
Production of Ferro-Silicon and Calcium Silicon Alloys
Initially the process of production of fern-silicon was developed empirically [1]. Ferro-silicon is made by reducing quartzite with metallurgical coke/gas coke/Low The process of Ferrosilicon production involves the reduction of sand or silica (Si) with coke / coal (C), and then reacting it with iron (Fe) which can be obtained from scraps. The Ferrosilicon Production Process DMS Powders DMS
احصل على السعر
Ferrosilicon an overview ScienceDirect Topics
Ferrosilicon production is a nearly slag-free process (the silicate-based slag amount does not exceed 3% to 5% of the alloy mass). However, the tapping of ferrosilicon and slag This article deals with material research of selected types of quartz and quartzites in order to determine the priority of their use in the production of ferrosilicon and pure silicon, respectively.(PDF) New Approach in Research of Quartzes and
احصل على السعر
Ferrosilicon and Silicon Technology ScienceDirect
This chapter examines the theory and technology of the production of silicon and ferrosilicon alloys. An overview of silica raw materials, silica transformations, and Carbothermic process of Ferro Silicon production is primarily a slag-less process. However, slag formation is observed in the regular operation as experienced by almost all the Ferro FERRO SILICON OPERATION AT IMFA A CRITICAL ANALYSIS
احصل على السعر
The Complete Book on Ferroalloys Semantic Scholar
This book concisely presents the core principles and varied details involved in processing of ferroalloys. The work includes detailed coverage of the major Metrics. The paper presents the results of a project performed under the conditions of the Re Alloys plant for the production of aluminum ferrosilicon having a Industrial Experience of Aluminum Ferrosilicon Production in
احصل على السعر
Metals Free Full-Text New Approach in Research of
Videm, T. Reaction rate of reduction materials for the (Ferro) Silicon process. In Proceedings of the INFACON 7, International Ferroalloys Congress, Trondheim, Norway, 11–14 June 1995; pp. 221–230. [Google Scholar] Myrvagnes, V. Analyses and Characterization of Fossil Carbonaceous Material for Silicon Production.In this review article, the state of the art of the complete processing chain in the production of solar photo-electric modules from raw materials (quartzites, quartz sand) is detailed. In particular, the silicon Integration of Kazakhstan Technologies for Silicon
احصل على السعر
What is ferrosilicon? Elkem
2 天之前The production of silicon ferroalloys uses carbon to remove the oxygen from silica, releasing carbon dioxide in the process. The high temperatures needed in our furnaces also consume a lot of energy. But we’re committed to doing what we can to reduce this CO₂ footprint, by increasing the proportion of renewably-sourced carbon we use, Proceedings of the 16th International Ferro-Alloys Congress (INFACON XVI) 2021. 11 Pages indirect emissions due the production of the electrical energy used in the production process. As production of metallurgical grade (MG) silicon is energy intensive, the indirect emissions from the electrical energy production contribute a Greenhouse Gas Emissions from Silicon Production
احصل على السعر
Ferrosilicon and Silicon Technology ScienceDirect
The development of the industrial process of silicon production took almost a century (Schei et al., 1998, Vishu et al., 2005). With the development of the electric arc furnace by Paul Héroult, the first commercial plant was started in the United States in 1907, where high silicon ferrosilicon and silicon could be produced industrially.After general ferro silicon manufacturing process, refining procedure is also necessary in order to remove Aluminum, Calcium, Carbon and other harmful elements. Sizing is also a very important part of ferro silicon manufacturing process. Standard lumps are easy to use as deoxidizing agent for steel factory. It’s crashed and then selected toFerro Silicon Manufacturing Process Method sialloy
احصل على السعر
(PDF) New Approach in Research of Quartzes and Quartzites
For carbothermic reduction, we used modified samples of. quartzes or quartzites in two granulometric classes: below 0.5 mm and 1–5 mm. The mass. ratio of quartz (or quartzite) to charcoal wasThe developed procedure used for SiO reactivity measurements was a useful tool to classify charcoal for use in the silicon production process. (1995) Reaction rate of reduction materials for the (ferro)silicon process. In: Proceedings of VII international ferro alloys congress Trondheim, Norway, 1995, pp 221–230. Vital BR (1984) MethodsReactivity assessment of charcoal for use in silicon production
