
An innovative approach for determining the grinding media
Herein, an innovative approach for determining the grinding media system of ball mill based on grinding kinetics and linear superposition principle was proposed. The optimal media ball size of −2 + 0.45 mm, −0.45 + 0.15 mm, and − 0.15 mm feeding Introduction Grinding operation is used extensively in the industry of beneficiation, metallurgy, chemical engineering, and electric power. Assisted by the An innovative approach for determining the grinding media system
احصل على السعر
Minerals Free Full-Text A Review of the Grinding Media in Ball
The performance of grinding media in a ball mill is measured in terms of wear rate, which is a function of the media composition, hardness, phase structure, and Herein, an innovative approach for determining the grinding media system of ball mill based on grinding kinetics and linear superposition principle was proposed.An innovative approach for determining the grinding media system
احصل على السعر
(PDF) Simulation for grinding balls production
In this present work, the grinding balls from high chromium white cast iron (ASTM A-532) were produced by using sand mold-gravity casting. The simulation casting process was conducted beforeMonitoring mill load is vital for the optimization and control of grinding process. This study proposed the use of an instrumented grinding media to assess solid Assessing load in ball mill using instrumented grinding media
احصل على السعر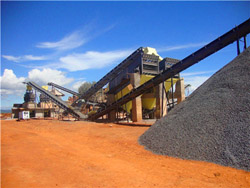
A Review of the Grinding Media in Ball Mills for Mineral
Although there are several types of grinding media, which include inert grinding media such as ceramic, zirconia, agate, and glass, this section is going to focus Balls for ball mills can be produced by die forging, rolling and casting methods. The rolling of balls can be realized as skew or cross rolling. This paper On some problems of producing grinding media by cross
احصل على السعر
Minerals Free Full-Text Changing the Pulp Properties and
The grinding process plays a crucial role in the floatability of mineral. The present study proposes a scheme to assist in the flotation separation of galena and pyrite A data set derived from 50 experiments on the wear rate of a low alloy steel ball was applied in this work. The experimental data were obtained from literature [].The experimental conditions, influential factors and the total wear rate for each experiment, which was determined by the grinding media weight loss, are implied in Table 1.To measure Modeling and prediction of wear rate of grinding media in
احصل على السعر
Effect of Grinding Media Size on Ferronickel Slag
The aim of this study is to evaluate the effect that the size of grinding media exerts on ferronickel slag milling efficiency and energy savings. A series of tests were performed in a laboratory ball mill using The gating system was designed for six grinding balls with 50 mm diameter for each grinding ball, as shown in Figure 3. The dimension of gating system design was obtained by input some parameters in(PDF) Simulation for grinding balls production
احصل على السعر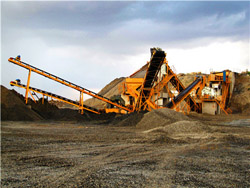
Open Access proceedings Journal of Physics: Conference
The gating system was designed for six grinding balls with 50 mm diameter for each grinding ball, as shown in Figure 3. The dimension of gating system design was obtained by input some parameters inTower Mills: 0.5”-1.5” grinding balls are recommended. The normal top size of media used is 10-25mm, but even smaller grinding balls can be used for very fine grinding. Isa Mills: <0.1” grinding balls are recommended. The Isa Mill is more efficient when using small media (i.e. high-chrome steel balls).Grinding Balls and Other Grinding Media: Key consumables
احصل على السعر
Grinding in Ball Mills: Modeling and Process Control Sciendo
Grinding in Ball Mills: Modeling and Process Control. Vladimir Monov, Blagoy Sokolov and. Stefan Stoenchev. Published Online: 16 Mar 2013. Volume & Issue: Volume 12 (2012) Issue 2 (June 2012) Page range: 51 68.Grinding iron ores in conventional ball mills involve a considerably high consumption of metallic media, resulting in high operating costs. In the case of compact itabirites, the high silica content increases such consumption, potentially exceeding the costs associated with electric power consumption in industrial operations. This paper presents Study on Partial Replacement of Metal Grinding Ball with
