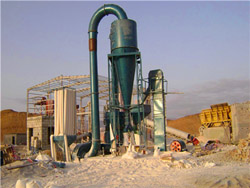
Impact of key parameters on the iron ore pellets roller
Thomazini has reported, through discrete element analysis (DEM), the screening efficiency of an iron ore pelletizing plant using a single deck roller screen The present work deals with the estimation of material and contact parameters of green iron ore pellets for simulation using DEM, followed by simulating a Modeling and simulation of green iron ore pellet classification
احصل على السعر
Effects of Rollers Speed Regime on the Roller Screen Efficiency
Roller screen is a key device in pelletizing plants employed to size classification of green pellets. Realistic observations showed that some pellets with size The roller screening process is an important step in the iron ore pellets production. This step is intrinsically linked to the balling production and the induration machine. Improvements Impact of key parameters on the iron ore pellets roller
احصل على السعر
Computer simulation to optimize roller screen settings
The objective of the current research is the simulation of a roller screen for the classification of iron green pellets. The geometry and characteristics of the problem DEM computer simulation was implemented to reveal the effects of different parameters on the efficiency of the roller screen. The numerical simulations were Computer simulation to optimize roller screen settings
احصل على السعر
Improvement in Roller Screening of Green Iron Ore Pellets by
Such results led to a proposition of a new configuration for the roller screen, which consisted in a significant reduction in roll diameter and deck slope, an It is a review manuscript describing the screen variables and its impact on the iron ore pelletizing process. The roller screening process is an important step in the iron ore Impact of key parameters on the iron ore pellets roller
احصل على السعر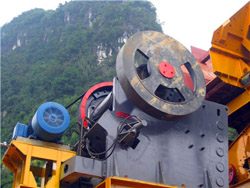
(PDF) Machine Learning based Image Processing for Iron Ore
In an iron ore pelletization plant, pellets are produced inside a rotating disc pelletizer. Online pellet size distribution is an important performance indicator of the pelletization process.Size of the fired iron ore pellets is a critical variable throughout the process, being normally controlled between about 8 and 18 mm using roller screens in the green pellet area [4] andModeling and simulation of green iron ore pellet classification in
احصل على السعر
(PDF) Impact of key parameters on the iron ore
pelletizing plant using a single deck roller screen (SDRS) at the discharge end of a balling disk using a gap strategy of 9.00 mm for undersize removal and 16.00 mm for oversizedThe first industrial application of the technology in the size reduction of iron ore pellet feed was by the Swedish company LKAB at the Malmberget plant in 1993 (Van der Meer, 1997) for increasing the surface area of the final concentrate prior to pelletizing. After this, application in the iron industry grew rapidly around the world.Pressing iron ore concentrate in a pilot-scale HPGR. Part 1
احصل على السعر
Application examples of high-pressure grinding rollers
A high-pressure roller mill with 2400mm and a roller width of 1650mm is used for fine crushing of ore, each with a processing capacity of 2500t/h; and the PT Freeport copper and gold mine inThe roller press, also called high-pressure grinding rolls (HPGRs), has been successfully used for over 25 years in increasing the surface area of iron ore concentrates for pellet feed production prior to green pellet formation. In spite of the long track record of application, there have been no systematic mathematical modeling Pressing iron ore concentrate in a pilot-scale HPGR. Part 2:
احصل على السعر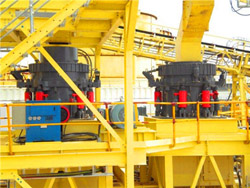
Developments in iron ore comminution and classification
HPGR technology was introduced to the mineral processing industry in the mid-1980s and has rapidly (for the mining industry) established itself as the convention in the comminution of cement, clinker, slag, iron ore, iron pellet plant feed, and diamond ore. There are now approximately over 500 machines operating in these applications.The quality of Indian iron ore resources is generally good with high iron content and high percentage of lumpy ore. More than 85% of the hematite ore reserves are of medium- to high-grade (+62% Fe) and are directly used in blast furnace and in direct-reduced iron (DRI) plants in the form of sized lump ore, agglomerated sinter, and Iron ore beneficiation: an overview ScienceDirect
