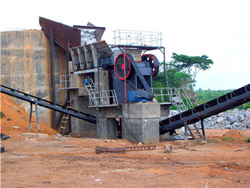
Energy saving by modification of the vibration mill
A vibration mill is the equipment often used nowadays for fine and ultrafine grinding. Research shows that what limits further improvement of the vibration mill's The results showed that the characteristic power spectra energy of both the mill noise and vibration can represent the mill load accurately. In addition, they Experimental Analysis of Semi-autogenous Grinding Mill
احصل على السعر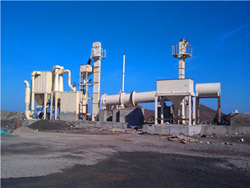
Motion of a Mill with Polyharmonic Vibration of the Grinding
The proposed mill with polyharmonic vibration of the grinding chamber operates as follows. The grinding chamber is loaded with a set of grinding bodies— for Commonly vibration mills are used to produce powders with a final particle size less than 5 µm. Mills are classified by drive design and the vibrations nature of a (PDF) The Development of a Cylindrical Vibration Mill and its
احصل على السعر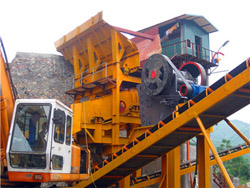
Vibration characteristics of an operating ball mill IOPscience
Abstract. A ball mill, which is used to finely grind materials, causes high levels of vibration and sound during grinding operations. The vibration and sound of mills In cooperation with the Siebtechnik, Mülheim, Germany, a single-pipe vibratory mill with a new mechanical vibration concept, the so-called “eccentric vibratory Eccentric vibratory mills — theory and practice ScienceDirect
احصل على السعر
Investigation of the effect of filling level on the wear and vibration
It was found that increasing the ore filling level would increase energy consumption and reduce the energy efficiency and the wear of liner and grinding media. 1. Introduction Some years ago vibration mill batch tests were done to compare “small” (10 mm) and “large” (30 mm) circles of vibration. This difference was Vibration mill results in the light of stress intensity and
احصل على السعر
Energy saving by modification of the vibration mill
A vibration mill is the equipment often used nowadays for fine and ultrafine grinding. Research shows that what limits further improvement of the vibration mill's Alternatively, establishing a correlation between impact energy and grinding rate provides a way of eliminating the simulation of fine particles. In the previous studies [17, 19, 20, 36], it has been shown that there is a link between grinding rate and impact energy for given grinding materials under different mill speeds and fill volumeImpact energy of particles in ball mills based on DEM simulations
احصل على السعر
DETERMINATION OF CORRELATION BETWEEN SPECIFIC
vibration values on the main driving motors less than 4 mm/s by periodical maintenance, the specific electrical energy consumption of the mill has reduced by 2.16% to 24.97 kWh/ton farine which corresponds to a saving of 0.55 kWh per ton of farine production. Keywords: Cement, Raw mill, Vibration, Energy, GrindingThe mode of vibration of the Vibro-Energy Grinding Mill is tailored to ensure close packing of the media. Cylinders are the usual grinding media since they will provide more contact area than any other Grinding Machines Designed and Manufactured
احصل على السعر
Studies in vibration milling ScienceDirect
The results of 300 experimental runs on vibration milling of soapstone, graphite, cXte, magnesite, rock phosphate, granite and zirX sand covering particle size range of (−0.25+0.10) to (−1.00+ 0.80) mm, density range of 2.29−4.59 g/cm 3, hardness range of 1–7 Mho's hardness number and surface energy range of 4.50–38.66 kg f m/m One of the varieties of vibration mills is a toroidal mill. It is a continuous-flow-type vertical vibration mill, where the vibration action on the grinding bodies is perpendicular to the Earth’s surface, which reduces the impact of gravity forces on grinding and ensures that the loss of supplied energy is minimal.Mechanochemical and Size Reduction Machines for Biorefining
احصل على السعر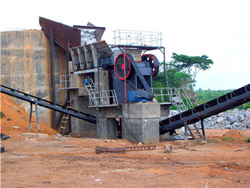
Experimental Analysis of Semi-autogenous Grinding Mill
In the present work, vibration, acoustic and thermal signals were correlated to the semi-autogenous grinding mill working parameters such as total power and inlet water flow rate, and then these parameters were monitored using vibration, acoustic and thermal analyses. Next, the influential controlling parameters were obtained to monitor the mill Modeling results can be used for the selection of the optimum mill size and operating parameters in order to obtain the desired grinding products and reduce energy consumption. Grinding kinetics shows that the breakage rate varies with grinding time, and thus the traditional linear theory of the population balance model cannot be applied to theModeling of Bauxite Ore Wet Milling for the Improvement of
احصل على السعر
Eccentric vibratory mills — theory and practice ScienceDirect