احصل على السعر
Stirred media mills in the mining industry: Material
Ball mills have traditionally been used for fine grinding of minerals, and in these cases smaller ball sizes than in conventional grinding are used to increase contact area and decrease collision intensity [15], and lower mill speeds are used to cause the media to cascade rather than cataract, shifting the typical forces experienced from impactThe company’s current gating system for grinding balls was redesigned and optimized from a number of concepts based on gating systems and casting technologies. The major improvements were; incorporating a conical pouring chamber to avoid molten metal splashes, overflow bores to signal mould cavity fill-up, tapered Optimization of the casting technology and sustainable
احصل على السعر
Effect of Grinding Media Size on Ferronickel Slag Ball Milling
The aim of this study is to evaluate the effect that the size of grinding media exerts on ferronickel slag milling efficiency and energy savings. A series of tests were performed in a laboratory ball mill using (i) three loads of single size media, i.e., 40, 25.4, and 12.7 mm and (ii) a mixed load of balls with varying sizes. In order to simulate the In ball mill operations, it is always helpful to optimise the grinding media system to min- imize the costs of the operation. In a research done by Yu et al. [16] to optimize grinding media systemGrinding Media in Ball Mills-A Review ResearchGate
احصل على السعر
The kinetics and efficiency of batch ball grinding with
Grinding balls were selected as shown in Table 1 for these reasons: firstly, it was observed that only balls smaller than 40 mm may show significant effects of media on grinding kinetics in small laboratory mills (20 cm diameters or smaller) [10]; secondly, to mimic the charge motion in industrial mill, the ratio of mill cylinder’s diameter to maximum In this test series, three loads with the same mass of single size grinding media (balls), i.e., 40, 25.4, and 12.7 mm diameter were used, while an additional test using a load of.(PDF) Effect of Grinding Media Size on Ferronickel Slag Ball
احصل على السعر
Using advanced mineral characterisation techniques to estimate grinding
An innovative approach for determining the grinding media system of ball mill based on grinding kinetics and linear superposition principle. 2021, Powder Technology. Citation Excerpt : Grinding operation is used extensively in the industry of beneficiation, metallurgy, chemical engineering, and electric power. Assisted by the impact andThe aim of this study is to evaluate the effect that the size of grinding media exerts on ferronickel slag milling efficiency and energy savings. A series of tests were performed in a laboratory ball mill using (i) three loads of single size media, i.e., 40, 25.4, and 12.7 mm and (ii) a mixed load of balls with varying sizes. In order to simulate the Effect of Grinding Media Size on Ferronickel Slag Ball Milling
احصل على السعر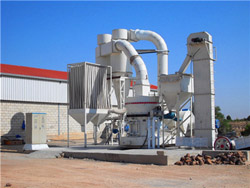
getting system for grinding media balls
Apr 29, 1999 and Uitrafine Grinding in a Stirred Ball Mill," Proc. Powder 8. . after to get weight loss — Q-50: shaft, arms, tank, grinding media; sand mill: WhatsApp Increasing Capacity of Existing Limestone Grinding Systems WhileA ball mill is a type of grinder widely utilized in the process of mechanochemical catalytic degradation. It consists of one or more rotating cylinders partially filled with grinding balls (made(PDF) Grinding in Ball Mills: Modeling and Process Control
احصل على السعر
Stirred media mills in the mining industry: Material
In ball mills, grinding performance can be increased by using media with different sizes and choosing the appropriate grinding media size distribution. It is thought that a similar approach can beThe maximum average temperature of grinding media up to 295.057 K appears at the grinding media filling 25% and the number of lifters 12. Subsequently, validation experiments are carried out to(PDF) DEM Investigation of Discrete Heat Transfer Behavior
احصل على السعر
Grinding Media STR Industries
Many facets of grinding media can be customized, such as: STR Industries is a professional ball manufacturer and we have been manufacturing media for 30 years. We are TS 16949 (auto industry standard, higher than ISO 9001) certified. Our 200,000 square foot facilities produce more than 400 metric tons of balls per month.
احصل على السعر