
Modeling and experimental study of grinding forces in
Grinding forces are composed of chip formation force and sliding force. A new mathematical model of grinding forces in surface grinding is developed in this Grinding is one of the grating machining that consistently to accomplish sufficiently high dimensional exactness or potentially great quality surface completions. Analysis on surface grinding of mild steel by varying
احصل على السعر
Tips for Improved Surface Grinding Norton Abrasives
urface grinding is a very typical grinding process which is done in many industries, especially general industrial and job shop type locations. While some facilities are set up with optimized machines, Abstract. Grinding is an important means of realizing precision and ultra-precision machining. Vibration caused by an unbalanced grinding wheel in Modeling and simulation of grinding surface topography
احصل على السعر
Temperature field model in surface grinding: A ResearchGate
Grinding is a crucial process in machining workpieces because it plays a vital role in achieving the desired precision and surface quality. However, a significant Subsequently, the grinding path for each grit is calculated using the grinding process parameters to evaluate whether it contacts the workpiece surface. Surface prediction in laser-assisted grinding process considering
احصل على السعر
Effects of the grinding conditions on geometry of microstructured
Precision grinding is a promising method for machining microstructured surfaces. Controlling microstructured surface geometries provides interesting insights Grinding is one of the effective manufacturing processes with which to produce highly accurate parts with an ultra-fine surface finish. The tool used to remove materials in grinding is called the grinding wheel. Abrasive grains made of extremely hard materials (alumina, silica, cubic boron nitride, and diamond) having a definite grit size but Modelling and Analysis of Topographic Surface Properties of Grinding
احصل على السعر
Modeling and simulation of grinding surface topography
Grinding is an important means of realizing precision and ultra-precision machining. Vibration caused by an unbalanced grinding wheel in grinding process has a significant impact on the quality of workpiece surface. However, the effect of wheel surface topography and/or the relative vibration between grinding wheel and workpiece are not Response surface methodology (RSM) is used to investigate the effects of three controllable input variables, namely grit size of grinding wheel, feed rate, and depth of cut on SR & MRR. Horizontal spindle surface grinding machine was used in order to conduct the experiment on die tool steel (AISI D3) work piece.Optimization of Surface Grinding Process Parameters Through RSM
احصل على السعر
JMMP Free Full-Text Analysis of Surface Grinding of
This paper analyzes the surface grinding of unfilled and glass-filled polyamides. The process is performed by varying the workpiece velocities to evaluate applied practical applications in the industry while being energy efficient. During the machining, the temperatures, normal forces, tangential forces, and spindle power were The seventh and final factor to consider is horse power. We have to consider the horse power of the grinding machine to determine the grade of the bond or hardness of the wheel. High Horse Power When a machine has a higher horse power available at the spindle, we should use a harder wheel grade.The 7 Factors Used to Determine a Grinding Wheel Specification
احصل على السعر
Surface Grinding Wheels: Types and Specification Fine
Above: Grinding wheels with different grain sizes. The grain size in your grinding wheel is classified as coarse 8-30, medium 30-60, fine 70-180 and very fine 200-600.The material removal rate will be more for your grinding wheel with coarse abrasives and less for a wheel with fine abrasives; also grinding wheels with fine or very fine Prediction of active grits count (cutting grits) In the present analysis, the number of cutting grits out of the. contacting grits is determined with the help of a simple abrasive wear. model asA method for prediction of active grits count in surface grinding
احصل على السعر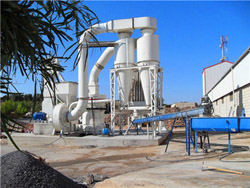
Surface Grinding Tips 10 Essential Tips Kaast Machine Tools