احصل على السعر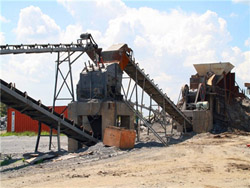
Pilot-Scale Test of Flue Gas Recirculation for The Silicon Process
Flue gas recirculation (FGR) for the silicon process may facilitate increasing the CO2 concentration in the off-gas, which will be beneficial for potential future carbon capture. Lower oxygen concentration in the combustion gas will also reduce NOX emissions. An existing 400 kVA Submerged Arc Furnace (SAF) pilot setup was modified A pilot scale, silicomanganese alloy production campaign was performed in a 440 kVA, single phase electric furnace in order to establish an overview of the minor- and trace element contents in process input raw materials and their distribution in the resulting primary and secondary products. Samples of the in-going raw materials (manganese ore, Element Distribution in the Silicomanganese Production Process
احصل على السعر
(PDF) MODEL OF THE FERROSILICON MELTING
The results of calculations for a physicochemical model of the ferrosilicon process with two isothermal reactors after 50 cycles. The system Fe-Si-O-C-Al-Ca-Mg-Ti, the reaction mixture (2), T1Carbothermic process of Ferro Silicon production is primarily a slag-less process. However, slag formation is observed in the regular operation as experienced by almost all the Ferro Silicon Producers in different proportions. The problem of slagging in the furnaces may be due to: a) Variation in the input burden charge material quality b) Fluctuations in the FERRO SILICON OPERATION AT IMFA A CRITICAL ANALYSIS
احصل على السعر
Metallurgy of Ferrosilicon SpringerLink
Bisilicide FeSi 2 exists in two versions: high-temperature FeSi 2 (HT) in the range of 937–1220 °C and low-temperature FeSi 2 (LT) below 937 °C. High-temperature modification is a non-stoichiometric compound that exists in a certain range of silicon concentration. In the literature, this silicide is described by the formula FeSi 2,3, i.e., as a One of the Ferro-silico-manganese uses is for molten steel de-oxidation process. The production of ferro-silico-manganese alloy uses manganese ore, quartz and iron ore as raw materials [20]. The copper smelting slag is rich in iron and silicon, and thus is an attractive substitute for the quartz and iron ore in the ferro-silico-manganeseFerro-silico-manganese production from manganese ore and
احصل على السعر
Metals Free Full-Text New Approach in Research of
Videm, T. Reaction rate of reduction materials for the (Ferro) Silicon process. In Proceedings of the INFACON 7, International Ferroalloys Congress, Trondheim, Norway, 11–14 June 1995; pp. 221–230. [Google Scholar] Myrvagnes, V. Analyses and Characterization of Fossil Carbonaceous Material for Silicon Production.To illustrate, the carbon footprint of a life cycle of each kilogram of silicon metal (taking into account the mining of raw materials, transportation, energy, as well as the production process(PDF) Greenhouse Gas Emissions from Silicon Production
احصل على السعر
Silica Fume Formation in Different Gas Atmospheres
Silica fume is an important byproduct from the silicon production process, with mainly concrete and refractory applications. In this work, the effect of different combustion gas atmospheres on the properties of silica fume has been investigated through small-scale experiments and a pilot-scale experiment. In the small-scale experiments, 5 Ferrochrome Production Process 8 6 Chrome Value Chain 9 7 Manganese Value System 11 8 Manganese Alloys Production Process 13 9 Manganese Value Chain 14 submerged arc furnace to produce ferro-silicon-chromium (FeSiCr) in a ‘dry’ or slag-free process. The ferro-silicon-chrome has a low carbon content. 7SOUTH AFRICANFERROALLOYS HANDBOOK 2013
احصل على السعر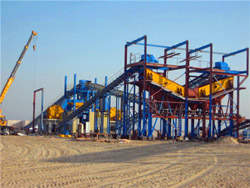
Energy balance of a 45 MW (ferro-) silicon submerged arc furnace
Teakla et al. [15] evaluated industrial silicon production processes in terms of resource utilization and potential process improvements. Kamfjord et al. [40] carried out the energy balance of aLindstad, G. Enstad and H.Tveit, "Clogging of ferro-silicon furnace off-gas channels at high temperatures" (Smelter Process Gas Handling and Treatment, Eds. T.J.A: Smith and C. J. Newman, The(PDF) Environmental aspects of Ferro-Silicon furnace
احصل على السعر