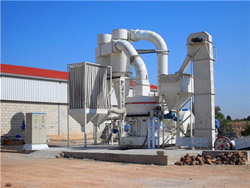
Ball Mill Critical Speed 911 Metallurgist
A Ball Mill Critical Speed (actually ball, rod, AG or SAG) is the speed at which the centrifugal forces equal gravitational forces at the mill shell’s inside surface Speed rate refers to the ratio of the speed of the mill to the critical speed, where the critical speed is n c = 30 / R. In practice, Optimal Speed Control for a Semi-Autogenous Mill Based
احصل على السعر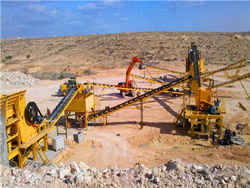
Industrial SAG mill dimensions and speeds.
For a given number of balls, if the mill rotation speed is higher than or equal to its critical speed, the balls stick to the mill wall and the grinding operation does not occur and centrifugingSimulation results under the ∅5250 × 500 mm mill model show that the mill operates with the optimal effect when the mill is under the condition of 80% critical speed and 15% fill level;...Operation Analysis of a SAG Mill under Different
احصل على السعر
Research on performance of a laboratory-scale SAG mill based on
Here, the mill fraction of critical speed is the ratio of the actual speed of the mill to the critical speed, and the empirical formula [25] of the critical speed of the For example, for an 36′ × 17′ SAG Mill, with a power consumption of 11.7 MW, operating at 73% solids, 13.5% balls charge and at 76% of the critical speed, with Modelling SAG milling power and specific energy
احصل على السعر
Energies Free Full-Text Operation Analysis of a SAG
The SAG mill power does not increase with an increase in the mill speed ratio, but when the speed reaches about 85% of the critical mill speed, the power decreases and the mill power increases again, Download scientific diagram SAG mill compared to crusher and ball mill product size distributions (75 mm), a high mill speed (75% of critical speed) and a coarse feed top size (19 mm).SAG mill compared to crusher and ball mill product
احصل على السعر
Operation Analysis of a SAG Mill under Different Conditions
the power of the mill does not increase linearly with an increase in the mill speed ratio, but will decrease after 85% of the critical speed, and finally increase again; the optimal steel ball ratio in the SAG mill depends on the simulation time (mill actual working time) and the limitation of the rated power.In a SAG mill the dimensions of the mill were 9.75. m × 3.5 m and the specific gravities of the mineral and that of the balls charged were 4.1 and 7.9 respectively.. The mill was rotated at 75% of its critical speed when 8 % of the mill volume was charged with grinding balls.Estimate:1. The mill power drawn, 2. The maximum mill filling possible.Semi Autogenous Grinding Mill an overview ScienceDirect
احصل على السعر
Pre-Processing to Increase the Capacity of SAG Mill
The accumulation of critical size material in the SAG mill charge is thus reduced by a specific combination between mill speed and ball charge (SAG-5 and SAG-6 tests), eliminating the circulating load when the mill is under the condition of 80% critical speed and 15% fill level; the power of the mill does not increase linearly with an increase in the mill speed ratio, but will decrease after 85% of the critical speed, and finally increase again; the optimal steel ball ratio in the SAG mill depends onOperation Analysis of a SAG Mill under Different Conditions
احصل على السعر
How to Calculate and Solve for Critical Mill of Speed Ball Mill
The formula for calculating critical mill of speed: N c = 42.3 / √ (D d) Where: N c = Critical Speed of Mill. D = Mill Diameter. d = Diameter of Balls. Let’s solve an example; Find the critical speed of mill when the mill diameter is 12 and the diameter of balls is 6. This implies that;Particle collision energy is mainly determined by lifter face angle and rock shape. Further, when the SAG mill runs at a low speed, the lifter face angle and rock shape become the main influencing factors of the mill torque, and the fraction of critical speed becomes the dominant factor with a high running speed of the SAG mill.DEM investigation of SAG mill with spherical grinding media and
احصل على السعر
Low SAG Mill Critical Speed Grinding & Classification Circuits
If you have to reduce the SAG mill speed because of avoiding liner breakage, maybe it’s better to modify the shell lifter design. Low speed may cause decreasing capacity, higher steel ball and liner wear rate. D80 of SAG mill may be finer because of more cascading action and less capacity which results in more retention time in SAG mill.The second step to decreasing high wear rates was to reduce the maximum operating speed on the SAG mill from 13.2 RPM (78% of critical speed) to 12.7 RPM (75% of critical speed). Justifications were made for the installation of an Omnicone crusher on the SAG pebble oversize material. Conservative estimates were made that as Variable Speed SAG Mill 911 Metallurgist