احصل على السعر
Mobile screening plants in a large-scale operation in India
1 天前India has vast reserves of iron ore and is the second biggest steel producer in the world. The mobile screening plants MOBISCREEN EVO from Kleemann are used during the extraction of the important material. India's total iron ore production for 2019 was 231 million tons, approx. 90 percent of which was used in domestic steel production. HematiteResearch regarding iron ore flotation began in 1931, demonstrating that reverse cationic flotation is a very efficient method for beneficiating oxidised iron ores. This method can also be applied(PDF) An overview of the beneficiation of iron ores via
احصل على السعر
Fig. 1. Pellet's movement over the roller screen
In an iron ore pelletization plant, pellets are produced inside a rotating disc pelletizer. Online pellet size distribution is an important performance indicator of the pelletization process.Finally these iron ore pellets under goes cooling in the cooling tower. Later the iron ore pellets goes with the sinter screeners for screening process. The unsized iron ore pellets are sent to the re-sintering process and the perfect sized iron ore pellets are sent to the Blast Furnace. 3. INTEGRATION OF HAMMER CRUSHERS 3.1 Hammer CrusherOPTIMIZATION OF IRON ORE PELLETS PRODUCTION IN
احصل على السعر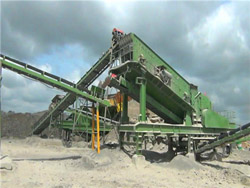
Iron Ore Processing, General SpringerLink
Iron ore handling, which may account for 20–50% of the total delivered cost of raw materials, covers the processes of transportation, storage, feeding, and washing of the ore en route to or during its various stages of treatment in the mill.. Since the physical state of iron ores in situ may range from friable, or even sandy materials, to monolithic Since its establishment in 1982, CVIC has been a leading supplier for the iron ore pelletizing industry. CVIC began as a supplier for pelletizing roller screen spare parts. Later, we started to design and manufacture our own roller screens. CVIC has witnessed the entire development process of the iron ore pelletizing industry from the shaftAbout CVIC Iron Ore Pelletization Solutions Roller Screen
احصل على السعر
Detection and segmentation of iron ore green pellets in
In steel manufacturing industry, powdered iron ore is agglomerated in a pelletizing disk to form iron ore green pellets. The agglomeration process is usually monitored using a camera. As pellet size distribution is one of the major measures of product quality monitoring, pellets detection and segmentation from the image are the key steps 1. A process for comminuting an iron ore at natural moisture or an iron ore product, at natural moisture comprising pressing with a roller press (HPGR), milling with a vertical roller mill (VRM), crushing with a roller crusher (RC), and/or screening with a high acceleration screen of at least 10G, the iron ore or the iron ore product at natural moisture.COMMINUTION PROCESS OF IRON ORE OR IRON ORE
احصل على السعر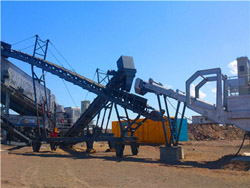
Impact of key parameters on the iron ore pellets roller
1 Metal 7 Inc, 285, des Pionniers, CP 1590, G4R 4X9, Sept-Îles, QC, Canada 2 Minerai de Fer du Québec, 1100, Boul. René-Lévesque Ouest, Suite 610, Montréal, QC H3B 4N4, Canada * e-mail: agandrade@metal7 Received: 18 March 2022 Accepted: 5 May 2022 Abstract. The roller screening process is an important step 英语网站资料. Contribute to sbmboy/en development by creating an account on .en/roller screen in iron ore processing plants.md at main
احصل على السعر
Computer simulation to optimize roller screen settings
The diameter of the pellets should be in a certain range, preferably 8-16 mm, to have a successful reaction in the direct reduction process. Therefore, iron pellet is the main requirement for making sponge iron, and is made via the agglomeration of iron ore small particles in a rotating drum or rotating disk (flange on the rim).A technology assessment checklist that investors should consider when making a new pellet plant investment decision is presented. Schematic of the straight grate pelletizing process. Thermal(PDF) GUIDELINES FOR SELECTING PELLET PLANT TECHNOLOGY
احصل على السعر