
Working principle and characteristics of cement mill
working principle: When the cylinder of the cement mill / raw material mill is driven to rotate by the transmission device, the grinding body is attached to the lining surface of The paper presents an overview of the current methodology and practice in modeling and control of the grinding process in (PDF) Grinding in Ball Mills: Modeling and Process Control
احصل على السعر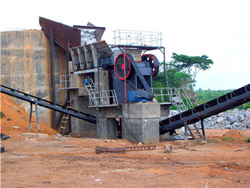
Cement Extraction, Processing, Manufacturing Britannica
Blending A first approximation of the chemical composition required for a particular cement is obtained by selective quarrying and control of the raw material fed to the crushing and Grinding is an essential operation in cement production given that it permits to obtain fine powder which reacts quickly with water, sets in few hours and hardens over a period of weeks....Overview of cement grinding: fundamentals, additives,
احصل على السعر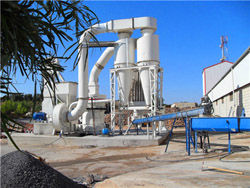
Cement
A cement is a binder, a chemical substance used for construction that sets, hardens, and adheres to other materials to bind them together. Cement is seldom used on its own, but rather to bind sand and gravel together.The process model considered in this study is based on first principles which did not exhibit the process dynamics of the real-time scenario. A hybrid model was Predictive Controller Design for a Cement Ball Mill Grinding
احصل على السعر
A Contribution towards a More Sustainable Cement:
In the present study, Portland type cement was prepared in laboratory-scale by Greek Wet Fly Ash and Mill Scales, as well as conventional raw materials such as limestone, shale and lava. The principle in the development of each model is to establish mass balance or energy . Mill. Cement and Concrete Research, V ol. 33, 2003, 439-445. 16. D i n g, B. C. Modern Predictive Control.(PDF) Grinding in Ball Mills: Modeling and Process
احصل على السعر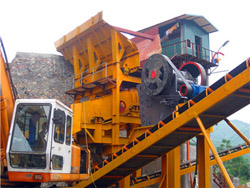
EVERY COMPONENT OF BALL MILL DETAILED
1.Axial/radial runout. 2.Alignment of the drive trains. 3.Uneven power splitting. 4.Centre distances variable. 5.Face load distribution. 6.Sealing of the girth gear. 7.Girth gear is through hardened only, fatigue strength is and vertical roller mill i.e., VRM [3–5]. Among these devices, VRM plays an important role in cement, accounting for more than 55% of China’s cement raw meal market [6], and its performance directly affects the cost of producing cement. VRM has the functions of grinding and powder selection, including a grinding unit and an air classifierRoller Mill Based on Experimental Method
احصل على السعر
Cements ground in the vertical roller mill fulfil the quality
This study investigated a mathematical model for an industrial-scale vertical roller mill(VRM) at the Ilam Cement Plant in Iran. The model was calibrated using the initial survey's data, and theThe cement manufacturing process involves the extraction and processing of raw materials, such as limestone, clay, and shale, which are then heated in a kiln at high temperatures to form clinkerCement Manufacturing Process and Its Environmental Impact
احصل على السعر
VRM Presentation PDF Mill (Grinding) Cement Scribd
VRM Working principle Vertical roller mill Feed size: f (Roller ) Material bed Feed material Max Particle size in feed: 5-8 % of roller diameter Grinding force = Roller weight + (pressure) Force Table moves with drive Roller rolls freely with table VRM Material Flow inside Gas & Product Material Feed Material Separator Rejects Internal Circulation Large Material falls Vertical Roller Mill. Vertical roller mills (VRM) are a type of mainstream clinker grinding equipment in the cement manufacturing process. Vertical roller mills are still newish cement mills since their history in cement production is no more than 20 years, but they have already become the standard cement equipment in many regions and are getting more Cement Mill for Sale Buy Cement Ball Mill & Vertical Roller Mill
احصل على السعر
Cement Milll Separator Cyclone Air Separator in Cement Plant