احصل على السعر
Energies Free Full-Text Operation Analysis of a SAG Mill under
Simulation results under the ∅5250 × 500 mm mill model show that the mill operates with the optimal effect when the mill is under the condition of 80% critical speed and 15% fill level; the power of the mill does not increase linearly with an increase in the mill speed ratio, but will decrease after 85% of the critical speed, and finally the SAG mill critical speed; Pc = SAG mill power consumption (kW); % 600 +100 = % of the fresh feed in the size range 152 +25 mm. M. Silva, A. Casali/Minerals Engineering 70 (2015) 156–161 157. In fact the later can be modelled as a function of the others. Addi-Modelling SAG Milling Power and Specific Energy Consumption
احصل على السعر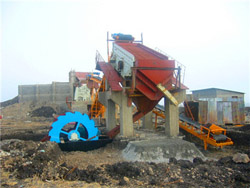
Semi-autogenous grinding (SAG) mill liner design and development
78% to 80% critical speed, pulp-lifter efficiencies could fall and affect overall mill performance. Using a smaller, not larger, bucket size to focus the impact of the charge at the toe, along with increasing mill speed as shell lifters wear, is a promising current development in shell liner design and SAG mill opera-Increasing the speed of the mill above the design point of 74% critical speed was also considered but did not result in greater power draw of the mill due to the mill motor design (Dunne et al 2001).Actual SAG Mill Operating Power Download Table
احصل على السعر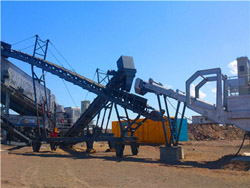
Optimization of the SAG Grinding Process Using Statistical
2. Background. The SAG grinding process has been modeled by various authors, either generating explanatory models of the grinding process, with the aim of modeling, simulating, and optimizing the individual process, as well as integrating it into aggregate processes, such as the mine-to-mill (M2M) paradigm, a practice that has A large SAG mill for a point at 74% of critical speed is very close to was subjected to a progression of 36 lifts per circle, 24 predicted power draw. It is also interesting to note that lifts per circle, and 12 lifts per circle. A value of 24 lifts when the speedSUPPLY, INSTALLATION, & COMMISSIONING OF THE WORLD'S LARGEST GRINDING MILL
احصل على السعر
conferenceseries.iop materials science and engineering open
Charge motion of the 4-m mill with different lifter shapes and at the same operating conditions: 70% critical speed, 35% mill load. Liner Spacing and Shapes. Liner designs depend mainly on various combinations of lifter angles, spacing, height, and mill speed as well. Making changes in lifter spacing and height would modify theMill, gear and pinion friction multiplier: 1.025. Mill Power required at pinionshaft = (240 x 16.5 x 1.025) ÷ 0.746 = 5440 Hp. Speed reducer efficiency: 98%. 5440 Hp ÷ 0.98 = 5550 HP (required minimum motor output power). Therefore select a mill to draw at least 5440 Hp at the pinionshaft.AG Autogenous & SAG Semi-Autogenous Mill Design Calculations
احصل على السعر
(PDF) Effects of Ball Size Distribution and Mill Speed and Their
In this research, the mill was run with the constant mill speed (70% of critical) A 1.8-m diameter pilot scale SAG mill which includes realistic end walls and a discharge grate is used.when the mill is under the condition of 80% critical speed and 15% fill level; the power of the mill does not increase linearly with an increase in the mill speed ratio, but will decrease after 85% of the critical speed, and finally increase again; the optimal steel ball ratio in the SAG mill depends onOperation Analysis of a SAG Mill under Different Conditions
احصل على السعر
(PDF) Assessment of the Performance of Grinding Circuit for
Furthermore, the SAG mill circuit indicated varying feed sizes (i.e. x F, 80 =102 to 185 mm) which could be rectified by closer monitori ng and control of ratiosTwo new SAG milling models are developed in this work, able to predict power or specific energy consumption, including the usual design variables such as mill size; balls charge level, solids concentration in the SAG mill feed and % of critical speed, but adding a variable that represents the feed size distribution.Modelling SAG milling power and specific energy ScienceDirect
احصل على السعر