
Introduction: Overview of the global iron ore industry
This chapter first provides an overview of world iron ore production and trade, as well as reserves and resources, followed by a summary of the key mining Mineral processing can involve four general types of unit operation: comminution particle size reduction; sizing separation of particle sizes by screening or classification; concentration by taking advantage of physical and surface chemical properties; and dewatering solid/liquid separation. In all of these processes, the most important considerations are the economics of the proceMineral processing
احصل على السعر
(PDF) Effective Processing of the Iron Ores ResearchGate
Effective technology for a complex wasteless processing of the iron ores has been designed and includes three main components (plats): comminution plant, Iron ore is one of the main raw materials to make steel. About 98% of the mined iron ore is used to make steel either by the blast furnace—basic oxygen furnace Comminution and classification technologies of iron ore
احصل على السعر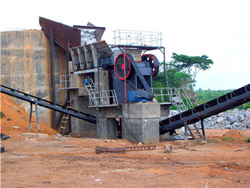
Iron Ore Processing, General SpringerLink
Iron ore sintering plants are associated with the manufacture of iron and steel, often in integrated steel mills. The sintering process is a pretreatment step in This study focussed on flowsheet simulation for mineralogical-based approach to geometallurgy of iron ores. Process unit models used were selected based on their applicability at particle level for iron ore Process simulations in mineralogy-based geometallurgy
احصل على السعر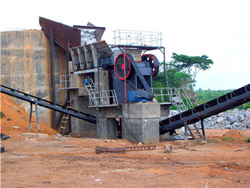
Reagents in Iron Ore Processing 19 Reagents in Mineral
This chapter deals with reagents that have been used in processing a variety of iron ores, especially low-grade types. The emphasis is on applications of various reagents for The chronological distribution of the references cited in this paper is given in Fig. 1 showing that the main reference material used in this review was published in the decade of the 1960s where there was significant research conducted in the United States on the processing of their iron ores. The author is aware of significant publications in Iron Ore Processing an overview ScienceDirect Topics
احصل على السعر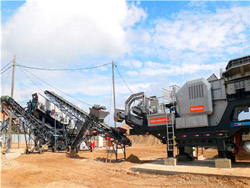
Comminution and classification technologies of iron ore
Rio Tinto iron ore processing plants. Rio Tinto Iron ore processing plants in the Pilbara region of Western Australia do not involve any chemical treatment. Flow sheets for the Brockman 2 (8.7 MTpa) and Mount Tom Price (28 MTpa) processing plants are given in Figs. 8.4 and 8.5 (Kinnel, 2013).Introduction: Ore, which contains an economical use of iron, is called an iron ore. There are many types of iron ore, magnetite (Fe3O4), hematite (Fe2O3) and (FeCO3), etc, which are mainly usedIron ore processing plant LinkedIn
احصل على السعر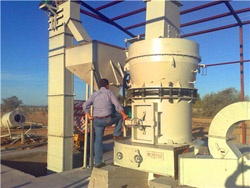
Iron (Fe) Ore Minerals, Occurrence » Geology Science
Transportation methods can include trucks, trains, or ships, depending on the location of the mine and the destination of the iron ore. Processing: At the processing plant, the iron ore concentrate may undergo further processing, such as pelletization or sintering, to create iron ore pellets or sinter, which are used in blast furnaces toOpen-pit mining is the most common method used to extract iron ore. It involves using large machines to excavate large pits in the ground. The extracted iron ore is then transported to a processing plant where it is crushed and filtered to remove impurities. Strip mining. Strip mining is another method used to mine iron ore.Iron Ore Mining The process of iron ore mining %y AtlamGroup
احصل على السعر
Iron Ore Rio Tinto
Rio Tinto Iron Ore. Our iron ore operations in the Pilbara comprise a world-class, integrated network of 17 iron ore mines, four independent port terminals, a 2,000-kilometre rail network and related infrastructure. Insights from data help us to explore and extract our iron ore efficiently. Today, we produce five iron ore products in Western Australia including the Peer-review under responsibility of Tsinghua University/ Basel Convention Regional Centre for Asia and the Pacific doi: 10.1016/j.proenv.2016.02.021 Available online at sciencedirect ScienceDirect The Tenth International Conference on Waste Management and Technology (ICWMT) An study on preparation and utilization of An Study on Preparation and Utilization of Tourmaline from Tailings
احصل على السعر
The Basics of How Ore Processing and Recovery Plants Work
