
Steelmaking
Modern steelmaking processes can be divided into three steps: primary, secondary and tertiary. Primary steelmaking involves smelting iron into steel. Secondary steelmaking involves adding or removing other elements such as alloying agents and dissolved gases. Tertiary steelmaking involves casting into sheets, rolls or othA process of removing iron impurities from ores, particularly useful for removing stains of iron impurities adhered to silica sand particles, comprises grinding the ore, washing and...Process of removing iron impurities from ores Google
احصل على السعر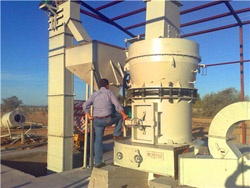
23.3: Metallurgy of Iron and Steel Chemistry LibreTexts
Impurities in the iron from the Blast Furnace include carbon, sulfur, phosphorus and silicon, which have to be removed. Removal of sulfur: The purpose of iron concentrators is to remove deleterious impurities and also to increase iron grades to an appropriate level suitable for steel making. This paper discusses about REMOVING IMPURITIES FROM IRON ORES: METHODS AND
احصل على السعر
(PDF) Development of Impurities Removal Process for
(PDF) Development of Impurities Removal Process for Low-Grade Iron ores using Mineral Processing Technologies PDF This study investigates the application of mineral processing to remove...Acid Leaching. Acid leaching is a strategy for removing iron impurities by understanding that quartz is not very soluble in acid (except hydrofluoric acid) and A Review on Removal of Iron Impurities from Quartz Mineral MDPI
احصل على السعر
Iron removal in production of purified quartz by
Iron, the predominant impurity in quartz ores, can be substantially removed via aqueous chemical processes using organic and inorganic acids. Quartz was Impurities with magnetic properties were removed by high field intense magnetic separator and in leaching tests, the influence of various factors including the performance of acids, reagent...Removal of Iron from Quartz Ore by Physical
احصل على السعر
Development of Impurities Removal Process for Low-Grade Iron
as impurities from Sanje iron ore. Sanje iron ore is the low-grade hematite ores found in Nampundwe area of Zambia from which iron is to be used as the feed in the steelmaking 1. Introduction. Australia’s iron ore industry is undergoing a major transformation. Reserves of traditional high-grade ores are becoming depleted while the replacement ore types are lower in grade and sometimes require beneficiation to remove or minimise contaminants such as alumina, silica and phosphorus (Dukino et al., 2000).The Characterisation of phosphorus and other impurities in
احصل على السعر
Phosphorus in Steelmaking Processes SpringerLink
This chapter examines the role of iron ore phosphorus in the development of steelmaking. The prosperity of steelmaking nations strongly depended on how they strategically dealt with iron ores with various phosphorus contents. At the beginning of steelmaking, the ore’s phosphorus content was immaterial. However, as Iron removal methods including conventional pre-treatment, magnetic separation, acid leaching, microbiological, roasting, and flotation, as well as combined iron removal methods in quartz ore, are(PDF) A Review on Removal of Iron Impurities from Quartz Mineral
احصل على السعر
Removal of Silica and Alumina as Impurities from Low-Grade Iron Ore
This study investigates the removal of silica and alumina as impurities from hematite based low-grade iron ore containing 34.18 mass% iron, 31.10 mass% of silica and 7.65 mass% alumina. Wet high-intensity magnetic separation (WHIMS) and reverse flotation (RF) were investigated. In WHIMS process, 93.08% of iron was Steelmaking. Steel mill with two arc furnaces. Steelmaking is the process of producing steel from iron ore and/or scrap. In steelmaking, impurities such as nitrogen, silicon, phosphorus, sulfur and excess carbon (the most important impurity) are removed from the sourced iron, and alloying elements such as manganese, nickel, chromium, carbon andSteelmaking
احصل على السعر
Which Processes Remove Impurities In Feldspar?