Product Name: cement mill cyclone air separators. Capacity: 10 250 TPD. Condition: brand new. Airflow: 16000 240000 m3/h. SEND INQUIRY. Cement mill separator, or cement separator, is a type of equipment that was widely used in the cement grinding system and raw mill system of cement plants. The function of the separator is to Cement Vertical Mill Structure: The vertical mill consists of a separator rotation system, a separator part, and an upper casing part upper casing with an inspection door and a feed port, a roller device, a transmission device, a tie rod portion, a disc seal, an upper and lower side, a side friction ring, and an unloading material ring, grinding disc adjusting device, Cement Vertical Mill for sale cementmillequipment
احصل على السعر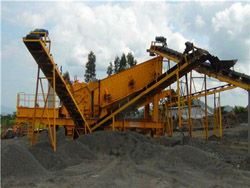
Ball Mill an overview ScienceDirect Topics
The working principle is that cement is removed from the mill before over-grinding has taken place. The cement is then separated into a fine fraction, which meets finished product requirements, and a coarse fraction which is returned to mill inlet. Recirculation factor, that is, the ratio of mill throughput to fresh feed is up to three.Feeding Size: ≤25mm. get price! Ball mills, also known as tube mills, are widely used in cement, silicate products, new building materials, refractory materials, fertilizers, black and non-ferrous metal dressings, and glass Cement Ball Mill Ball Mill For Sale Cement Mill 15
احصل على السعر
polysius® booster mill
Bead mill working principle for dry cement grinding. One crucial characteristic of this mill is the high energy density, 10-20 times higher than of a ball mill, and the resulting very compact design. The bead-stirring elements on the shaft inside the fixed shell reach a tip speed of 5 times the critical speed.Ball mill for cement grinding 3 Cement grinding taking on the tough tasks Cement ball mills have to achieve the desired grinding fineness with maximum grinding e ciency and minimal wear and tear. It’s a tough job when you consider the operating conditions of the mill but our equipment is built to last. Hard wearing kitBall mill Superior cement quality, More fl exibility, higher
احصل على السعر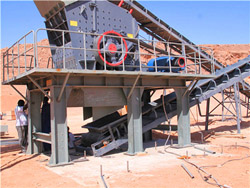
Vertical Roller Mill Operation in Cement Plant
The cement rotary kiln. When operating the vertical roller mill, the operator must control the inlet and outlet air valves to make the air volume of the system in a balanced state, so as not to affect the air pressure at the back end of the rotary kiln. We are AGICO, a professional cement equipment manufacturer and cement plant contractor.Introduction Cement is manufactured by heating a mixture of ground limestone and other minerals containing silica, alumina, and iron up to around 1450 C in a rotary kiln. At this temperature, theCement Finish Milling (Part 1: Introduction & History)
احصل على السعر
Cement Cyclone Separator In Cement Plant Factory Price
Cement separator, also known as cement mill separator, cement classifier, is widely applied to the coal mill in cement plant, raw mill, and cement milling system. It can be usually divided into three types: separation separator, centrifugal air separator, and cyclone separator. AGICO CEMENT combines foreign high-quality powder selecting technology, Cement Mill Compressor Room Raw Mill Boiler Turbine AFR Hopper RM bag filter 1.2 DEMAND: Energy demand is mainly classified into two types as shown in Fig 1: 1. Non value added process 2. Value added process Energy Management for Compressed Air in Cement Industry using Lean PrincipleEnergy Management for Compressed Air in Cement Industry
احصل على السعر
VRM THE LATEST TECHNOLOGY Bashundhara Cement
Vertical Roller Mill (VRM) is the most advanced technology in cement production procedure. Bashundhara Cement has adopted VRM from LOESCHE, Germany in both the factories to ensure the best quality. With higher fineness achieved with VRM, it creates stronger and better quality concrete and thus, proves its superiority over other cement brand.Grinding occurs at the beginning and the end of the cement making process. Approximately 1.5 tonnes of raw materials are required to produce 1 tonne of finished cement. The electrical energy consumed in the cement making process is in order of 110 kWh/tonne and about 30% of which is used for the raw materials preparation and Cement grinding optimisation ScienceDirect
احصل على السعر
Ventilation Prediction for an Industrial Cement Raw Ball Mill by
1. Introduction. In the cement industry, grinding is one of the most consuming energy stages in the production units. Around 65% of the total used electrical energy in a cement plant has to be utilized to grind raw materials, coal, and clinker [1,2].Through the process, many variables can affect the efficiency and productivity of
احصل على السعر