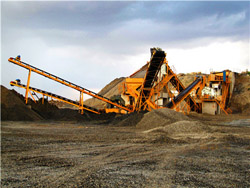
Fracture Processes in Granite Blocks Under Blast Loading
contribute to a better understanding of the fundamental mechanisms of the rock fracture by blasting. Keywords Blasting Rock fracture Crack opening Fragment Rock and crushed stone products generally are loosened by drilling and blasting and then are loaded by power shovel or front-end loader into large haul trucks 11.19.2 Crushed Stone Processing and Pulverized
احصل على السعر
Evaluation of blast efficiency in aggregate quarries: facts and
Blasting and materials handling are two core operations in aggregate quarrying industries that account for a higher percentage of operating costs when Many researchers have examined the effect of specific charge value used in blasting and therefore pile size distribution occurred as a result of the blasting on crushing grinding processesGeneral flow chart belonging to the Bornova
احصل على السعر
A review of some nonexplosive alternative methods to
Abstract The conventional blasting rock excavation method is the main means of rock breakage because of its high productivity, and it is relatively inexpensive compared to This paper examines the role blasting plays in optimum crushing and grinding with the emphasis on energy reduction. The role of different blasting energy Effects of Blasting on Crushing and Grinding Efficiency
احصل على السعر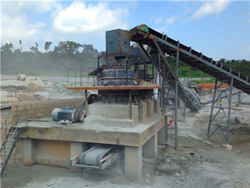
Fracture Processes in Granite Blocks Under Blast Loading
Last Updated: 12 Jun 2023. Request PDF Fracture Processes in Granite Blocks Under Blast Loading The fracturing of six granite cubes (400 × 400 × 400 mm³) Blasting operation is a conventional way for fragmenting rock in mining and civil engineering projects. In surface mining, production begins with drilling and blasting Optimization of Blasting-Associated Costs in Surface Mines
احصل على السعر
[PDF] The Effects of Blasting on Crushing and Grinding Efficiency and
It is reasonable to postulate that the size distribution of blasted fragments, and the internal softening of individual fragments by blasting can affect crushing and grinding The conventional blasting rock excavation method is the main means of rock breakage because of its high productivity, and it is relatively inexpensive compared to other methods. However, it raises safety concerns and can negatively impact the environment. The major disturbances that may be induced by this method include flyrock, gas emissions, and A review of some nonexplosive alternative methods to
احصل على السعر
ITP Mining: Mine-to-Mill Optimization Energy
aggregate production process. Researchers at Virginia Polytechnic Institute and State University, along with their project partners, are looking at mine-to-mill technology to effectively optimize the production of crushed stone. A general purpose blasting simulation package (JKSimBlast) will be used to evaluate blasting performance.Bench blasting is the most widely used method of production blasting in quarrying, strip mining and construction excavation. This involves drilling inclined, vertical or horizontal blastholes in single- or multiple-row patterns to depths ranging from a few meters to 30 m or more, depending on the desired bench height.Quarrying Process and Equipment Applications Epiroc US
احصل على السعر
Physical Bauxite Processing: Crushing and Grinding of Bauxite
3.1 Introduction to Crushing and Grinding of Bauxite. The most common initial process step to feed an alumina refinery with bauxite is the crushing or sizing of the raw bauxite material that is extracted from the mine. The feed material is crushed or sized so that it is conveyable, as well as correctly dimensioned, for the next step in the process.Contribute to redmik40/sbm development by creating an account on .sbm/sbm china most famous sand blasting machines impact crusher
احصل على السعر
11.19.2 Crushed Stone Processing US EPA
11.19.2 Crushed Stone Processing 11.19.2.1 Process Description1-2 Rock and crushed stone products generally are loosened by drilling and blasting, then are crusher output, which is typically about 0.50 to 2.5 centimeters (3/16th to 1 inch), is returned to the sizing screen. Various product streams with different size gradations arelevels during blasting process ranged between 102.8± 2.6db and 130.4± . Farzana1, S Z, A.H Nury., B B iswa and A Das (2 014) A study on noise po llution of stone crusher machine at .(PDF) A STUDY ON NOISE POLLUTION AT STONE QUARRYING
احصل على السعر
Low cost Stone Crusher Manufacturer India Jaw crusher for
