
Wet and dry grinding of coal in a laboratory-scale ball mill:
Abstract. In this study, experimental data for wet- and dry-ground coal samples under wet and dry grinding are characterized by commonly used distribution functions. First, both the R-R and Swrebec functions have superior fitting performances Abstract. In this study, experimental data for wet- and dry-ground coal samples under wet and dry grinding are characterized by commonly used distribution Wet and dry grinding of coal in a laboratory-scale ball mill: Particle
احصل على السعر
(PDF) 43 Drying of Coal ResearchGate
43 Drying of Coal Authors: Jerzy Piko A. S. Mujumdar McGill University Abstract and Figures Drying of low-rank coal (LRC) is Differences in dry and wet grinding with a high solid concentration of coking coal using a laboratory conical ball mill: Breakage rate, morphological Differences in dry and wet grinding with a high solid
احصل على السعر
Dry Grinding Plants Mining Technology
Conventional liquid and gaseous fuels, a significant advantage for an optimum combined drying and grinding process; The delivery of turn-key Abstract and Figures. This study shows the performance of a currently running vertical roller coal mill (VRM) in an existing coal-fired power plant. In a power plant, the coal mill is the criticalAn investigation of performance characteristics
احصل على السعر
Wet and dry grinding of coal in a laboratory-scale ball mill: Particle
Abstract. In this study, experimental data for wet- and dry-ground coal samples under wet and dry grinding are characterized by commonly used distribution Indian coal washing plants face tremendous pressure in maintaining clean coal yield and handling the rejects. Conventional coal washing plants generate clean coal Sustainability of coal mines: Separation of clean coal from
احصل على السعر
Flotation of oxidized coal dry-ground with collector
The combustible matter recovery of oxidized coal dry-ground with collector is much higher than that of oxidized coal dry-ground directly only while the grinding time Made available by U.S. Department of Energy Office of Scientific and Technical InformationHigh efficiency dry-grinding plants for coal (Journal Article
احصل على السعر
Flotation of oxidized coal dry-ground with collector
In the flotation tests of oxidized coal dry-ground with collector, the pulp was first agitated in the flotation cell for 3 min, after which 2-octanol frother (1 kg/ton) was then added and the pulp was conditioned for an additional 1 min. The grinding process was conducted in a laboratory dry rod mill. The grinding time was 20 min, 40 min, 60Dry grinding is one of the most important issues for the chemical, mineral, cement industries, and solid-fuel-burning power plants. Energy requirement in these industries is very high in the comminution processes (especially in the grinding processes). Wet and dry grinding of coal in a laboratory-scale ball mill: Particle-size distributionsThe effects on the grinding parameters of chemical,
احصل على السعر
Operational parameters affecting the vertical roller mill
A cement Vertical Roller Mill modeling based on the number of breakages. Vertical roller mills (VRM) are widely used to grind, dry, and select powders from various materials in the cement, electric power, metallurgical, chemical, and nonmetallic ore industries. For the sectors above, the VRM is a powerful and energy-intensive grinding Beside all these the ability to crush, grind, classify and dry within a single unit, low wear rates, less floor space, etc. are other advantages of VRM system. In this study, pilot scale tests were performed with a mobile vertical-roller-mill grinding plant to investigate the relationships between operational parameters.Operational parameters affecting the vertical roller mill
احصل على السعر
Conventional and recent advances in gravity separation
The ratio between combustible organic matter and inorganic impurities of coal is also one of the variables in coal classification. Coal gangue is a significant residue of coal mining and cleaning, which accounts for approximately 10–15% of raw coal [3].The first group of impurities in coal, which are also the most commonly encountered, are quartz LOESCHE has more than 100 years of experience in the comminution of cement, raw material, clinker, coal, slag and minerals and its vertical roller mills form the core of many plants used for the dry-grinding process of these materials.Loesche Mining Technology
احصل على السعر
An investigation of performance characteristics and
