
Thermodynamic Performance Analysis of a Raw Mill System in a Cement Plant
A schematic diagram of the raw mill system in a cement plant is illustrated in Fig. 1. In this process, raw materials, such as CaCO 2,SiO 2,Al 2 O 3,Fe 2 O 3,The utilization of coal in the cement and concrete industries takes three basic forms: (1) as a fuel in the production of cement clinker; (2) ash produced by Coal utilization in the cement and concrete industries
احصل على السعر
Coal Mill Systems ResearchGate
Abstract The role of vertical coal firing mills in cement plants are discussed. The potential risk of fire and even an explosion can be limited if the coal meal product is Figure 1.Schematic of raw vertical roller mill circuit in the Ilam cement plant. Table 1. Monitoring variables in the Ilam cement plant (STD: Standard deviation).Modeling of energy consumption factors for an
احصل على السعر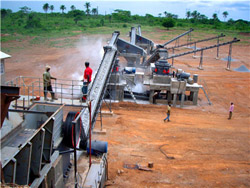
Analysis of material flow and consumption in cement
The coal mill is a vertical roller mill, in which the coal particles are collected in a bag filter through a grit separator. The required size of coal is 80% of 90 μm and less The plant processes 65 MT/h of clay, 260 MT/h of limestone and 12.5 MT/h of gypsum to produce 220 MT/h (1.75 million MT/year) of cement. View Get access to 30 million figuresFigure 1: Process Flow Diagram of the Cement Plant
احصل على السعر
Design and analysis of a cogeneration plant using heat
The proximate analysis of coal is C=47, H=3.17, O=8.7, N=1.5, S=0.91 and ash=33. The moisture content in the coal is taken at 11.7%. The higher heating value of Vietnam cement industry has a long history from 1899 and so far, there are 76 cement production lines with total design capacity of 81,56 million tonnes a year, which have been meeting domesticFigure 2. Schematic diagram of a cement industry
احصل على السعر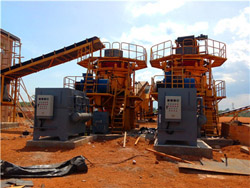
Schematic of cement production. Download
The innovation in the entire pyroprocess in modern cement plants is the use of an additional calcining vessel, in which the raw-mix undergoes calcination to a level of 90 to 95%.The innovation in the entire pyroprocess in modern cement plants is the use of an additional calcining vessel, in which the raw-mix undergoes calcination to a level of 90 to 95%.Schematic of cement production. Download
احصل على السعر
Integrated energy optimisation for the cement industry: A
Integration of all energy-intensive components of a cement plant production process in a simulation package. • Uniquely, the simulation model incorporates constraints such as maintenance, production and dynamic energy costs. • The system was implemented on four different cement plants and a total energy cost saving of 7.1% was achieved.Keywords: cement; ball mill; conscious laboratory; random forest; support vector regression 1. Introduction In the cement industry, grinding is one of the most consuming energy stages in the production units. Around 65% of the total used electrical energy in a cement plant has to be utilized to grind raw materials, coal, and clinker [1,2].Ventilation Prediction for an Industrial Cement Raw Ball
احصل على السعر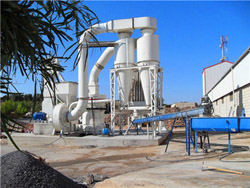
(PDF) IMPROVING THERMAL AND ELECTRIC ENERGY EFFICIENCY AT CEMENT PLANTS
Cement production is a resource-intensive practice involving. large amounts of raw materials, energy, labor, and capital. Cement is produced from raw materials such as limestone, chalk, shaleThe results show that approximately 2.48t, 4.69t, and 3.41t of materials are required to produce a ton of the product in raw material preparation, clinker production, and cement grinding stages(PDF) Analysis of material flow and consumption in cement production
احصل على السعر
ATOX coal mill FLSmidth
The ATOX coal mill is suited for various installation types, whether inert or non-inert, and direct or indirect firing systems. An inert system designed for indirect firing is the most common solution for cement plants. Equipped with the high-efficiency RAKM dynamic separator, the ATOX coal mill will grind any type of coal to the requiredCement production is highly energy consuming process Schematic view of a typical vertical roller mill with the with energy utilization of around 110-150 kWh/t (Villa, streams is illustrated in Figure 1 and Table 1 gives the 2005). Majority of this energy (40 %) are consumed for names of the streams.Performance Evaluation of Vertical Roller Mill in Cement