What is the cost of Stone crusher in India? Stone crusher price starts from Rs. 30,00,000 lacs and goes upto 2,50,00,000 crores depending on the capacity of the Stone crusher. A 30 TPH Jaw crusher price in Delhi is Rs. 65,00,000 lacs. A mini jaw crusher machine price starts from Rs. 15,00,000 lacs.You've already forked crusher 0 Code Issues Pull Requests Packages Projects Releases Wiki Activity You can not select more than 25 topics Topics must start with a letter or number, can include dashes ('-') and can be up to 35 characters long. 1 Commit. 1 Branch. 0 Tags. 57 MiB . Tag: Branch: Tree: master. Branches Tagscrusher/sbm explain wedging and blasting methods of stone
احصل على السعر
SIZE REDUCTION BY CRUSHING METHODS By
5 5.2 Gyratory crusher : A gyratory crusher is similar in basic concept to a jaw crusher, consisting of a concave surface and a conical head; both surfaces are typically lined with manganese steelThis study reports on the design optimisation of the swinging jaw crusher plate. Jaw crusher machines are used in the mining and construction industry for crushing rocks and mineral ores to the appropriate sizes for direct application or further processing. During the crushing process, large and non-evenly distributed impact forces occur, Optimisation of the swinging jaw design for a single toggle jaw crusher
احصل على السعر
A review of some nonexplosive alternative methods to
The conventional blasting rock excavation method is the main means of rock breakage because of its high productivity, and it is relatively inexpensive compared to other methods. However, it raises safety concerns and can negatively impact the environment. The major disturbances that may be induced by this method include flyrock, gas emissions, and crusher receives the run-of-mine ore after blasting and produces the first reduction in size after mine field blasting. The output of the primary crusher is fed through the grinding and milling process of the processing plant. An increase in the degree of fragmentation gives lower crushing costs as more material passes through as undersize.Rock Fragmentation Evaluation towards Blast-To-Mill
احصل على السعر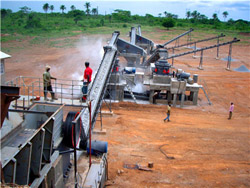
Dust emission from crushing of hard rock aggregates
All processes of aggregate production are potential sources of dust emission. Dust constitutes a major environmental concern in many quarries, with crushing suggested as the most significant source of it ( Bada et al., 2013; Petavratzi et al., 2005; Sairanen et al., 2018 ). Dust from drilling has been previously examined in two natural Blasting can also have a direct impact on crushing and grinding performance because of the degradation in rock mechanical properties (Nielsen and Kristiansen, 1996; Michaux and Djordjevic, 2005Blasting-crushing-grinding: Optimisation of an
احصل على السعر
Key Blasting Parameters for Deep-Hole Excavation in an
The cut blasting process can be clearly seen in Figure 3.At the moment of 240 μs, the cut area turns red, and the stress wave effect of the explosive is the largest, and it affects the whole area.At 280 μs, the stress waves of the first and third rows of charge holes are superimposed along the hole coring line, causing the rock in the hole coring In order to blast the in-situ rock to the desired fragment size, blast design parameter such as bench height, hole diameter, spacing, burden, hole length, bottom charge, specific charge and rock(PDF) Optimization of Blasting Parameters- A case study
احصل على السعر
Quarrying of Stone: Types, Methods & Tools
The following instruments are required within the process of blasting like a dipper, jumper, priming needle, scraping spoon, and tamping bar. Tools for Quarrying of Stone: The following tools are required within the blasting process as follows: (1) Dipper: It is used to drill a gap to the required depth.2 Jul 2022; Granite grinding machines. Granite grinding machines are composed by a number of ancillary equipment, mining equipment, and then blasting process, clinker blasting process through the granite, granite clinker fragments, rock hammer, falling ball, and the lower crusher, gyratory crushermachines and other equipment, crude materials sent by Granite processing grinding mill machines C&M Mining
احصل على السعر
11.19.2 Crushed Stone Processing and Pulverized
crusher product, normally 7.5 to 30 centimeters (3 to 12 inches) in diameter, and the grizzly Typical stone processing plant . Drilling and Blasting SCC-3-06-020-09, 10 Truck Loading SCC-3-05-020-33 Haul Roads stone processed, the process throughput rate, the type of equipment and operating practices used,
احصل على السعر