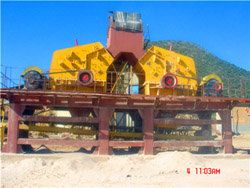
A comprehensive investigation of a grinding unit to reduce
Energy consumption rate for the production of cement is calculated to be 3,964.46 MJ/ton cement, which reduced to 3,779.77 MJ/ton cement by decreasing the raw meal moisture content and by the effect of waste hot gas supplied to the grinding system.During grinding process, the energy obtained from the rotary burner is consumed. In this study, the first and second law analysis of a raw mill is performed and Reducing energy consumption of a raw mill in cement industry
احصل على السعر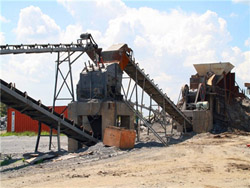
Energy consumption assessment in a cement production plant
After installation of pre-grinders, measurements revealed that specific energy consumption in raw material grinding and cement grinding decreased about 14% Coal has been the main stay of Portland cement production and remains so with coal providing around 90% of the energy consumed by cement plants around the Coal utilization in the cement and concrete industries
احصل على السعر
Modeling of energy consumption factors for an industrial cement
Carbon Research (2023) Cement production is one of the most energy-intensive manufacturing industries, and the milling circuit of cement plants consumes Approximately 60–70% of the total electrical energy used in a cement plant is utilized for the grinding of raw materials, coal and clinker [63]. The electrical energy A critical review on energy use and savings in the cement industries
احصل على السعر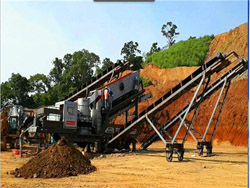
Energy-Efficient Technologies in Cement Grinding
In this chapter an introduction of widely applied energy-efficient grinding technologies in cement grinding and description of the operating principles of the related equipments and comparisons over The cement industry, an industry characterised by low margins, is responsible for approximately 7% of anthropogenic CO2 equivalent (CO2e) emissions Towards a business case for CO2 mineralisation in the cement
احصل على السعر
Modernizing cement manufacturing in China leads to
NSP rotary kilns started to account for more than 10% of the market share in 2001, and China’s national cement production peaked in 2014. Therefore, 2001 Contribute to sbmcrushers/sbmchina development by creating an account on .sbmchina/sbm equipment in cement plant coal surface mining
احصل على السعر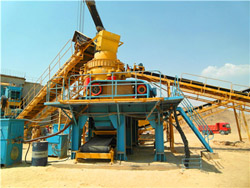
Ambuja Cement Annual Report 2020-21
With a cumulative 29.65 MTPA manufacturing capacity across five integrated units and eight grinding units, Ambuja Cement is one of India’s most trusted cement manufacturing companies. Our state-of-the-art manufacturing operations are backed by coal and limestone mining leases, captive power plants and port terminals, helping it The coal grinding process Grinding Mill China. coal mill in power plant coal mill Coal grinding process is the surface area of the coal is crushed and its growing process. To add a new surface, molecules must overcome the adhesion grinding process in coal KOOKS
احصل على السعر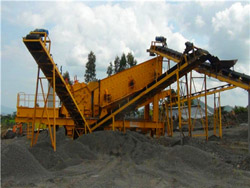
(PDF) Dust Emission Monitoring in Cement Plant Mills: A
cement plant at a distance of less than 300 m, as shown in [44]. Al Smadi et al. found that, at 250 m from the factory, the dust concentration in the air was 359.61 μ g/Nm 3,while at aThe cement industry is responsible for approximately 7% of anthropogenic CO 2 equivalent (CO 2e) emissions 1,2 with the highest carbon intensity of any industry per unit of revenue 3.To combatTowards a business case for CO2 mineralisation in the cement
احصل على السعر
A Review on Pyroprocessing Techniques for Selected Wastes
Due to the high levels of operational reliability and availability, ball mills remain the most frequently applied finishing grinding unit in cement plants. Compared with newer milling devices such as VRM and HPGR, ball mills have the highest specific power consumption and the lowest power utilization (about 32–35 kWh/ton depending on theCoal has been the main stay of Portland cement production and remains so with coal providing around 90% of the energy consumed by cement plants around the world. It takes 200–450 kg of coal to produce 1 ton of cement. In 2015 the cement industry consumed around 4% of global coal production, around 330 Mt/year (Global Cement, 2016).Coal utilization in the cement and concrete industries
