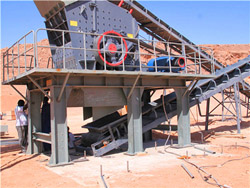
Grinding Kinetics Adjustment of Copper Ore Grinding in an
Wołosiewicz-Głąb M, Pięta P, Foszcz D, Ogonowski S, Niedoba T. Grinding Kinetics Adjustment of Copper Ore Grinding in an Innovative Electromagnetic Mill. Applied Sciences. 2018; 8(8):1322. https://doi/10.3390/app8081322 Chicago/Turabian StyleThe discussion on the concept of dry and wet copper ore grinding in an electromagnetic mill (EMM) also focuses on the efficiency-related advantages of the former from the perspective of both(PDF) Grinding Kinetics Adjustment of Copper Ore
احصل على السعر
Current Status of Copper-Ore Processing: A Review
tion-hydrometallurgical processing of mixed copper ore at the Udokan deposit is considered. The conclu-sions reveal the current trends in the processing of Principal forms in which copper ores are found include native copper, porphyry copper, massive deposits, and mixed ores. Native copper is simply the metal found unadulterated in nature. Occasionally copper is still Copper processing Ores, Refining, Smelting
احصل على السعر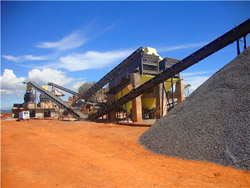
Predicting the effect of operating and design variables in grinding
Simulations of a batch grinding test for copper ore for a feed of 1.18-1.00 mm. Stirrer speed at 3.0 m/s, slurry at 50% solids (in weight) and ball size of 20 mm. This paper presents results of copper ore grinding tests and investigates the differences between dry and wet grinding technique using EMM. The tests were carried out using the same EMM device, the Comparison of Wet and Dry Grinding in
احصل على السعر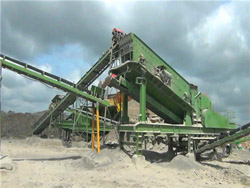
Copper ore grinding in a mobile vertical roller mill pilot plant
Within the scope of this study, the performance of VRM was compared with rod-ball mill circuit for copper ore grinding application. The VRM tests were The results indicated that the grinding process affects significantly the flotation metallurgical performance of Salobo’s ore. The conditions that yielded the The effect of grinding conditions on the flotation of a sulphide copper ore
احصل على السعر
Mechanochemical sulfidization of a mixed oxide-sulphide copper ore
Mechanochemical sulfidization by co-grinding with sulfur was developed for treatment of a sulphide-oxide copper ore. •. A 0.5 wt.% sulfur led to the higher floatability Mechanochemical sulfidization of a mixed sulfide/oxide copper ore by co-grinding with sulfur and additives including Mg(NO 3) 2 and Fe(NO 3) 3 salts and iron, aluminum and magnesium powders was investigated for the first time. Also, the influence of sulfidization during the wet-milling process was examined on the separation efficiency Mechanochemical sulfidization of a mixed oxide-sulphide copper ore
احصل على السعر
Copper Flotation 911 Metallurgist
A Copper Flotation Flowsheet. Because the copper in this type of ore usually assays only plus or minus 1% copper, the porphyry copper operations must be relatively large in order to be commercial. Abstract An analysis of flowsheets for processing sulfide and oxide copper ores, reagent modes, processing equipment, and flotation indicators in some domestic and foreign processing plants and productions is carried out. Autogenous and semiautogenous mills are commonly used in the primary grinding stage in ore processing plants, which Current Status of Copper-Ore Processing: A Review Springer
احصل على السعر
Grinding Kinetics Adjustment of Copper Ore Grinding in an
However, by grinding copper ore for 30 s, a product characterized by a fraction of 0–0.02 mm in an amount of more than 77% was obtained. Table 3 presents the energy consumption problem with respect to grinding time. It can be seen that the specific energy changes with a longer processing time.For Tongkeng ore, the optimized grinding conditions are grinding time 5.4 min, grinding concentration 67% and filling ratio 35%. For Gaofeng ore, the optimized grinding conditions are grinding time 3.8 min, grinding concentration 73% and filling ratio 34%. Such figures would represent yearly additions of 8.3 kt in copper and 250 kg in Special Issue "Grinding Modeling and Energy Efficiency in Ore
احصل على السعر
Mechanochemical Treatment to Remove Arsenic from Copper Ore
This study tested the removal of arsenic from copper ore concentrate via a mechanochemical treatment by planetary ball milling. The harmful components of ore, such as arsenic, are increasing year by year and decreasing the copper grade, therefore there is a strong need to improve the separation of arsenic from copper ore. The effect of Simulations of a batch grinding test for copper ore for a feed of 1.18-1.00 mm. Stirrer speed at 3.0 m/s, slurry at 50% solids (in weight) and ball size of 20 mm. Disappearance plots have been prepared as a function of particle size, and results are typical shown in Fig. 5. From these plots it is possible, in analogy to the analyses ofPredicting the effect of operating and design variables in grinding
