
A comparative study on the effects of dry and wet grinding
Dry grinding produces rougher surfaces (mechanically activated centers) and more agglomerated particles than wet grinding. On the other hand, the greater High-Performance Dry Grinding, Table 1 Advantages and disadvantages of high-performance grinding according to VDI 3411 and Kopac and Krajnik Full size table High-Performance Dry Grinding SpringerLink
احصل على السعر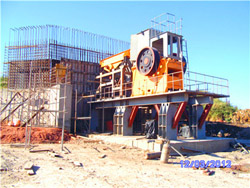
Comparison of Wet and Dry Grinding in
Only in case of the shortest processing time, equal to 5 s, are the dry grinding results better . This is most likely due to higher third of the slurry. So the grinding efficiency of wet grinding can surpass that of dry grinding by some 20-25%. But the lining and grinding media wear may well WET GRINDING AND DRYING-GRINDING OPERATIONS
احصل على السعر
Grinding SpringerLink
Long-duration dry grinding results in cold-welding and pelletizing of fine particles, whereas the slowing-down phenomenon usually happens relatively quickly. This manuscript compiles various effects of dry grinding on flotation and compares them with wet grinding. Dry grinding consumes higher energy and produces A comparative study on the effects of dry and wet grinding
احصل على السعر
(PDF) Different Effects of Wet and Dry Grinding on the Activation of
The dry grinding method produces higher NaCl percent and whiteness than the wet grinding method. However, the wet grinding method was better in water The 3C-SiC nanopowder obtained by dry grinding of the formed free nanoporous layer (see Section 11.2) was directly dispersed in a Krebs buffer solution.The formed suspension Dry Grinding an overview ScienceDirect Topics
احصل على السعر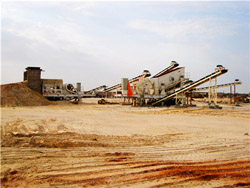
A comparative study on the effects of dry and wet grinding
Deniz et al. [34] and Bu et al. [35] studied the effect of wet and dry grinding of coal and observed that the wet grinding method is a more efficient methodology for the fine grinding of materials.Stirred Mills Ultrafine Grinding. In Mineral Processing Design and Operations (Second Edition), 2016. 10.2.4 Operation of Vertical Mills. Vertical stirred mills are usually charged with media occupying 80% of the mill volume which is in sharp contrast to tumbling mills that are seldom charged more than 40% of their volumes to allow space for the tumbling Stirred Mill an overview ScienceDirect Topics
احصل على السعر
Key issues and challenges in spice grinding ScienceDirect
Grinding is an age-old technique of particle size reduction to produce powders that can be used as intermediate or end products. Grinding aims to reduce the size of the particle by mechanical means such as impact, compression, shear, and cutting (Sahay and Singh, 1996).Hammer mill, plate mill, ball mill, pin mill, roller mill are Lower operating temperatures are achieved by the liquid slurry, which dissipates heat from the mill since it has a far greater heat capacity than the solid. The disadvantages of dry-micronization are avoided by wet-milling. Dry-micronization frequently adds disorder into the milled crystalline API, primarily in the form of amorphous material.A comparative study of Dry milling vs Wet milling Senieer
احصل على السعر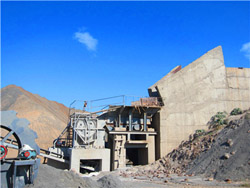
Control of a closed dry grinding circuit with ball mills using
It is based on the reduction of solids by impact, friction, compression, and abrasion forces. The two main advantages of using grinding are uniformity and increased surface area ratio of solids, which enables and improves the performance of post-grinding operations (Chen et al., 2009; Petrakis and Komnitsas, 2019; Ramasamy et al., 2005).High-Performance Dry Grinding, Table 1 Advantages and disadvantages of high-performance grinding according to VDI 3411 and Kopac and Krajnik . Full size table. The grinding process is generally connected with high heat generation during chip formation, which needs to be dissipated. Cutting without cutting fluid i.e., without lubrication orHigh-Performance Dry Grinding SpringerLink
احصل على السعر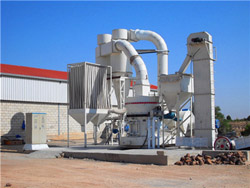
(PDF) A comprehensive review on the grinding process:
A comprehensive review on the grinding process: Advancements, applications and challenges. ARCHIVE Proceedings of the Institution of Mechanical Engineers Part C Journal of Mechanical Engineering2. Starch in cereal grains. Cereal grains are rich in starch ranging from 40% in oats up to 80% of dry matter in rice, with the variation in starch content dependent on variety, climatic conditions, and agronomic practices [].Starch is synthesized into a form of rough spherical granules and, within each feed grain starch granule, multiple concentric Effects of Grain Processing with Focus on Grinding and
