
Ball milling A green and sustainable technique for the
Ball milling is a mechanical technique used to grind powders into fine particles [1]. Generally, a ball mill consists of a hollow cylindrical vessel that rotates Introduction Tungsten (W) and its alloys are promising candidates for high-temperature applications because of their high melting point, high mechanical Influence of ball milling processing on the microstructure
احصل على السعر
Ball milling: a green technology for the preparation and
Abstract. Ball milling is a simple, fast, cost-effective green technology with enormous potential. One of the most interesting applications of this technology in the field of Nanotechnology-enhanced metals and alloys for orthopedic implants. Lei Yang, in Nanotechnology-Enhanced Orthopedic Materials, 2015. 2.1.2 High-energy ball milling. High-energy ball milling is a mechanical deformation process that is frequently used for producing nanocrystalline metals or alloys in powder form. This technique belongs to the High-Energy Ball Milling an overview ScienceDirect Topics
احصل على السعر
Ball milling A green and sustainable technique for the preparation
Reviews are available on acid leaching of ilmenite [[48], [49], [50]] but to our knowledge, a review on mechanical activation applied along with the other treatment techniques is not available.Ball milling is used as a preliminary technique performed before main techniques. Mechanical activation by ball milling is known to increase the reactivity A rotary ball mill is an efficient abrasive equipment that can be used for grinding, mixing, and dispersing various materials. It usually consists of a rotating cylinder and spherical abrasives. The material is placed in the Rotary Ball Mill Rotary Ball Mill Design And
احصل على السعر
Lattice deformation of LiNi0.5Mn1.5O4 spinel cathode for Li-ion
Fig. 1 shows HR-TEM images of the starting LNMO powder and the 6BM and 120BM milled powders. The starting LNMO powder synthesized by heating at high temperatures formed an agglomerate consisting of fine particles (∼100 nm) with sharp edges (Fig. 1 a).The specific surface area of this powder was 5.2 m 2 g −1, A ball mill is a type of grinder widely utilized in the process of mechanochemical catalytic degradation. It consists of one or more rotating cylinders partially filled with grinding balls (made(PDF) Grinding in Ball Mills: Modeling and Process Control
احصل على السعر
Ball milling process variables optimization for high-entropy alloy
The increase in lattice parameters at the early stages of milling may be a result of severe plastic deformation, which increases the strain in the system. The saturated lattice parameter, 0.2884 nm, is close to 0.2878 nm [67] and 0.2873 nm [68] reported for BCC AlCoCrFe HEA, but lower than the theoretical value predicted by Eq. 2 (0.3023 nm).Ball mill is mainly made up of feeding part, discharging part, rotary part and driving part, including reducer, small drive gear, electrical machine and electronic control. The hollow shaft adopts steel casting, and its inner lining is detachable and changeable while the rotary rack wheel uses casting gear hobbing and there is a wear-resistingBall Mill-Ball Mills-Henan Hongke Heavy Machinery Co., Ltd.
احصل على السعر
Leaching of Silver from Mechanically Activated Naumannite
In this paper, the structure, morphology, chemical composition and leaching of naumannite (Ag2Se) were studied. Mechanical activation of Ag2Se in a planetary ball mill resulted in increasing its specific surface area. The influence of milling time on the particle size was studied by particle size distribution analysis and scanning electron microscopy. The ball mill Ball milling is a mechanical technique widely used to grind powders into ne particles and blend materials.18 Being an environmentally-friendly, cost-effective technique, it has found wide application in industry all over the world. Since this mini-review mainly focuses on the conditions applied for the prep-Ball milling: a green technology for the preparation and
احصل على السعر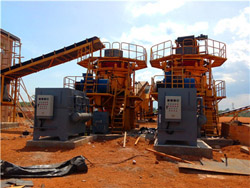
Gangue Mineral an overview ScienceDirect Topics
The three most common iron ore minerals are magnetite, hematite (the spelling “hematite” is preferred here over “haematite”), and goethite, which together account for an estimated > 99% of the iron minerals contained in world seaborne-traded iron ores in 2012. Table 2.1. Common iron ore and gangue mineral definitions. Empty Cell.The ball mill and grinding balls were cleaned for rock/mineral comminution experiments by washing with 5% decon solution, rinsing with deionized water and drying, milling 10 g of rock for 10 minMechanochemical processing of silicate rocks to trap CO 2 Nature
احصل على السعر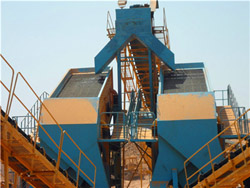
Cement Ball Mill Operation Ball Mill For Sale
Cement Ball Mill Operation is an essential process in the cement manufacturing industry. It involves grinding clinker, gypsum, and other materials into a fine powder to create cement. The operation of the Types: Mining ball mills are divided into two categories, Overflow ball mills: center discharge ball mills; Lattice type ball mills: Peripheral row ore type ball mills. Batch small ball mill: Diamond Mining Process; Ball Mill Mining Grinding Mill Mineral Processing
احصل على السعر
Ball Mill (Ball Mills Explained) saVRee saVRee
Crushed ore is fed to the ball mill through the inlet; a scoop (small screw conveyor) ensures the feed is constant. For both wet and dry ball mills, the ball mill is charged to approximately 33% with balls (range 30-45%). Pulp (crushed ore and water) fills another 15% of the drum’s volume so that the total volume of the drum is 50% charged.The XMQL420*450 ball Mill is mainly composed of 420×450 lattice ball mill, 150×1200 spiral classifier, 35 liter pendulum feeder and 90×600 screw conveyor, which can form continuous cutting and grinding work.The equipment install the Small Laboratory Milling Machine Grate Lattice Ball Mill for
احصل على السعر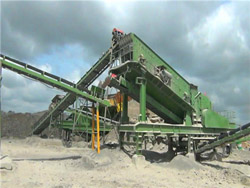
Grinding Media in Ball Mills-A Review Preprints
Review Grinding Media in Ball Mills-A Review Nyasha Matsanga 1,*, Willie Nheta 1 and Ngonidzashe Chimwani 2 1 Mineral Processing and Technology Research Centre, Department of Metallurgy, University of Johannesburg, P.O.BOX 17011, Doornfontein 2028, South Africa; [email protected] 2 Department of Mining Engineering, The grinding process in ball mills is notoriously known to be highly inefficient: only 1 to 2% of the inputted electrical energy serves for creating new surfaces. There is therefore obvious room for improvement, even considering that the dominant impact mechanism in tumbling mills is a fundamental liability limiting the efficiency.Reducing the energy footprint of grinding circuits: the process
احصل على السعر
Process flow diagram of the primary ROM ball milling circuit.
A fuzzy controller was designed for the control flow rate inside the ball mill to avoid overfilling or emptying the mill [34]. The fuzzy system was used to optimize the ball milling circuit [35] .High Efficiency Small Mini Lab Grate Ball Mill Lattice-type Ball Mill For Gold Mineral Grid Ball Ltd. is an over 30 years professional manufacturer and exporter of mining machinery for crushing Pre-sales service: We provide you with the prophase plan, process flow design and manufacturer equipment according to your specialHigh Efficiency Small Mini Lab Grate Ball Mill Lattice-type Ball Mill
احصل على السعر
Ball Grinding Process SpringerLink
Ball grinding process is a grinding method of crushing ore with ball-shaped grinding medium in the grinding mill. In the ball grinding process, because the steel ball has 360° free rotation, it is suitable for falling motion and throwing motion. When the rotating speed of the cylinder is low, the medium rises to a certain height along the
احصل على السعر