Other primary metals that ore processing plants are used to recover include copper and iron ore. There are also rare metallic minerals like nickel, cobalt, and scandium which are mined usingCurrent industrial practice of processing of iron ore fines in India does not involve much beneficiation. However, few plants in India are treating fines during washing, classification, and jigging process [4]. In other parts of the world, iron ore fines are beneficiated for magnetite- and hematite-rich iron ore in * P. Dixit prashant.dixitCharacterization and Beneficiation of Dry Iron Ore Processing Plant
احصل على السعر
091102 Iron ore Climate Action
agglomerated iron ores are iron ore pellets which are used as raw material for primary iron and steel making. The stand-alone production of non-agglomerated iron ores and concentrates is not covered by the EU ETS, since the amounts of emissions are too small. The production of iron ore pellets can be described as follows: Non-agglomerated iron Cliff’s Tilden plant in Cleveland, USA, is the only iron ore beneficiation plant, where selective flocculation technique, using degraded starch as the flocculant, has been applied to produce pellet grade Existing and New Processes for Beneficiation of
احصل على السعر
Characterization and Beneficiation of Dry Iron Ore Processing Plant
During dry processing, hard massive ore results in generation of coarser fraction known as sized ore having size from 10 to 40 mm and used in blast furnace while soft goethite-rich mineral tends to generate fine fraction known as fine ore having size below 8–10 mm. Dry processing of iron ore is popular for treating hard massive hematitic Automated optical image analysis of natural and sintered iron ore. E. Donskoi, J.R. Manuel, in Iron Ore, 2015 Abstract. To evaluate an iron ore resource, develop processing routines for iron ore beneficiation, and understand the behavior of the ore during such processing, extensive mineralogical characterizations are required.For calculating Ore Beneficiation an overview ScienceDirect Topics
احصل على السعر
Advances in screening technology in the mining sector Mineral Processing
Processing plants such as those of Roy Hill are characterized by a high number of screening devices. In fact, 16 banana screens are used in that plant alone. Fig. 9 shows a 40 Mta iron ore processing plant operated by Vale in the Carajas Mine. The photo shows parallel linear vibrating screens for secondary screening.38%. Recovery rate. 74%. Manganese beneficiation machines: GZD-850×3000 vibrating feeder,PE-500×750 jaw crusher,Φ1200 cone crusher,B500x10 m belt conveyor, 2YK1535 inclined vibrating screen,Ф2700×4500 ball mill, High-strength Magnetic drum separators. 07 150 TPH Bauxite ore beneficiation plant in Indonesia. 10 Best Ore Beneficiation Plants for Sale (with Costs)
احصل على السعر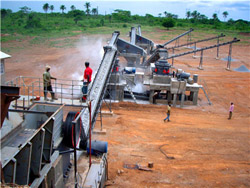
Iron ore sintering ScienceDirect
Sintering is the most economic and widely used agglomeration process to prepare iron ore fines for blast furnace use. In this chapter, the sintering process is first described to identify the key steps of the process, that is, granulation and thermal densification. Discussion is then focused on the effect of the chemical, physical, andWith 5 mines, 4 processing hubs and 2 port facilities, our Pilbara iron ore business is all connected by more than 1,000 kilometres of rail infrastructure. At each mining hub ore from the mines is crushed, beneficiated (where necessary) and blended to create high-grade hematite lump and fines products.Iron ore BHP
احصل على السعر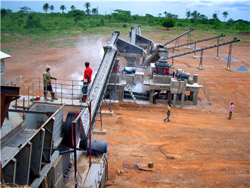
Coal Processing Methods 911 Metallurgist
Use of Coal in Iron Ore Processing Anthracite and coke breeze have been used for many years to sinter flue dust recovered at blast furnace operations. The use of magnetic taconites, which requires that the ore be ground to very fine sizes before it can be beneficiated, made necessary the development of a method to reconstitute the This new direct reduction technology uses iron ore fines instead of pellets and is therefore more energy efficient and uses cheaper ore material compared to state-of-the-art technologies. Via a collaborative research project, ENRAG developed the fundamentals of a fully transient simulation engine for the operation of a future HYFOR Hydrogen Based Direct Iron Ore Reduction Plant Simulation
احصل على السعر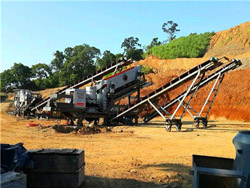
Mineral processing CSIRO
Iron ore sintering. We helped a major mining company better understand how different iron ores behave during the sintering process. This knowledge can be used to optimise processes for cost savings and productivity benefits.
احصل على السعر