Keep the surface grinding machine clean and free from debris. Regularly remove swarf, chips, and grinding residue from the work area and coolant tanks. Clean and lubricate machine components as per the manufacturer’s recommendations to ensure optimal performance and longevity. 10. Continuous Learning and Improvement.Surface roughness and the material removal rate (MRR) are two important indicators during the grinding process. The former determines the surface quality while the latter reflects the grinding efficiency directly. In this paper, the two indicators are taken into consideration simultaneously and differently by converting them into a comprehensive Optimization of Grinding Parameters for the Workpiece Surface
احصل على السعر
Principles of Precision Surface Grinding Services
Surface grinding services utilize precision surface grinding methods to make cubic metal parts square and parallel or the ends of metal rods perpendicular. Request a Quote. 973 239-1100. About Us. consider the effects of a part’s diameter, length, straightness, and manufacturing method. Read Content.Heat generation is a critical issue in grinding. If the grinding point generates significant heat, dimensional and shape accuracy may decrease due to thermal deformation, and the machined surface may deteriorate due to grinding burn. Therefore, monitoring the temperature during grinding is important to obtain ideal machining Development of In-Process Temperature Measurement of Grinding Surface
احصل على السعر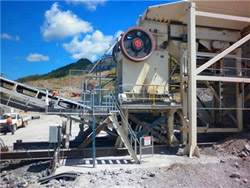
Evaluation of surface grinding of AISI 304 stainless steel using dry
pressed air on surface integrity of the workpiece using Mitutoyo SJ-210-NATA. Surface roughness of the workpiece were measured for both dry and compressed air during the grinding process for the purpose of comparison. 3 Results and discussion 3.1 Consideration on depth of cut In order to consider the depth of cut for surface grindingGrinding operation can be considered as a subset of cutting operation where each wheel in grinding wheel acts as a single point cutting tool. The common types of grinding are surface grinding and cylindrical grinding. Here for analysis purpose we consider only cylindrical grinding (ie both inside and outside diameter grinding). II. MethodologyFmea Analysis of Grinding Defects IOSR Journals
احصل على السعر
Dynamic force modeling and mechanics analysis of precision grinding
Modelling and analysis of micro-grinding surface generation of hard brittle material machined by micro abrasive tools with helical chip pocket. J. Mater. Process. Tech., 297 (2021), Article 117242, 10.1016/j.jmatprotec.2021.117242. View PDF View article View in Scopus Google Scholar.A reliable prediction of grinding forces and surface morphology is critically important to the design of a grinding process. However, due to the complex microstructure of a grinding wheel which contains randomly-sized and randomly-distributed abrasive grains, a practical prediction model has been unavailable. This paper aims to Analytical grinding force prediction with random abrasive grains
احصل على السعر
A Study on Calculating Grinding Temperature: Proceedings of
This study presents a prediction study of the surface hardness in surface grinding ASIS 1045 steel. Base on the experimental data on the changes in characteristics of steel in the heat treatmentGrinding is applied widely in manufacturing of high-precision component. And, pursuing the forming mechanism, together with predicting topography characteristics and roughness of the grinding surface, is becoming more and more important in improving the grinding quality. The grinding surface is formed by the interaction between the Kinematics modeling and simulating of grinding surface
احصل على السعر
Sheet Metal Grinding Beginners & Experts Guide
Consider sheet metal grinding angle: As you grind metal, the disc angle should be about 5 to 10 degrees. Of course, you should determine this from the horizontal surface. Grinding pressure should remain constant: Always apply reasonable pressure since overdoing it will cause overheating. Additionally, it will glaze the grinding disc grains.This chapter presents an experimental study of grinding forces as relationship of workpiece speed v, feed rate sa and depth of cut a. For the modeling of cylindrical grinding used was response surface methodology and genetic algorithms. Modeled was the tangential force Ft and the normal force Fn in cylindrical grinding. The Grinding Force of Cylindrical and Creep-Feed Grinding Modeling
احصل على السعر
Intro to Grinding Methods, Machines and Tools Practical
Grinding is used to finish workpieces so that they meet the required surface finish quality. It rids unwanted material from the workpiece, like any rough texture that remains from previous machining applications. Grinding machines or tools use an abrasive wheel to remove metal from the workpiece. When the wheel rotates, it cuts
احصل على السعر