Vibratory mills consist of cylindrical or trough-like elastically suspended grinding pipes, which by means of a balanced mass system, are excited to circular vibrations with accelerations Rω 2 (R the radius of the vibratory circle of motion and ω the angular velocity of the unbalanced mass) of up to approximately 10 g — rarely above that. Inside Vibration mills are widely used to obtain powders with the particle size of the final product of less than 10 microns. Depending on the design of a drive from and the nature of vibrations of a(PDF) Optimization of material grinding in vibration mills
احصل على السعر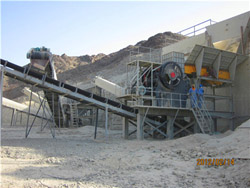
VIBRO-ENERGY SWECO PDF Catalogs DirectIndustry
Open the catalog to page 1. rte SW'£CO /Vrert Drive Vibro-Energg Motion Generator has been specifically designed to operate under the extreme vibratory stresses inherent in SWECO Finishing Mills. As an integral part of the chamber assembly, energy is transmitted directly into the parts/media mass resulting in greater capacity per horsepowerThe Vibro-Energy principle of applying high frequency, three dimensional vibration to a chamber containing small cylindrical griding media helps to overcome both of these limitations. It takes less total energy to reduce or break a small particle than it does a large one. For ultra-fne grinding, only very small impact forces are necessary. Any force Working of a Vibro-Energy Mill Chemical Market
احصل على السعر
Energies Free Full-Text Increasing Energy
Tumbling mills have been widely implemented in many industrial sectors for the grinding of bulk materials. They have been used for decades in the production of fines and in the final stages of ore This work concentrates on the energy consumption and grinding energy efficiency of a laboratory vertical roller mill (VRM) under various operating parameters. For design of experiments (DOE), the Minerals Free Full-Text Analysis and
احصل على السعر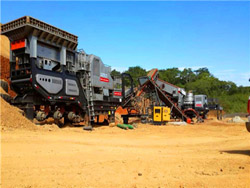
Vibration characteristics of an operating ball mill IOPscience
Abstract. A ball mill, which is used to finely grind materials, causes high levels of vibration and sound during grinding operations. The vibration and sound of mills provide significant information about the internal conditions and can be used to estimate the status of the ground material. We developed a simulation model for the vibration of aWe have found that similar to stirred ball mill results the mass related specific energy (1) W M = (Md − Md 0) ω t / M (Md: torque during comminution; Md 0: torque without grinding media and particles; ω: angular velocity; t: duration of grinding; M: particle mass) is a characteristic parameter.During the main investigation grinding media Vibration mill results in the light of stress intensity and
احصل على السعر
Investigation of the effect of filling level on the wear and vibration
Introduction. Ball mill is a typical and common milling equipment, and it has been widely used in cement, silicate products, non-ferrous metal beneficiation, glass ceramics, medicine, construction and other production industries (Luo, Liu, Jia, & Cai, 2011; Mishra & Rajamani, 1992; Suryanarayana, 2001).However, the ball mill is a typical type Fine and ultrafine grinding of limestone are frequently used in the pharmaceutical, chemical, construction, food, and cosmetic industries, however, research investigations have not yet been published on the combination of energy and life cycle modeling. Therefore, the first aim of this research work was the examination of main Energy-Model and Life Cycle-Model for Grinding Processes
احصل على السعر
Energies Free Full-Text Increasing Energy Efficiency and
Tumbling mills have been widely implemented in many industrial sectors for the grinding of bulk materials. They have been used for decades in the production of fines and in the final stages of ore comminution, where optimal levels for the enrichment particles’ sizes are obtained. Even though these ubiquitous machines of relatively simple The present study investigates the propensity of predicting ore grindability characteristics and varying pulp densities through acoustic measurements on the Magotteaux ball mill. Specifically, the grinding behaviour of two different mill feeds (model quartz and iron ore) together with solid loadings (50, 57, and 67 wt% solids) were Investigation on measuring the fill level of an industrial ball mill
احصل على السعر
Comparative comminution efficiencies of rotary, stirred and
Fig. 4 shows a linear correlation for the results from all the milling devices on both biomasses, in agreement with the Rittinger model which states that grinding energy is directly proportional to created specific surface area [35]. The coefficient of this linear correlation is related to type of biomass and type of mill.
احصل على السعر