The coal-grinding plant fully meets the expectations in terms of Dry separation technologies capable of efficient recovery of commodities are relatively rare and highly dependent on theTypical coal washing plants adopt dense media cyclone for coarse coal (−13 mm + 0.5 mm size) and froth flotation technique for the fine coal (−0.5 mm size) [3]. Deniz et al. [34] and Bu et al. [35] studied the effect of wet and dry grinding of coal and observed that the wet grinding method is a more efficient methodology for the fineSustainability of coal mines: Separation of clean coal from
احصل على السعر
LOESCHE-MILLS
1927 First Loesche coal mill delivered for the Klingenberg power station in Berlin. 1953 500th coal mill plant sold worldwide. 1961 Introduction of hydraulic spring assembly system. 1965 Construction of first pressure mill (LM 12.2 D). 1980 Delivery of first modular coal mill (LM 26.3 D). 1985 Delivery of first self-inerting coal grinding plant (LM Dry Grinding Plants. Product rates for cement raw material of 1,400t/h and mill drive ratings exceeding 10,000 kW are managed as flawlessly as 2t/h at 110kW. Naturally we also supply suitable associated machines for units to all mill sizes for example classifiers for finenesses less than 7,000 Blaine or d50 less than 5 μm, and hot-gasDry Grinding Plants Mining Technology
احصل على السعر
Mechanochemical stabilization of heavy metals in fly ash from coal
Fly ash from coal-fired power plants was treated by the dry milling and wet milling method. The technical feasibility of stabilizing typical heavy metals, including Pb, Cr, Cd, Ni, Cu, and Zn because of their severe toxicity and then enriching them to enriched in different degrees in fly ash during coal combustion (Zhang et al., 2002) was studied.Coal mill is the main equipment in the pulverized coal preparation process.Because calcining top-grade cement clinker requires a stable supply of coal powder as the fuel of cement kiln, and more than 85% of AGICO Cement Grinding Mill Cement Plant
احصل على السعر
Wet and dry grinding of coal in a laboratory-scale ball mill: Particle
Deniz et al. [34] and Bu et al. [35] studied the effect of wet and dry grinding of coal and observed that the wet grinding method is a more efficient methodology for the fine grinding of materialsThe flotation of oxidized coal can be well‐improved by dry-grinding, and the flotation of oxidized coal dry-ground with collector will also be discussed in this investigation. The grinding time is 0 min, 20 min, 40 min, 60 min and 80 min. The dodecane was used as the collector. The flotation tests were conducted in a 1.5 L XFD flotation cell.Flotation of oxidized coal dry-ground with collector
احصل على السعر
A comparative study on the effects of dry and wet grinding
Water scarcity dictates to limit the use of water in ore processing plants particularly in arid regions. Since wet grinding is the most common method for particle size reduction and mineral liberation, there is a lack of understanding about the effects of dry grinding on downstream separation processes such as flotation.Ring-Roll (Bowl-Mill) and Ball-Race Mills comprise most coal pulverizers currently in service at pulverized coal power plants. The grinding rolls are stationary in this design, while a worm gear drive rotates the ring (commonly known as the bowl). Powerful springs force the grinding rolls against the ring, providing the pressure required toCoal Pulverizer Power Plant Pall Corporation
احصل على السعر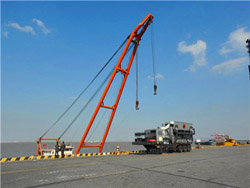
Tube mills for dry grinding. Polysius
grinding and drying of diverse materials, such as minerals, cement clinker, ores and coal. Having successfully designed and built grind-ing plants since1880, Polysius possesses the necessary comprehensive process and plant knowhow. Moreover, the company’s Research and Development Centre provides back-upIt is a mechanical device used to grind raw coal into pulverized coal powders. The most used coal mills in cement plants are air-swept ball mills and vertical roller mills. At present, most cement plants use coal as the main fuel in the clinker production process. The standard coal consumed by the new dry process for producing 1 ton of cementCoal Mill in Cement Plant Vertical Roller Mill & Air-Swept
احصل على السعر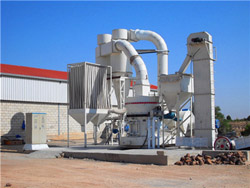
A comparative study on the effects of dry and wet grinding
Deniz et al. [34] and Bu et al. [35] studied the effect of wet and dry grinding of coal and observed that the wet grinding method is a more efficient methodology for the fine grinding of materials.
احصل على السعر