
Iron ore sintering ScienceDirect
Sintering is the most economic and widely used agglomeration process to prepare iron ore fines for blast furnace use. In this chapter, the sintering process is first Iron ore sintering is the iron ore powder agglomeration process that changes fine iron ore powder into the lumpy iron-bearing raw material used for blast Iron Ore Sintering SpringerLink
احصل على السعر
Sinter plant
Main feed into a sinter plant is base mix, which consists of iron ore fines, coke fines and flux (limestone) fines. In addition to base mix, coke fines, flux fines, sinter fines, iron dust (collected from plant de-dusting system & ESP) and plant waste are mixed in proportion (by weight) in a rotary drum, often called mixing and nodulizing drum. Calcined lime is used as binder of the mixed material alSintering is a thermal agglomeration process that is applied to a mixture of iron ore fines, recycled ironmaking products, (PDF) Iron Ore Sintering: Process ResearchGate
احصل على السعر
Iron ore sintering ResearchGate
Sintering is the most economic and widely used agglomeration process to prepare iron ore fines for blast furnace use. In this chapter, the sintering process is first Based on the particle size, iron ores are classified as iron ore fines (<10 mm) or iron ore lump (6.3–31.5 mm); iron ore fines are first processed in a sinter plant, Sinter Plant Operations: Raw Materials SpringerLink
احصل على السعر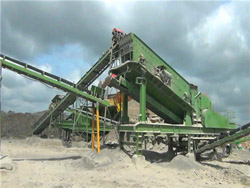
Prediction and Optimization of Internal Return Fines Generation in
The undersize so generated is called internal return fines, which are generally recirculated into the sintering machine. A very high level of internal return fines The sinter plant that converts the iron ore fines into a desirable blast furnace feed, offers an avenue for recycling wastes. One of the several wastes that are Utilization of Pellet Fines in the Iron Ore Sintering Process
احصل على السعر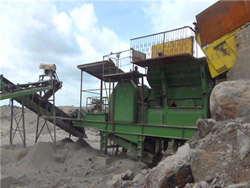
Iron Ore Sintering: Quality Indices Taylor & Francis Online
Read this article. Sinter plants process a mixture of iron ore fines, recycled ironmaking products, slag-forming agents and solid fuel (coke) with the finality HPS can be treated as an environmentally sustainable process as we can utilize iron ore fines and consume less coke, which is the need of the hour. (ii) The hyper-parameter-tuned ANN model showed Prediction of Sinter Properties Using a Hyper
احصل على السعر
Comminution and classification technologies of iron ore
Most of the high-grade hematite iron ores are typically subjected to simple dry processes of crushing and classification to meet the size specifications required for direct shipping ore (DSO). This involves multistages of crushing and screening to obtain lump (−31.5 + 6.3 mm) and fines (approximately −6.3 mm) products.Sintering is a thermal process (carried out at 1300 deg C to 1400 deg C) by which a mixture of iron ore, return fines, recycled products of the steel plant industry (such as mill scale, blast furnace dusts, etc.), The Sintering Process of Iron Ore Fines IspatGuru
احصل على السعر
Sinter Mix an overview ScienceDirect Topics
1.1.3.2.1.2 Iron-Bearing Materials. Ore fines and iron concentrates make the main part of the sinter mix.The grain size of ore fines and concentrates is typically 0–8 and 0–3 mm, respectively. Grains smaller than 0.1 mm are not desired because they reduce the gas permeability of the bed and thus decrease the sintering efficiency.Recycled materials, and sulphur to produce low –Si, low-S iron. 7. Increase of sinter percentage in Blast Furnace burden, increases the. productivity also. Sinter Making0260307 Free download as Powerpoint Presentation (.ppt), PDF File (.pdf), Sinter Making0260307 PDF Iron Ore Industries Scribd
احصل على السعر
Iron ore granulation for sinter production: Developments,
The kinetics of iron ore granules growth is also an important issue of greater engineering concern 42-44). In the actual iron ore granulation drum, the particle growth is often dependent on one or several modes of conversion between mechanisms. Population balance model (PBM), proposed more than thirty years ago, was first used in laboratory-Prior to dispatch of sinter to the blast furnace for hot metal production, the sinter product from the sinter cooler is screened to remove smaller/finer particles. The undersize so generated is called internal return fines, which are generally recirculated into the sintering machine. A very high level of internal return fines generation limits the use Prediction and Optimization of Internal Return Fines Generation in Iron