احصل على السعر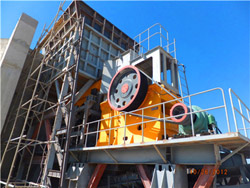
(PDF) Mining Activities, Cement Production Process and
Cement has hydraulic properties like slaked lime and hardens when mixed with water. Compressive strength increases in time and reaches its practical top limit after 28 days. Mixing crushed stoneCement production process typically involves: •. grinding limestone (and other raw materials to achieve the right chemical composition) to about 90% passing 90 μm in a dry circuit, •. making cement by the chemical reaction between the components of the ground mixture. This chemical reaction occurs at high temperature in a rotary kiln, •.Cement grinding optimisation ScienceDirect
احصل على السعر
Review on vertical roller mill in cement industry & its
Now a days Cement plants are producing 75–80% PPC & 20–25% OPC due to high market demand of PPC. Production of PPC is cheaper and it's market rate is also lower than OPC by nearly 25 rupees per bag, so general consumer are attracted towards PPC cement. Cement companies also want to produce more and more PPC grade.There are four stages in the manufacture of portland cement: (1) crushing and grinding the raw materials, (2) blending the materials in the correct proportions, (3) burning the prepared mix in a kiln, and (4) grinding the burned product, known as “ clinker ,” together with some 5 percent of gypsum (to control the time of set of the cement).Cement Extraction, Processing, Manufacturing Britannica
احصل على السعر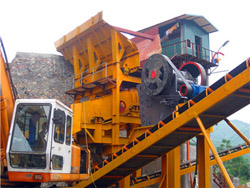
JP deal positions UltraTech as largest cement
The acquisition comprises of an integrated cement unit at Sewagram and a grinding unit at Wanakbori in Gujarat. The combined capacity of both the divisions of the Gujarat unit is 4.8 mtpa with a 57.5 Energy audit and waste heat recovery from kiln hot shell surface of a cement plant. Options related to waste heat recovery in cement plant has been studied. Thermodynamics of rotary kiln, energy losses, refractory selection and impact are discussed. Temperature profile of rotary kiln with recovering losses of kiln temperature are investigated.Energy audit and waste heat recovery from kiln hot shell surface
احصل على السعر
Low carbon measures for cement plant a review
Cement manufacturing is an energy and carbon-intensive industry. The cement industry contributes approximately 5% of the global man-made carbon dioxide (CO 2) emissions and is thus becoming the second largest CO 2 contributor in industry after power plants. A wide range of options are available to considerably reduce CO 2 China Cement Plant manufacturers Select 2023 high quality Cement Plant products in best price from certified Chinese Building Plant, Crushing Plant suppliers, wholesalers and factory on Made-in-China China High Capacity Cement Clinker Grinding Plant with Cement Ball Mill Low Price Manufacturers . US$ 1000000-10000000 / Piece. 1 PieceChina Cement Plant, Cement Plant Manufacturers, Suppliers,
احصل على السعر
PROCESS CONTROL FOR CEMENT GRINDING IN
The power ingesting of a grinding process is 50-60% in the cement production power consumption. The Vertical Roller Mill (VRM) reduces the power consumption for cement grinding approximately 30-40% associated with other grinding mills. The process variables in cement grinding process using VRM are strongly nonlinear and India’s cement production is expected to increase at a CAGR of 5.65 per cent between FY16-22, driven by demands in roads, urban infrastructure and commercial real estate. India’s cement production was expected to range between 380-390 million tonnes in FY23, a growth rate of 8 to 9 per cent y-o-y.Pyroprocessing and Kiln Operation Indian Cement Review
احصل على السعر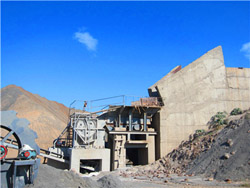
Dust Emission Monitoring in Cement Plant Mills: A Case
This paper is a case study of a Portland cement plant in Romania, the experimental determinations presented mainly focusing on dust emissions in an important sector of the plant (cement mill and related facilities), with dust extraction from two chimneys in working areas (cement mill filtration system and grinder component separator filtrationIn this study, certain measures are implemented in an existing raw mill in a cement factory and the specific energy consumption of the unit is calculated to be 25.52 kWh/ton farine.(PDF) Determination of correlation between specific
احصل على السعر