
Iron Ore Processing, General SpringerLink
Making iron and steel from iron ore requires a long process of mining, crushing, separating, concentrating, mixing, agglomeration (sintering and pelletizing), In India, where iron ore processing is one of the major industries, the generation of tailings is estimated to be 10-25 % of the total iron ore mined, amounting to 18 million tons per year Iron Ore Processing an overview ScienceDirect Topics
احصل على السعر
Characterization and Beneficiation of Dry Iron Ore
fine ore having size below 8 –10 mm. Dry processing of iron ore is popular for treating hard massive hematitic ores; however, fines generated during processing of Iron processing Ores, Smelting, Refining: Iron ores occur in igneous, metamorphic (transformed), or sedimentary rocks in a variety of geologic environments. Most are Iron processing Ores, Smelting, Refining Britannica
احصل على السعر
Introduction: Overview of the global iron ore industry
1.1.1. World steel and iron ore production Steel is vital to the global economy. Its unique combination of strength, formability, versatility, recyclability, and low The iron ore pelletizing process consists of three main steps: Pelletizing feed preparation and mixing: the raw material (iron ore concentrate, additives—anthracite, dolomite—and binders are prepared Iron Ore Pelletizing Process: An Overview
احصل على السعر
(PDF) Iron Ore Pelletizing Process: An Overview
PDF On Jul 11, 2018, Sandra Lúcia de Moraes and others published Iron Ore Pelletizing Process: An Overview Find, read and cite all the research you need on ResearchGate Plant capacitiesIntroduction In the beginning, there were direct shipping and smelting of iron ores. These ores were fully oxidized, consisting of high-grade hematite containing Developments in the physiochemical separation of iron ore
احصل على السعر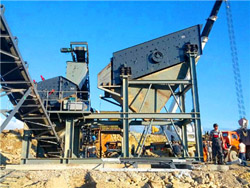
Suppression of airborne particulates in iron ore processing
Iron ore taconite pellets were obtained from a processing facility located in the Midwest United States, identified as “Plant D”. The sample, received in a 208 liter (55 gal) drum, was split into twelve 19 liter (5 gal) buckets each weighing approximately 23 kg (50 lb), using coning and splitting techniques.Iron (Fe) is a metallic element that constitutes 5.6% by weight of the Earth's crust and is the fourth most abundant element in the crust. Iron ores are rocks from which metallic iron can be economically Iron Ore Geoscience Australia
احصل على السعر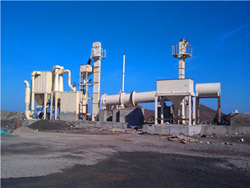
Iron ore beneficiation: an overview ScienceDirect
Yield from the plants has been generally 100% as no waste is discarded from such plants. Hence, the product grade is equivalent to the feed grade. Dry-processing flowsheet of dry plant of Joda iron ore mines, Tata Steel Ltd is depicted in Fig. 2.9. Download : Download full-size image; Figure 2.9. Dry plant process flowsheet of Joda Rio Tinto Iron ore processing plants in the Pilbara region of Western Australia do not involve any chemical treatment. Flow sheets for the Brockman 2 (8.7 MTpa) and Mount Tom Price (28 MTpa) processing plants are given in Figs. 8.4 and 8.5 (Kinnel, 2013). The flow sheets are relatively simple. Dry processing involves up to three crushing Comminution and classification technologies of iron ore
احصل على السعر
Research Progress of Intelligent Ore Blending Model
The iron and steel industry has made an important contribution to China’s economic development, and sinter accounts for 70–80% of the blast furnace feed charge. However, the average grade of domestic iron ore is low, and imported iron ore is easily affected by transportation and price. The intelligent ore blending model with an intelligent mills that utilize this process also have auxiliary operations in the form of coke and sinter/pellet plants. According to the American Iron and Steel Institute, coke is the most important raw material fed into the blast furnace (Valia, 2015). It is used to reduce iron ore to iron. High quality coal is heated in an oxygen-Cost Effectiveness Analysis of HYL and Midrex DRI
احصل على السعر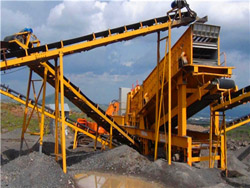
Effects of iron-ore mining and processing on metal