احصل على السعر
Virtual Sinter ® : Digital Twin for Integrated Sinter Plants
Sinter Plants, that produce iron ore sinter, are important units in an integrated steel plant. They face several operational challenges due to frequent changes in input raw materials, the inability to instrument key equipment in the plant, and the absence of real-time sinter quality measurement. To address these challenges, Virtual Sinter®, a In this study, a sintering test of high-alumina limonite from Indonesia, matched with an appropriate magnetite concentration, is performed. The sintering yield and quality index are effectively improved by optimizing the ore matching and regulating the basicity. For the optimal coke dosage of 5.8% and basicity of 1.8, the tumbling index of Characteristics and Sintering Mechanisms of Iron Ores with a High
احصل على السعر
What Iron Ore Crusher For Sinter Fines
Manuel, in Iron Ore, 2022. Sinter. Low-temperature ( 1300 °C) iron ore sinter is an agglomerate of unmelted and partially melted nuclei particles (+ 1 mm) and a matrix bonding phase produced from the melting of fine ore (− 1 mm) and flux particles, with the majority of melt formation occurring in the granule adhering Contribute to dinglei2022/en development by creating an account on .iron ore grind size sinter
احصل على السعر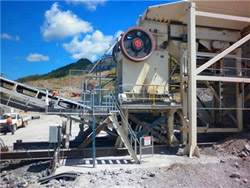
ISO 11323:2010(en), Iron ore and direct reduced iron ? Vocabulary
blend of ores and other iron-bearing materials, such as mill scale, basic oxygen steel-making slag, dust, etc., used for a sinter test Note 1 to entry: This term does not include return sinter fines (7.2.13),fluxes, coke breeze or other solid fuels.The ore size ranging in between 0.5 mm and 8 mm along with coke breeze fines, flux fines, other iron concentrates and suitable binders are generally used for sinter preparation which is a thermal agglomeration process [22,23,24].Utilization of Some of Major Steel Plant Wastes to Produce Metallic Iron
احصل على السعر
Microstructure and Minerals Evolution of Iron Ore Sinter:
Microstructure and Minerals Evolution of Iron Ore Sinter: Influence of SiO2 and Al2O3 Zhiyun Ji, Yuanjie Zhao, Min Gan coke breeze, and return fines. Table 1. Chemical compositions of iron ores. Iron Ore Types Number Chemical Compositions/% bLOI aTFe FeO CaO MgO SiO2 Al2O3 /% Typical Brazilian iron ores 1# 63.86 5.02 0.10 0.11 4.59 Measure the flow area of the specimen on the carrier sheet and calculate the liquid phase fluidity index (FI) of iron ore powder with the following equation. a = 𝑏 − 𝑐𝑐. (1) where: a —the liquid phase mobility index; b —the area of the specimen flowing on the carrier table; c —the area of the original specimen. 3.Sintering Properties and Regression Analysis of Imported Iron Ore
احصل على السعر
Influence of particle size distribution of iron ore fines on
1. Introduction. Shipping by sea currently accounts for more than 80% of global trade volume, with iron ore accounting for the largest solid bulk turnover per year, totaling 1.4 billion metric tons by sea in 2016, mainly from Australia (57%) and Brazil (26%) to China (71%) [1].Brazil is the second largest iron ore exporter and has approximately sinter plants crusher. Star crusher A,sinter crusher,steel plant equipment KUNG. Find Details about Star crusher A,sinter crusher,steel plant equipment from Taiwan Stone Crushingsinter plants crusher
احصل على السعر
Sintering plant at a glance PPT SlideShare
5. 5 Material flow Diagram Sintering Plant Flux Hammer Crusher Flux Screen +3mm Stock Bin & proportioning section Iron Ore Fines -3mm Coke breeze from C O PMD Hot Sinter return -5mm Cold Sinter return Cold Sinter return Coke return from B F -25mm -3mm Fuel Storage Coke crusher Sinter M/c Hot screen SLC Cold screen Sinter 2.1 G Index of Sinter Base Mix. G index of sinter base mix was carried out using expressions considered from the research paper published by Crores et al. [].G index of sinter mix was carried out by varying the washed ore addition from 0 to 55% in the sinter base mix by preplacing the iron ore fines of − 10 mm size.Influence of Iron Ore Sinter Base Mix Fines (− 0.150 mm) Size on
احصل على السعر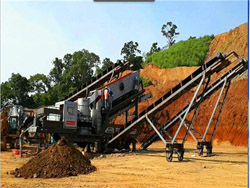
Calcium Ferrit Generation During Iron Ore Sintering —
Iron ore sintering is a heat treatment process for agglomerating fine particles into larger lumps, which then serve as the major burden for blast furnace. The production of high-quality sinter is critical for efficient blast furnace operation [ 1 3 ].
احصل على السعر