
Wet ball milling of niobium by using ethanol, determination
4 Citations Metrics Abstract This study investigates the effect of using ethanol as the process control agent during the wet ball milling of niobium (Nb). Dried A comparative study on wet and dry mechanical ball milling of sawdust biochar showed that ball milling of biochar with water resulted in smaller and more Ball milling as a mechanochemical technology for
احصل على السعر
Influence of dry and wet ball milling on dispersion characteristics of
Dry and wet ball milling approaches are compared on dispersibility of CNT nanofluid. Grinding is effective method for reducing the agglomerated particle size of Wet and dry grinding of coal in a laboratory-scale ball mill: Particle-size distributions ScienceDirect Article preview Abstract Introduction Section snippets Wet and dry grinding of coal in a laboratory-scale ball mill: Particle
احصل على السعر
Comparative Study on Improving the Ball Mill Process
Taguchi-based experimental design technique provides a systematic and efficient mathematical approach to understand complex process of ball mill process The effects of high energy milling on the shape, size and low temperature sinterability of plate-like alumina powder was studied. The milling effects were studied Effect of high energy ball milling and low temperature
احصل على السعر
Ball Milling in Organic Synthesis: Solutions and Challanges
For most applications in organic synthesis, including catalysis, ceramic materials (e.g. ZrO 2) are the best choice. They are chemically inert and the material Yuan et al. (2020) showed that wet ball milling for 12 h was more effective in obtaining smaller particle size and more evenly distributed biochar than dry ball milling, Effects of wet and dry ball milling on the ResearchGate
احصل على السعر
Wet Milling vs Dry Milling: The Differences,
Now that we have a basic understanding of the industrial milling process, let’s examine the difference between wet milling and dry milling. Dry milling typically uses particle-on-particle contact to reduce Mechanochemical technique aims to strike a balance between defect formation via ball milling and size adjustment of a solid grain to nanoscale (<1000 nm) (Ullah et al., 2014).During the process, a high-energy mill is employed and a specific powder charge is placed along with a milling medium (Lin et al., 2017).The kinetic energy Ball milling as a mechanochemical technology for
احصل على السعر
(PDF) Grinding in Ball Mills: Modeling and Process
A ball mill is a type of grinder widely utilized in the process of mechanochemical catalytic degradation. It consists of one or more rotating cylinders partially filled with grinding balls (madeThe ball mill process parameters discussed in this study are ball to powder weight ratio, ball mill working capacity and ball mill speed. As Taguchi array, also known as orthogonal array design, adds a new dimension to conventional experimental design, therefore, Orthogonal array (L9) was carefully chosen for experimental design to Comparative Study on Improving the Ball Mill Process
احصل على السعر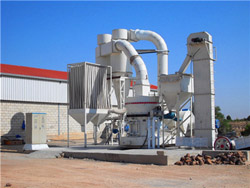
(PDF) Ball milling : A green technology for the preparation
a) Schematic representation of a ball mill (horizontal section); (b) different types of instruments (this figure has been adapted from ref. 19 with permission from Royal Society of Chemistry).The major difference between wet and dry process is the mix preparation method before burning clinker in the kiln. The energy efficiency of dry ball-mill grinding of cement depends on factors such as ball charge fill-ratio, mill length/diameter ratio, size distribution of the ball charge, operating conditions of the air separators, air flowA Review on Pyroprocessing Techniques for Selected Wastes
احصل على السعر
Dry Production Methods ScienceDirect
Embedded Fe–C alloy NPs with an average size of 50 nm were obtained by ball milling using preheated steel cut chips [24].Pd NPs with an average size of 5.5 nm have been obtained using a commercial planetary ball mill system [25].Note that the starting material consists of 400 μm Pd particles.In terms of small sizes and monodispersity, this Ball milling technique, using mechanical alloying and mechanical milling approaches were proposed to the word wide in the 8th decade of the last century for preparing a wide spectrum of powder materials and their alloys. In fact, ball milling process is not new and dates back to more than 150 years. It has been used in size comminutions of ore, Ball Milling an overview ScienceDirect Topics
احصل على السعر
What Are the Differences between Dry and Wet Type Ball Mill?