احصل على السعر
Coal Mill an overview ScienceDirect Topics
Observer-Based and Regression Model-Based Detection of Emerging Faults in Coal Mills. Peter Fogh Odgaard, Sten Bay Jørgensen, in Fault Detection, Supervision and Safety of Technical Processes 2006, 2007. 5.2 Experiments with and design of the regression model-based approach. Operating data from a coal mill is used to compare the fault detection Contribute to crush2022/mill development by creating an account on .mill/sbm diagrams of cement batching plants.md at main
احصل على السعر
Alternative Fuels from Waste Products in Cement Industry
One hundred percent substitution was recorded in a plant-utilizing liquid waste in its main burner. The main alternative fuels used in cement industry are residue oil and solvents, contaminated wood and process waste from wood, used tires and rubber waste, plastic waste, thermal fraction of domestic waste, sewage sludge, and animal meal.i ABSTRACT Title: Modelling for integrated energy optimisation in cement production plants Author: Mr. J.A. Swanepoel Supervisor: Prof. L. Liebenberg Degree: Master of Engineering (Mechanical) Cement production is an energy intensive process. In South Africa the cost of energyModelling for integrated energy optimisation in cement
احصل على السعر
Modeling operational cement rotary kiln variables with
2.1. Dataset. For exploring the relationships between kiln feed rate, and ID fan speed, and other operating variables, a dataset was collected from one of the pre-heater and rotary kiln (Clinker Baking unit) circuits (line 1) in the Ilam cement plant (Figure 1).The Ilam plant has two lines for cement production (5,300 t/d).A schematic of the cement plant equipped with the tail-end CaL process is shown in Figure 3. In this configuration, the CaL system, characterized by two interconnected circulating fluidized bed reactors, is placed between the preheating Frontiers Evaluating the Carbon Footprint of Cement Plants
احصل على السعر
Modeling of energy consumption factors for an
circuit of cement plants consumes around 4% of a year’s global electrical energy production. It is well Figure 1.Schematic of raw vertical roller mill circuit in the Ilam cement plant.Download scientific diagram Schematic diagram of a cement plant with a membrane-based CO 2 capture unit (The end-of-pipe option). Abbreviations: R/M, Raw Mill; B/F, Bag Filter; F/D, Fuel DryingFigure 3-15 Schematic diagram of a cement plant with a
احصل على السعر
Cement Plant an overview ScienceDirect Topics
Fuels, burnability and characterization of cement raw meal. Vipin Kant Singh, in The Science and Technology of Cement and Other Hydraulic Binders, 2023. 6.4.6.1 Preblending of coal. Cement plants receive coal from more than one source, and even from the same source of supply, there are wide fluctuations in the ash content. Such fluctuations upset the Distribution of dust emissions at bag filters in the cement mill section no.1 (mill filterpoint A and separator filter-point B, Figure 1) of the analyzed cement plant.(PDF) Dust Emission Monitoring in Cement Plant Mills: A
احصل على السعر
Dust Emission Monitoring in Cement Plant Mills: A Case
This paper is a case study of a Portland cement plant in Romania, the experimental determinations presented mainly focusing on dust emissions in an important sector of the plant (cement mill and related facilities), with dust extraction from two chimneys in working areas (cement mill filtration system and grinder component separator filtrationVertical roller mills (VRM) are widely used to grind, dry, and select powders from various materials in the cement, electric power, metallurgical, chemical, and nonmetallic ore industries. For the sectors above, the VRM is a powerful and energy-intensive grinding field [1], [2]. It is used to grind slag, nonmetallic ore, and other block A cement Vertical Roller Mill modeling based on the
احصل على السعر