in underground mines is a major safety threat for mining personnel, and it can also cause major damage to mining equipment and result in severe production losses. Water inrush can be attributed to the coalescence of rock fractures and the formation of water channel in rock mass due to the interaction of fractures, hydraulic A new method using a deep neural network (DNN) model is proposed to predict the ore production and crusher utilization of a truck haulage system in an underground mine. An underground limestone mine was selected as the study area, and the DNN model input/output nodes were designed to reflect the truck haulage system characteristics. Big Applied Sciences Free Full-Text Deep Neural Network for
احصل على السعر
Special Issue "Backfilling Materials for Underground Mining"
Special Issue Information. Backfilling of mined-out areas is a fundamental component of many underground mining operations. The backfill material provides support to the surrounding rock mass, reduces wasteful dilution, enables a safe working area for production activities and mitigates the risk of surface subsidence.The identification of the dust characteristics in coal mine working faces is essential for preventing coal dust explosion and occupational diseases. In this paper, dust samples from the coal mines in southern Shanxi province and Henan province, central North China, were selected as the research objects. The results show that the dust contains primarily Characteristics of Dust in Coal Mines in Central North China
احصل على السعر