The water can wash away the fine particles in time to avoid over-grinding. The wet ball mill has a low noise, and low environmental pollution. The wet ball mill has a simple transportation device with less auxiliary equipment, so the investment is about 5%-10% lower than that of a dry ball mill. The grinding particle size is fine and uniform.The process uses a ball mill, a cylindrical chamber with a grinding medium such as balls that rotates on its axis to achieve the desired fineness of the final product [9,75]. The grinding media crash into the particles, reducing their size and creating a more consistent blend [ 76,77 ].Producing Metal Powder from Machining Chips Using Ball Milling Process
احصل على السعر
Dry grinding in planetary ball mills: Evaluation of a stressing
The optimum process parameters setting concluded that balls to powder weight ratio are 20:1, the optimum ball mill working capacity is 2 L while the optimum speed of the ball mill is 105 rpm.Section snippets Experimental set-up. The dry grinding of alumina was performed in a planetary ball mill PM400 (Retsch GmbH) with a sun wheel radius R SUN of 150 mm and a gear ratio of k = −2. The gear ratio is defined as relative rotational speed of grinding chamber n GC in relation to the rotational speed of the sun disc n SUN: k = n Dry grinding in planetary ball mills: Evaluation of a stressing
احصل على السعر
Comparison of Wet and Dry Grinding in
Comparison of dry and wet grinding process in an electromagnetic mill is presented in this paper. The research was conducted in a batch copper ore grinding. Batch mode allows for precise The optimization of processing plants is one of the main concerns in the mining industry, since the comminution stage, a fundamental operation, accounts for up to 70% of total energy consumption. The aim of this study was to determine the effects that ball size and mill speed exert on the milling kinetics over a wide range of particle sizes. This Kinetics of Dry-Batch Grinding in a Laboratory-Scale Ball Mill
احصل على السعر
Comparison of Wet and Dry Grinding in Electromagnetic Mill
Comparison of dry and wet grinding process in an electromagnetic mill is presented in this paper. The research was conducted in a batch copper ore grinding. Batch mode allows for precise parametrization and constant repetitive conditions of the experiments. The following key aspects were tested: processing time, feed size, size of The mill used was the Quadro Comil, a conical screen mill for uniform size reduction and de-agglomeration (Fig. 1), which can be used for wet or dry milling. The infeed product is introduced into the conical screen chamber (cone mill) and the rotating impeller imparts a vortex flow pattern to the incoming material.Comparison of wet milling and dry milling routes for
احصل على السعر
~mill2022/sbm: sbm formulations wet mtw grinding mills
sbm/sbm formulations wet mtw grinding mills.md -rw-r--r-- 34.7 KiB . View; Log; Blame; View raw; 40cddf99 — mill2022 sbm a month agoA ball mill is a grinder which is used to grind, blend and mix materials like chemicals, ores, pyrotechnics, paints, mineral dressing process, paint and ceramic raw materials. Its working principle is impact and attrition. Ball milling have proved to be effective in increasing solid-state chemical reactivity and production of amorphous materials.Wet Ball Milling Vs Dry Ball Milling Orbis Machinery
احصل على السعر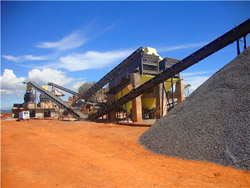
Milling tests with the Fritsch Planetary Ball Mill fritsch.de
The Planetary Mill PULVERISETTE 5 premium line provides two stations of grinding bowls with 500 ml volume (largest capacity on the market). Each grinding bowl can be filled 1/3 part of the volume (± 170 gr sample). So, if we use two grinding bowls, the optimum capacity is about 170 x 2 = 340 g per milling process. 3.Grinding in Ball Mills: Modeling and Process Control. Vladimir Monov, Blagoy Sokolov and. Stefan Stoenchev. Published Online: 16 Mar 2013. Volume & Issue: Volume 12 (2012) Issue 2 (June 2012) Page range: 51 68.Grinding in Ball Mills: Modeling and Process Control Sciendo
احصل على السعر