The study area is located in Minas Gerais State (Iron Quadrangle Region) and in Espírito Santo State, Brazil (Fig. 1), which has an extensive iron-ore mining and processing plant. Various studies have confirmed the environmental contamination by trace metals in the Iron Quadrangle (de Mello et al. 2006 ; Matschullat et al. 2000 ; Pimentel etMineral size recovery curves in spirals are calculated using data from two iron ore processing plants. • Recovery of iron carrier particles increase up to 0.2 mm and then decreases due to the Bagnold force.. The decrease of recovery for coarse silica carrier particles is more important than that of iron carrier particles.Size recovery curves of minerals in industrial spirals for processing
احصل على السعر
Characterization and Beneficiation of Dry Iron Ore Processing Plant
The generation of iron ore fines in dry processing plant of Khondbond region, India is about 30–40% of the total feed. The iron ore fine assayed 58.73% Fe (T), 5.54% Al 2 O 3, 6.6% SiO 2, and 4.37% LOI. Particle size distribution of fines showed that 50% (by weight) of material are below 1800 μm.Iron Ore Pellet Dustiness Part I: Factors Affecting Dust Generation, Mineral Processing and Extractive Metallurgy Review, 36:4, 258-266, DOI: 10.1080/08827508.2014.928876(PDF) Iron Ore Pellet Dustiness Part I: Factors ResearchGate
احصل على السعر
Iron processing Smelting, Refining, Alloying
Iron making. The primary objective of iron making is to release iron from chemical combination with oxygen, and, since the blast furnace is much the most efficient process, it receives the most attention here. Alternative Flotation of Iron Ores: A Review. A tremendous amount of research has been done on refining the flotation process for iron ore and designing the reagents which go into it. This paper reviews the industrial practices and fundamental research surrounding iron ore flotation. The advantages and disadvantages of direct flotation, cationic reverseFlotation of Iron Ores: A Review: Mineral Processing and
احصل على السعر
Iron Ore Processing, General SpringerLink
The iron ore processing industry produces usable concentrations of iron-bearing material by removing nonferrous rock (gangue) from low-grade ore. In the United States, predominant iron ore is taconite which is a hard, banded, low-grade ore. Ninety-nine percent of the crude iron ore produced in the United States is taconite.Iron ore sintering consists of heating a layer of fines until partial melting occurs and individual ore particles fuse together. For this purpose, a traveling-grate machine is used, and the burning of fine coke (known as coke breeze) within the ore generates the necessary heat. Before being delivered to the sinter machine, the ore mixture isIron processing Ores, Smelting, Refining Britannica
احصل على السعر
Iron ore sintering ScienceDirect
The sintering process begins with preparation of a sinter mixture consisting of iron ore fines, fluxes, solid fuel (called bonding agents in Japan) such as coke breeze, and return fines from the sinter plant as well as recycled ferruginous materials from downstream iron and steelmaking processes.Activities involved in finding, mining and processing iron ore at our Pilbara operations have been simplified in the following diagram. Rio Tinto operates 11 iron ore mines in the Pilbara and the specific sequence of activities varies from mine to mine. Excellence in planning, scheduling and quality control are fundamental to the process.Iron Ore production in the Pilbara Rio Tinto
احصل على السعر
Mineral Processing an overview ScienceDirect Topics
12.7 Ore to Concentrate and Metal. Mineral processing or mineral beneficiation or upgradation involves handling of three primary types of ROM ore material which has been blasted, fragmented and brought out from in situ position. These materials can be used directly or by simple or complex processing and even applying extractive metallurgy likeAluminium ore processing. We have developed a process that lowers the cost of refining bauxite to alumina by treating the waste product generated—red mud—to recover a costly ingredient, caustic soda. Dry slag granulation. Our sustainable, dry method for slag granulation derives value from waste and has the potential to transform the metalMineral processing CSIRO
احصل على السعر
Our operations Fortescue
Our Fortescue Hive is a purpose-built Integrated Operations Centre in Perth that opened in 2020 and includes our Planning, Operations and Mine Control teams, together with Port, Rail, Shipping and Marketing teams. In FY23, the Hive was expanded to include an Iron Bridge control desk. The Hive allows team members across our value
احصل على السعر