
Research into the crushing and grinding processes of iron ore with
Abstract. Main properties of the processes of iron ore destruction in terms of its simultaneous effect by mechanical load and electric field of ultra-high frequency have Dina Klymenko Abstract and Figures Main properties of the processes of iron ore destruction in terms of its simultaneous effect by mechanical load and electric field of ultra-high frequency...(PDF) Research into the crushing and grinding
احصل على السعر
Reduction of Fragment Size from Mining to Mineral Processing: A
5 Citations Explore all metrics Cite this article Abstract The worldwide mining industry consumes a vast amount of energy in reduction of fragment size from Introduction Hematite and magnetite are the most prominent iron ores. Most of the high-grade hematite iron ores (direct shipping ore (DSO)) are subjected to Developments in iron ore comminution and classification
احصل على السعر
Transforming iron ore processing ScienceDirect
The new circuit would eliminate secondary to tertiary crushing, desliming stages, complex flotation circuits, product thickening and the flotation reagent plant. The conventional routes for making iron and steel require that the ore be upgraded through a series of physical separation processes in sequence. The unit STRATEGIES FOR PROCESSING LOW-GRADE IRON ORE MINERALS
احصل على السعر
Comparing strategies for grinding itabirite iron ores in
Typical lower grade iron ores are represented by itabirites, which are metamorphic banded-iron formations (Hagemann et al., 2016), and consist basically of PDF On Jan 1, 2021, Yingchun Yang and others published Different Effects of Wet and Dry Grinding on the Activation of Iron Ore Tailings Find, read and cite all the research you Different Effects of Wet and Dry Grinding on the Activation of Iron
احصل على السعر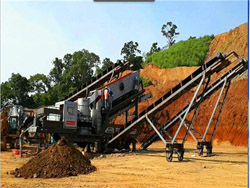
Development of a Novel Grinding Process to Iron Ore
The grinding tests were performed feeding a blend of 80% ore A (compact and harder) and 20% ore B (porous and brittle). The variable parameters ore. Hard ores, including some copper, gold, iron, and molybdenum ores, may require as much as a tertiary crushing. Softer ores, such as some uranium, bauxite, and titanium/zirconium ores, require little or no crushing. Final comminution of both hard and soft ores is often accomplished by grinding11.24 Metallic Minerals Processing US EPA
احصل على السعر
Transforming iron ore processing ScienceDirect
Much of the remaining iron ore resources in Brazil consist of low-grade itabirite ores. Accordingly, a typical beneficiation circuit includes a four-staged crushing/screening plant, followed by grinding in a closed-circuit ball mill, desliming in hydrocyclones and final ore mineral concentration via multistage reverse flotation and Abstract. Sintering is the most economic and widely used agglomeration process to prepare iron ore fines for blast furnace use. In this chapter, the sintering process is first described to identify the key steps of the process, that is, granulation and thermal densification. Discussion is then focused on the effect of the chemical, physicalIron ore sintering ScienceDirect
احصل على السعر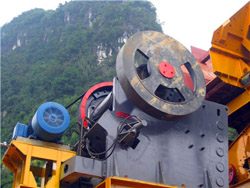
Energy and Environmental Profile of the U.S. Mining Industry 4
The most important iron ore-forming minerals are: • Magnetite Magnetite (Fe3O4) forms magnetic black iron ore. There are large deposits of magnetite in Russia and Sweden. • Hematite Hematite (Fe2O3) is a red iron ore. Hematite occurs in almost all forms, from solid rock to loose earth. It is the most plentiful iron ore and occurs inof the processed ore shipped to the iron and steel industry is in the form of pellets. Other forms of processed ore include sinter and briquettes. The average iron content of pellets is 63 percent. 11.23.2 Process Description2-5,41 Processing of taconite consists of crushing and grinding the ore to liberate iron-bearing particles,11.23 Taconite Ore Processing
احصل على السعر
Processes for Beneficiation of Iron Ores IspatGuru
Iron ores normally fall within one of the three categories namely (i) direct shipping, or high grade ores, which contain enough iron to be charged to the iron making furnace directly and may only require crushing, screening, and blending, (ii) associated low grade merchant ores which occur around the high grade ores that can be mined The crushing process of iron ore typically involves three stages: primary, secondary, and tertiary crushing. Each stage of crushing reduces the size of the ore particles, making it easier toHow iron ore is crushed? LinkedIn