احصل على السعر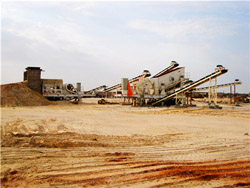
A critical review on the mechanisms of chemical additives
In the grinding of a taconite ore with sodium hydroxide, Hartley et al. [93] reported an increase of grinding efficiency for a feed with a narrow (uniform) size compared to a feed with a wide range size. From their observations, the application of GAs is more effective on narrow PSD feed compared to the feed with a widespread PSD.Energy costs typically comprise one of the largest ongoing costs of mining operations, of which 70% is devoted to the comminution of the ore (Norgate and Jahanshahi, 2010). Furthermore, the most significant energy cost occurs in the grinding circuit of the Milling section, where up to 97% of the energy cost is incurred (Ballantyne et al., 2012).Mine operating costs and the potential impacts of energy and grinding
احصل على السعر
Maximise pyrite depression in copper ore flotation using
The flotation results obtained in high salinity water at pH 8.0 after grinding with forged steel and Hi-Cr steel media as reported in the previous work (Mu and Peng, 2021) are also shown in Fig. 1.When forged steel was used as grinding media, 78.0% chalcopyrite recovery and 39.9% pyrite recovery with a low Cu grade of 4.3% were The mining industry has faced significant challenges to maintaining copper production technically, economically, and environmentally viable. Some of the major limitations that must be Chemical Composition Data of the Main Stages of
احصل على السعر
Minerals Free Full-Text Potential Benefits in
The technology of high-pressure grinding, originally invented and developed by professor Klaus Schönert [], is currently considered as one of the most efficient methods of hard ore Introduction. Wet milling in ball mills followed by flotation is the general practice employed in the beneficiation of copper sulphide ores in which the major minerals of commercial significance typically are chalcopyrite (CuFeS 2), bornite (Cu 5 FeS 4), covellite (CuS) and chalcocite (Cu 2 S). The flotation response of ground minerals can be A review of the effects of the grinding environment on the
احصل على السعر
Effect of microwave pretreatment on grinding and flotation
The present study initially investigates the kinetics of microwave-assisted grinding and flotation in a porphyry copper deposit. Kinetic tests were conducted on untreated and microwave-irradiated samples by varying the exposure time from 15 to 150 s. Optical microscopy, energy-dispersive X-ray spectroscopy, and scanning electron The present study initially investigates the kinetics of microwave-assisted grinding and flotation in a porphyry copper deposit. Kinetic tests were conducted on untreated and microwave-irradiated samples by varying the exposure time from 15 to 150 s. Optical microscopy, energy-dispersive X-ray spectroscopy, and scanning electron Effect of microwave pretreatment on grinding and flotation
احصل على السعر
Increasing the grind size for effective liberation and flotation
For the porphyry copper ore tested in these investigations, a coarse copper sulphide grain size coupled with a high association with hard microwave-transparent (i.e. quartz) and hard microwave-heating (i.e. pyrite) minerals resulted in a grind size increase of 50–60 μm for equivalent liberation or an approximate 2.5% increase in liberationHowever, by grinding copper ore for 30 s, a product characterized by a fraction of 0–0.02 mm in an amount of more than 77% was obtained. Table 3 presents the energy consumption problem with respect to grinding time. It can be seen that the specific energy changes with a longer processing time.Grinding Kinetics Adjustment of Copper Ore Grinding in an
احصل على السعر
Copper Mining Bulk Ore Sorting Thermo Fisher Scientific
The goal is to grind the ore just enough for optimum copper mineral liberation in the froth flotation plant circuit. Under-grinding reduces recovery; overgrinding reduces throughput and wastes energy. Real-time particle size analysis in slurry is the key to effective grinding control in finer particle sizes prior to froth flotation.Moisture of bulk material has a significant impact on energetic efficiency of dry grinding, resultant particle size distribution and particle shape, and conditions of powder transport. As a consequence, moisture needs to be measured or estimated (modelled) in many points. This research investigates mutual relations between material moisture and Sensors Free Full-Text Measurement-Based Modelling of
احصل على السعر
Crushing and grinding process of copper ore Crusher Plant
In the grinding process, the two-stage one-closed grinding is an efficient grinding process, which can make the copper ore grind more fully. Among the beneficiation processes, the most successful new processes that have appeared in recent years are mainly mixed flotation processes. Stage 1: crushing and screening
احصل على السعر