Iron removal by flotation process can be very good for iron-containing minerals in clay and fine-grained grades, but it is not effective for hard ores. For severely weathered ores, secondary sludge may be produced in the stage of crushing and grinding, which is likely to cause high viscosity of flotation foam, resulting in lower collector Iron is one of the most stubborn impurities in quartz minerals, and the iron content partly determines the various applications of quartz. Iron can exist in quartz in the forms of iron minerals, fluid inclusions, and lattice impurities. The removal of iron and the consequent purification of quartz minerals are the key processes to obtaining high A Review on Removal of Iron Impurities from Quartz Mineral
احصل على السعر
Removal of Sulfur From Iron Ore with Physical and Chemical
together. Low-grade iron ore, with a high sulfur content, constitutes a significant bottleneck especially in technical applications. Various physical and chemical methods for removal of sulfur from a high sulfur content iron ore are applied. However, the sulfur removal process must be economical to be applicable reasonably.Name of iron compound main components Sintering is a process used to agglomerate iron ore fines in preparation for blast-furnace smelting and is usually Blast furnaces in Australia are located at Port Kembla and Whyalla. The removal, by oxidation, of impurities in pig iron such as silicon, phosphorus and sulfur andIron Geoscience Australia
احصل على السعر
Removal of impurities from a metal by chemical method is
Click here👆to get an answer to your question ️ Removal of impurities from a metal by chemical method is called: Solve Study Textbooks Iron: Cuprite: Copper: Haematite: Hard. View Medium. View solution > The common impurities present in bauxite ore are_____ Medium. View solution > Why is leaching used as the method of concentrationIron is one of the most stubborn impurities in quartz minerals, and the iron content partly determines the various applications of quartz. Iron can exist in quartz in the forms of iron minerals, fluid inclusions, and lattice impurities. The removal of iron and the consequent purification of quartz minerals are the key processes to obtaining high A Review on Removal of Iron Impurities from Quartz Mineral
احصل على السعر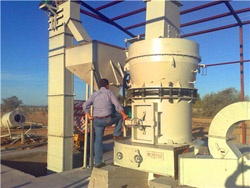
Advances in Beneficiation of Low-Grade Bauxite SpringerLink
In low-grade ores and run-of-mine (ROM), minerals are mostly associated with different impurities in the bauxite . The major impurities present in bauxite are silicon,iron oxides, and calcium, which introduces processing problems that can affect its utilizations in ceramics, abrasives and refractories [].Removal of these mineral The common ores of iron are its oxide, hematite, Fe2O3, and magnetite, Fe3O4. They can be reduced to iron by heating them with carbon in the form of coke. Skip to content. Removal of impurities: SILICA: add calcium oxide: CaO + SiO 2 ——> CaSiO 3: CARBON: add oxygen: C + O 2 ——> CO 2: PHOSPHORUS: add oxygen: 2P + 5O 2 ——> P 4 OIron Extraction W3schools
احصل على السعر
REMOVING IMPURITIES FROM IRON ORES: METHODS AND
Overall, the acceptable level of phosphorus, sulphur and silica in the iron concentrate should be less than 0.04%, 0.15 % and 1.5 % respectively. Scarcity of high grade iron ores necessitatesIron Ores 2 causes certain environmental problems [5–6]; the hematite method needs to be carried out under high temperature and pressure, which consumes large energy and5,100 126,000 145M
احصل على السعر
Civil Engineering Building Materials IndiaBIX
Exercise : Building Materials Section 3. 41. The cracks caused by shrinkage of the exterior surface of the wood exposed to atmosphere, are called: twisted fibres. 42. The process of decarbonising the pig iron completely and then adding proper percentage of carbon for manufacturing steel, is called. Open hearth process.Iron is a key detrimental impurity in silica sands that determines their contribution to high-technology industries. Herein, a simple ecologically sound approach is investigated for iron removal from a silica sand sample obtained from the El-Zaafarana area-Egypt. The sample was subjected to a detailed microscopic mineralogical study Characterization and Iron Removal Enhancement of El Springer
احصل على السعر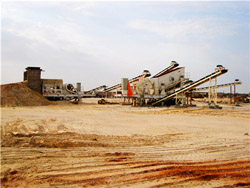
A review of hydrometallurgy techniques for the removal of impurities
Hydrometallurgy is considered a promising method to produce solar-grade silicon (SOG-Si) from metallurgical-grade silicon (MG-Si) due to its advantages of low cost, simple operation, and easy control. Researchers have investigated different hydrometallurgy techniques for impurity removal from MG-Si. This study systematically reviews The molten iron from the bottom of the furnace can be used as cast iron. Cast iron is very runny when it is molten and doesn't shrink much when it solidifies. It is therefore ideal for making castings hence its name. However, it is very impure, containing about 4% by weight of carbon. This carbon makes it very hard, but also very brittle.Iron Extraction and Purification / Steel ChemKey
احصل على السعر
What is a process for removing impurities from crude iron?
The most basic process is melting. From the earliest times of metal-working the melting of iron ore was used to ‘float’ the impurities to the surface, as slag. Even before the use of melting furnaces, the process of cyclic heating and working of the metal drove out many impurities. As furnace technology and control became better, the
احصل على السعر