احصل على السعر
Ore Pretreatment Methods for Grinding: Journey and Prospects
focused on copper ore, bauxite, coal, iron ore, sphalerite, ilmenite, e t c .T h es a m p l es i z es t u d i e dv aried between 10 and 250 g for − 10 mm particle sizes.Crushing is the process of size reduction of ore. Size reduction process begins with usage of explosives at the area for production of ore. In later stages, the size reduction process performed with crushers before grinding in mills is called "crushing". Although there is no limit set, the downsizing process over 3 mm is considered as "crushingWhat Is The Crushing Process MEKA
احصل على السعر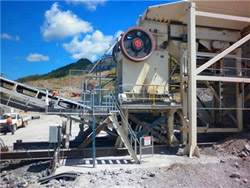
(PDF) SIZE REDUCTION BY CRUSHING METHODS ResearchGate
The process "Comminution" involves size reduction and size-wise classification called as screening or separation. The objective of this report is to provide the details of size reduction methodsUnderstanding and optimizing the comminution process in terms of mineral liberation, fragmentation, and fracture energy are aligned with sustainable approaches and overall international goals of(PDF) Comminution a Heart of Mineral Processing
احصل على السعر
11.24 Metallic Minerals Processing US EPA
ore. Hard ores, including some copper, gold, iron, and molybdenum ores, may require as much as a tertiary crushing. Softer ores, such as some uranium, bauxite, and titanium/zirconium ores, require little or no crushing. Final comminution of both hard and soft ores is often accomplished by grindingIron Ore Crushing Process Conveyor Drawing. Iron ore crushing and screening system. Iron ore crushing plant is a stepped crushing process crushing block raw material from about 500mm to fine material Get Price tertiary crushing of iron ore Cheshire homes. tertiary crushing of iron ore asmtrustorgin the process of primary and secondary Tertiary Crushing Of Iron Ore
احصل على السعر
Nuclear fuel cycle' Extractingg uranium from its ores
Crushing and grinding; Leaching; Solid-liquid separation and washing; Solvent extraction or ion-exchange, Yellow-cake precipitation and drying. The run-of-mine ore, which in some instances may be 25cm or more in diameter, is crushed and then ground to the consistency of fine sand. Since most ores being processed today contain from about 0.02%The first step of physical beneficiation is crushing and grinding the iron ore to its liberation size, the maximum size where individual particles of gangue are separated from the iron minerals. A flow sheet of a typical iron ore crushing and grinding circuit is shown in Figure 1.2.2 (based on Ref. [4]).This type of flow sheet is usually followed when the crude ore Crushing Circuit an overview ScienceDirect Topics
احصل على السعر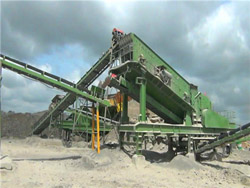
Comparing strategies for grinding itabirite iron ores in
Much of the remaining iron ore resources in Brazil consist of low-grade itabirite ores. Accordingly, a typical beneficiation circuit includes a four-staged crushing/screening plant, followed by grinding in a closed-circuit ball mill, desliming in hydrocyclones and final ore mineral concentration via multistage reverse flotation and Iron ore beneficiation can be brought about through three approaches, namely, selective dissolution, microbially induced flotation, and selective flocculation–dispersion. The bioprocesses are specially suited to treat fines, slimes, and waste tailings. 4. Potential applications include.Ore Beneficiation an overview ScienceDirect Topics
احصل على السعر
Why is there a need to crush iron ore bearing rock? LinkedIn
The reasons for crushing the ore-bearing rock include: Size Reduction: Iron ore typically exists in large, hard and unwieldy chunks. Crushing the ore helps reduce it to a size that can be more22.1 Introduction. The iron ore production was about 2611 million metric tons in the world in the year 2010 [1]. Assume that (1) the iron ore production is kept 2611 million tons every year, (2) the price of final iron ore product is 75 US$ per ton, and (3) the ore recovery in the mining process is 85%. Under these conditions, the total oreIron Ore an overview ScienceDirect Topics
احصل على السعر
Grinding down energy consumption in comminution
It accounts for around 53% of mine energy consumption which equates to at least 10% of production costs. In comparison, leaching and absorption, the next biggest energy consumers, take up 22%
احصل على السعر