احصل على السعر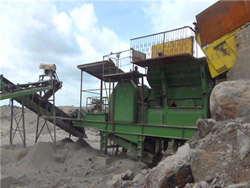
Dry Grinding ALPA Powder Equipment
Dry milling can make particles reach micron size. But if you want to achieve smaller nanometer sizes, wet grinding is the only way to achieve this goal. Greatly reduce the cost of materials. Significantly reduce power and heat consumption. Very low greenhouse gas emissions. Greatly reduce water consumption. Elimination of additional Dry grind mills can be used in conjunction with air classifiers or screeners to form a closed grinding process loop (Figure 5). By continuously classifying out fines and return-ing oversize material to the mill, such systems can very efficiently provide sharp particle-size-distribution grinds. As a rule of thumb, dry grinding generally will achieve2009 GetsNimbler Union Process
احصل على السعر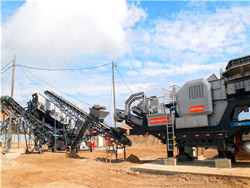
Solids Choose the Right Grinding Mill Chemical
Dry grind processing is ideal for products with particle size specifications of 2–3 microns average or larger. Dry grinding offers many potential cost savings. Advantages 1. Fast, efficient and reliable fine grinding 2. Freeze-drying is an important processing unit operation in food powder production. It offers dehydrated products with extended shelf life and high quality. Unfortunately, food quality attributes and grinding characteristics are affected significantly during the drying process due to the glass transition temperature (during drying Effect of Freeze-Drying on Quality and Grinding Process of Food Produce
احصل على السعر
(PDF) Key issues and challenges in spice grinding
Cryogenic (C2) 7.06 2 Cause Energy requirement − 1.85 6 Effect. Dry ice (C3) 3.89 Cause Grinding time − 0.21 Effect. Chilling (C4) 3.47 Cause Grinding loss − 0.25 Effect. Grinding zoneReferences (1) Cryomilling is a ball mill micronization process that is carried out at a low temperature (RETSCH, 2021). The grinding jar is cooled to ca. −196°C by liquid nitrogen supplied(PDF) A Review on Cryogenic Grinding ResearchGate
احصل على السعر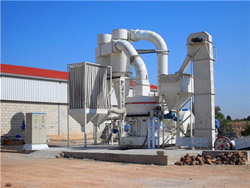
What Are the Differences between Dry and Wet Type Ball Mill?
The water can wash away the fine particles in time to avoid over-grinding. The wet ball mill has a low noise, and low environmental pollution. The wet ball mill has a simple transportation device with less auxiliary equipment, so the investment is about 5%-10% lower than that of a dry ball mill. The grinding particle size is fine and uniform.The grinding process can either be performed dry or with the aid of a solvent [140]. Multiple mechanisms of co-crystal formation using dry powder methods have been discussed [107] over the last 10 years and due to little or no solvent being used, these methods can be considered as green routes for obtaining co-crystals in high yield [141] .Grinding an overview ScienceDirect Topics
احصل على السعر
Wet Milling vs. Dry Milling in the Pharmaceutical Industry
Grinding mechanisms can vary, but particles are reduced in size either by colliding with other particles (particle-particle) or through colliding with grinding media or walls. Once the dry milling is complete, the particles exit the grinding chamber and are conveyed to product collection or a classifier, which can return larger particles to theThis corresponds to nominal ratios of length to diameter that decrease from around 1/3 for the smaller mills to less than ¼ for the larger mills. The grinding characteristics of the ores processed have varied from 2-3 Hph/lt for a 10 20 mesh grind up to 15 20 Hph/lt for a 65 mesh grind. Wet Versus Dry Primary GrindingAutogenous Grinding & Semi Autogenous Grinding Circuits
احصل على السعر
Dry Milling an overview ScienceDirect Topics
Dry milling and wet milling of cereal grains are used to produce ethanol and to partition the grains into an array of feed components (Figure 2).Wet milling is a more complex process and requires high-quality grains to produce high-value products suitable for human use. Some of the co-products, such as maize gluten meal, may be marketed in Evaluation of HPGR and VRM for dry comminution of mineral ores. A. Jankovic Ç. Ozer W. Valery K. Duffy. Engineering, Environmental Science. 2016. The mining industry is searching for more energy efficient and dry comminution equipment as an alternative to conventional crushing followed by wet grinding circuits.Evaluation of dry grinding using HPGR in closed circuit with
احصل على السعر